Video
Design Engineering Tips for Reducing Manufacturing Costs on New Product Designs
In this video, you’ll learn expert tips on how to reduce manufacturing costs on new product designs. We’ll answer top questions like:
– Does my design have manufacturing issues?
– How do my design decisions affect product costs?
– Am I selecting the best material to reduce manufacturing costs?
– Are tolerances driving expensive secondary processing?
– How is product performance impacting cost?
Using a manufacturing cost reduction software like aPriori makes answering all of these questions easy. Arm your design engineering team with the tools they need to reduce manufacturing costs early in the product lifecycle.
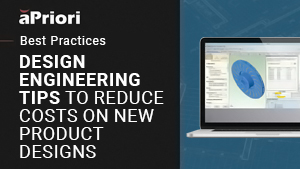
Transcript
Alison Leedham: In this session, we will review design engineering tips for reducing manufacturing costs on new product designs. We will look at how you can utilize aPriori as a tool throughout the design process to ensure that you are designing your products at the lowest possible total cost.
I’m a senior expert services consultant here at aPriori. I received my degree in mechanical engineering. Prior to joining the aPriori team, I worked as a product design engineer designing headphones at Bose Corporation.
In the following scenario, picture yourself as a design engineer working on a design for a new product. Of course, you want to design the best product possible that’s going to meet all the design constraints while keeping the cost of the product as low as possible. As you are designing your product, you might be asking yourself a few questions:
- What design for manufacturability issues might there be with this design?
- How are my design decisions impacting cost of production?
- Am I selecting the best raw material?
- Are my tolerances driving any expensive secondary manufacturing processes?
- How does the product performance impact cost?
- Are extra features that I’m adding to improve the product performance worth the added costs that they might be incurring?
As a previous design engineer myself, I know these questions would cross my mind as I worked through different design iterations. I did not have a tool like aPriori back then to help me answer some of these questions. Especially as a novice engineer in the beginning, I often found myself relying on expertise and guidance of colleagues or going back and forth with suppliers across the globe, both of which took time and resources, two of the things we don’t necessarily have a lot of.
How Automation Can Lead to Major Cost Reduction Strategies
In this session, we are going to take a look at how we can use aPriori to help reduce manufacturing costs on new product designs throughout the design phase. We’re going to touch on traditional design engineering methods, talk about how we can use aPriori to reduce costs, and then we’ll actually walk through two design cost reduction examples together. As I go through this presentation, I want you to think about some of the products you have designed in the past:
- Was there a particular product that ended up being much more expensive than you expected?
- Was there information you wish you had that would have helped you make a more informed decision throughout the process?
- Have you ever lost a lot of time going back and forth with a supplier discussing design for manufacture ability feedback?
My hope for today is that you will walk away from this presentation with an idea of how you’ll be able to apply aPriori as an automated tool for the next product you design. It is thought that 80% of manufacturing costs of a product derive from design decisions that are made in the early design stages. This goes to show just how critical those early design phase decisions can be to the overall production cost.
Having vital information such as cost and ease of manufacturability as a design engineer will help enable you to make informed decisions throughout the entire process. As you progress from the design to manufacturing timeline, your design freedom starts to decrease. You begin narrowing in on your final design concept; you are designing parts that need to fit together; you are making decisions that impact decisions that are being made by other functions of the production process; all those concepts you had in the beginning are starting to transform into an actual product that you are going to start to manufacture.
How Design Engineering Have Traditionally Learned About Manufacturing Cost Drivers Affecting Their Designs
Of course, no design is perfect from the get-go, as you go through the design process, you will likely find there are things that might need to change, but these decisions only get more costly the further along you are. Ideally, we want to minimize the amount of design changes as early as possible to avoid the increasingly expensive costs through the product design cycle. To first reduce our costs we need to understand what is actually driving the cost of our design.
Traditionally, the methods design engineers have to understand cost drivers include getting guidance from manufacturing engineers or suppliers, both of which carry a long lead time and are often solicited later on in the design process. In my previous experience, this was by far the most common way to get any insight into cost or manufacturing. I would reach out to our manufacturing expert to get a gut check on ease of manufacturability. This could take a couple of days, depending on how busy our internal expert was. I would send the CAD over to our suppliers in China and wait to receive a PowerPoint full of DfM feedback. This back and forth could go on for weeks. We would review all the DfM feedback, determine what was feasible to change and what wasn’t, go back to the supplier on items they suggested that could not be changed due to product requirements or impacts to the full assembly, weighing in on the manufacturing risks and deciding what I was comfortable with and what I wasn’t. I would then tweak the CAD with all the changes and send it back for another round of feedback. Of course, the time change made for higher downtime as well. The process was just not very efficient, and it was often the very last thing I would do gearing up to release the CAD for manufacturing.
And that scenario was in a perfect world where all of the stakeholders and partnerships were available to me. Suppliers and manufacturing engineers are both very busy, so while it would be great to pull them in earlier, you also don’t necessarily want to be sending a supplier constant requests for quotes and feedback on designs that might never materialize into business for them. And we haven’t touched upon the importance of the design engineer’s previous experience. I remember the very first part I tried to design right out of college with little to no manufacturing experience. Let’s just say my original concept could not possibly be manufactured, but I had no idea about this until I met with some of the more experienced engineers on my team.
