How the Manufacturing Digital Twin Helped Woodward Address Labor Shortages
Key Takeaways:
- Woodward is using digital twin capabilities to address labor shortages
- The digital twin helps Woodward self-quote and reduce supplier lead time
The Full Article:
Woodward is an aviation and aerospace systems and components manufacturer based in Fort Collins, Colorado. With more than 7,300 employees and $2.25 billion in revenue, Woodward develops advanced control systems for commercial and military aircraft, ground vehicles, and other equipment.
Like many manufacturing industry companies, Woodward also faces staffing shortages due to a lack of skilled engineers and machinists, which was accelerated by the pandemic. According to Deloitte, U.S. manufacturers are expected to have 2.1 million unfilled positions by 2030. Compounding the issue is the fact that 75% of machinists in the United States are 45 years or older, and likely exiting the workforce within the next decade or so.
Chris Platz, Global Commodity Manager at Woodward, says the company applies automation and simulation insights to compensate for labor shortages, accelerate procurement, and digitally transform Woodward with digital twin and related smart manufacturing capabilities. By using aPriori, Woodward has been able to achieve more with fewer resources.
Woodward Cuts Supplier Negotiation Time by 90% with aPriori
Woodward’s global commodity team is focused on improving cost insights and supplier collaboration. The strategy also supports broader efforts to streamline product design and improve planning.
Woodward uses aPriori’s digital manufacturing simulation solution to help make product design, sourcing, costing, and manufacturing decisions quickly and with greater accuracy. aPriori digital factories simulate product design and production runs in real time – and automatically provide actionable manufacturability guidance. This enables development teams to run complex design and production scenarios quickly to determine the best options for cost, materials, and manufacturing processes.
Working closely with strategic suppliers enables Woodward to tap into their expertise, control costs, and ensure access to critical materials and components – especially for new product development. Consulting firm McKinsey reports that companies with collaborative supplier relationships can outperform their industry competitors by nearly 2X.
As part of this process, Woodward focused on developing a more collaborative relationship with their key suppliers. These relationships engender a higher level of negotiations along with a detailed and accurate record of each supplier’s equipment list, built into the digital factory, guaranteeing a fair and reasonable price for Woodward.
Along with key suppliers, Woodward embraced the supplier digital factory and self-quoting (Zero RFQ) initiative to identify open capability and capacity. The Zero RFQ initiative has dramatically accelerated Woodward’s sourcing process by automating supplier selection. This process is further enhanced by working with key suppliers to configure aPriori’s digital factories to reflect each supplier’s cost structure. Woodward benefits from near-instant quotes without sacrificing accuracy. Here’s how it works:
- Woodward uses aPriori to assess the cost and manufacturability of parts matching open opportunities within the supplier’s digital factory.
- A summary report containing parts packages, what the parts should cost, tooling, and suggested routing are then shared with the supplier.
- Suppliers then have one week to validate the model results and agree to the parts award(s).
As a result, the company went from a 10-week supplier lead time to a one-week lead time, thanks to aPriori’s manufacturing digital twin insights. Additionally, this supplier lead time reduction enabled Woodward to mitigate their labor shortages, since Woodward was able to go from a five-person quoting team down to one person quoting supplier prices.
Address Sourcing Proactively
By using aPriori, Woodward gleaned manufacturing insights to anticipate and address sourcing and quoting issues. Now, Woodward can negotiate labor, overheads, and margins with suppliers quickly and efficiently. With aPriori and the manufacturing digital twins (in particular, the digital factory), Woodward has capability optimization and improved decision-making. The company can get a clear picture of its supply base and determine the parts they can make versus an outside supplier.
aPriori helped Woodward with routing recommendations, provided a related tool list for suppliers, and offered insights on how to make the part. It is also a win for the suppliers, who face labor constraints when quoting parts. They save time and effort since aPriori has already provided Woodward with much of the essential supplier information. For instance, the supplier no longer has to figure out routings since aPriori provides them along with the necessary materials and tools lists. Typically, a supplier competitive bid or market analysis will only yield a win rate of approximately 7-10%.
aPriori shortens quoting times and increases win rates with real-time data. As a result of being able to self-quote, the company drastically improved parts awarding to the right suppliers based on three Cs (capability, capacity, and cost).
Use COBOTs to Help Employees
Another critical initiative within Woodward is using COBOTs (a computer-controlled robotic device designed to assist a person) to augment their staff. They are a quick, easy way to augment the machinist labor pool to produce high-quality, lower-risk parts. Woodward is working with aPriori on specific supplier digital factories that take COBOTs into consideration. Woodward can create part families (material type, part size, required tooling packages) to build COBOT part packages.
“As we move into our third year of using aPriori, we are going to be really focused on aP Generate – the overnight modeling and expanding the COBOT operation. We are working with aPriori currently on building a digital factory with a COBOT.” Chris Platz, Global Commodity Manager, Woodward
Workforce Benefits of Digital Twins
In addition to accelerating the procurement process, Woodward has been able to reduce the number of people required for quoting. Now, Woodward can reallocate these employees to the machine shop floor to improve efficiency and profitability.
