4 Ways Digital Twins Transformation is Reshaping Manufacturing
Key Takeaways:
- Manufacturers are using digital twins to improve productivity, mitigate market uncertainties, create more agile supply chains, address labor shortages, and meet sustainability goals
- Digital twins transformation can achieve millions of dollars of manufacturing cost savings
- Improving product manufacturability ensures faster time to market and revenue/market share growth
The Full Article:
Can digital transformation create tangible value? For many executives, their expectations are falling short. The Harvard Business Review reveals that 89% of large global companies are implementing digital transformation (DX) and artificial intelligence (AI) initiatives. However, just 31% and 25% captured expected revenue lift and cost savings, respectively. How can manufacturers retool their efforts to gain faster, seamless adoption, and meet critical revenue and savings objectives?
By leveraging digital twins on a wider scale, manufacturers can enable digital transformation – via a highly strategic approach – to scale faster for a more tangible impact. Matching digital initiatives with changing business processes empowers manufacturers to:
- Deliver more accurate estimates on cost and CO2e reductions
- Improve efficiency and productivity
- Drive faster collaboration between teams
- Transform supply chain management
- Innovate fast to out-compete the competition
- Execute at digital speed
During my keynote at our recent Manufacturing Insights Conference, I explored how the following aPriori customers have mitigated risks by leveraging digital twins in their business transformation and, in the process, optimized their business in ways not possible without digital manufacturing solutions.
Risk Driver #1: Improving Productivity and Efficiency During Uncertainty
The International Monetary Fund (IMF) expects global economic growth to slow to 2.9% in 2024. This downward movement is largely due to supply chain issues, and increased material and energy costs.
aPriori customers Flex and Signify are examples of how leveraging digital twins can improve productivity and efficiency, lessening the associated risks.
Flex uses digital factories to address supply chain/material cost fluctuations. The company was using various processes across the organization to manually quote. With aPriori’s digital twins and digital factories, Flex gained consistent, simulation-driven, and accurate global cost models, reducing price fluctuations and winning more business. With a streamlined, centralized quoting process across the organization, Flex introduced a mechanical products RFQ pilot project in Mexico. Two years later, aPriori was implemented at other Flex sites, including in China, Europe, and Malaysia. The entire organization now has access to aPriori’s digital factories. Consequently, time-to-quote was decreased by 35-80% in its locations. Flex’s overall RFQ win rate also improved from 15% to 68%. Flex reduced the time to generate a bill of materials (BOM) from three days to just 30 seconds.
Signify needed to create value at scale to pioneer innovative breakthroughs. However, global and market uncertainties and disruptors tested this objective. Signify focused on driving more automation for procurement to boost supplier innovation and cost efficiency. Their sustainability teams worked cohesively via a single standardized, automated methodology to quote more than 10,000 parts annually across the entire organization. Should cost and quoting clarity and consistency through aPriori boosted productivity and lowered costs for the company.
Risk Driver #2: Building Resilient and Agile Supply Chains
The pandemic, global conflicts, and inflation continue to impact manufacturers. Supply chains have been affected and remain a major concern for more than three-quarters of CFOs. Building more resiliency into sourcing and procurement is critical.
Kearney cites 96% of CEOs are evaluating reshoring, will reshore, or have already reshored their operations. It is an increase from 78% in 2022. Manufacturers recognize that their supply chains should not be overly reliant on a single country or region for manufacturing. North American companies are starting to move manufacturing or supply chains to closer locations such as Mexico.
Pan-European and Asia-Pacific organizations are looking to Eastern Europe and Malaysia, respectively, to service those regions. With many moving parts, a supply chain move requires careful evaluation. You might lower transportation costs by choosing suppliers closer to your operations. However, labor costs there might be higher. Digital factories efficiently facilitate this process of evaluating supply chain or manufacturing moves, providing accurate, detailed data to make more informed decisions faster.
Eaton uses digital twins and digital factories to build a resilient supply chain for EV products. The company streamlines cost engineering and should-cost to scale its manufacturing operations. Cloud applications enhance their ability to collaborate and collect data more efficiently. Eaton uses aPriori to scale and add supply chain resilience. It also helps them understand a design’s impact on manufacturability, sustainability, cost, and sourcing. Eaton increased productivity dramatically, reduced design iterations and costs, decreased RFQ response times, and accelerated time to market.
