Video
How to Implement Design for Manufacturability & Design to Cost
Want to reduce time to market for NPI projects and minimize ECOs related to manufacturability and cost issues?
In this session, you’ll learn how aPriori’s DFM & DTC features can help achieve these critical objectives without negatively impacting precious time for innovation. Watch the video to succeed in design-for-manufacturability implementation.
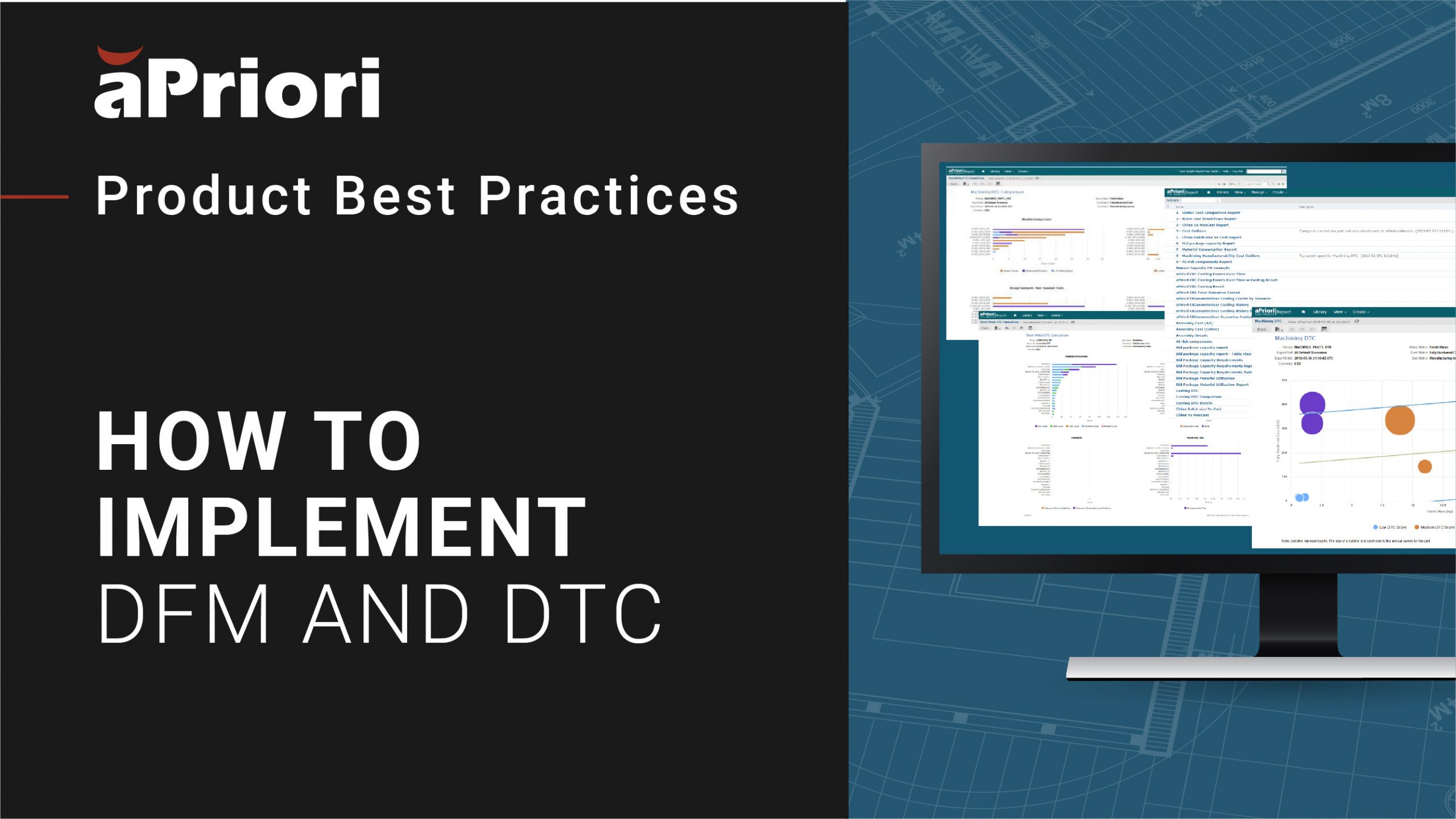
Transcript
How aPriori Helps Manufacturers Improve Their Margins
Patrick Hartnett: My name is Patrick Hartnett, and I’m a Customer Success Manager here at aPriori. And today, I’m fortunate to be joined by one of our lead application engineers, Marc Bakuniec. So, let’s begin. So, who is aPriori? aPriori is the leading provider of digital manufacturing simulation software. We work with our customer base to help reduce the cost of goods sold by leveraging your digital twin. With our digital factories, we automatically generate design-for-manufacturability and design-to-cost insights, helping manufacturers collaborate across the product development process to make better sourcing, manufacturing, and design decisions. And drive product costs lower and create higher-value, quality products in less time. So, how do we help our customers improve their margins during the product development process? Generally, we help within five main functional areas: Research and development, design, sourcing, manufacturing, and value engineering. All of these functions are charged with similar cost-reduction goals.