So how can we use aPriori to help us reduce manufacturing costs and help us throughout the design process?
How Can aPriori Help Design Engineers Automate the Design Process and Reduce Manufacturing Costs?
aPriori provides a lot of useful information that the design engineer otherwise might not have. Using the outputs from aPriori, you can quickly identify cost drivers to understand where you should focus your efforts to reduce costs, whether this be redesigning to optimize expensive features, relaxing expensive tolerances or changing materials. aPriori also provides DFM feedback to help you understand what manufacturing thresholds are being crossed and which features are difficult and expensive to make, or where you might run into quality issues. You can get this feedback instantly and get ahead of resolving issues you might have otherwise not realized existed until you heard back from your supplier.
aPriori gives design engineers the the ability to be proactive in their designs and streamline the process. aPriori also provides you with directional feedback.
- Did that change you just made make your design less expensive or more expensive to manufacture?
- Is that added feature worth the increase in costs you might incur?
- Are you in between two design concepts and want to understand which design is more cost-effective and easier to manufacture?
As a designer, most of what you can affect in cost is going to be your direct or variable costs. And what is that direct cost made up of? Material and make costs. Understanding what you can actually impact is key to affecting cost savings in your design.
Material Considerations:
- Is there a less expensive material that can be used in this design? (direct material costs)
- Is there a different material I can use that can be manufactured more quickly?
- Material utilization? How much material are we actually using and how much of that is going to waste?
Make Costs:
- Labor and manufacturing overhead
- How can my design influence the cycle time that’s required to actually manufacture the part?
- How many times does the part have to be set-up?
- What type and size machines are going to be used on the production floor?
- Secondary processing or tooling costs?
- Operating costs?
- Direct labor costs?
The good news is that all of this information is readilyy available for you in aPriori once you run your part. Let’s take a look at an example using aP Design.
Step by Step: How to Reduce Manufacturing Costs Automatically in aP Design
Let’s say I’ve designed a sheet metal part. This is my first design iteration. It is a 6 millimeter thick sheet metal part with tolerances on all the holes. It is a pretty thick bracket because the weight of the part needs to hold in the overall assembly. We want to make sure the part is able to hold the weight that’s required of it. The issue with this design is that the part became quite expensive, so as the designer, I want to reduce the cost so I run it through aPriori. I want to understand what the cost drivers are so that I know exactly where to attack. Where will I get the most bang for my buck? Is it going to be in the material cost or the make cost?
Step 1: I click into the cost results in aPriori to get more detailed information about my cost breakdown. I learn that the majority of the cost is actually in the material. This is where I will want to focus my efforts because this will have the biggest impact on my cost.
Step 2: From here I click into the material and process window to learn more about the material I selected. The material utilization tab will show the cost per kg of the material selected and then also the utilization for the part. I can click to the next tab to see the details about the stock size that aPriori selected. And for sheet metal specifically, I can take a look at how a part is being nested on the selected sheet. In aPriori you do have the ability to set your utilization to true part nesting, which will orient the part in whatever way to allow for the greatest utilization to be used. Rectangular shape nesting is going to orient the part all in the same direction, or you can override the percentage to a user default if needed.
Step 3: I review the design guidance that aPriori provides. It is showing me that there is a DFM risk rating of high – with 47 design warnings for this part! As I click into each issue, the associated features are highlighted on the CAD model. I see I have a few different proximity warning issues, hole to bend, hole to hole, and hole to edge. I click into the hole to bend proximity issues, and see all the DCDs that have a hole to bend proximity issue are actually highlighted on our model. aPriori also shows me the current distance between the hole and the bend and a design suggested distance to resolve potential manufacturing issues that might arise with the current design. Here I can click on the blue lightbulb for more information, the information box will illustrate the issue as well as explain potential problems and provide guidance for how to take action to resolve the issue.
Step 4: Next I look at the process routing to understand how aPriori is actually manufacturing these holes. I can navigate to the process window to take a graphical look at the cycle time breakdown by each process. aPriori tells me that 43% of the cycle time to make this part is actually in machining these holes. This involves additional machining operations to our sheet metal part which doubles the cycle time. I note that this process graph can be sorted both by cycle time and fully burdened cost. If I click into the investigation tab, I can review a number of different items: the number of non-standard tools, the number of unique tools – using non-standard tools and too many unique tools can actually increase your manufacturing complexity and cost. aPriori points this out so I can try and minimize the number of unique and non-standard hole diameters and fillet radii that are on a part. In a similar vein, the investigation tab will also tell me the number of distinct feature sizes that there are in a part. I can also view the number of machining set-ups and the number of machined features, both of which can incur additional costs.
Step 5: aPriori informs me of any specialized finishing required for features that will also drive up the cost. I can click into any of these categories to understand what GCDs are being affected. If I click into the machining set-ups topic, I can see this part requires two different set-ups to machine the holes. I can click on each set-up to see which features are being manufactured under them, the yellow arrow illustrates the set-up direction. I’ve just learned that not only do I have additional machining steps in my design, but that they also require two different set-ups.
