Optimize Design Engineering with Workflow Integration of CAD
According to McKinsey, smart workflows and seamless interactions between humans and machines will be a given in corporations by 2025. Their insights also noted that employees will have a heavier reliance on data-driven technologies to further optimize their work.
In this article, we will discuss manufacturing simulation and CAD integration. We will explore the various solutions that can complement 3D CAD as well as highlight how integrating it into product lifecycle management creates smart workflows and more seamless interactions.
For manufacturing design engineers, 3D computer-aided design (CAD) systems can help create and improve designs, facilitate better communication and documentation, and increase productivity. However, without the right workflows and integrations, they cannot identify every design issue or optimize the full value of the product via a strong design workflow.
Leverage Your 3D CAD Data with the Push of Button
With real-time technology and cloud advances, manufacturers can leverage digital twins of physical entities and processes such as manufacturing products inside a digital factory. They can run through high-level simulations and what-if scenarios throughout the product development process.
The best solutions easily and seamlessly integrate into the product development process, creating smart workflows and fostering seamless interactions. The best solution will:
- Leverage and transfer your 3D CAD data with the push of a button to gain additional insights.
- Allow design engineers to stay inside their chosen CAD application.
- Afford design engineers the ability to focus on more technical issues since they need not do anything other than input their design.
With aP Generate from aPriori, a design for manufacturability (DFM) and cost report is automatically emailed to them as soon as the design is checked into PLM.
Improve Workflows and Collaboration with A Digital Twin
A digital twin is the virtual representation of the real product. It can be used just like the physical product in the digital environment and will behave the same way. This means it can support both design and manufacturing functions, and even beyond.
Different teams are interested in different elements of data. However, it is all inside a single digital twin and a single source of truth. As a result, design engineers:
- Receive much more than a 3D representation of the product being manufactured.
- Can obtain and leverage the right tools, manufacturability, cost, and sustainability insights.
- Access an end-to-end visual of the product anywhere and at any stage of product lifecycle.
- Have the option of permitting their suppliers access to the digital twin as well.
- No longer require copies and disparate, siloed data in different formats since the digital twin removes that need.
A typical CAD workflow only goes so far. But it is easily augmented with data from the physical world. It can be in the form of (Computer Aided Engineering) CAE tools such as Finite Element Analysis (FEA) or Computational Fluid Dynamics (CFD) to simulate how the product will behave and perform.
Prior to that, it also can simulate the manufacturing process. Before starting time-consuming, expensive CAE simulation, valuable insights can be gained from simulating the manufacture of the designs, particularly when real-world manufacturing conditions (material properties, labor time and costs, tooling costs, available machinery and process routings, machine cycle times, overhead costs) can be assessed.
Unite and Streamline PLM with the Digital Twin + CAD Integration
An effective solution will uncover important manufacturability and cost details by simply inputting data such as production volume, manufacturing location, and the primary production method to be used. All stakeholders across the product lifecycle can view results of the digital twin analysis via simulations of the actual manufacturing operation options available. It allows them to pinpoint potential problems and recommend the most optimal approach(es) with a few tweaks to the design.
By enriching the digital twin early, while the 3D CAD is still being developed, issues can be addressed early in the product development process. Manufacturability is a huge driver of product cost. The sustainability of a product can be greatly improved with feedback earlier in the process. Getting actionable feedback on those three elements can be just a single click away with the aPriori CAD integration.
Design for Manufacturability Across the Product Lifecycle for Seamless Interactions Across Teams
Though experienced design engineers will have some understanding of DFM, their primary focus is to design an aesthetically pleasing, high performing, and functional product. However, manufacturers are recognizing the benefits of early-stage manufacturability, cost, and sustainability feedback. If obtaining this data is integrated into a design engineer’s workflow, it can help this process by:
- Providing greater manufacturability and cost details, with actionable feedback to enable design refinement if necessary to meet them.
- Creating smart workflows through seamless interactions and better collaboration across all teams as well as increased productivity.
- Mitigating design issues and costs, accelerating time to market and greater profitability.
- Ensuring fair market price for externally sourced parts.
When manufacturing insights are integrated into the CAD workflow, any cost, design, or manufacturability hiccups can be identified and managed quickly, saving time and money without sacrificing a quality design or product.
Reduce Product Development Time
To better understand each component of a design’s influence on overall cost, the right tools are needed. CAD integration can accelerate the simulation of dozens of different manufacturing processes based on design-level inputs.
These tools are the key to unlocking the heart of manufacturability analysis. To get quality products to market on time and within budget, design engineers need a tool that offers design alternatives to address issues.
Design engineers lacking such tools remain siloed within their area of expertise or undertake the time-consuming task of seeking out manufacturing subject matter experts to analyze the components for which they are unfamiliar. Furthermore, the inability to identify unnecessary design features that require additional manufacturing operations also impede the product development. Other factors such as design issues that necessitate recalculated supplier quotes, renegotiations, or late-stage design issues can be mitigated with a smart workflow solution that seamlessly integrates a manufacturer’s CAD files.