Woodward is using digital thread (digital transformation) capabilities to integrate robotics (COBOTs). The company also is taking additional steps to improve sustainability and support other business goals. Ultimately, the company would like to create a more efficient machine versus man ratio within the next five to 10 years. The goal is to enable one machinist to manage six-to-eight machines versus only one or two machines. This move will further alleviate their labor shortage issues. Woodward also is working to reduce raw materials usage, especially scrap recovery, via aPriori.
Labor shortages will continue for the foreseeable future. Such technological advances improve efficiencies and provide critical insights and recommendations, enabling organizations to do more with fewer workers via enhanced automation and guidance. As a result, manufacturers will remain competitive and agile, ensuring their staying power.
Reduce Quoting Lead Times and Ensure Greater Accuracy
Digital manufacturing enables more strategic, collaborative customer relationships.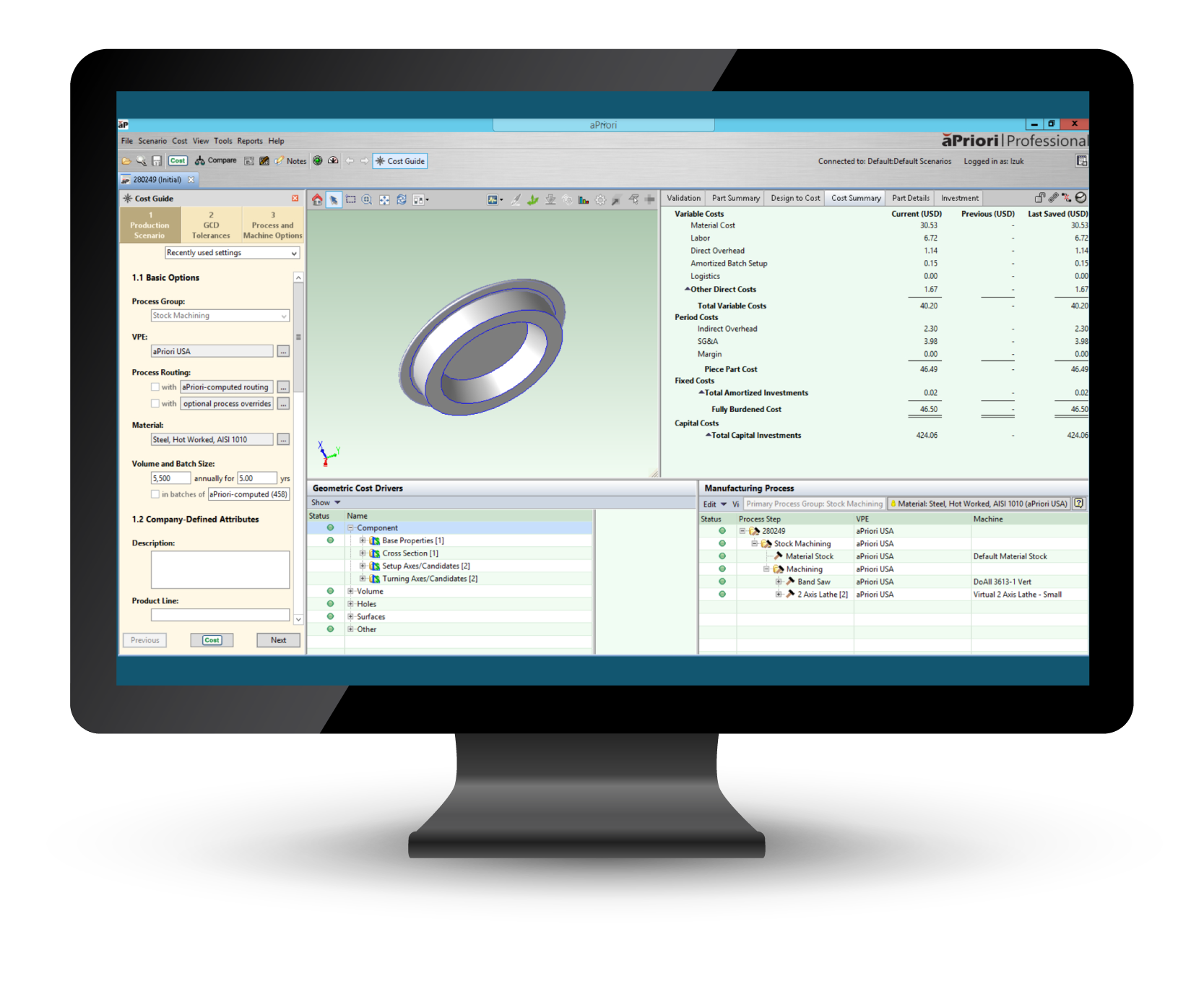