Unlock the Secrets to Accelerating Manufacturing Cost Reduction
Key Takeaways:
- Conventional manufacturing cost estimation often misses the mark due to outdated information, cumbersome manual processes, and bottlenecks
- Digital manufacturing insights provide real-time data, detailed analysis, and the scalability to increase profits
The Full Article:
Product development teams face the challenge of designing and sourcing their products to maximize profit margins before new competition or market changes emerge.
This is especially challenging for manufacturers that produce relatively low-volume products with high part counts. Alongside meeting these marketplace demands and innovating rapidly, organizations need to provide a competitive price point, enabling them to beat the competition and capture a large revenue share.
By leveraging the following estimation approaches, you can streamline your manufacturing process while reducing costs.
Surface-Level Costing Could Impact the Bottom Line and Time-to-Market Outcomes
Many manufacturing businesses use traditional costing methodologies to identify savings opportunities. A popular approach is to assess the bill of materials (BOM) for products with the most expensive components or parts that have long lead times. However, this strategy only scratches the surface, leaving the bulk of potential reductions invisible to the manufacturing team at large.
Beneath the surface of traditional cost models lies critical issues that may not become apparent until the late-stage production process. This can result in the production of lower quality products, running Initial production products at a loss, or comprising time to market (TTM).
The limitations and inefficiencies of traditional costing processes include:
- The lack of precision needed to optimize early design-stage product costs, particularly down to the level of component optimization.
- The challenges of sourcing requirements across an increasingly complex portfolio of materials, components, and suppliers across the globe can cause delays or bottlenecks.
- Having updated current data to understand current “should costs.” For example, should you still be paying a premium for a material, or has there been a market correction/cost reduction?
- Manual data entry errors are common, making manufacturing cost forecasts inaccurate. Tools like spreadsheets offer limited collaboration capabilities, which prevents meaningful cross-functional collaboration.
Digitalize to Modernize Your Manufacturing Company’s Costing Strategies
Digital manufacturing simulation software, such as aPriori, provides real-time and actionable insights for the entire product definition. It helps forward-thinking manufacturers identify cost, manufacturability, and sustainability issues early in the critical design process, enabling them to make informed redesign decisions.
Product development teams can use the technology’s automation and data analytics to pinpoint opportunities for design and production optimization quickly. Having these insights from the outset equips teams with the knowledge needed to avoid late-stage and expensive engineering change order (ECO) requirements. These opportunities can then be presented to program managers, engineering professionals, and other project stakeholders focused on cost and TTM improvements.
This approach not only identifies outliers but also provides relative information surrounding those outliers, bringing the exponential value of component cost reductions into focus at scale.
So, how does aPriori provide valuable insights and improve collaborative decision-making? The following provides some insight into this question:
- aPriori automatically analyzes the geometry of 3D computer-aided design (CAD) models to provide real-time cost data for parts and sub-assemblies. Product design and cost engineers can immediately simulate and gain insights or have an automatic evaluation when a CAD model is checked into the company’s product lifecycle management (PLM) system. To learn more about how aPriori analyzes CAD model geometry, check out our webinar, “Excel to Excellence: Revolutionizing Cost Engineering with 3D CAD Precision.”
- aPriori’s manufacturing insights contain information on manufacturability, net weight, and carbon footprint. This supports cost reduction decisions without compromising carbon footprint or product quality as well as enabling business-critical cost and carbon trade-offs.
- aPriori provides configurable digital factories containing nearly 90 Regional Data Libraries (RDLs) and various physics-based Manufacturing Process Models (MPMs) to generate precise estimates rapidly. Moreover, companies can conduct multiple “what-if” scenarios and evaluate the cost-effectiveness of alternative designs, raw materials, suppliers, and manufacturing operations.
- With aPriori’s digital twins and the digital thread, manufacturers can break down silos across their product development teams.
- Companies can use aPriori’s real-time collaboration application, aP Workspace, to connect all stages of the product life cycle through a single platform. By accessing aP Workspace’s centralized manufacturing data, teams can communicate and make rapid, data-driven decisions to increase product cost efficiency.
Scale Manufacturing Cost Reduction with Design for Manufacturability
Value engineering traditionally targets cost reductions that are not identified during new product development. Digital manufacturing simulation software, such as aPriori, provides a more granular approach to evaluating product cost structures. This software enables teams to analyze underlying expense drivers and includes design for manufacturability (DFM) insights into manufacturers’ configured digital factories.