PH: In design, it could be meeting target costs or reducing design for manufacturability issues prior to product release. In sourcing, it could be trying to achieve price reduction goals with key suppliers. And in value engineering, meeting cost-down targets. So, what problems do our customers generally face? Resource constraints, whether that’s time, people, or data. In the tools that they have available to them, generally, we see our customers prior to aPriori, using historical comparisons and similar to’s, leveraging homegrown spreadsheets, going out to suppliers, requesting quotes, or going to an internal subject matter expert to get product design feedback. The challenges that we can see faced there are inconsistent and subjective results, and time and labor intensive. If you’re waiting for a quote to come back from a supplier, it’s non-extensible. And then the accessibility or visibility of cost or manufacturing lessons learned.
PH: In the impact on the business can be, we see redundant efforts that happen across different, functional silos. There can be a low percentage of cost coverage or suboptimal impact by not focusing on the right parts that will drive your product forward. So, imagine a different approach, aPriori’s geometry extraction allows designers and engineers to do early-stage costing to identify manufacturability issues and avoid costs. We take that geometry extraction and use… And run it through our manufacturing simulation, which provides accurate analysis of real-world manufacturing conditions. That manufacturing simulation is then paired up with our regional data libraries, which enables quick evaluation of manufacturing options, both in-house and at supplier facilities, using region-specific cost data for machines, materials, and overhead. Last and maybe most important is aPriori’s single database architecture allows cost engineers, designers, and buyers to collaborate and evolve cost estimates as the design takes form.
PH: I’m sure many of you have seen this chart before and probably in some other sessions earlier today as well. But as we go through the design cycle, we know that costs are committed and that the ease of change as we release into manufacturing becomes increasingly difficult. So, our manufacturing simulation window is really during the design phase. aPriori can help customers identify and eliminate cost drivers and manufacturability issues early, helping designers quickly evaluate design alternatives and compare opportunities or compare designs to highlight savings opportunities. And then also help our customers track the overall cost and design performance of a product over time. Next, we’re gonna run through a manufacturing simulation to support design. So, Marc will take us through that. So, the steps that will be taken, where we’ll analyze the part for cost of manufacturability.
PH: We’ll identify parts that have the most design-to-cost and design-for-manufacturability issues, highlight the important cost drivers on these parts to provide guidance for remediation, and then get the right information to the right people at the right time to be able to make a change that actually adds impact and can drive value. So, with that, I’ll hand it over to Marc.
The Limitations of Traditional Cost Estimation Tools
Marc Bakuniec: Okay, everybody, let’s get started with the live presentation. So, we are going to start our journey today in aPriori’s reporting solution. The reporting solution allows us to generate value for our customers. This gives us transparency and visualizes the data that we create with aPriori. This session is focused on engineering and the engineering community, so we are using a report and a dashboard here in this scenario for a new product introduction. So, when introducing a new product, you will often set target costs on different functional units. These are displayed here in red. Now, what is traditionally a problem with traditional tools is that you will not have transparency into your current product cost because things are changing all the time. With aPriori, that changes. Being able to use the CAD model to quickly generate a cost calculation and a manufacturing simulation allows us to have real-time cost transparency in our new projects.