Put aPriori in the Hands of Your Design Engineers to See Continuous Improvement of Your Manufacturing Business
So using all this information we just reviewed in aPriori, how can we reduce the cost of this design? We found that the majority of our cost is in material cost. aPriori has a material database which will show us how different materials compare in properties and in unit price. Should we consider the stock form that is less expensive? Can we change the design to reduce waste? How about those additional machining steps? Do we need the tolerances on those holes or do we have room to relax them? Can we change the diameter of the two smaller holes so that they can be made on the term instead of being machined?
With my design engineering hat on, I went back to the drawing board and redesigned the part with these factors in mind.
In design iteration option one, I’ve reduced the thickness to 4 millimeters, changed the material from steel 1020 to steel 4140. aPriori tells me that the stronger material is a little more expensive, so I will have to see how that impacts cost. These changes reduced the cost by $12.
In design iteration option two, I reduced the thickness to 4 millimeters again, but kept the original material. Looking at the process tab in aPriori, I can see that we actually no longer have any machining operations changing to the thinner stock and the 1020 steel allowed for the turret press to actually be able to make the diameter hole necessary for the design. I can then use the cost comparison function in aPriori to really understand how the three designs compare in cost. Let’s take a look at the results. In aPriori you can run these design comparisons against each other to see how they compare in material, guidance, processing and costs, we can see how design option one and two, both compared to the original design. You can do a cost comparison of up to 10 parts in aPriori. One thing to note here is that for the comparisons, the parts are always being compared to the very first part. So we can see our middle part is being compared to the first part and our third part is also being compared to the first part. We can see based on this comparison that our final design option two is lighter, the utilization has improved, the overall cycle time has decreased and every aspect of our cost has decreased. With the click of a few buttons in aPriori, these changes reduced the cost per part by $17.
In design iteration option three, we want to try and reduce the cost of this machine part. What is driving the cost. The cost breakdown in aPriori shows us that most of the cost is in labor and overhead costs. From here, we need to understand what is actually driving that make cost. Let’s take a look at the process breakdown. In the previous example, we were looking at this graph sorted by cycle time, here we’re going to look at it sorted by cost. aPriori shows us that the majority of the cost is actually coming from the 4 axis mill. We have drill press or reciprocating grinding operations, but they are really very minimally impacting our cost. Clicking into the design guidance tab in aPriori shows me that we have a number of machining issues for this part, most of them being the side milling length diameter ratio issue. What this means is that the tool required has too high of a ratio between the length in diameter, which may cause the tool to deflect. Tool deflection can lead to chatter, reduced tool life inconsistent final dimensions on your part, and poor surface finish. This ends up driving higher cycle times, because in order to decrease the force that is pushing on the tool, you need to slow it down. Next, we can click into the investigation tab to take a look at the machining set-ups, any slow machining operations and features that require specialized finishing. aPriori shows us which features are slow operations and features that require specialized finishing operations. We can click into each operation to see what features need the different specialized finishing operations. We can also view the current tolerance as well as the basic machining threshold tolerance for the process. If we take a look at the cycle time percentages here, we can see that with the slow machining operations, they amount to less than 3% of the total cycle time and the specialized finishing operations amount to less than 1% of the total cycle time. If we focus on either of these areas, it’s not going to make much of an impact to our overall cost. So I take what I learned from aPriori, go back to my design, and make a couple of changes to the to fillets improve the length to diameter ratio issue that I was seeing before. Now my side milling machining issues actually went down from 22 to 2. Flipping back to aPriori’s process window I can see that the cycle time actually decreased from 1500 seconds to 1100 seconds. These changes reduced the cost of the part by $68.
Using aPriori I am able to use the design guidance feedback to hone in on what was driving a lot of the cost, make an informed design change, and then quickly re-run the part in aPriori to understand the actual cost impact of that decision. There is no guessing involved and no wasting any time trying to make changes that will not move the cost needle.
Summary
I hope these examples were helpful in showing you how you can use aPriori to reduce costs in your design. To summarize, the simple steps for reducing manufacturing costs in aPriori are:
- Identify your cost drivers. Is it the material or the make costs that is making up the majority of the cost? Identifying your cost drivers first allows you to focus your efforts where it will make the most impact.
- Review the DFM feedback provided by aPriori. You might find that there are certain features that are very expensive or even impossible to manufacture. You might learn that there are potential quality issues and you can reduce those steps to mitigate quality risks if the design constraints allow.
- Learn more about the manufacturing cost of your design by using aPriori. This step will not only help you with your current design, but future designs as well.
- Implement your design changes. Use all the information you gather from aPriori to make informed decisions on your design. Then re-cost the new design to understand the cost impact of your decisions.
aPriori is a powerful tool that can be leveraged as soon once design concepts have CAD data. aPriori will arm you with the information needed to aid you, the designer, in making the best decisions for your product, whether that’s understanding how to balance performance versus cost, reducing the risk of manufacturing quality issues, or understanding the cost drivers and how to reduce them.
And the best part is you can do it all yourself in minutes with aPriori.