Understanding How to Utilize the Digital Factory
Each stage of the new product development lifecycle has made an effective jump to digital technology — except for manufacturing. Many major manufacturers have yet to implement a digital manufacturing solution that simulates production cost, performance, quality, and other critical considerations.
A growing number of companies, however, are using digital factories to extend their digital transformation solutions to increase profits and reduce time to market. This article outlines how digital factories operate and why companies are running them.
What is a Digital Factory?
A product digital factory is a virtual representation of a physical factory. By simulating the manufacturing process, product teams gain manufacturing intelligence to improve design, sourcing, and decision-making. Each digital factory is configured to mirror a physical factory. By using digital factories during the early design phase, engineering teams can identify and address potential issues quickly – from cost overruns to additional manufacturing capacity requirements.
The digital factory integrates seamlessly with digital enterprise solutions and business processes. This enables teams to collaborate and make decisions in real time using the latest product, sourcing, and manufacturing information. Here’s how digital factories run as part of Industry 4.0 initiatives:
- The digital twin: The development process starts with a product idea and the blueprint for how it works. A product’s digital twin provides this blueprint, which includes digital design files (3D CAD) and product and manufacturing information (PMI). This can also incorporate information stored in product lifecycle management (PLM) and related systems.
- The digital thread: Digital twin information is shared with other operations via the digital thread – including the digital factory. The digital thread ties together the digital and physical worlds. It connects the digital twin to sourcing, manufacturing, and other internal teams so they can access current product specifications. Once a product is launched, the digital thread can collect live product data to support field service efforts, provide product marketing with performance and usage information for future product enhancements, and more.
- The digital factory: This software solution combines product specifications, manufacturing information, and regional cost data to optimize production for speed, cost, performance, and other business priorities. Digital factories enable design engineers, cost engineers, sourcing – and even suppliers – to collaborate on product design rapidly and confidently via the digital thread. Digital factory advantages include:
-
- Optimize products for design for manufacturability (DFM) and design to cost (DTC) via automated analysis and recommendations
- Gain powerful should cost data for sourcing negotiations and identify cost outliers
- Evaluate design alternatives in real-time, including design/part modifications, sourcing options, and manufacturing alternatives (production process, geography, etc.)
- Provide engineering teams and management with real-time key performance indicator (KPI) updates
According to a Bain & Company survey, manufacturers cited multiple priorities that digital factories address – such as improving production planning and optimizing digital twin product information. Looking at the broader importance of digital transformation, nearly two-thirds of commercial respondents to a Deloitte survey said that businesses that don’t digitize during the next five years will be “doomed.”
What are the Elements of a Digital Factory?
The digital factory for manufacturing products includes three primary capabilities:
1) Design for Manufacturability (DFM): The digital factory uses digital twin product specification details to create the framework for simulated production runs — including product tolerances, surface finish, properties, size, weight, geometry, complexity, and material. When a mechanical engineer completes a design change, the digital factory automatically analyzes the digital twin updates and identifies opportunities to improve design for manufacturability (DFM) and design to cost (DTC).
Design and value engineering teams review the recommendations and update the 3D CAD files accordingly. Then, sourcing teams use this information to optimize material selection and manufacturing processes – and to identify potential supply-chain challenges early in the development process.
2) Manufacturing Process Models: Product development teams use digital factories to calculate material costs and run production scenarios to compare outsourced production options globally, determine in-house manufacturing capacity, and evaluate different manufacturing processes. To simulate production, teams configure digital factories for specific manufacturing equipment, processes (e.g., machining, metal casting, extrusions, etc.), routings, production volumes, and more.
Engineers can analyze production options down to the machine level, simulate multi-factory or multi-process routings, and accurately simulate cycle times for each production process. aPriori digital factories support more than 440+ manufacturing cost models. Learn more about aPriori’s manufacturing process models here.
3) Regional Data Libraries: Relevant, accurate data is pivotal to meeting cost targets. The aPriori Regional Data Libraries (RDLs) provide cost insight by geography – including labor, overhead, and tool shop rates. Using quarterly RDL updates, sourcing teams can develop accurate costing assumptions based on relevant market information. RDLs also provide a global library of machines, associated capabilities, and related operational cost information.
Granular production detail is essential for digital factories to model costs accurately and capture nuanced manufacturability criteria in the simulation. Learn about aPriori’s 87 regional data libraries here.
How to Use Digital Factories
aPriori leverages digital thread capabilities to connect teams across the product development lifecycle and provide new levels of manufacturing intelligence. Here’s how teams can use digital factories and digital manufacturing.
Design Engineering and Cost Engineering
When a digital twin design is saved in a PLM system, aPriori automatically generates a full manufacturability analysis of the updated part and identifies potential DTC and DFM issues. Reports can be stored in the PLM system and sent to cost engineers automatically.
The cost engineer reviews the findings and uses a report link to open the identified part in the digital twin. With this guidance, the cost engineer makes design changes to satisfy DTC goals and improve manufacturability. Teams can automatically share reports with other stakeholders including design engineering leaders and product managers.
Engineers cannot foresee every potential manufacturability issue. To support engineering teams, digital factories capture and analyze the sheer quantity and variety of variables underlying manufacturability.
Sourcing for Digital Manufacturing
Rather than relying on outdated cost information in ERP or other systems, a digital factory combines detailed product specifications and real-world manufacturing site assumptions to provide a current, accurate cost estimate.
