A Guide to Manufacturing Cost Estimation
Our insights are crafted for a diverse audience—from design engineers to procurement specialists—ensuring that you have actionable data to optimize processes and drive profitability. By leveraging modern estimation techniques, you can gain a clearer understanding of production expenses and unlock efficiencies throughout the entire manufacturing process. To download this comprehensive guide, simply fill out the form!
Download the Guide Now!
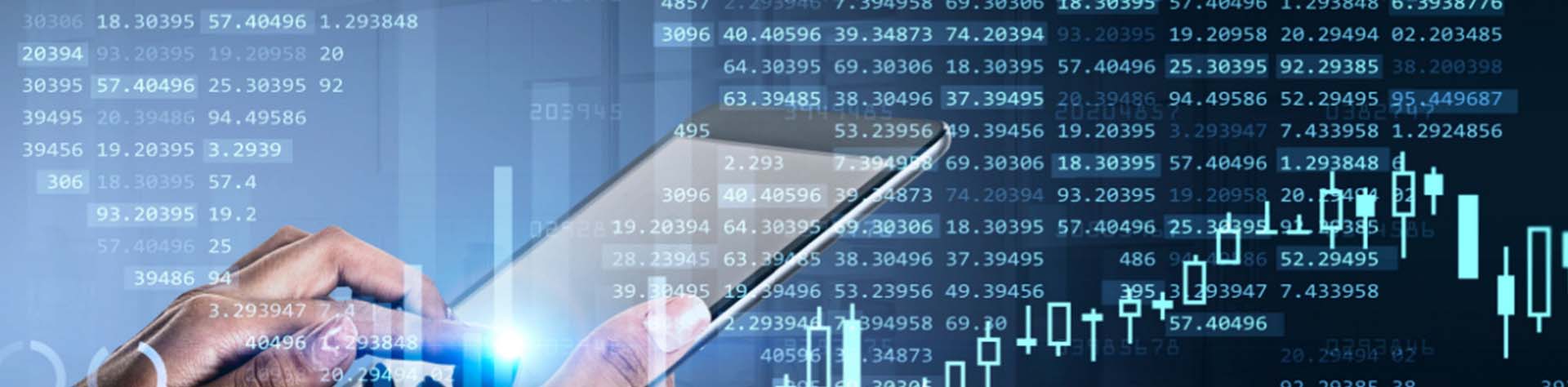
What is Cost Estimation in Manufacturing?
Manufacturing cost estimation is the collection of methodologies and tools used to forecast the expected final cost of a manufactured product.
This analysis enables manufacturers to make crucial decisions, such as identifying profitable products, selecting cost-effective suppliers, and determining which existing innovations require re-engineering to stay cost-competitive. With aPriori’s precise manufacturing cost estimation, organizations can effectively reduce late-stage engineering changes and negotiate better terms with suppliers.
The depth of this analysis can range from simple back-of-the-envelope calculations to comprehensive and precise simulation-driven cost management platforms like aPriori. Manufacturing cost estimates provide an essential foundation for related analyses, including:
Learn more about designing products that prioritize customer value.
Why It Matters: The Cost Estimation Imperative for Manufacturers Today
As product development and quoting timelines shorten, manufacturers increasingly leverage advanced cost estimation capabilities to adopt lean manufacturing and cost-reduction strategies. Failure to keep pace with these strategies will make it difficult for them to compete globally.
New technology supports these novel cost-reduction methodologies, making this relentless drive toward cost optimization possible. As these technologies increase, the trend toward highly competitive manufacturing seems only to accelerate.
To understand where manufacturing is heading and why better product cost estimation methods are driving a revolution, briefly considering how manufacturers have managed estimation in the past is helpful.
