How The Digital Thread Ties Design, Sourcing, and Manufacturing Together
Key Takeaways:
- Manufacturers are applying digital thread and digital twin capabilities to gain speed and insights
- The digital thread can eliminate bottlenecks and costly delays by connecting digital twins across product development, sourcing, sustainability, and manufacturing
The Full Article:
If you ask 10 manufacturing executives to define “digital transformation,” you’ll likely get 10 different answers. Fortunately, a strict definition for digital transformation or Industry 4.0 isn’t as important as how manufacturers execute strategies to reach their business goals and measure their successes. Manufacturers that execute digitalization effectively can bolster productivity and profits, accelerate time to market, and strengthen supply chain resiliency.
At its core, digital transformation provides a technology and data foundation that is interoperable, scalable, and has the agility to support business needs today and in the future. And like any new approach, it requires the right executive leadership, people, processes, and employee buy-in to succeed.
Digital transformation isn’t monolithic: it includes multiple capabilities that must work seamlessly together to drive business value. If one digital transformation capability isn’t working efficiently or isn’t aligned with the others, it stalls the entire business process. For example, spreadsheets and custom systems contain siloed data that can’t be integrated automatically into business systems – and isn’t part of a digital thread.
How the Digital Thread Connects Digital Twins to Growth and Innovation
From our perspective, digital transformation for manufacturing includes four key areas across the product development ecosystem. Understanding the value, role, and opportunities for each pillar can help to align new capabilities with prioritized business needs:
1) aPriori Digital Product Twins refer to 3D CAD models or virtual representations of physical products that include components and assemblies, along with overall product size and shape. It serves as the design optimized via simulation and additional modifications. It becomes the framework to analyze the current product design, using simulation to see how design changes will affect sustainability, cost, and manufacturability. Discover how Carrier saved millions with aPriori’s digital product twin.
2) aPriori Digital Process Twins determine the most effective way to manufacture a product by simulating manufacturing processes and routings (e.g., injection molding and additive manufacturing). aPriori’s physics-based manufacturing process models allow engineering, manufacturing, and purchasing professionals to explore production alternatives down to the machine level. Companies simulate manufacturing processes using the digital twin to identify the most appropriate production process for cost, sustainability, and manufacturability. Learn how AGCO used aPriori’s digital process twin to gain manufacturability and cost insights in just a few clicks.
3) aPriori Digital Factory Twins represent physical factories. This virtual model includes precise factory-specific production capabilities along with detailed costs – including labor, electricity, materials, and overhead rates in 87 regions globally. Manufacturers use digital factory twins to help evaluate their supply chain CO2e across the value chain (Scope 3) by creating a virtual representation of supplier factories and their own manufacturing locations. Get a glimpse into how AGCO built an internal digital factory, covering processes and routings, configurations, and production.
4) The Digital Thread ties together multiple digital twins and data from related digitalization applications (e.g., finite element analysis [FEA] software). It connects the digital twin and product information including sourcing, manufacturing, and field service data. And, it can extend business processes across traditionally distinct operations (e.g., product design and sourcing). Read how to accelerate product sustainability with digital twins and the digital thread.
How the Digital Thread Connects the Entire Product Development Team
Digital transformation’s value is largely determined by the digital thread: how organizations connect departments and operations, and use information to make decisions rapidly. Manufacturers that weave a digital thread throughout the product development lifecycle can connect the digital twin to data from the physical world – including manufacturing capacity, supply chain sourcing and cost information, field service reports, and other operations.
The digital thread’s closed-loop process provides a single, reliable source of information that stakeholders can use to make informed decisions. This enables teams to work faster and more efficiently by using updated digital product information.
As an example, cost engineering teams can review early designs and make recommended updates to address manufacturability and other issues. And once engineers update a CAD model, sourcing can immediately use the revised specifications to secure updated quotes.
And field data can inform design updates, such as a service team identifying a performance issue when the product is deployed in a high-temperature environment. Or, usage data from connected products deployed globally may reveal that a current product motor is underutilized and can be replaced by a less-powerful, less expensive alternative without affecting performance.
The Power of End-to-End Digital Twins
aPriori automatically extracts geometric data from 3D CAD files checked into product lifecycle management (PLM) systems. The solution leverages the 3D data and connects three digital twins—product, process, and factory—to generate precise carbon, cost, and manufacturability breakdowns.
aPriori digital factories are fully configurable and can simulate real-world production based on a product’s design (geometry), raw materials, energy consumed, machines available and manufacturing processes, overhead rates, and more. aPriori delivers these insights using real-world production process groups and economic conditions for 87 global regions.
Importantly, digital twins empower manufacturers to extend their existing PLM investments to innovate rapidly and increase their profitability. And because product manufacturing teams can maintain their typical workflow, companies can realize a high return on their investments quickly.
