Actionable Digital Transformation Strategies for Manufacturing
Key Takeaways:
- Learn how to use digital twins to optimize and align product design, manufacturing processes, and production
- See how manufacturers are applying digital transformation capabilities to gain new levels of speed, automation, profitability
The Full Article:
Unyielding market pressure and global disruptions have reshaped the economic landscape. Big challenges call for bold action, including taking risks and adopting new ways of working and thinking.
SpaceX and Apple are just two examples of companies with new capabilities that have shaken up their respective industries. In manufacturing, forward-thinking companies are embracing the digital transformation journey and its initiatives to unlock new opportunities, innovate rapidly, improve business outcomes, and stay ahead of their competition.
But how are they doing it? To answer that question, this article covers the following digital transformation strategies and best practices for manufacturers:
- What is Digital Transformation in Manufacturing?
- Digital Twins for Manufacturing
- How Product Development Uses Digital Transformation
- How Sourcing Leverages Digital Transformation
- How Suppliers Use Digital Transformation
- Take the Next Step in Digitalization
1. What is Digital Transformation in Manufacturing?
Digital transformation is often synonymous with “Industry 4.0” and “digitalization.” At a high level, digital transformation in manufacturing refers to converting manual manufacturing operations into digital formats (also known as digital twins) to simulate the entire product development lifecycle: product designs, manufacturing processes, and factories. Digital tools enable stakeholders to address manufacturing complexity by automating multiple manufacturing scenarios simultaneously within minutes.
Gain Automated Insights
Manufacturers that can rapidly simulate design and production scenarios are well-positioned to anticipate new opportunities and sidestep potential roadblocks. Using the digital twin model, companies can simulate the product design, manufacturing process, and factory specifications simultaneously.
It enables companies to run “what-if” scenarios regarding product cost, carbon, manufacturing process, and location – and make data-driven decisions quickly and accurately. By extending simulation capabilities throughout the product development lifecycle, manufacturers have the visibility to address profitability, sustainability, manufacturability, and risk.
Benefits of Digital Technologies
Digital transformation benefits for product manufacturers include improved production cycles, faster time to revenue, increased customization, more efficient utilization of engineering resources and better products. Not to mention the overwhelming competitive advantage digital solutions can unlock for manufacturers.
McKinsey confirmed that successful digital transformations yield exceptional returns. Across many manufacturing sectors, it is common to see 10%- 30% increases in throughput, 15%- 30% improvements in labor productivity, 30%-50% reductions in machine downtimes, and 85% increases in more accurate forecasting.
2. Digital Twins for Manufacturing
Today’s manufacturing companies need end-to-end digitalization to extend the value of their existing investments, such as 3D CAD and product lifecycle management (PLM) systems. Digital transformation with automation capabilities can enable organizations to work more efficiently and collaboratively to meet their manufacturability, cost, and sustainability targets.
As digitalization has evolved, manufacturing industry leaders are coalescing around the idea of connecting multiple digital twins to provide end-to-end visibility, insights, and responsiveness. Specifically, companies are thinking beyond the traditional product digital twin to gain new insights from digital manufacturing process twins, and digital factory twins.
Companies can combine automation and manufacturing simulation software to thread three digital twins together and unlock actionable, real-time data analytics for better decision-making.
Next, let’s review how engineering, sourcing, and supplier teams are improving their operations as they become more digital.
3. How Product Development Uses Digital Transformation
Digital transformation in product engineering starts by integrating the digital twin (3D CAD model) with smart manufacturing processes to make informed design decisions based on how well the product is optimized for a specific production line. Digital technologies also enable cross-functional teams to collaborate and share data across the product lifecycle.
Impact Example
A large European defense contractor started using aPriori to help facilitate conversations between engineering and sourcing. In one example, sourcing received a low number of bid responses, and the bids they received were expensive. The suppliers attributed their high quotes to a manufacturing specification that required a small undercut in the middle of a component.