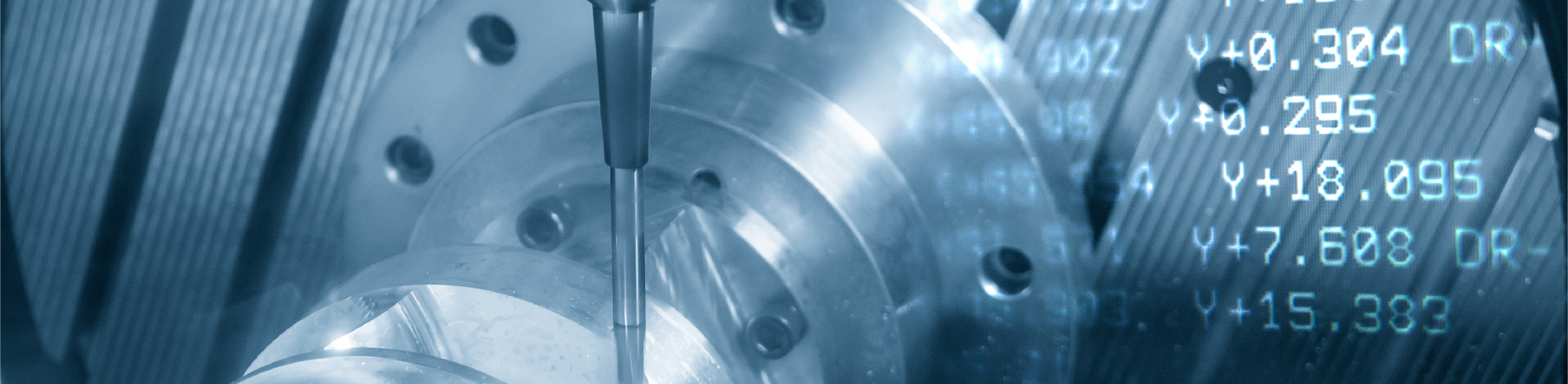
The Evolution of Manufacturing Cost Estimation Techniques
Every manufacturing operation must employ a basic cost estimation process to ensure profitability. This often involves tallying up expected input costs based on recent market prices and then adding markup for packaging, shipping, and profit. If the estimate exceeds current market prices, then production is not viable.
Companies typically use homegrown databases of historical data for this approach. The introduction of MS Excel in 1985 became the most common tool for these costing strategies, especially effective for small suppliers with a few cost estimators in the same office. However, when managing design, manufacturing, and sourcing on a national or global scale, it becomes too complex to try and manage the extreme number of cost variables in a spreadsheet.
Direct costs, such as wages and raw materials, depend on production process efficiencies and vary when estimating design alternatives.
The early to mid-1980s saw the arrival of specialized cost estimation software designed for manufacturing cost estimators. This software required significant training to utilize effectively. These early systems, which did not leverage modern database technology, often caused considerable cost model consistency challenges for design and sourcing team members across different regions.
By the early 2000s, manufacturers were seeking manufacturing cost estimation systems that would enable designers and engineers to quickly determine whether a new design, represented by a solid 3D CAD model, meets the target cost in the early stages of the design process. Sourcing managers also saw the value in should cost estimations, providing detailed manufacturing insights for better supplier negotiations. Cost estimation teams, usually understaffed, needed automated systems for tasks like batch costing of CAD models to identify cost outliers. The evolving requirements are driving manufacturers toward solutions with modern database architecture available via a web browser and equipped with extensive libraries of material and machine data.
Cutting-edge manufacturing cost estimation systems, such as aPriori, provide three levels of automation, including:
- Part/assembly 3D CAD geometry analysis: Get instant cost estimates and feedback on manufacturability from 3D CAD models
- Bulk costing analysis: Efficiently evaluate multiple parts/assemblies to identify cost-saving opportunities
- PLM integration-based analysis: Streamline workflows by integrating automated design analysis and actionable insights into the product lifecycle management (PLM) system
Lean Manufacturing: A More Holistic Conception of Cost, Waste, and Value
Introduced in the mid-1980s, lean manufacturing emerged as a cost optimization strategy amid widespread concern within the U.S. business community about the insurmountable efficiency of Japanese manufacturers. Business leaders worldwide sought to learn and emulate the methodologies driving Japanese successes. In less than 40 years after World War II completely devasted the industrial sector, Japan transformed into the envy of the world’s manufacturers, who needed to uncover the keys to its efficiency.
