Case Study
How AGCO Streamlines Manufacturability Analysis with aPriori
How can engineers generate accurate cycle time models for parts without slowing down design work (and therefore delivery time) for made-to-order agricultural products?
In the past, this work has relied on tools like spreadsheets, which are non-standardized, lack traceability, and often rely on experience-based models that cannot be easily replicated across different manufacturing processes and facilities.
In this case study, we look at how AGCO’s GSI division leveraged aPriori’s digital factories to standardize manufacturability analysis, with usage now expanding to automated, large-scale cost modeling via seamless PLM integration.
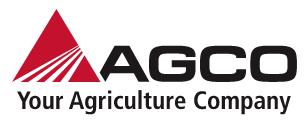
Company Details
Industry
Agricultural Equipment
Number of Employees
23,500
Revenue
$11.14 billion
Website
aPriori Product
aP Pro; aP Generate
The Problem
Standardizing Manufacturing Cycle Time Analysis for Made-to-Order Agricultural EquipmentThe Solution
Use Digital Manufacturing Simulation to Standardize Manufacturability and Cost ModelingWho is AGCO?
Agco is a farmer-focused company that develops a variety of products that help feed our world. They offer a diverse range of market-leading agricultural equipment including tractors, combine harvesters, and smart software solutions that help optimize everything from planting seeds to equipment maintenance. AGCO maintains an extensive global operation, with brands like Challenger, Fendt, GSI, Massey Ferguson, and Valtra.
Problem: Standardizing Manufacturing Cycle Time Analysis for Made-to-Order Agricultural Equipment
The GSI division at AGCO offers a range of integrated grain systems designed to maximize yield across the end-to-end process of grain storage, conditioning, and handling. GSI’s grain bin products are sold via a digital catalog, with users able to select custom product features and dimensions. The product is subsequently custom-engineered for each order.
In the past, cycle times for this process were managed using individual spreadsheets. The GSI accounting department recognized that cycle times being identified in business/MRP systems were not necessarily being replicated on the shop floor. These discrepancies made projecting labor time and cost in the factory difficult, and GSI needed a method for standardizing manufacturability models to be more repeatable, accurate, and precise for this made-to-order product. The ideal solution needed to provide flexible, customizable manufacturability analysis without impinging engineers’ ability to quickly begin work on new customer orders.
The GSI team discovered aPriori as a promising solution and was happy to learn that the software was already in use at AGCO.
Solution: Configuring a Digital Factory to Match the Shop Floor
aPriori was introduced to AGCO in 2007, first to its manufacturing groups in Kansas and Minnesota. By 2009, their implementation expanded to global should cost work for new products in Brazil and Italy. Today, AGCO maintains about 120 aPriori licenses. These early successful deployments elsewhere in the AGCO organization allowed the GSI group to move forward confidently with aPriori as a tool for cycle time analysis and beyond.
GSI began building out a digital factory designed to model their own manufacturing capabilities. This process began with a walkthrough, with AGCO engineers identifying each machine used on the shop floor, the time needed for each process, and how parts were routed to the next workstation. This knowledge-gathering work was iterated for each manufacturing process and facility at GSI. This initial data was used by AGCO’s expert services team to configure a custom digital factory.
Learn more about the aPriori digital factory and how it works.
Results: How the Digital Factory Helped GSI Move from “Black Box” Spreadsheets to Synchronized Cycle Times
Before implementing aPriori, the GSI group relied on spreadsheet files with no auditable trail for cycle time analysis. Now, aPriori provides a standardized solution–any user analyzing the same part, anywhere across the globe, will arrive at the same cycle time result (which has been carefully configured to closely match the reality on the shop floor).
The GSI team is now expanding the use of aPriori to automated costing applications. Using the digital factory, GSI can rapidly simulate manufacturing for thousands of older parts. This ensures that factory KPIs are based on updated, verified models while helping the organization continue to standardize its full portfolio of components using the digital factory.
aPriori is also increasingly leveraged by GSI’s design engineers. Because GSI’s products are engineered to order, product cost targets have been high-level, without component-by-component cost breakdowns. Simulated manufacturing in the digital factory allows design engineers to focus their efforts on components with substantial manufacturability or cost issues, without wasting time optimizing components that are already efficiently designed.
Looking forward, GSI design engineers will employ aPriori earlier in the design process, where simulated manufacturing can be used to rapidly model the cost delta between high-level design choices. Direct integration with AGCO’s PLM system (Windchill) allows design engineers to submit parts to aPriori using just a few clicks with AP Generate, which simulates manufacturing in the background and e-mails a manufacturability report.
Learn step-by-step how to build a digital factory from aPriori from AGCO super-users . In the following video, you’ll get insight into how AGCO was able to build an internal digital factory that covers everything from processes and routings, configurations, and production:
Experience aPriori in Action
Meet with an aPriori expert and learn how we can help you to eliminate product costs, improve productivity, and reduce your carbon footprint.