Sourcing brought the design to engineering, opened the part in aPriori, and received automated guidance to improve design for manufacturability (DFM). Engineering validated this issue and updated the design. The result: a 50% quote reduction based on the design change.
4. How Sourcing Uses Digital Transformation
Best-in-class companies have been implementing new technologies that provide sourcing teams with early insights into what’s coming down the product pipeline. This capability supports collaborative, fact-based discussions internally across the product teams and externally with suppliers. Today, we’re seeing companies employing new ways of working with the supply base.
Impact Example
One global manufacturer’s cost engineering team needed to scale its should cost capabilities and collaborate globally more efficiently. The company adopted aPriori’s cloud-based solution and analyzed more than 150,000 parts for cost during its first year. aPriori contributed to more than $30 million in realized savings.
5. How Suppliers Use Digital Transformation
Because OEMs are accelerating new product development to reach the market faster, suppliers are under pressure to respond just as quickly—and sometimes much earlier—in the design process. The quotes need to be accurate to avoid costly mistakes.
To address speed and accuracy as well as operational efficiency, more providers across the supply chain are exploring the use of digital factories. If OEMs and their suppliers use aPriori manufacturing insights data, both sides can better understand what’s driving costs – and collaborate to bring those costs down.
Impact Example
By embracing digital transformation, Flex, a major supplier, has exponentially accelerated its quoting process from weeks to days. The company has also increased its win rate from 12% to 68% just by being more responsive.
6. Take the Next Step in Your Digital Transformation Strategy
At its core, the digital transformation process provides a technology and data foundation that is interoperable, scalable, and agile enough to support business needs today and in the future (e.g., machine learning, artificial intelligence [AI], robotics, IoT, etc.). Like any new approach, it requires the right executive leadership, people, business processes, and employee buy-in to succeed.
Digital transformation initiatives that connect teams, data, and business models and processes have an opportunity to realize quantifiable benefits quickly. That’s because product team members can make informed business decisions to get to market faster, remain competitive, improve innovation, and ensure revenue growth.
Digital Transformation Efforts Can Yield Big ROI
A clear digitalization roadmap, along with aPriori’s manufacturing insights, can provide a framework for true business transformation. The return on investment? Greater operational efficiencies, reduced costs, enhanced profitability, faster time to market, and more innovation opportunities. More importantly, a centralized data source associated with digital transformation provides a flexible foundation for the next step in your digital journey, including AI.
Cut Costs, Reduce Design Iterations and Carbon, and Get to Market Faster?
aPriori makes the seemingly impossible, possible.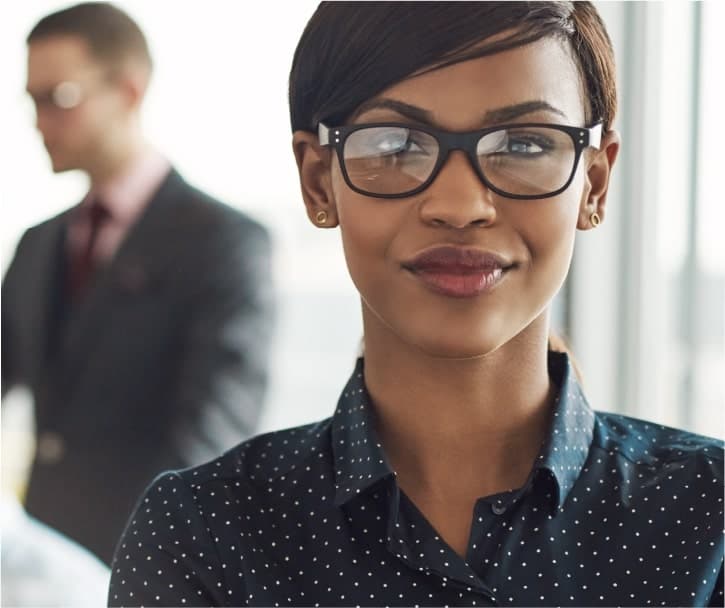