Case Study
Design-Stage Cost Insight Drives Speed and Savings for CNH
Introduction
For time-sensitive product development cycles, reducing the number of loops between design, cost, sourcing, and manufacturing teams is critical to reducing time-to-market.
In this case study, we explore how CNH Industrial used aPriori to speed up its development process. Their experience shows how bringing detailed cost analysis capabilities into the design stage not only saves time but also opens up new opportunities for strategic cost management.
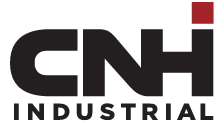
Company Details
Industry
Agricultural Equipment
Number of Employees
60,000
Revenue
$25 billion
Website
aPriori Product
aP Pro; aP Design; aP Generate; aP Analytics
The Problem
Identify Cost Reduction Opportunities for a Time-Sensitive Product Design CycleThe Solution
Use Digital Manufacturing Simulation to Standardize Manufacturability and Cost ModelingWho is CNH?
CNH Industrial is a world-class equipment and services provider that supports agriculture and construction work across the globe through respected brands such as Case and New Holland. A truly global operation, CNH employs 60,000+ people across 67 manufacturing plants and 56 research and development centers distributed across 180 countries.
Problem: Identify Cost Reduction Opportunities for a Time-Sensitive Product Design Cycle
CNH needed a tool that could help align designs to cost targets during the initial design phase – before designs are finalized – or even worse, in testing. Catching cost issues early would greatly reduce the risk of needing to circle back to redesign. The right tool would need to fit into a time-sensitive development cycle, providing detailed cost and manufacturability insights without slowing down designers’ ability to iterate quickly.
CNH Industrial’s cultivation equipment group in North America selected aPriori as a promising solution to fulfill these needs (with the potential to be put to much broader use in CNH’s global organization).
Solution: Leverage Digital Manufacturing Simulation to Open Up New Cost Management Possibilities
aPriori’s rollout began with a small pilot project, where a team of three design engineers began leveraging the software to generate fast feedback on cost and manufacturability issues, catching cost issues early in the design process.
Design-stage digital manufacturing simulation with aPriori is far faster and less time-consuming than using traditional tools like spreadsheets to estimate costs.
CNH engineers also report that aPriori provides an excellent avenue for validating the work of new engineers with limited design experience while developing their skills by highlighting specific opportunities for cost optimization. In the past, design-stage cost management relied on rules of thumb and personal experience. With the digital factory as a virtual training ground, this knowledge can be retained, organized, and transferred to a new generation of engineers.
Results: $312,000 in Annual Savings Identified with the First Two Months
Within the first two months of adopting aPriori across a single small harvester design team, CNH engineers identified substantial savings opportunities across a number of components. Design changes to a shank cultivator were able to save $143,820 alone in annual costs. The identification of excess internal manufacturing costs for turnbuckle design led to a redesign and outsourcing that drove savings of $97,659.
Their total within just a few months of adopting aPriori? $312,000 in annual savings.
Accelerated cycle times for cost analysis can help speed up time-to-market, but they also open up many more strategic possibilities for bringing down costs. Because design engineers receive immediate feedback, they can explore alternatives early in a project, when there is still time to consider design alternatives, sourcing options, and make-buy economics.
This highly successful pilot project has paved the way for the use of aPriori across more and more of CNH’s global operations since the software’s initial adoption in 2019. As of late 2022, nearly 900 users were making use of aPriori, a key part of CNH’s continuing pursuit of a world-class engineering vision. As the use of digital manufacturing simulation moves beyond small teams and spreads throughout this global organization, it provides added value in unifying cost modeling methodology between different plants, regions, and countries.
Learn more about how CNH’s harvesting group began leveraging aPriori in this presentation recorded during an aPriori Insights Conference:
Expanded use of aPriori extends beyond designers; sourcing teams can also leverage the manufacturing data gleaned from aPriori to bring down costs for purchased parts. CNH leverages granular data on the should cost of parts to initiate constructive conversations with suppliers. While a given supplier cannot always match the optimal price identified in aPriori, a detailed estimate provides a robust foundation for conducting fact-based negotiations that center on why a given supplier’s costs are higher–and how they can be brought down.
Learn more about how aPriori can help model should costs in our guide here.
Hear more about how about the relationship between CNH and aPriori in this podcast episode between aPriori’s Leah Archibald and former design engineer and now cost reduction leader for CNH, Jegan Dhanapal.
Experience aPriori in Action
Meet with an aPriori expert and learn how we can help you to eliminate product costs, improve productivity, and reduce your carbon footprint.