At its core, lean manufacturing focuses on eliminating waste, or muda, throughout a manufacturing organization. This waste can include unused materials, unsold products, and any cost that does not directly add value to the final product. Further, this waste contains idle workers waiting for shipments, excessive shipping durations from cross-country warehouses, and unsold secondary products or scrap.
While Japanese manufacturers’ successes helped popularize the lean terminology, the expansive benefits of eliminating waste and the risks of inefficiency due to under-analyzed practices and design decisions have long been considerations for forward-thinking manufacturers.
Henry Ford, a pioneer of mass production, underscored the importance of recognizing inefficiencies for better cost management in his autobiography. He opined:
“I believe that the average farmer puts to a useful purpose only about 5% of the energy he expends … not only is everything done by hand, but seldom is a thought given to a logical arrangement. A farmer doing his chores will walk up and down a rickety ladder a dozen times. He will carry water for years instead of putting in a few lengths of pipe.”
For Ford’s farmer, recognizing the potential for process improvement and capital investment was key to better cost management. Today, however, identifying costs in manufacturing is far more complex. It involves an in-depth evaluation of every product cost element and its relationship to characteristics like form, fit, and function, alongside the process requirements for manufacturing, sourcing, and distribution.
Without advanced technology, no amount of study can rigorously estimate the complex interplay between engineering and business variables.
Costing Systems Technology: The Key Limit on Cost Estimation Speed and Quality
Manufacturers have continued to use successive waves of technology to try and capture at least a vague approximation of the complex variables aggregated in a product’s final cost. Better cost estimation techniques have always been tied to technological capability. For most of history, manufacturing cost estimation has been a matter of slow and steady experimentation.
Technologies from the personal computer to the enterprise spreadsheet made this experimentation more efficient and allowed for the consideration of more calculation-intensive variables. However, these traditional cost estimation procedures are always, at some level, vague and ad hoc. Complex variables are abstracted through practical (but ultimately imprecise) methods like comparing to similar past projects or assigning linear, per-unit costs to employed materials.
A collection of Excel spreadsheets for tallying component and labor costs is certainly better than resorting to overly simplified cost-plus pricing. But spreadsheet software doesn’t really begin to tie estimates to design-level decisions. That capability has only become accessible to manufacturers with the growth of manufacturing costing technologies that integrate engineering-level analytics with broader cost management concerns like supply chain, manufacturability, and labor costs.
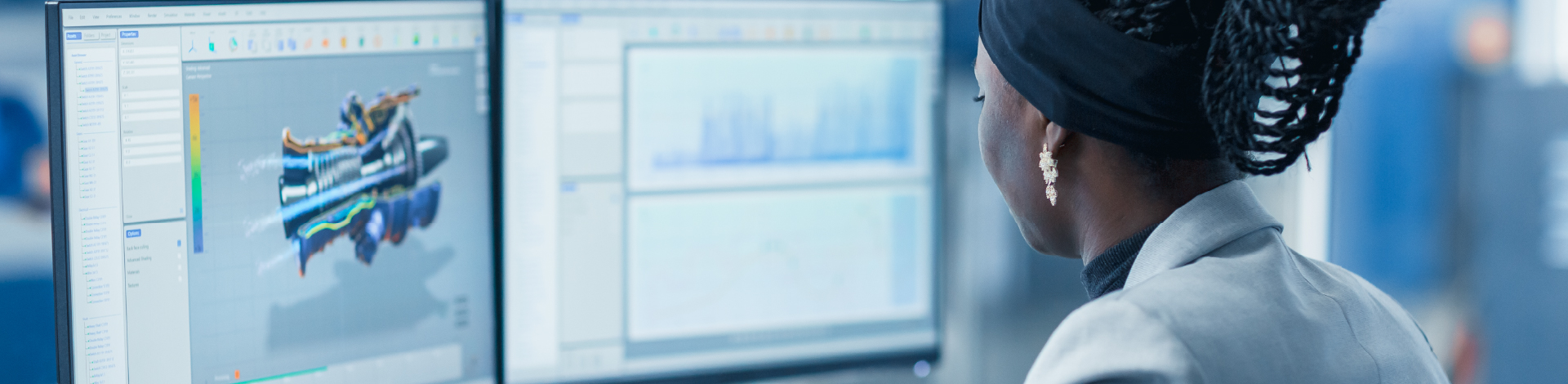
The Significant Rise of Manufacturing Cost Estimation Software
The success of innovative cost-reduction strategies like lean manufacturing is inexorably tied to successful manufacturing cost estimation. To determine which costs ultimately drive value, a manufacturer needs a platform to tie them to the functional features of a product design.
