Best Practices for Maximizing the Impact of DFM and DTC
The ability to generate precise, reliable simulations of product cost and manufacturability can dramatically enhance the product development process.
When design engineers can spot potential manufacturing issues early, non-manufacturable or unnecessary costly designs never leave the drawing board. When designers can see the cost implications of different design alternatives in near real-time, they can make value-maximized design decisions without compromising product development timelines.
These sorts of benefits are the ultimate goal of the most impactful DFM (Design for Manufacturability) and DTC (Design to Cost) strategies.
This article presents a concise overview of insights delivered in a presentation at our Cost Insight Conference in November 2020. For a deeper dive, the full video of this presentation is available below. In the video presentation, you can watch up close as we use simulated manufacturing to bring a sample component’s price from $800 down to $280.
Why are DFM and DTC so important for manufacturers today?
Manufacturers are under more pressure than ever to develop products that innovate to deliver enhanced value to the end user while improving profit margins wherever possible. And they are under pressure to meet these challenges on urgent timelines, with product development cycles shorter than ever. Meanwhile, global supply chains create more complex, fast-moving cost drivers than ever.
Manufacturability and cost transparency is essential to meeting these challenges. Achieving them without slowing down the design process, however, can be a real business problem. This article focuses on key goals for manufacturers working to institute the most impactful possible DFM and DTC capabilities. For a deeper look at these two methodologies, please see our article on Design to Cost here and our Practical Guide to Manufacturability here.
While DTC and DFM are distinct paradigms, they are also closely intertwined. Manufacturability is a vital determinant of cost, and both share each of the obstacles discussed below. Because of this close relationship, we refer to these practices collectively as DFMC (Design for Manufacturability and Cost) in the discussion below.
Common Obstacles to Implementing Effective DFMC Practices
The benefits of effective DFMC practices are readily apparent. Achieving them in practice, however, can be a substantial business challenge. Common obstacles that prevent manufacturers from enhancing their ability to generate useful DFMC insights are:
- Time: product development timelines are urgent, and designers generally don’t have time to spend weeks conducting manufacturability analyses or manually costing out different design alternatives.
- Tools: many designers simply lack the tools needed to generate detailed DFMC insights. The cost drivers underlying even a simple component can be incredibly complex, the result of everything from materials costs to labor rates for a supplier on the other side of the world.
Solutions like homegrown spreadsheets are workable but generally remain rooted in historical comparisons to similar products—they have no ability to actually simulate the manufacturing of a design. Spreadsheet-driven cost modeling is also quite labor-intensive. - Limited Cost Transparency for Existing Products: many companies manage designs for thousands of distinct components, many of which may not have been updated for years. The cost drivers for manufacturing these designs do change, however. The result is that it can be difficult for a manufacturer to maintain genuine cost and manufacturability transparency for current products.
Engineers will never be able to re-design every component, and prioritization is essential. But without some baseline level of transparency, there is no reliable method for prioritizing which components offer the highest potential ROI on redesign, resource, or renegotiation.
Overcoming the Obstacles to Achieve More Impactful DFMC Capabilities
The right tools can offer a direct path around the obstacles above. We look at some important high-level goals for DFM and DTC below, and how an approach based on digital manufacturing simulation can help.
Capture the Complex Interactivity of Design, Cost, and Manufacturability
Without the right tools, timely analysis of the vast web of interactive variables behind cost and manufacturability is simply impossible. Even the most subtle aesthetic design decision has the potential to generate a slight manufacturability issue that introduces substantial cost inefficiencies.
Manufacturers benefit immensely from the ability to use a digitally simulated manufacturing approach to analyze these variables almost immediately. aPriori, for example, can work directly from a CAD file, extracting the actual geometry of the design to generate a “digital twin” of the product. This geometry can then be run through a true digital manufacturing simulation at a “digital factory” which can be configured to reflect real-world manufacturing conditions (either for internal manufacturing facilities or third-party suppliers). This simulation is paired with regional data libraries, enabling analysis of geography-specific cost drivers for machines, materials, and overhead.
This simulation-driven approach allows cost engineers, designers, and sourcing teams to collaborate more effectively while a design is still taking shape. Because updated CAD’s can quickly be uploaded to aPriori for further analysis, alternatives can be compared quickly and easily.
Use Design Stage Manufacturing Cost Modeling to Transform Product Development
As the design cycle progresses, more and more costs become effectively locked in. Flexibility to modify the design becomes increasingly restricted (particularly after the design has been released to manufacturing). Even if cost and manufacturability issues are caught before a component goes into production, it may be too late.
Because digital manufacturing simulation can be conducted directly from a CAD-based digital twin, the full breadth of DFM and DTC intelligence can be pushed much earlier in the design cycle. This means more time to consider other design options, more time to collaborate with manufacturing and sourcing teams and catching issues before inefficiencies become baked into designs that may be used for years.
Implement Cost Modeling at the Speed of Design
Design cycles are moving faster than ever, and detailed DFMC analyses should be available in near real-time.
First, faster results help avoid bogging down the design process—exhaustive modeling capabilities won’t be utilized if they don’t fit the urgent pace of design work. Second, faster results allow for more time to explore alternative design choices. Finally, real-time results provide a direct route around the delays imposed by quoting in a traditional design cycle. Traditional third-party quotes can take weeks, leaving little time for corrections if bids come in above expectations.