Identify and Eliminate Cost Drivers With aPriori Manufacturing Simulation
MB: So, in this case, we can see the blue is the current product cost that we have based upon the CAD designs simulated by aPriori, and we can get real-time cost transparency into our project and see which one of our functional units is tracking towards target cost, above target cost or underneath target cost. So, these are interactive reports that we can click on and go into the next level of detail. The functional unit I just clicked on is way above the target cost. So, this is one that I would like to look at more deeply, dig into, and figure out what are actually the cost drivers in this functional unit. So, in this next level of the report, we can see here graphically and nicely displayed, are the cost drivers of this functional unit, and also, in the table below, we can see some additional data. So, coming back to this high-level chart that we see here, this brings you transparency into your new products, and we can now use the additional analysis tools of aPriori to figure out how we can bring this functional unit that we just looked at, under the target cost.
MB: To do this, we will utilize the additional functionality of aPriori and the additional reports. This, here, being a design-to-cost report. So, in general, the capability of aPriori to create cost calculations based upon the 3D CAD model allows us to do batch simulations, meaning we can cost dozens, hundreds, or thousands of parts and automatically analyze them in this case, for design-to-cost and manufacturability issues. So, first of all, in this graph, we have the cost above the finish mass. This means that components that are above this linear line are components that have a high cost compared to their mass. So, these are ones that we might want to look at a little bit more closely. In addition to the cost versus mass displayed here, we have something even more important, which is the color coding of these components.
MB: These components that are in purple, as we can see in the legend on the bottom, have a high design-to-cost score, and this means that these components have manufacturability issues that have been identified by the aPriori manufacturing simulation. So, if we look into one of these purple components on the first page, we can see some high-level information, cost information, and material information. The second page is even more important, where it shows us the design-to-cost feedback conducted by the aPriori simulation. So, this is a machined component, and aPriori has identified some manufacturing issues and some slow operations, as well as highlighted where we are enforcing the design standards that we have set as a company when it comes to tool selection, radii, or hole sizes. So, in this part, we have some sharp corner issues that are hard to manufacture and machine.
MB: We also have some radii in this part that make the tool very thin and long, meaning that we have to reduce our cutting speeds, or we have the danger that our tool will even potentially break. There are also some obstructed surfaces in this component, which are very hard to manufacture. So, these are things that we would like to look at in more detail, and I’ll show you an example in just a few minutes of how this would work in the actual aPriori solution. In addition, aPriori has highlighted there are slow operations, contouring operations, and some other kinds of operations that are very ineffective for machining this part. We would also analyze tolerances and, as I said, highlight which kinds of tools have been used when it comes to hole sizes and the radii selected for this component. And are these actual standard tools that we, as a company, would like to enforce?
MB: So, coming back to the high-level overview, our design-to-cost report that we just looked at and came from aPriori really helps us to identify outliers from a design perspective, find the needle in the haystack, and focus the engineering team on the components where we have optimization potential, from a design or manufacturability standpoint. Now, if we switch from the reporting environment to the actual aPriori Cost Insight Design environment, this is part of our enterprise cloud platform and is a specific user interface for the design engineer. In general, we have a very easy, easy-to-use user interface, and at the top end here, you can see some of the production inputs that have to be provided to create a cost calculation. So, this is a stock machined component, calculated in the digital factory aPriori USA, and we have an annual production volume set as well as material selection. These are the basic inputs required, besides the 3D CAD model, to create a cost calculation.
MB: We can see already that this part has a high design-to-cost score, so bridging the gap from the report that we just saw, this could be one of our outliers that we just found in that report, with a high design for manufacturability or design-to-cost score. We will go into more detail in just a few minutes on this specific topic. Besides the design guidance, we also have access as a design engineer to the process routing. This is displayed in this case in cycle time. So, we can see we have a band saw, cutting our raw material to length and then a five-axis mill process suggested by aPriori and the escorting cycle times. We can also look at this graph at a cost level. So, this is the breakdown of the cost of this part, on the different process steps when it comes to the material, the bandsaw process, and then also the five-axis mill process, which currently contributes approximately 73% of the cost of this part.