That’s precisely what the most advanced manufacturing cost estimation software can provide: a simulation-driven analysis of every aspect of a product’s cost structure. This analysis is available in minutes or less, giving designers actionable cost data on the anatomy of the product cost. This comprehensive accounting needs to include details like the cost of raw materials, material utilization, scrap buy-back, purchased parts/components, cost of tooling, labor cost, machine depreciation, and a wide array of indirect facility-related costs.
An advanced manufacturing cost estimation technology should include a role-based user experience that all key stakeholders in the product development process can leverage, including:
Product design engineers can create initial designs, evaluate iteration options to balance product performance and profitability, and gain visibility into the early-stage impact of design changes.
Procurement, sourcing, and supply chain professionals can obtain detailed cost breakdowns, identify cost outliers, and use this information to conduct fact-based negotiations with suppliers and reduce product costs.
Manufacturing cost estimators can evaluate and optimize costs throughout product development and manufacturing processes by acquiring detailed insights into cost drivers and production scenarios.
Project management can collaborate with other departments to align its design for manufacturability goals with the entire product life cycle team (despite the project scope). Additionally, managers can involve themselves throughout a project to analyze the data from the team’s work.
These complex analytical capabilities add up to a toolkit that doesn’t just make product cost estimation faster and more accurate (though the right software certainly accomplishes this) but also allows designers to explore robustly costed alternatives. In contrast, a product is still being designed. The ability to integrate dynamic, simulation-driven cost estimates with the design process itself allows manufacturers to transform the way they think about cost.
The right technology allows cost to be treated not as an ad hoc limit placed on product design but as an independent variable of the design process itself.
When simulation-driven estimation first became a technical possibility, it was only the domain of dedicated experts in computer-aided engineering. However, the market has seen rapid democratization of simulation, with providers like aPriori offering advanced cost estimation software that can be used by product designers and costing experts alike.
As this design-driven approach to cost estimation continues to advance rapidly into the daily practices of manufacturers worldwide, strategies founded on this capability are beginning to proliferate. The most important is design to cost.
Design to Cost (DTC): Bringing Robust Estimation Procedures Into the Design Process
Design to cost (DTC) is an organizational methodology that integrates cost management with decision-making during the early design stage, as explored in our article. The DTC approach moves away from conventional methods that rely on arbitrary cost-cutting targets. Instead, product managers collaborate with designers and engineers to establish a specific cost target for a new product introduction (NPI). This target is based on current market conditions and aims to maximize profitability.
Accessible within the software, this cost target enables designers to quickly generate new manufacturing cost estimates as they add a new layer of detail to the model, facilitating the identification and elimination of cost drivers. Consequently, this process allows the product team to achieve cost and profitability targets consistently with precision and confidence.