Optimize the Power of Design by Integrating Your CAD Systems with aPriori
3D CAD files can be imported into aPriori’s manufacturing insights platform, ensuring design engineers receive real-time feedback on design feasibility as well as design cost drivers. More importantly, good workflow integration will increase acceptance and provide actionable guidance to improve the design. It also will pre-emptively lessen potential problems in later production stages. Going one stage further, aPriori can be integrated into your PLM system.
PLM integration means designers perform their usual check-in via their PLM system. aPriori can then perform all the design for manufacturability and cost analysis. It will email the results to the design team, eliminating oversights, enabling designers to focus on immediate issues, and remediating problems through the system’s recommendations.
Conclusion
Design engineers play a critical role in product lifecycle management. A manufacturing simulation solution such as aPriori integrated with their CAD systems will result in a higher value product, reduced costs, faster time to market, and greater productivity and collaboration.
aPriori is unique in how it achieves DFM, cost and sustainability. Without being able to assess all three in a single view, it becomes much harder to make the right decisions. Precise, mechanistic analysis and simulation also can mean the difference between a great design that is cost-effective, manufacturable, and sustainable, and one that compromises value.
How Does aPriori Integrate with Your CAD System?
Speak to one of our product specialists to learn more.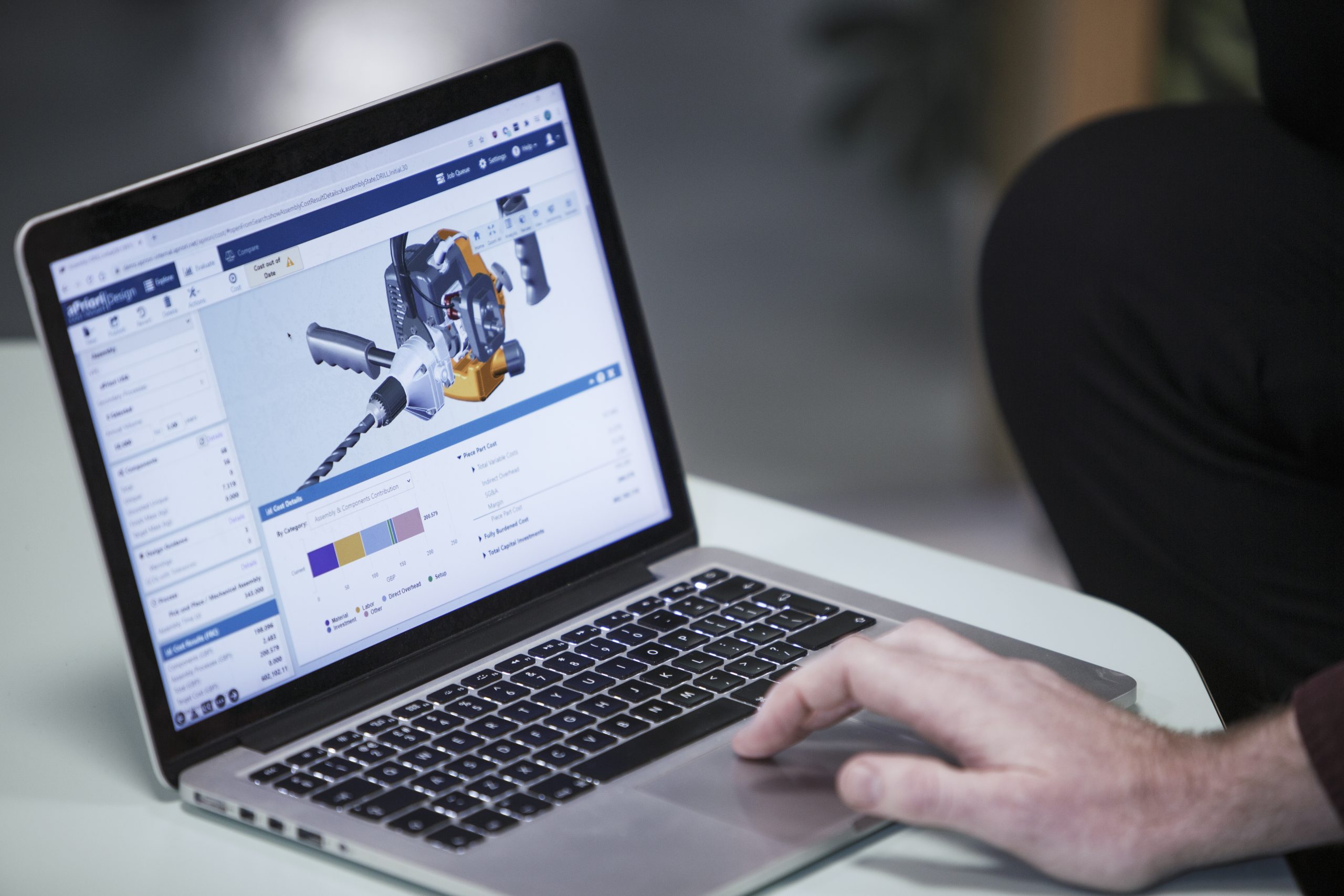