MB: In addition to the process details, we also have the ability to dig deeper into the cost details. On the right-hand side, we can see a breakdown of the cost for this component. If we want to see more information, we can see the material cost, labor, and all the other different cost positions. In general, this component currently, at a fully burdened cost level, is costing $874. And on the left-hand side, we can see a nice breakdown of the cost into material, labor, overhead, setup costs, and other manufacturing costs that are contributing to this component. So, going back to the design guidance, which is the focus of this presentation, when it comes to implementing design-to-cost and design-for-manufacturability standards in companies, the guidance tab will give us feedback very similar to what we just saw in the reporting environment when it comes to the actual issues that we have with this component.
MB: So here we can see very similar things to what we just discussed in the report. We can see this component has sharp corners and obstructed surfaces. We have some side milling length-to-diameter ratios. So again, a small radius that means we have to go into a pocket with a very small tool and some other operations that are not ideal. We will go into this in more detail in just a second. First, let’s have a look at the investigation tab. On this tab, we can highlight things like, for example, cycle time and really get a nice display of red being high cycle times and blue being low cycle times on this component. But this gives us, on a high level, areas of the part that are cost drivers, but it does not really give us actionable insights into what we should do to change these issues that we have here. So, this is something we’ll see then, in a second, in the guidance tab. We can also do very interesting things like looking at the length-to-diameter ratio of the side milling operations, as well as looking at things like the holes and fillets in the part and setups, for example.
MB: If we switch back to the Guidance Tab, let’s focus a little bit more on the specific issues that we have in this component. And the goal here is to obtain as a user actionable insights into things that we should specifically change in this design to avoid manufacturability issues and to improve manufacturability and, therefore, also the cost of the component. So, if we look at the sharp corners that we have, aPriori will directly highlight the upper area of the part here and show us that we have a sharp corner in this pocket, which either the design engineer has just forgotten to add a radius into this pocket, or if it’s the intended design, this is really hard to manufacture and will be very costly. So aPriori is highlighting it as a potential design issue that we should definitely have a look at in more detail.
MB: Looking at the obstructed surfaces in the component, we have this undercut in the part, which is very hard to manufacture. So, this is something aPriori will also highlight. And then we have the side milling length to diameter ratio, which is coming from this pocket that we see here, where in this pocket we have a pretty deep pocket, but also defined by the radius that we have in this corner of the pocket or in the corners of the pocket, in general. We can see that the tool to get in here is very small and thin. And so, this is something that is not ideal. Generally, if possible, it would be great if we could extend or make this radius in the corner of the pocket larger. In addition to highlighting these manufacturability issues, we also have the guidance. So, if, as a designer engineer, you’re not exactly sure what the problem is and how to solve it, you can very quickly go into the information that aPriori provides. And you will see a nice description of what the problem here is and how to solve this specific problem.
MB: And so, we have this for all of the different areas, the sharp corner issue as well. What is the problem, and how do we solve this issue? So, this is really giving us actionable insight into this part and what we should be changing in the part specifically to make it more manufacturable and more cost economic. So, what do we do as a design engineer? Well, we typically are working in our CAD system, so I’m going to switch over to my CAD system to take some of this feedback that we have just been given by aPriori and change it live in the CAD system and then have… See what kind of an impact this will have on the design-to-cost feedback. So, I’m gonna take just this one design-to-cost feedback that we received from aPriori: The radius in this pocket, I have increased it, and we have now gotten rid of one of the guidance issues that aPriori has highlighted.
MB: The nice thing is here, we have a plug-in which basically connects aPriori and your CAD system together and automatically uploads this new version of the CAD file to the cloud, which is the environment which… In which we have the Cost Insight Design solution. And by the way, this is very slow due to the fact that I’m on Zoom at the moment, I tried this earlier and, of course, prepared for the session, and it’s about five times faster if I’m not in parallel, working with Zoom and transferring everything across the internet. Just a quick comment on that side. So, aPriori is currently uploading this new version of the CAD model with the design changes I made to the cloud platform. In a few seconds, we will have the updated cost simulation based on this new CAD model. So, this gives you a real streamless connection between CAD and aPriori for the design engineers to generate value by reducing the cost of goods sold.