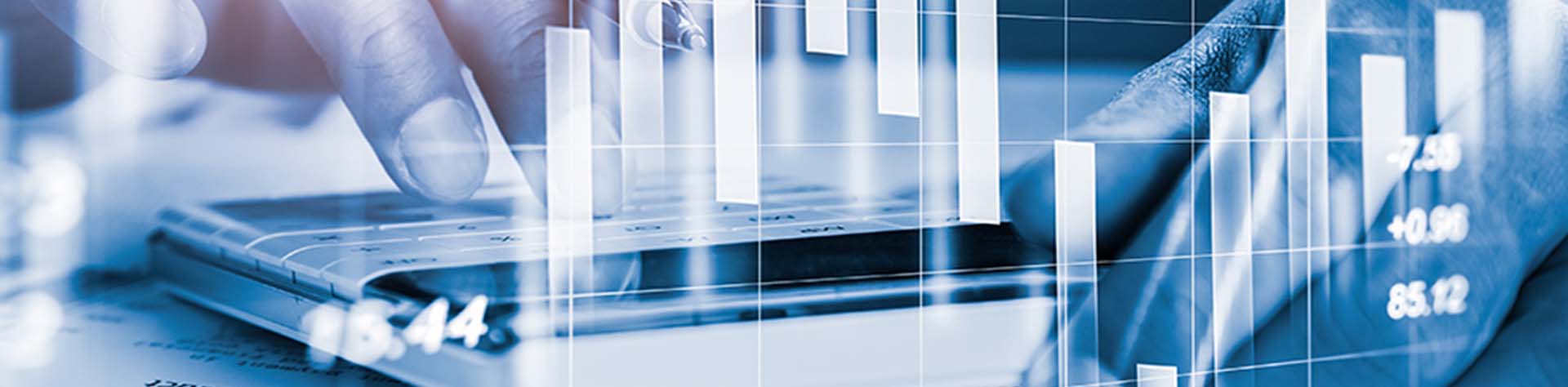
Understanding Product Cost Drivers
Considering cost as a true, fully quantified design variable is vital, as design decisions lock in about 80% of a product’s cost. This includes not only direct costs of specified materials but also a range of secondary costs.
While we divide these cost drivers into direct and secondary categories, the key to a robust cost estimation approach is recognizing and evaluating the complex interrelationships between them. For instance, selecting a more sophisticated machining process that requires outsourcing to a country with higher tariffs, but lower labor costs raises significant questions, including:
- Is this an intelligent business decision?
- Would altering the design to eliminate the need for this machining process enable the part to be manufactured locally?
Manufacturers today are grappling with such questions, which simple spreadsheet-type solutions cannot resolve.
Key Cost Driver Examples in Manufacturing
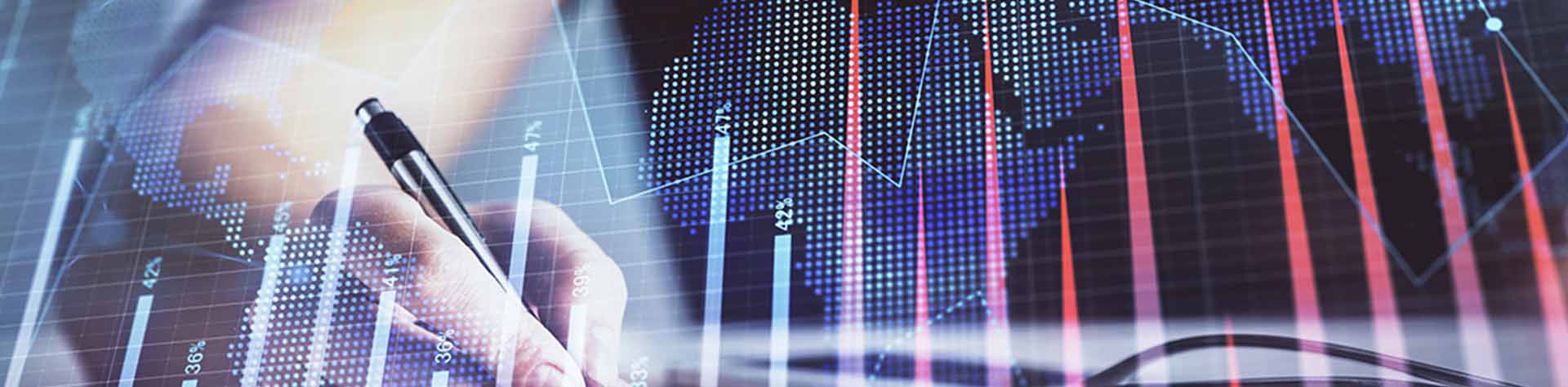
How to Successfully Estimate Product Costs
The first step in estimating costs involves evaluating current production parts to identify opportunities for negotiation or re-engineering to reduce product expenses.