Risk Driver #3: Tackling Labor Shortages Requires Complementary Recruiting Strategies
Forbes notes there was a shortage of nearly 600,000 stable US manufacturing jobs as of June 2023. By 2030, it is expected to climb to 2.1 million. Nearly 70% of European employers suffer similar shortages, citing the surge in older workers exiting the workforce. These shortages impede productivity and stagnate growth. Automation can compensate for shortages, eliminating manpower for manual tasks and enabling accelerated innovation. These new technologies also attract a larger talent pool and enable upskilling, ensuring higher retention rates. Digital twins transformation allows manufacturers to do more with less. Collaboration is more effective and drives product price performance including design cycle optimization.
Woodward optimizes business processes and addresses labor shortages with digital twins transformation. With a very large, complex global supply chain to manage, and 75% of US machinists aged 45 or older, Woodward needed to retool operations to remain competitive. It underwent a three-pillar approach to digital transformation:
- the use of COBOTs (collaborative robots safely working and interacting with humans) to support labor,
- sourcing from emerging countries and key supplier digital partnering, and
- digital factory simulation representing suppliers’ capabilities, capacity, and cost structures.
Woodward improved its supplier collaboration, decreased quoting times to one-tenth of the previous process time, and reduced procurement labor requirements. Digital twins transformation enabled product development acceleration and production without sacrificing quality or profitability. Suppliers also benefited by reducing quoting iterations. In one case, a supplier was able to reduce quoting staff from five people to one, enabling the other four to return to the factory floor to focus on more pressing functions.
Risk Driver #4: Sustainability is Disrupting Manufacturing
Sustainability is driving major changes in manufacturing. In 2024 alone, KPMG notes that nearly 50,000 companies will be subject to sustainability reporting including non-European Union companies and those with subsidiaries regulated by the Corporate Sustainability Directive (CSRD). Rigorous data reporting and disclosures are required along with disclosure of hundreds of metrics and targets. Moreover, these regulations could impact product pricing due to the carbon border adjustment mechanism (CBAM). Some believe the price of materials could increase by as much as 30%. (Learn how manufacturers are addressing the EU’s CBAM “carbon tax.”)
Though lifecycle assessment (LCA) tools can help address sustainability issues by consolidating and reporting data on a complete product, they don’t provide proactive, actionable insights to reduce design or manufacturing’s carbon footprint – let alone ensure manufacturers remain competitive and profitable. Digital twins optimize product competitiveness and profitability while lowering CO2e emissions. In the process, manufacturers can transform their operations and gain a competitive advantage.
Carrier has very successfully used aPriori not only to meet ESG goals but also realized more than $21 million in annual savings. The company set a goal to reduce customers’ carbon footprint by more than a gigaton by 2030. However, Carrier hit a speed bump when suppliers wouldn’t share the data necessary to run the sustainability calculations. That’s where aPriori came in. Carrier was able to access manufacturability, CO2, and cost data, using digital twins to make informed decisions about product design, materials, and manufacturability. They also accelerated their time to market with more sustainable innovations. Consequently, Carrier uses aPriori to analyze CO2e impacts and accelerate Environmental Product Declaration (EPD) certification by 33%.
Digital Twins Transformation Mitigates Risk and Accelerates Growth
Focused strategic initiatives leveraging digital twins are essential to enabling digital transformation. In addition to our customer success stories, consider this: Deloitte analyzed 10 years of financial disclosures from more than 4,000 global organizations. It found that the right combination of digital transformation actions can unlock as much as $1.25 trillion in additional market capitalization across all Fortune 500 companies. It also increases productivity, market position, and value. Deloitte confirms that the success of these goals hinges on:
- Digital transformation alignment with a corporate digital strategy
- Both digital transformation and the corporate digital strategy need the organization’s support to ensure the adoption and adaptability of new processes across the enterprise
aPriori’s end-to-end digital twin platform can share data cross-organizationally, which is vital to these goals. Creating a thread that connects each digital twin (product, process, and factory) unlocks critical insights into a more sustainable, manufacturable, and profitable design.