MB: And what we see from our customers is that they often are able to reduce their time to market and improve their design processes in general by having this real-time cost feedback provided by aPriori in the design and engineering community, we can reduce our design iterations, we do not necessarily have to go to a supplier, for example, which is a very traditional methodology of getting cost information. In engineering or… In a project, a new project that we have for a new product. And so, this really helps our customers to generate this kind of value, reducing the cost of goods sold, optimizing and designing products for manufacturability and for cost, and of course, also improving their design cycle times.
MB: So, in a few seconds, we will see that aPriori has finished uploading this CAD model into the cloud, and then aPriori will automatically switch back to the active cost calculation and display the updated results. What will be happening in the aPriori environment once the file is uploaded is that aPriori will simulate the manufacturability of this part based on the geometric cost drivers that are extracted from the 3D CAD model. And that’s what’s happening exactly now.
MB: We can see aPriori is translating this CAD file, and in a few seconds, we will have the updated cost simulation and the updated cost calculation, which will then incorporate my design changes, and we will be able to see that we have reduced the amount of guidance issues compared to the previous version of this CAD model. When aPriori is simulating, aPriori is also comparing different manufacturing routings. So, for a machine part, aPriori will look at what and how can I machine this part. Ideally, what is the best manufacturing routing for this part? Is it a 3-axis mill? Is it a 4-axis mill or a 5-axis mill? Should it be turned and milled? All of this is happening at the moment while aPriori is simulating this part in the background.
MB: So, let’s just wait a few seconds here, aPriori should be done in a second. Again, if you’re not connected to Zoom, et cetera, this is all very much quicker, and you basically have real-time cost feedback within a few seconds utilizing the aPriori plugin into the CAD system. All right, so we have the updated calculation. I don’t know if anybody specifically looked at this point that we had here before we did this design change. We had 38 guidance issues on this component, and now we only have 30 left. It still has a high DFM risk because there’s still a lot of feedback that aPriori has given us when it comes to the guidance tab. But what we can see here is we do not have machining issues when it comes to the side milling length-to-diameter ratio anymore. So, we have gotten rid of this specific manufacturing issue, and of course, we would now utilize the other feedback back by aPriori and implement this into the design to create a more manufacturable component.
MB: If we take all of the feedback that aPriori provides to us, which is this version of the part, we would end up ideally with a part that has a low design for manufacturability or design-to-cost score. We can see here on this component now we have only seven guidance issues left. Let’s have a quick look at these guidance issues. So, we have a sharp corner issue left still on this component, and we have some contoured surfaces left as well. Just to highlight quickly, what have we implemented based upon the feedback by aPriori. Besides, as we can see, having the radii in the pockets increased, we can see that we have gotten rid of the sharp corner issue that we had in this pocket. Over here, we can see the feedback aPriori provided when it comes to these undercuts here is avoided by having this nice cutout in the part where we can get in here with a nice facing tool to improve the manufacturability in this area.
MB: And we have also reduced the amount of contouring operations. This part, actually on the original version, is curved on the top, but that is not necessarily the design intent or the form, fit, and functional requirement for this component. So, with the feedback from aPriori when it comes to contouring, we have also created a planner face on the top of the part now so that we can very nicely and effectively face these areas of the part and do not have to contour them anymore. So, if we remember the original part, we were over $800, and this has now brought the fully burden cost of this component and this optimized version of the part down to approximately $280. So, we have about a third of the original cost now for this component compared to the original design. And this is the kind of savings when it comes to optimizing your cost of goods sold that aPriori typically brings to our customers.
MB: We have also gone a step further with this component. aPriori can very quickly also let you evaluate alternative manufacturing processes. This part here is, or this scenario, this calculation scenario of the part we have chosen to evaluate this part as a sand casting compared to machining it from stock. Now, obviously, this design is not optimized for casting, so we do have a high DFM risk. If we choose to move forward with this casting design, we would then utilize the design guidance for the casting to then look at things like there are missing draft angles in this part. There are some other issues that we have when it comes to the radii of the part on the parting line, et cetera. So again, if we choose to move forward with this design variant, the casting aPriori would give us feedback on how to optimize this design for the casting process.