Each simulated digital factory production run provides the sourcing/and or cost engineering team with a detailed “should cost” model that projects a product’s total cost. These should cost models reflect a real product’s cost structure — including labor, materials, overhead, equipment/facility rates, and, profit margin. These should cost estimates serve as targets that can be used to evaluate designs, optimize existing products, identify cost outliers, and negotiate with suppliers.
Importantly, sourcing teams can use digital factories to evaluate what/if scenarios. Calculating how each factor contributes to a component’s ultimate cost structure is complex. Changing materials selection, for instance, may require a different manufacturing process only available in another region that has higher rental and transportation costs.
Robust manufacturing cost modeling software within a digital factory provides the visibility to address potential issues early in the design process or to inform supplier negotiations.
Advantages of aPriori Digital Factory Software
Transitioning from legacy operations to a digital business is critical to maintaining a competitive edge. Companies that connect digital operations from product development through manufacturing can gain powerful insights to capitalize on market opportunities.
aPriori digital factories can help to improve profitability, accelerate time to market, and develop reliable manufacturability and cost models. Simulated manufacturing helps to avoid last-minute manufacturing issues or cost overruns — issues that risk delaying orders, harming customer relationships, and losing market share. Companies that use digital factories can transform their processes and drive their businesses forward.
Drive Business Value with Digital Factories
We'll show you how!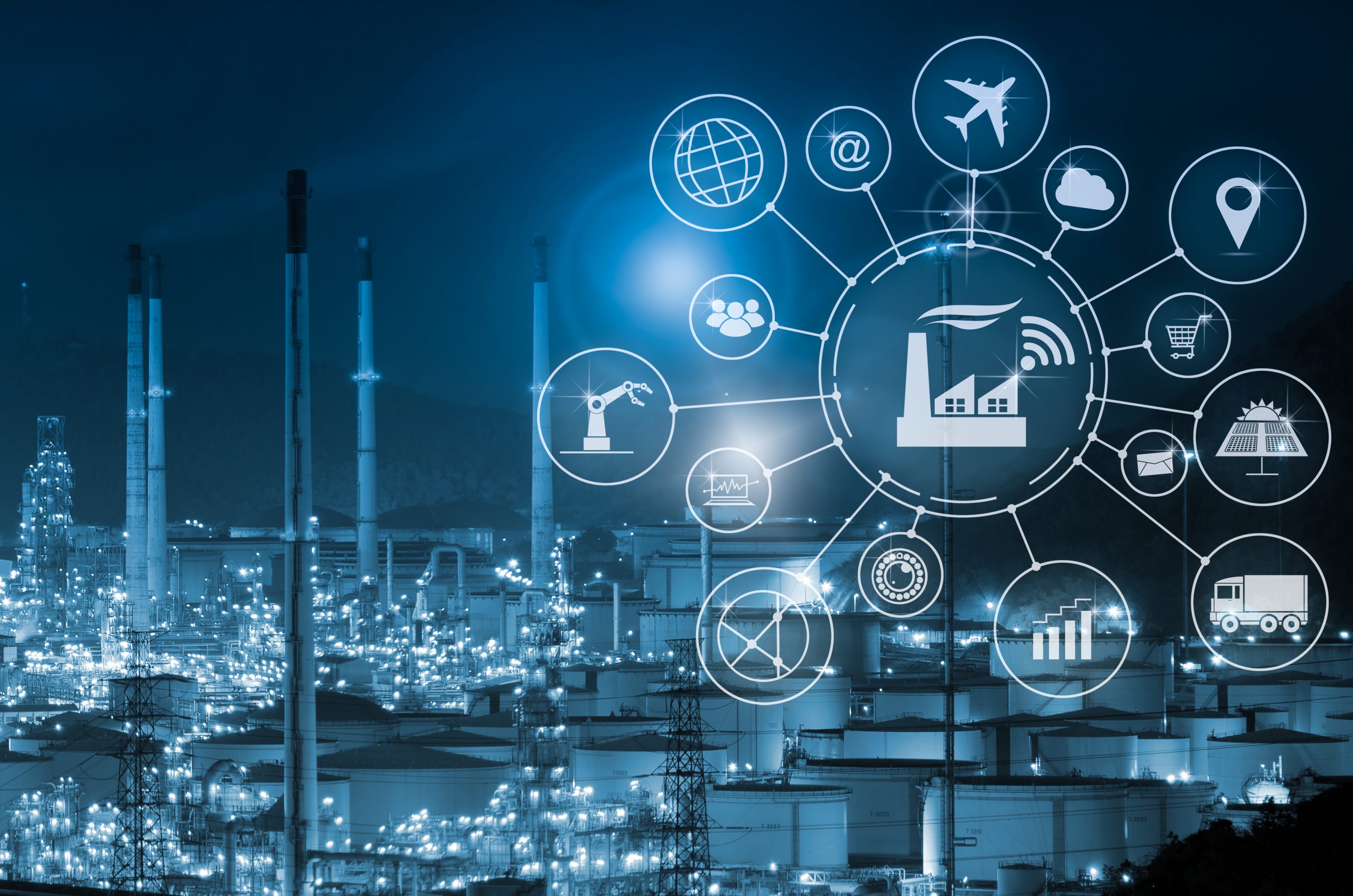