3 Strategies to Improve Design for Manufacturing
Though many manufacturers have made great strides in digitizing their operations, there is still room for improvement. According to the National Association of Manufacturers (NAM), 4 million manufacturing jobs will likely be needed by 2030. NAM also noted manufacturers consume more than 30% of the nation’s energy, and environmental regulations account for 90% of the difference in compliance costs between manufacturers and the average firm.
Continuous supply chain, labor, and inflation challenges, along with the above statistics, underscore the importance of a design for manufacturing process. It’s one thing to intend to improve manufacturability to address these issues. It’s quite another to optimize it for the best possible impact – for the organization as well as the environment. By maximizing the potential of design for manufacturing, manufacturers can overcome these challenges and come out stronger, more agile, and more innovative.
What is Design for Manufacturability?
Design for manufacturing, also known as design for manufacturability (DFM), is the engineering practice of designing products to optimize their manufacturing ease and production cost, given form, fit, and function requirements. In manufacturing operations, effective DFM relies on various analyses for different products and production methods, ranging from tight tolerances and cooling times for molded parts to material type or machine selection. The DFM process takes on a critical role in ensuring manufacturability and product quality while keeping manufacturing costs in line through the product development lifecycle.
The early stages of the product design phase are optimal for design for manufacturability effectiveness, resulting in better decisions throughout the design process, fewer redesigns and supply chain disruptions, a high-quality product, faster time to market, and significant cost savings.
In this article, we will cover three strategies that can help optimize design for manufacturing. We also will highlight the benefits of maximizing this process and the solutions that can help support that effort.
3 Strategies to Improve Design for Manufacturing
Design for manufacturing provides optional support in the product design stage. When ready to move to the production phase, design for manufacturing becomes essential rather than optional. It underscores that successful design for manufacturing is more complex and requires a more holistic approach. In other words, design is one aspect of manufacturability. Other factors that influence manufacturability, such as material availability and production capacity, need to be considered.
- Take a holistic approach to DFM. Most effective DFM looks at the big picture instead of focusing solely on one aspect of product design. For instance, many manufacturers focus on keeping costs down. However, it is not the only factor that should be considered in the design phase. By taking a holistic approach at the onset of product design, with the right manufacturing solution, all aspects and/or goals can be addressed early in the process. As a result, designers can ensure manufacturability and sustainability while meeting cost objectives. For instance, specific tooling may not be feasible from a production standpoint. Identifying the issue early in the process enables designers to course-correct cost-effectively. Another example might be the supply chain. Through a more holistic approach to DFM, all aspects of product design are considered, collaborated on, analyzed, and remediated. Sourcing can determine the best supplier based on availability and price, then, if necessary, work with the designer to revise the design based on available materials, cost objectives, and timelines. In other words, all facets of product design and production are interrelated and should be treated as such and as early on in the development process as possible.
- Close communication gaps across product development. More collaboration from beginning to end ensures that issues such as material shortages and manufacturability can be addressed quickly and support goals such as sustainability at each stage. Additionally, outsourcing is pervasive among original equipment manufacturers (OEMs), making it even more important to communicate and collaborate across all product development channels. A bottleneck in sourcing and procurement will have a domino effect on cost, production, and possibly design.
- Utilize a manufacturing insights solution that seamlessly works with your CAD. This strategy is critical at the inception of product development. Manufacturing insights and analysis early in the design phase mitigate problems later, including late-stage redesigns. For instance, manufacturing insights can identify manufacturability issues early in the design process, recommending easily addressable, cost-effective solutions that mitigate late-stage redesigns. It also helps keep costs in line. Problems late in product development tend to be the costliest and the options more limited. With the proper solution, an in-depth analysis can be conducted without the need to gather, organize, and present data manually, which can inhibit and slow innovation, compromise sustainability efforts, or delay product development timelines. aPriori holds a vast amount of data from the PLM system and 3D CAD. However, unlike other solutions, aPriori unlocks this critical data and presents it – via the digital twin and PLM system – in impactful ways, such as identifying the most expensive parts, highlighting time-consuming production issues, and pinpointing supplier capabilities as material usage.
The Benefits of Enhanced Design for Manufacturing
- A product’s early design determines 80% of its environmental impact throughout the lifecycle. Robust manufacturing process simulation detects manufacturability and sustainability issues early in the design process, dramatically reducing late-stage redesigns and lowering the carbon footprint.
- The best design for manufacturing solutions not only provide early insights but actionable recommendations to resolve them – be it a cost outlier or manufacturing feasibility issue. Often, the recommendations are straightforward and easy to implement to mitigate issues. For example, a part with a straight edge may indicate a tolerance issue. An effective design for manufacturing insights solution will provide recommendations for easily and cost-effectively redesigning the part to reduce manufacturing complexity and, therefore, cost, such as rounding internal edges on a machined part. Additionally, a good solution will offer several alternatives based on the manufacturer’s own capabilities, resources, and more.
- Enhanced design for manufacturing ensures that your product development team is optimizing every opportunity to improve manufacturability, provide more value, keep costs in line, and lower CO2 emissions.
- It streamlines all facets of the product lifecycle. Design engineers can more efficiently create a product that meets all cost, manufacturability, and sustainability goals. What’s more, they can collaborate with sourcing, cost engineering, and production early in the process to address potential issues across product development, avoiding late-stage redesigns or potential product flaws.
- An effective design for manufacturing solution improves agility, accelerates time to market, and fosters more innovation. Concerns around supply chain delays and material costs can be addressed quickly since sourcing and cost engineering can get the equivalent of supplier quotes in minutes. Should the costs influence design, an iteration can be completed more expediently rather than waiting days for the information. Since design engineers can receive this critical information faster, the number of design iterations also decreases. Another example is cost versus carbon. If the manufacturer wants to lower the carbon footprint of a product, a good design for manufacturing solution will provide the necessary calculations and analysis to determine where carbon can be lowered and money saved through a side-by-side comparison. It accelerates the design engineer’s ability to iterate quickly to achieve the optimal sustainability approach for that product.
Optimizing Your Most Valuable Resources
The most successful manufacturers understand how to maximize the resources at their disposal. For organizations, their most valuable resources are people, time, and technology.
Therein lies the sweet spot. Optimizing your design for manufacturing solution ensures that you are utilizing your three most precious resources in the most efficient and impactful way. As a result, you’ll save time taking your product to market, empower your ability via the technology to lower your carbon footprint and add value to your product, and utilize your people for maximum efficiency.
Manufacturability and Profitability Through Design Are Possible
Leverage the power of design for manufacturability.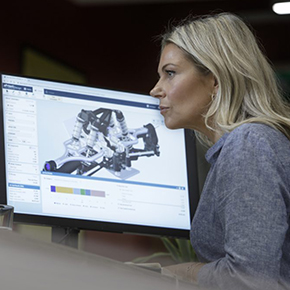