Manufacturing Cost Models that Reflect the Dynamism and Variation of Real-World Cost Drivers
A useful manufacturing cost model cannot be restricted to abstracted, idealized simulation of production in a perfectly efficient factory. The most effective solutions need to be fully configurable to reflect granular cost drivers that vary by facility and region.
Real-world cost drivers are changing all the time. The practical consequence of this dynamic quality is that, without the ability to quickly generate updated manufacturing cost models, many manufacturing companies lack true DFMC transparency into not only new designs but current products.
Digital manufacturing simulation offers a direct solution. Because CAD models can be used to quickly generate a detailed cost and manufacturability model, design stage DFMC capabilities are equally useful for existing products. With the ability to conduct batch simulations, aPriori effectively transforms an organization’s CAD file repositories into dynamic, simulation-driven cost models that can be updated at any time, applied to different regions, and updated to reflect changes to the design.
Up-to-date information on the current product and costs makes it much easier to identify cost outliers in the product portfolio, prioritize targets for cost reduction (via either redesign or negotiation), and dive deeper to understand the root causes of costs that come in above projections. Techniques like cost versus mass analysis help identify outliers, but aPriori’s simulation engine goes far deeper, analyzing granular manufacturability issues like the cost of machining a sharp corner. In addition to design guidance, the digital factory offers an analysis of process routing.
aPriori can not only identify issues but provide actionable suggestions for solving them. Once a potential solution is generated, aPriori can quickly validate the new design to ensure it has resolved the associated cost or manufacturability issue.
How aPriori Digital Factories Work
Learn about aPriori digital manufacturing simulation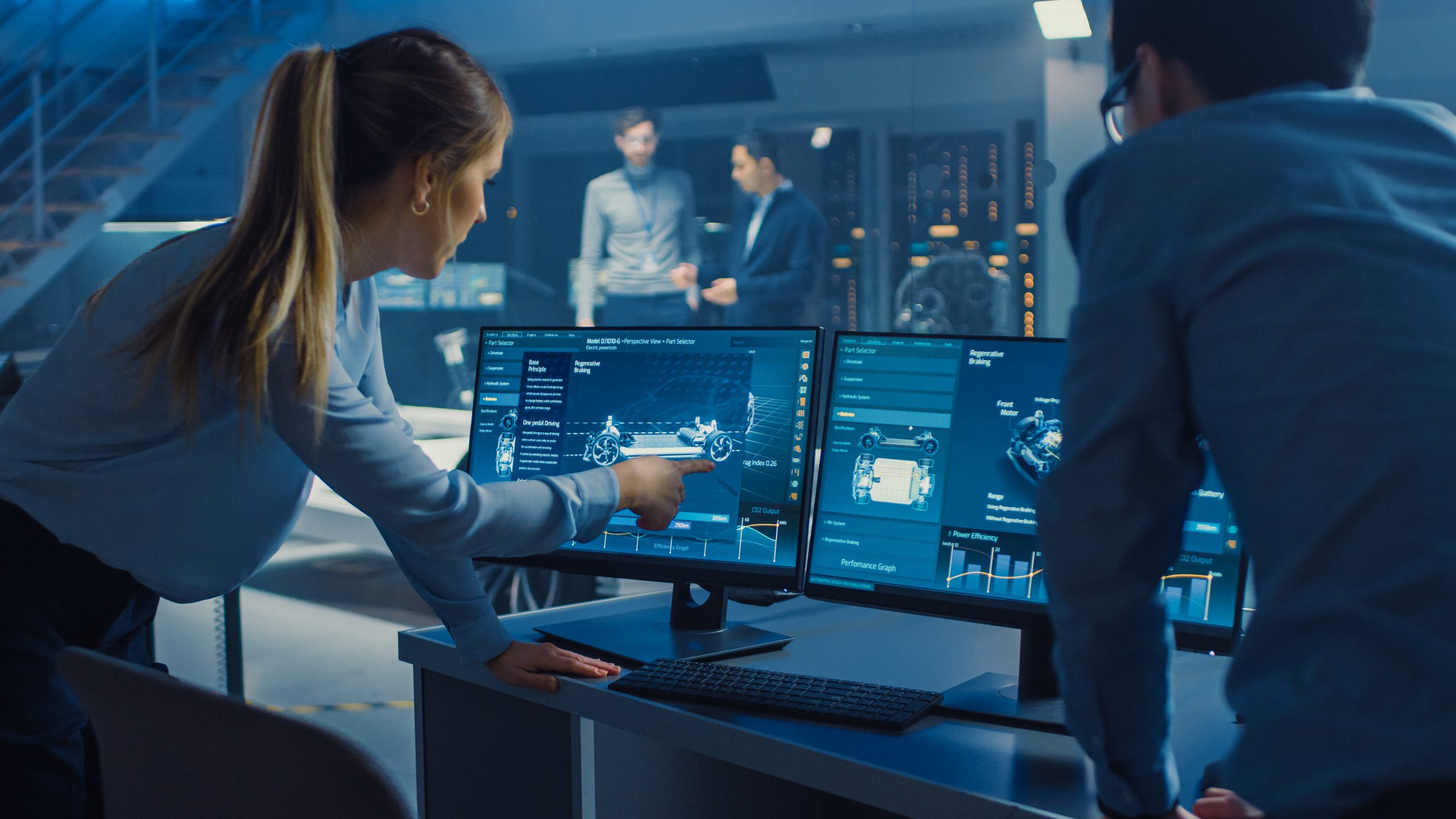