MB: If we look at the cost for this variant of the design, we have a piece part cost here of 157, and if we include the capital investment necessary for the tooling of the part, we would be at $167. So, if we look at this from a cost perspective, this would actually be a very interesting opportunity to potentially move forward in our product development process with the casting version of the part. We can then very quickly take these alternatives and do a comparison of them. So here we can see side-by-side these three different variants of the part, the original part with the high design for manufacturability score and the 38 guidance issues that we had, which cost us $874. Moving on to the optimized version, utilizing the feedback from aPriori’s actionable insights, changing our CAD model, and optimizing this part for cost and for manufacturability, we were able to bring it down 67%, almost 68% to $281.
MB: And then our third variant of the part is casting, which would be 167 if we look at it, including the amortized investment for the necessary tooling, which would bring down the cost for this component to 80% of the original cost that we had. So, this really helps us to generate transparency in the product development process, reduce our design iterations, and move forward in the product development process with the ideal design, which will help reduce our cost of goods sold and make sure we also achieve our target cost. Where we came from way at the beginning of our report, where we saw that we had one of the functional units above target cost, we identified one of the cost drivers as a design outlier in this functional unit and have then created different alternatives to move forward with to greatly reduce the cost for this component.
MB: And, of course, we could utilize this functionality with the other components of that functional unit to bring down the cost in general to hit our target costs. So, let’s assume that we decide to move forward with the optimized machine version of the part. If you’re going to a design review in the context of your product development process, you might want to create a part cost report. So, we can directly out of the aPriori environment create a report, which would then look similar to the one that I’m showing you right here, which would gather all the general information on the top, including a screenshot where we have our production volumes, we have our masks and material, et cetera, as well as a nice, detailed breakdown on our cycle times machine rates, labor rates, and a detailed cost breakdown in addition. So, this is something that, of course, aPriori also provides not only the reporting environment where we started out, which is typically used for more advanced dashboards and reports, but we also can create Excel reports directly out of the Cost Insight Design environment.
MB: Now, if we switch back to the reporting environment and have a look at one of the further capabilities that we have, if we’re kind of leaving the actual design-stage process and moving forward to the, let’s say, sourcing and further topics that we have as we move along the product development process, we could now take this component and cost it across multiple factories. In this case, we have costed this component across basically all of our AD digital factories that aPriori provides out of the box. And this can really support make-versus-buy decisions in your company. Typically, you would focus on the low-cost environments, as we can see here on the right hand of this report. And if aPriori is implemented, and we have created digital factories of your own manufacturing locations and your supplier environments potentially, you could also, of course, have make-versus-buy decisions not only between the aPriori factories but also between potential suppliers or your own factories. Which factory has the best manufacturing equipment to make this part ideally? This concludes the presentation, my part of the presentation, and I will hand it over to Patrick for a summary of the presentation, and then we will open it up for questions.
PH: Marc, can you just confirm that you can see the demo screen?
MB: I can, yes.
PH: All right, perfect. Thank you. All right. So, just to summarize what Marc had taken us through, we took a series of parts. I know that the first example analyzed those parts for the cost of manufacturability issue and then looked for the parts that had the most design-to-cost and design-for-manufacturability issues. We’re able to highlight the important cost drivers on those parts and provide guidance for mediation. So, Marc was able to demonstrate taking that machine part from $870 down to $280 and then also able to run a scenario analysis to show what that would look like potentially as a cast part. This isn’t unrealistic from what happens during some of our workshops with customers in the design phases; we can work with you on parts that are still in design, have released drawings, and be able to help you analyze parts to decide on the direction that makes the most sense and engage in the redesign of parts with that aPriori guidance.
PH: In recent workshops, we’ve seen savings of $200,000 and more by moving from an assembled part to a cast part. We’ve seen projects recently where the volume had dropped off from the initial estimate, and it was originally planned to be cast and dropped to be moved to be a machine part, saving 25% of the product cost. So, the demonstration that Mark gave is very realistic to what happens during some of our workshops with design engineers. The last step that Mark showed was also super important. So, who are you reviewing those changes with, whether it will be manufacturing or sourcing? Do you have a strategy of who you’re going out to target for manufacturing? Whether that’s internal or external, setting a should cost with the sourcing team so that they know what they wish should expect to pay prior to engaging in negotiations.