This evaluation needs to generate benchmarks for what an efficient cost of a component should be. These benchmarks fall into two high-level categories:
Manufacturing costing systems accurately estimate the cost that a component “should” cost if it follows efficient manufacturing processes. While not every supplier is perfectly efficient, this analysis allows manufacturers to identify significant discrepancies between the current costs they pay and the should costs generated by their manufacturing cost estimation software. An inefficient supplier or a design flaw that drives excess cost may cause this discrepancy.
After identifying cost outliers, you can reduce them through redesign or renegotiation. Our article on manufacturing cost reduction explores a wide range of potential sources for savings.
The benefits of should cost analysis and estimation include the following:
- Identifying cost outliers and improving supplier collaboration to capture cost savings
- Generating internal estimates and quickly evaluating design and manufacturing alternatives rapidly
- Streamlining procurement operations with accurate estimates
- Prioritizing design iterations by applying cost outlier analysis
We also offer a more detailed guide for conducting a spend analysis.
As a high-level technique for identifying design inefficiencies, this approach generates an expected cost given a similar mass, material specification, and manufacturing process. If a component dramatically diverges from this expectation, it is more likely to employ unnecessary complex design choices.
Costing Systems Technology: The Key Limit on Cost Estimation Speed and Quality
To generate cost analyses during the design stage, your manufacturing cost estimation software must be extremely fast and easy to use.
With aPriori, for instance, the analysis begins by importing a 3D CAD file. After specifying a few basic inputs such as production volume, manufacturing process, and manufacturing location, aPriori can generate a comprehensive manufacturing cost estimate in seconds.
As changes are made to the CAD design (or manufacturing/supply chain selection), new estimates can be generated within a few seconds to ensure the design team is adhering to established cost targets. The ability to conduct rapid analysis of alternative scenarios using simulation-driven costing is essential for informing the design process without bogging down engineers. To generate the most cost-effective option, estimation platforms capable of analyzing every production process used in each potential routing are essential.
Product Cost Estimation Techniques: Comprehensive Tooling for Optimal Manufacturing Cost Analysis and Estimation
To provide this analysis, platforms like aPriori must include a comprehensive library of out-of-the-box (OOTB) manufacturing cost models. Moreover, the software should incorporate an extensive suite of Regional Data Libraries (RDLs), which encompass material libraries containing properties and costs, as well as machine libraries representing all the different types of machines used by manufacturing centers worldwide. These physics-based process models enable engineering, manufacturing, and purchasing professionals to explore cost-saving production alternatives down to the machine level.
A short representative list of manufacturing cost models available from aPriori OOTB includes:
Download our datasheet for the full list of models employed by aPriori.
The final ingredient in realizing the full value of the insights provided by your manufacturing cost estimation software is a culture shift toward a cost-conscious product engineering culture. Engineers are trained to think about functionality and reliability first, and design-stage cost management represents an added analytical complexity.
A willingness to rethink a product from the ground up is essential for generating the most impactful estimate.
For a comprehensive overview of our nearly 90 RDLs, download our datasheet.
