Cost Drivers in Manufacturing: Managing Complex Interactivity
Key Takeaways:
- Complex interactivity can make design to cost analysis a challenge for manufacturers
- Discover how aPriori improves the cost, sustainability, and manufacturability of product designs
The Full Article:
Manufacturers are under competitive pressure to integrate systematic cost management practices like design to cost (DTC) into early product development. Traditionally, engineers were expected to design products that met target costs but were not given a tool to do so effectively.
However, systematically analyzing a manufactured product’s critical cost drivers goes beyond a few calculations. Truly integrating cost optimization at the design stage is, in fact, a complex business problem.
This complexity stems from the dynamic interaction of design choices with the full breadth of a product’s total cost structure. These interactions range from the straightforward (more material drives more cost) to the less obvious (adding or even modifying a simple feature, like shrinking a casting hole, can shift the manufacturing process and change costs).
This article examines prototypical cost management issues, highlighting the importance of a systematic approach in identifying cost drivers and the need for manufacturing insights software.
What Are Cost Drivers in Manufacturing?
Cost drivers in manufacturing are the underlying factors or root causes that increase expenses throughout the product development cycle. Manufacturing cost drivers may change due to material price fluctuations, new union contracts, supply chain disruptions, and other external factors.
In today’s manufacturing environment, organizations must assess and manage the following types of cost drivers within their activity-based costing (ABC) strategies:
Direct and Variable Costs
- Material cost drivers encompass material type, material utilization, and standard and non-standard material stock size.
- Direct labor and overhead cost drivers include cycle time to produce a part, machinery, secondary processes, and machine hours. Due to possible variations in work schedules, direct labor hours are also considered and classified as a critical variable cost.
Indirect Costs
- Factory-related cost drivers comprise energy, heating and cooling, cleaning, shipping, maintenance, and other manufacturing overhead.
- Administrative cost drivers include general management, marketing and sales, and IT support services.
The Ripple Effect of Cost Throughout Design
The nature of product design means that virtually every cost driver is densely interwoven with broader design concerns in form, functionality, and manufacturability. Even a simple change can create a cascade of secondary cost fluctuations throughout the design. And these cost changes are not necessarily intuitive.
Even choices constrained to a single manufacturing floor can introduce many alternatives. However, when the scope of decision-making extends to a global supply chain, quantifying alternatives becomes difficult without a specialized tool.
A few example scenarios of complex cost interactions help illustrate why. While the relevance of specific cost drivers varies across industries, the following examples showcase the complexity, interactivity, and non-linear cost implications of design choices.
Unanticipated Secondary Manufacturing Processes and Costs. Design choices determine how a product can be produced. A secondary machining process may require additional machine setup and cycle time, resulting in higher manufacturing costs. However, if the machining process is already utilized to make another design feature, the cost of adding a machining requirement may be small. Understanding these cost implications is especially crucial for global manufacturers with various commodities and production processes.
Take the example of a casting with a small hole that needed to be machined because the casting process was unsuitable. Adding a machined hole to this design would add far less marginal cost than the first.
Volume-Driven Effects. The effective impact of a design choice can vary widely depending on the expected production volume. This fact can make design choices challenging to evaluate at face value. Engineers may recognize that adding a feature like a series of holes lying close to a bend adds minimal cost to a high-volume product via a stamping process. But it may add more quality risk and cost to a low-volume part produced via a laser and bend process.
Tolerance Selection Driving Unnecessary Costs. Product design often involves a degree of arbitrary conservatism in tolerance selection—when in doubt, specifying a tighter tolerance may offer better reliability. This practice risks a design where unnecessary tolerance margins increase costs, sometimes even forcing the move to another production process. The visibility of tolerance specifications’ cost implications is needed to encourage designers to consider the true tolerance requirements more carefully.
A Manufacturing Insights Platform That Reflects the Cost of Design Choices
The technological and economic complexity driving manufactured products’ final and true cost is not new. But the presence of viable solutions for cutting through this complexity with design-level analytics represents a novel opportunity.
In the past, the complexity of cost estimation resulted in simplified, less-accurate approaches—comparing a product to past projects, tallying input commodities, and using back-of-the-envelope calculations. While sometimes capable of capturing a handful of fundamental design choices, these traditional costing methods can only provide a rough order of magnitude estimates. However practical, these abstractions cannot systematically account for all the factors driving manufacturing costs, much less provide data-driven comparisons of strategic alternatives.
The right manufacturing cost estimation software should do something else entirely: provide a comprehensive analysis that reflects the full breadth and interactivity of manufacturing and design choices and their actual cost implications.
This software provides mechanisms for analyzing the feasibility of manufacturing processes. It enables product teams to seamlessly compute the cost of raw materials, direct labor hours, and more. The solution also incorporates modeling complex interactivity. This modeling generates actionable, real-time insights to help companies optimize their products for cost early in design.
Reduce the Cost and Complexity of Manufacturing With aPriori
aPriori’s Manufacturing Insights Platform uses 3D CAD files to automate and simulate the entire production process. This end-to-end view of product design and manufacturing is central to understanding how a seemingly minor change can impact cost.
aPriori enables teams to automate “what-if” scenarios to determine, for example, if a seemingly minor design change will significantly impact the cost and speed of a manufacturing process or limit the pool of suppliers due to specific machine/production requirements. And aPriori goes beyond just addressing profitability by enabling teams to evaluate how product development updates can simultaneously impact cost, sustainability, and manufacturability.
aPriori uses the digital thread to connect its three digital twins: digital product twin, digital process twin, and digital factory twin. aPriori’s digital factories can simulate production based on design geometries, manufacturing overhead costs, direct labor hours, machine hours, and more.
With actionable guidance and comparisons of alternative manufacturing processes across facilities, aPriori makes it possible to “see the forest for the trees” in cost management.
Want to learn more? Get DTC examples and strategies for effective product cost optimization.
Driving Profitability & Sustainability Through Cloud Collaboration
Explore how to make more informed, cost-effective, and sustainable product decisions with cloud collaboration!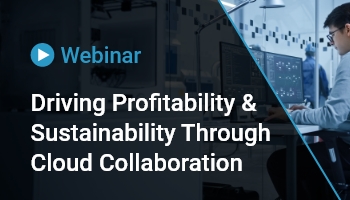