PH: And then lastly, capturing those savings. So, understanding the cost avoidance and being able to communicate that back up. As a program team, it’s super critical to be able to understand where you started and where you ended and be able to document the cost savings your team’s generated, as well as the manufactured body issues that you’ve eliminated because those would be late-stage ECOs potentially had you released that product into production. So, at this point, we’ve got about 10 minutes left. We’d like to take a couple of questions and respond to anything that you guys have put into the question-and-answer panel. It’s still open, so feel free to enter questions there. We’ve got one in the Zoom chat, and this says, at the moment, you click… All right, so Jose Luis, if this is incorrect, feel free to let me know. But at the moment you click the cost and the plugin, do you rewrite to the PLM system a new version of the design?
Jose Luis: Yep. Hi Patrick. Yep. Correct. The question is, at the moment you are in Creo, and you click over to evaluate the cost, you are directly rewriting this new version into the PLM. It’s clear that you have the new version in Creo, but is this only the DWT part, or are the CAD parameters loaded in the PLM? That’s the question I have. Or is it just a local background, and you need to check in later?
PH: Great question. No, that is something you’d have to check into PLM; that’s just a local session between Cost Insight Design and whatever native CAD program you’re using.
JL: Thank you.
MB: If I can maybe add to that, there are separate sessions on Cost Insight Generate, and Cost Insight Generate would allow you to basically trigger the aPriori costing process as you check into your PLM system. So, we specifically did not present Cost Insight Generate and the potential workflows and automation that we have in that context in this presentation here today. But in general, it is definitely possible to have aPriori, the CAD system, and the PLM system hooked up together in connection with workflows there to have the costing process automatically conducted once you’ve checked the part into PLM, for example.
JL: Understood. Thank you very much.
PH: All right, Marc, we’ve got a couple of other questions here. So one is, how does aPriori help in defining the target cost?
MB: So, the target cost is typically not something that aPriori really focuses on. That is something that is set normally together with the sales operations, looking into the market and seeing what kind of margins we want to realize and what the competition looks like. What can we sell this product for? That’s typically then broken down into functional units of the product. And that’s something that is typically set on a different level. aPriori does not necessarily have a huge impact on setting the target cost. What we bring to the table is then the transparency in where you are currently versus your target cost.
PH: Yep. So, you can set a target cost for a specific part or assembly and then track that through the design process. I know I didn’t phrase that as a question, but it was intended to be a question.
MB: Oh, yeah, absolutely.
PH: And then, like we stated before, at the end, once you’ve released this product, you’re preparing to release this product, it will help you establish a should cost to be handed off to your sourcing team, or if you’re going to and build this internally, it can help you develop a cycle time standard that can be used across your manufacturing floor. And then a follow-up question to that is how does the operator help break down the cost target at an assembly versus a component level?
MB: So, we’re basically very flexible in having a structure as you would like to see based upon sub-assemblies, based upon functional units, and we are very flexible also on setting target costs on a component level. So that can be a part level. It can also be on a sub-assembly or functional group unit level. So, what we can help with is understanding the structure of the assembly based on the CAD model or based on a bill of material. And then basically have the different targets, either roll up. So, if you have targets set on the part level, we could automatically roll up all the targets to the assembly or functional unit level and then help by having transparency in that context. Patrick, you’re on mute, I believe.
PH: We’ve got another question here in the Zoom chat. Thank you for giving me that heads-up. So, great demo, is the D2C guidance also available for manufacturing processes other than machining?
MB: Yeah, so design to cost is one of the big topics at aPriori, and we have this available for many different manufacturing process models. It’s supported currently, and we’re working on extending this, of course, to all of our cost models over time. Currently, it’s available for casting, as we also saw in the demonstration for plastic molding for sheet metal components. I believe those are the main ones that we support at the moment. And, as I said, we are working on supporting it in the future for pretty much all of the process groups that we support in aPriori.