Real-Life Examples of Product Cost Estimation
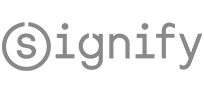
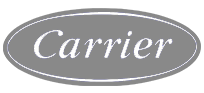
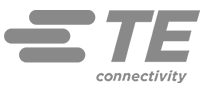
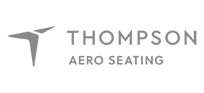
Increasing Should Cost Analysis by 8x to Digitalize Procurement
Signify is the global leader in lighting for consumers, professionals, and the Internet of Things (IoT). The company is dedicated to best-in-class procurement practices to ensure optimal cost, quality, and availability of components. To increase its capability in generating should cost analyses for products from external vendors, Signify recognized the need for automation.
The company partnered with aPriori to generate should cost models for mechanical parts, an approach that indicated the beginning of a successful digital procurement strategy.
Result(s): Using aPriori’s automation-driven platform, Signify achieved its goal of increasing should cost analysis by 8x, enabling it to optimize costs across a diverse product portfolio.
Gain more insight into how aPriori increases cost management performance and efficiency.
Below, we explore a few more real-life examples of product cost estimation excellence.
Saving Up to $30 Million in Critical Project Costs
Carrier manufactures products across three primary market segments: HVAC (both residential and commercial), refrigeration, and fire/security.
The company’s costing department initially implemented aPriori, but it has significantly evolved into a core technology across design engineering and sourcing.
Result(s): With the power of aPriori’s effective cost management platform and its role in driving substantial financial benefits, Carrier is projecting savings of approximately $30 million in critical product development projects.

Achieving Double-Digit Cost Reductions Through Informed Supplier Collaboration
TE Connectivity, a global leader in connectors and sensors, produces more than 236 billion products annually across the communications, industrial, and transportation sectors.
The company faced three main inflationary cost challenges in its supplier partnerships, including:
- Energy costs increased by 300%, leading to a 10% rise in a supplier’s machine rate
- Production costs rose by 30% over the past three years
- Labor and manufacturing quotes in a supplier’s country were 2x the regional average
To address these issues, TE Connectivity’s procurement team employed aPriori’s capabilities for accurate cost estimation and should cost analysis. This approach provided them with granular insights into a supplier’s total cost structure, facilitating successful negotiations for expense reductions.
Result(s): TE Connectivity managed to tackle each challenge with aPriori, leading to the following results:
- The 10% machine rate increase was deemed unreasonable, and it impacted the product cost by only 4%
- Negotiated a 15% reduction in raw material costs, offsetting the initial increase
- Strengthened its negotiation power, resulting in reduced labor and manufacturing costs

Analyzing Should Costs to Save 40% on Top-50 Most Expensive Parts
Thompson Aero Seating, specializing in premium airline seating for first—and business-class travelers, employs aPriori’s should cost analysis to determine the actual costs of its 50 most expensive stock machine parts. The company’s sourcing team leveraged these should cost breakdowns for productive discussions with suppliers.
Result(s): Within two months of adopting aPriori, Thompson Aero Seating reduced the cost of its top 50 priciest machined parts by an impressive 40%.
Next Steps: Toward a New Frontier in Manufacturing
The global manufacturing industry is only beginning to tap into the full potential of modern cost estimation technologies. As these technologies become more prevalent, market leaders who effectively leverage them will likely add cost and pricing pressure on their competitors. We can expect product manufacturing to remain highly competitive in the foreseeable future: overlooking any opportunity for cost optimization is a potential threat to market share.
It is crucial to select the right manufacturing costing software to navigate this market and generate actionable cost estimates at the speed demanded by today’s customers. For more insights into the vital features of a cost management platform for maximum business impact, check out our article on the key functionalities to look for in cost estimation software.
aPriori Provides Actionable Insights for Better Manufacturing Cost Estimation
aPriori partners with manufacturers to integrate simulation-driven cost estimation into their design process, enabling organizations to manage costs independently. The platform enhances manufacturing visibility and allows for real-time “what-if” scenario assessments to identify cost-effective suppliers, materials, and production methods.
aPriori provides actionable insights and detailed data, ensuring that forward-thinking manufacturers achieve product excellence through effective manufacturing cost management.