How to Build the Ultimate 2023 Should Costing Playbook
Today’s manufacturing organizations seek a fair and accurate price for critical supplier components and assemblies. However, fair prices and cost-saving wins cannot be realized without the necessary data-backed, fact-based insights provided by should costing methodologies. Indeed, companies that lack should cost estimates fail to get their suppliers to budge and negotiate on their original quotes.
As we approach 2023, manufacturers must develop and implement a should costing playbook to ensure success in the coming year. Manufacturing teams, like those in professional sports, can use a playbook to improve performance and teamwork to achieve their annual goals.
In this article, we will discuss how to create a should costing playbook by addressing collaboration, digital technology and people. We also highlight how dedicated cost engineers act as team leaders by taking charge of should cost analysis.
What is Should Costing and the Should Cost Model?
Should costing is the comprehensive methodology for calculating the expected total cost of an assembly, component or product. An effective should costing process must account for material costs, labor costs, overhead costs and manufacturing profit margin.
The should cost model, on the other hand, are the resources utilized to identify cost drivers and produce accurate projections. Internal processes and estimating tools, such as conventional spreadsheets and manufacturing insights software, are commonly used in should cost modeling.
Manufacturers can use should costing to more strategically source components while driving supplier negotiations based on quantitative, fact-based cost projections. The goal for manufacturers is to identify gaps between supplier quotes and should cost estimates to achieve significant cost savings. Further, should cost analysis enables manufacturing organizations to accomplish the following:
- Get Ahead by Being Prepared. Organizations can accurately estimate product costs before the request for quotation process (RFQ). This enables companies to explore low-cost design alternatives and accelerate the product development process to improve time to market (TTM).
- Make Smarter Procurement and Manufacturing Decisions. Organizations can better understand and manage a component’s overall cost structure. They have the necessary cost estimations to make more informed procurement, production and sourcing-based decisions.
- Develop Long-Term Supplier Relationships. Both the buyer and supplier share key insights that assist the other in planning, adapting and preventing cost, sourcing, and manufacturability issues. Companies and suppliers can now improve their collaboration and participate in win-win discussions.
Three Key Areas to Consider When Developing a Should Costing Playbook
Manufacturing organizations must prioritize and manage three key areas to build a robust playbook. The three factors that must be addressed are people, digital technology and cross-functional collaboration. Companies that manage the three aforementioned areas effectively are more likely to capitalize on cost-reduction opportunities and create strong supplier relationships. The three factors are discussed in detail below.
1. People and Product Development Departments
To ensure the success of the playbook, manufacturing organizations must unify the appropriate internal departments, personnel and stakeholders. An effective should cost roster must include design engineers, sourcing professionals, and, most critically, cost engineers or product cost analysts.
Cost engineers are responsible for producing accurate and timely product cost estimates as well as directing all cost-cutting strategies. Dedicated cost engineers serve as team captains or leaders, identifying and relaying cost-saving opportunities to their design and sourcing colleagues.
Manufacturing cost specialists must follow the three steps or procedures outlined below when performing should cost analysis:
- Leverage Should Cost Models. Cost engineers must have robust processes and toolsets in place to calculate should costs effectively. They may leverage manual spreadsheets or sophisticated cost modeling software, such as aPriori, to provide benchmarks for identifying cost outliers.
- Share Critical Cost Insights With Internal Colleagues. Cost analysts must provide cost insights to design engineers, identifying the factors that cause components to exceed cost targets. Should cost estimates must also be communicated to sourcing professionals to assist them with supplier negotiations.
- Capitalize on Valuable Cost-Saving Opportunities. Should cost insights from cost engineers are deemed effective if they drive smarter design, strategic sourcing and faster TTM. Simply put, should costing must ensure that companies make better, more informed design, raw material, supplier and manufacturing process decisions.
2. Digital Should Cost Models and Manufacturing Insights Software
Forward-thinking organizations recognize the true value of welcoming and incorporating digital transformation into their 2023 playbooks. According to McKinsey, organizations that invest in manufacturing software, such as digital-twin technology, can accelerate TTM by up to 50%. Further, digital-twin technology enables manufacturing companies to improve revenue by up to 10% while enhancing product quality by 25%.
Unlike manual, time-consuming spreadsheets, manufacturing insights software leverages the digital twin to generate should costs based on ever-changing market conditions. The software enables cost engineers to deliver precise, timely should cost estimates that reveal gaps between data-backed projections and supplier quotes.
Manufacturing insights software, like aPriori, considers underlying cost factors (e.g., labor and material) and simulates production to generate detailed cost insights. Further, the software’s automation-driven capabilities enable the streamlined production of error-free cost estimations for many products and parts. This saves valuable time for cost engineering departments when breaking down the costs for each component in a supplier’s quote.