PH: Great. All right, a couple of other questions. In your experience, what are some prerequisites for having a successful workshop?
MB: I’m sorry, I just saw this another question come in here, I was a little bit distracted. So basically, the prerequisite for a successful workshop is defining a use case. First of all, when conducting a workshop, it’s important to understand what are we actually trying to prove with a workshop when you’re a prospective customer looking to potentially invest into aPriori. So, defining a use case is a very important step. Defining, of course, parts potentially also having design alternatives. aPriori, when we do a workshop, of course, will not be fine-tuned to represent your specific manufacturing environment. So we will be working with out-of-the-box factories, and if we can do, for example, a relative cost comparison between two different design variants, that can be a very effective way of showing how aPriori could give you transparency into your product development process in evaluating design alternatives and showing you which one is the more cost-effective and of course where we have design-to-cost feedback and potential manufacturability improvement that we could then bring into those designs that typically from an engineering perspective will give us a nice starting point to prove the value that aPriori can bring to your business after it is implemented.
PH: Yep. Yeah, I would echo that for sure. And I think that having thoughts in advance on what parts might be good opportunities for design alternatives is fantastic ’cause it allows us to do that quick simulation. Again, you don’t need to go to a supplier for a quote, just like Marc showed for looking at a machine-versus-cast part, right? There’s no definitive change to the model itself. Just running it through those different process groups and then having a balance of parts that still have opportunity to be impacted obviously would be best for a prospective customer because there’s still time to make a change that you’re not running a VA/VE activity at that point. Got another question. Excellent demo again. So, a lot of shout-outs. Great job, Marc. How about electromechanical assemblies in electronic components? And I’m looking up right now what time Stephanie’s session is tomorrow, but if you wanna answer that question, I’ll chime in with that at the end.
MB: Yeah, absolutely. As Patrick said, we do have a session specifically on electronics tomorrow. I mean, traditionally, we had a focus on mechanical components, but over the last couple of years, we’ve extended our cost models to also include electronics. We support p.c.p.a calculations, as well as wire harnesses, at the moment. And so yeah, we also support electromechanical assemblies and electronics in the process groups that I just mentioned.
PH: Perfect. Thank you. I just looked it up, and it is at 9:20 tomorrow morning. So, if you’re interested in going to the electronic session, that will be again tomorrow at 9:20 in the morning. All right. One more question. How much value does the typical customer see in return when moving to an engineering use case? Marc, do you want me to jump onto that slide that we have?
MB: Yeah, I guess that could make sense to support that with a visual background. So, for those of you who have been following the conference, we obviously support many different use cases with our customers. Different use cases have different time to value, as we can see in this graph here, as well as different potentials when it comes to generating value. Everything you’re seeing here is very conservative based on our experience with our customers. I mean, you’ve heard in the presentations today things like 40% cost savings on certain components from some of our customers who have presented. So obviously, there is potential to go even higher if you look at it really conservatively, no matter what you are currently doing in your engineering environment, which tools you are using, etcetera. aPriori will bring an additional five to 10% in typical cost avoidance. So, if we’re using aPriori in a new product introduction, it’s not so much actual savings. It’s actually avoiding the cost being designed into your products right from the beginning.
MB: That can have additional effects, of course, reducing the amount of value engineering that we have to conduct after we have released the product to market. So, besides the impact on cost avoidance, conservatively five to 10% minimum with the engineering use case, we, of course, have productivity improvement as an additional value for the people who are conducting cost calculations in the engineering community as well as other things like reducing ECOs and the amount of rework which is required after we have released the product for potential value engineering. Value engineering, of course, is also a use case that is typically associated with engineering. And in this case, we have a little bit less degree of freedom typically compared to new products, where we see conservative savings of three to 5% based on the potential that we have also seen in this presentation today. So, it’s a very similar use case but, of course, less degree of freedom if we have a product already in the market compared to a completely new one.
PH: All right. So that looks like it, we exhausted our question list. Thank you all for attending today’s session. We hope that you guys all have a great day. Thank you again, Marc. I really appreciate it.
MB: Thank you, everybody.