5 Keys to a Strong Digital Thread
The digital thread can deliver added value by enabling automation, extending business processes among departments, and providing updated business data to make informed decisions. Here are five keys for manufacturers to consider as they establish an effective digital thread.
1. Connect Stakeholders to Increase Productivity and Profits
Establish a “central source of truth” for product manufacturing that draws from critical systems and then uses the digital thread to connect performance and manufacturing data between the digital twin and downstream applications (e.g., design engineering, sourcing, manufacturing partners, etc.). Removing department silos enables product teams to design and validate simultaneously and collaborate with their cost engineering and sourcing counterparts to ensure that products are manufacturable, and meet target costs, and production deadlines.
2. Simplify and Accelerate Operations with Automation
Automation plays an important role in increasing efficiency and reducing operational complexity. Incorporate automation in design for manufacturability (DFM) and manufacturing cost analysis. Use rules, roles, and triggers to alert groups/teams to take action, generate reports for senior stakeholders, and more. Manufacturing examples can include:
- Identify components for re-design or re-quote with high-cost impact
- Identify outliers with manufacturability issues
- Alert stakeholders of specific high-risk part designs for immediate review
3. Improve Planning with Fact-based Insights
Effective strategic planning requires the ability to draw from information, including robust product data, detailed manufacturing cost models, and regional supplier libraries. Executives can use this data for planning and analysis scenarios such as:
- Evaluate the viability of using a replacement material to circumvent supply chain delays
- Examine how various manufacturing processes will affect production cost and availability
- Conduct matrix costing to compare regional manufacturing costs differences by labor, materials, overhead, equipment/facility rates, and profit margin
- Consider other what-if scenarios to plan for potential market changes
4. Use Digital Factory Simulation to Optimize Manufacturing
Dynamic fluctuations in material prices, regional manufacturing costs, and supply chain roadblocks make access to current information essential. Because ERP systems contain historical pricing information, they only provide directional insight. Updated materials and manufacturing pricing provide sourcing teams with data-driven insights to identify cost savings and meet production targets. An optimal digital representation of a physical factory includes:
- Regional data libraries: Provide an extensive collection of data to calculate manufacturing costs and run scenarios for production in multiple geographies.
- Manufacturing cost models: Research cost-saving production alternatives through cost model simulations in minutes.
5. Improve Supply Chain Agility (and Reduce Risk)
Reduce the time and expense associated with bid and proposal development. Manufacturers can accelerate procurement via a collaboration engine to understand suppliers’ granular manufacturing costs and capabilities. Digital factories can also help streamline the quoting process itself. For established manufacturer-supplier relationships, the sourcing model can be refined to support a “zero-RFQ” process where manufacturers issue a purchase order for a design without waiting for a quote at all. Read how rail transportation manufacturer Alstom dramatically improved its sourcing process by implementing a Zero-RFQ process.
Develop a Strong Digital Thread for Measurable Success
More than 80% of CEOs plan to increase their investments in digital transformation, according to a 2021 survey from industry analyst firm Gartner. While this reflects urgency in gaining new capabilities and curtailing costs, it’s unclear how successful these efforts will be. The Keenfolks, a consulting firm, reports that nearly three-quarters of organizations are struggling to calculate the ROI of their digital transformation spend.
Manufacturers have a clear opportunity to cut costs and time to market by aligning product design closely with procurement and production. Digital transformation initiatives that use the digital thread to connect departments have an opportunity to realize quantifiable benefits quickly. Digital transformation initiatives can provide teams with real-time insights that drive effective decision-making for new product development and value engineering projects. Organizations can measure success by evaluating new smart manufacturing capabilities enabled and how extensively they are used throughout the enterprise via the digital thread.
Frost & Sullivan Names aPriori the Digital Manufacturing Solutions Leader
Get the full story.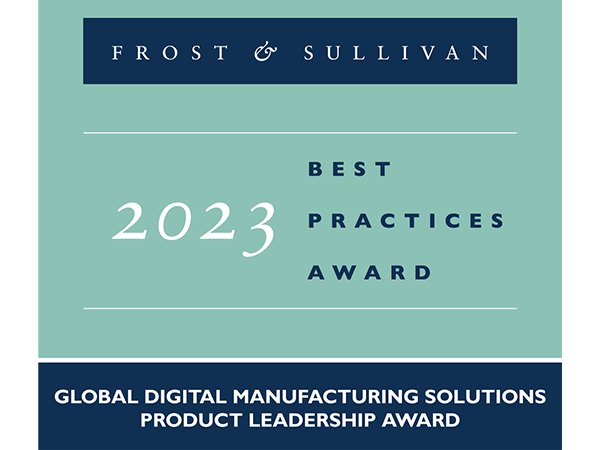