3. Cross-Functional Collaboration Across the Product Life Cycle
Building an effective playbook necessitates cross-team collaboration and participation across all phases of the product development process. Should costing, as previously stated, is a collaborative endeavor led by cost engineers rather than an individual, one-off solo project.
aPriori’s digital manufacturing solutions enhance product team collaboration by providing real-time, shared visibility into cost engineers’ credible should cost estimates. Designers and cost specialists, for example, can collaborate in aPriori to discover component cost outliers and eliminate them through cost-effective redesigns.
aPriori’s accurate should cost estimates eliminate adversarial negotiations in favor of sourcing and supplier cost-reduction collaboration. To capitalize on cost-saving opportunities, sourcing managers must train their personnel in fact-based negotiations and leveraging aPriori’s data trends.
At its core, digital transformation breaks down departmental silos and provides a more accurate, faster and efficient source of collaboration.
It is Time to Plan and Prepare for 2023
As we approach 2023, manufacturers must have a detailed should costing playbook or game plan to score cost-saving wins. The ideal playbook must consider three essential areas: collaboration, digital technology and people or internal personnel. That way, manufacturers can better align corporate goals and increase collaboration among product development departments to meet cost-based targets.
WHAT IS COST TO COST?
What does it take to get to an accurate cost projection? In this podcast episode, Kearney’s Dominik Leisinger leans on his industry experience to explain "Cost to Cost."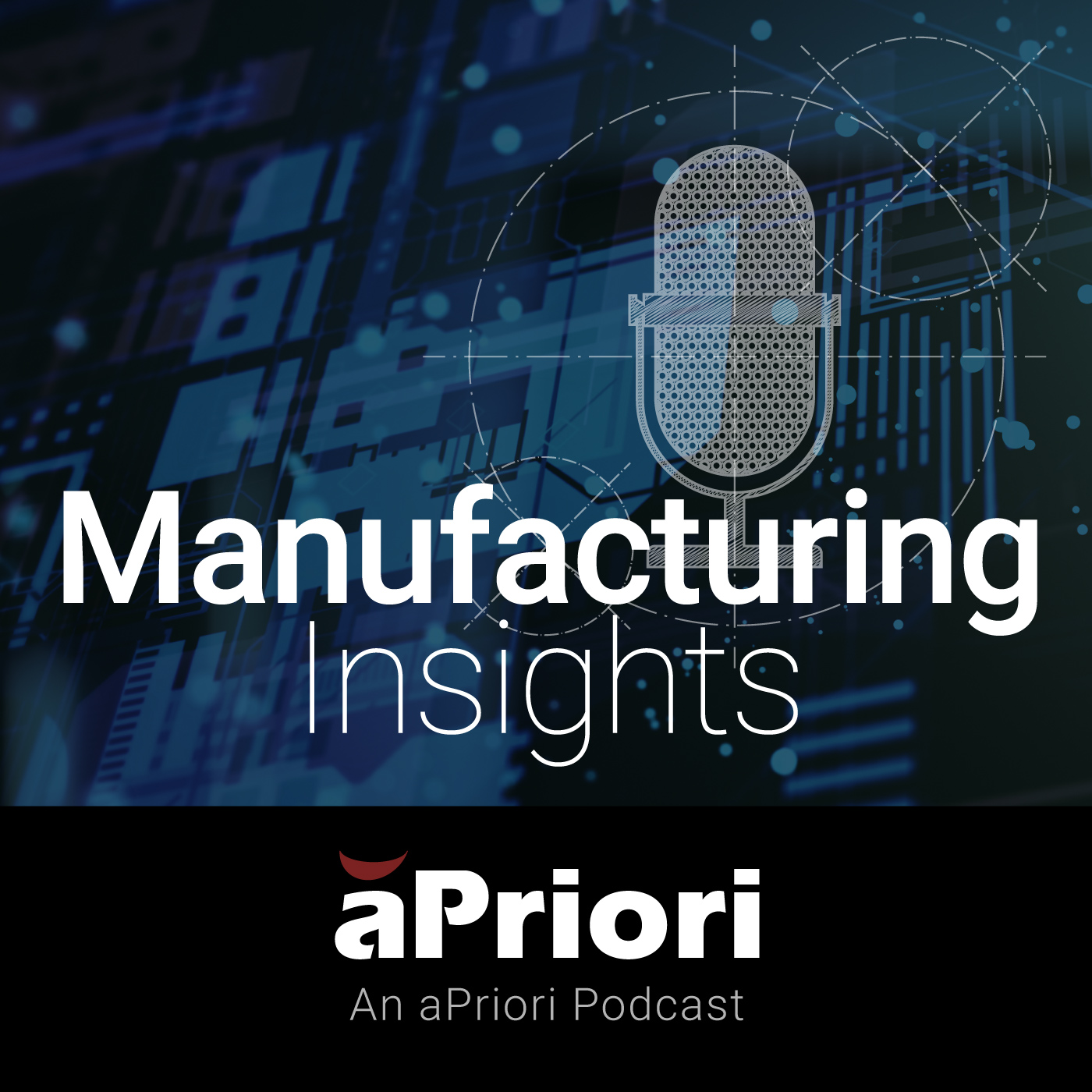