The Time Is Now To Transform Your Operations
Learn how the digital factory optimizes manufacturability, sustainability, and profitability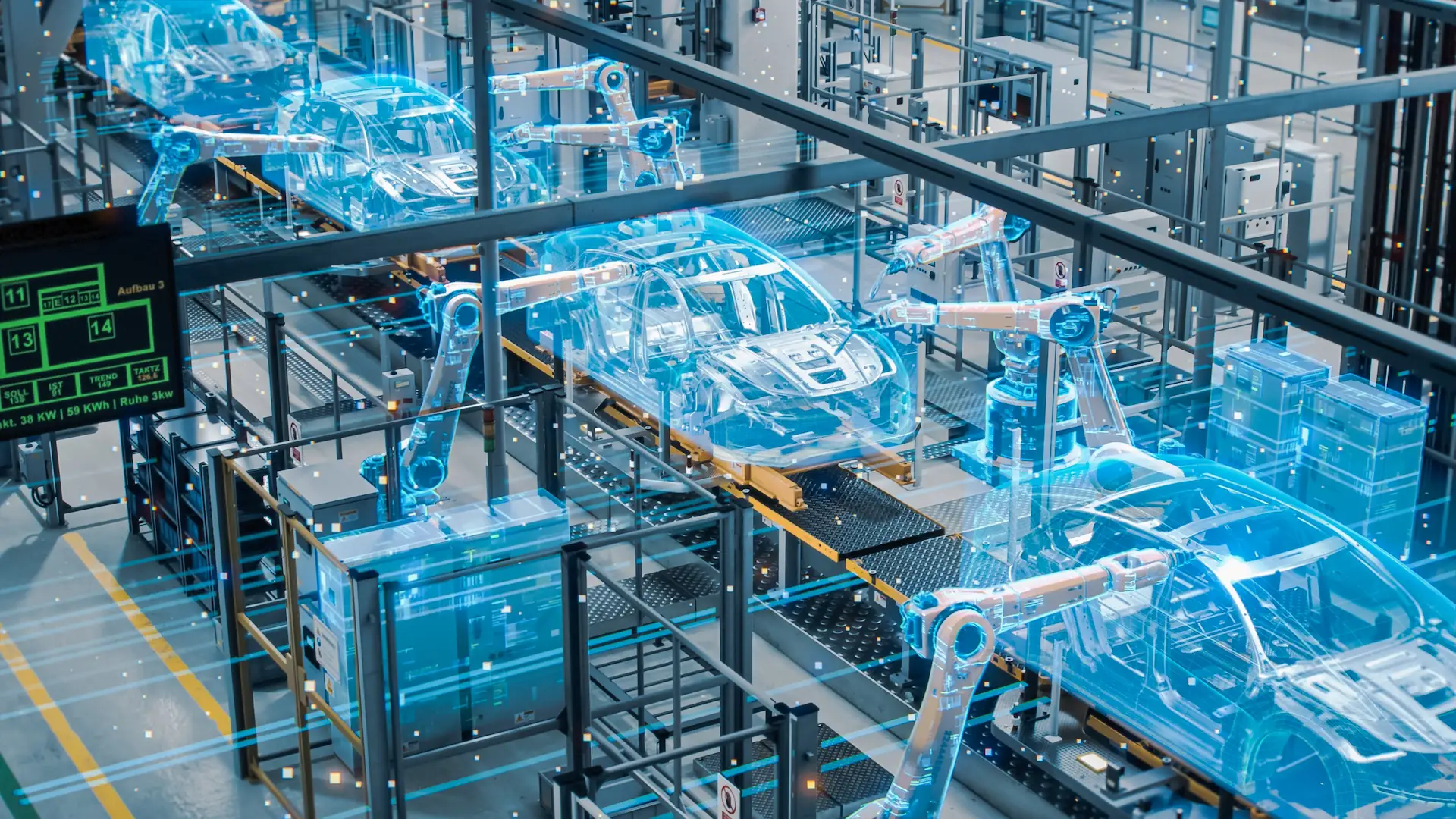