By incorporating robust DFM feedback into their products, teams can eliminate excessive costs from the outset, resulting in greater savings over time. Further, adopting a DFM approach not only improves profitability but also helps manufacturers maintain product quality.
This underscores the importance of adopting a DFM approach to promote a PLM culture and improve the cost-effectiveness and manufacturability of product design.
Should Cost vs. Quoted Cost or Actual Cost
Plotting component quotes can help sourcing teams identify cost outliers and prioritize the parts that significantly affect expenses. This standard practice can lead to considerable manufacturing cost reductions.
However, what if you plot the should cost and quoted cost on a single chart? You can still see the outliers for standard manufacturing cost reductions, and you also gain more insight – such as where quoted cost and should cost are out of sync.
The Value of Should Cost and Transparency
When the should cost is much lower than the actual cost, creating a strong partnership and having an open, transparent discourse with suppliers can go a long way. By doing so, you can capitalize on opportunities to lower costs in manufacturing, and you gain the key insights needed to make conversations with providers (suppliers) productive.
However, what happens when the should cost is much higher than the quoted cost? You may initially believe that you are getting a great price, but there might be something about those parts that are driving down the cost in the supply chain. Two factors could be at play here: it could be the supplier’s desire to win your business, or the supplier could have a more efficient process. While the former is always a benefit, the latter creates an “ah-ha” moment where an original equipment manufacturer (OEM) can capitalize on supply chain and manufacturing process optimization opportunities.
Cost Thousands of Components Faster and More Accurately
Imagine that in today’s manufacturing industry, the average cost engineer is responsible for estimating thousands of components. As the market continues to demand higher levels of innovation and faster TTM, the traditional methods of cost estimation are no longer feasible. There is not enough time to uncover the full cost burden of products using conventional methods.
This is where aPriori comes in: cost engineers can use aPriori’s bulk costing module to generate automated, precise estimates at scale to keep pace with more requests. This capability enables costing teams to quickly uncover cost-cutting opportunities for multiple products simultaneously, influencing cost-effective sourcing decisions and accelerating TTM. Full automation can be achieved through PLM integration, where every component will be analyzed for cost, carbon, and manufacturability at any predetermined stage of the component and product life cycle.
Real-World Manufacturing Cost Reduction Examples
In collaboration with IndustryWeek, our State of Manufacturing Procurement survey found that 71% of manufacturers with annual revenues of $100 million consider modernizing cost-reduction analysis important.
Top manufacturers are realizing significant savings by digitalizing their sourcing and procurement capabilities. For instance, the following organizations have implemented aPriori’s robust manufacturing cost reduction capabilities to achieve these savings:
- CNH Industrial identified $312,000 in annual savings within the first two months of using aPriori.
- Carrier used aPriori to evaluate multiple components, driving over $20 million in value.
- Nikola captured tooling cost savings of up to 30% with aPriori.
Optimize Your Cost Efficiency Through Automated Cost Management
Automating costing approaches and integrating them with PLM systems is crucial in today’s manufacturing environment. Digital manufacturing simulation solutions like aPriori provide real-time analysis and metrics, enabling proactive cost reduction and fostering collaboration between cost, design, procurement, and external suppliers.
Moreover, embracing DFM and should cost analysis further optimizes cost structures, leading to increased efficiency and profitability for forward-thinking manufacturers.
This post was originally published on Feb. 3, 2021, and updated on May 7, 2024.
A Guide to Manufacturing Cost Estimation
Discover how to streamline manufacturing cost reduction and boost profit margins.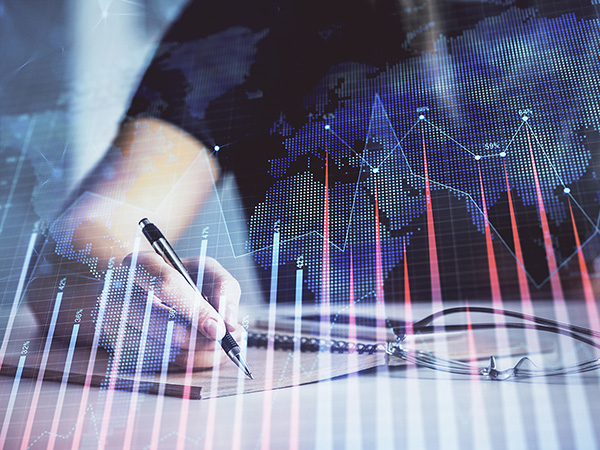