Unseen Design Engineering Challenges: What Leaders Can Do To Navigate Them
Key Takeaways:
- Design engineering challenges can result in leaders having disparate perspectives on the biggest product development issues
- Whether it’s trying to meet cost targets without compromising quality and performance or reducing project delays due to late-stage manufacturability issues, all lead to one critical conclusion. Without data-driven insights throughout product development, any number of issues can trip up manufacturability, profitability, and deliverability
The Full Article:
Several years ago, Gartner released a survey that found that 45% of product launches were at least one month behind schedule. The same survey found that only 55% of product launches occur on time.
Engineering leaders face design challenges today that include:
- Failing to meet launch deadlines due to late-stage manufacturability issues.
Studies on complex systems and manufacturing indicate significant costs and delays arising from late-stage discovery of design or manufacturability flaws. Research shows early detection of design errors can substantially reduce costs. Errors caught later, like post-production, are exponentially more expensive and time-consuming to resolve.
- Meeting cost targets accurately and consistently.
This indicates that a significant majority of teams struggle with balancing cost targets and maintaining quality and performance. Industry reports substantiate it, noting that balancing cost efficiency with product value is a top priority for R&D teams. Companies increasingly adopt methodologies like design-to-value to address these challenges, emphasizing the importance of robust cost modeling tools.
- Lacking the necessary manufacturability knowledge beyond CAD.
The majority of their education focuses on theoretical knowledge. Some estimates suggest that a significant number of engineering roles, especially in design, may not require extensive hands-on activities. Most designers start their careers directly from an academic route these days, rather than a hands-on apprenticeship or promotion from the manufacturing floor. As a result, they lack the manufacturability knowledge. CAD skills alone are not enough. CAD is so easy to use these days that you can create any shapes you like, without any clear understanding of how they will be made.
- Having to compromise quality or performance for the sake of on-time delivery and/or cost targets.
This statistic is similarly validated by our recent industry survey (see below). A typical design and development phase is six to 12 months, with average testing and validation in the two to four-month range. The latter can be expensive. Consequently, it ends up being eight to 16 months of critical time and effort that most teams cannot afford to waste. Cost and manufacturability feedback early in product development can drastically reduce time and expense as well as root out product development that is not feasible before getting too far down the road.
More Speedbumps That Can Trip Up Design Engineering Efforts
Although the above internal factors greatly influence how cost-effectively and quickly design can accelerate product launches, other real-world problems can create additional speedbumps. They include:
- Design and Manufacturing Priority Conflicts: Many product launch timelines are delayed due to early-stage designs prioritizing performance over manufacturing feasibility. Early design and manufacturability feedback can remove this speedbump and accelerate time to market. This feedback can also serve as a facilitator for product development problem-solving.
- Design and Engineering Silos: Many companies lack integration between design, engineering, and manufacturing teams. Our survey mentioned below touched on the point that many manufacturers lack true product development collaboration. Again, early cost and manufacturability insights in the design stage can improve collaboration and mitigate late-stage iterations.
- Inadequate Predictive Tools: A lack of real-time analytics for cost and manufacturability leads to decisions that fail to anticipate production bottlenecks. It is often due to limited digital simulation and insight tools that can model and predict outcomes during early design phases.
Addressing these challenges requires better integration of design and manufacturing tools, more robust supply chain visibility, and proactive cost and feasibility assessments during the early stages of product development. Solutions like those provided by aPriori are well-positioned to tackle these issues and streamline predictive manufacturing analysis and collaboration.
In our survey, manufacturability was 3rd on the list of most significant delays:
These statistics underscore the value of aPriori in empowering engineering teams to mitigate these challenges with real-time cost and manufacturability insights.
Data-Driven Insights For Accurate Cost Targets & On-Time Delivery
Here is how solutions like aPriori can address the above challenges and transform their operations into more profitable, competitive, agile, and efficient ones:
- Manufacturability Issues: aPriori’s real-time cost estimation and manufacturability analysis tools can empower engineering leaders to make smarter design decisions, reduce costs, and accelerate time to market. Its digital manufacturing simulations and the AI-powered design insights it provides can close the late-stage manufacturability issues early in the process. Additionally, hidden costs and production challenges can be identified at this stage, ensuring a more streamlined, timely path to a product launch. Moreover, if a late-stage change is necessary due to market trends or customer feedback (also known as scope creep), it can be remediated quickly and more cost-effectively, reducing potential delays.
- Cost Target Misses: Many engineering teams lack the tools to evaluate cost and manufacturability in real-time, leading to costly redesigns and delays. As a result, many focused on getting to market because it was the only metric they had. However, the design leader’s manager may be very interested in getting to market at the target cost. Early design decisions significantly influence manufacturing and operational costs. While specific percentages vary slightly, approximately 70% to 85% of a product’s lifecycle costs are determined in the design stage. Bulk costing enables quick, accurate cost estimates that align with new designs. Cost and engineering design process issues can be addressed in this most critical stage.
- Knowledge/Experience Shortfall: Digital manufacturing solutions can help compensate for a lack of STEM activities (like mechanical engineering courses). Manufacturers need STEM professionals to fill complex jobs. Automation using digital twins can help bridge the skills gap. Additionally, resource constraints and inefficient collaboration and project management can be addressed. Simulation tools can manage timelines, track progress, and identify bottlenecks. Automated systems can analyze the right resource allocation to meet project requirements and capacity. Freeing up time and talent creates brainstorming opportunities between departments to balance cost and quality targets and enhance newer design engineers’ knowledge and skills.
- Quality/Performance vs On-time Delivery and Cost: Design leaders are so focused on time-to-market as they have traditionally no way to measure the cost of their design. Consequently, time-to-market served as the only real metric. What’s more, adapting to changing standards and sustainability demands requires significant investment, which adds complexity to cost management. These systemic and operational issues complicate the cost-performance balance for engineering leaders. It underscores how aPriori can help engineering leaders stay on schedule by enabling real-time cost and manufacturability insights, reducing delays, and ensuring on-time product launches. But it doesn’t have to be an either/or proposition. Design to Cost (DTC) and Design for Manufacturability (DFM) make both possible and seamless.
Know The Root Causes, Mitigate Design Challenges, Optimize Product Development
Understanding and addressing these root causes requires streamlined processes, realistic planning, and adaptive project management approaches. Leveraging predictive analytics and robust project tools can significantly mitigate the above issues, building more agility, time to innovate, and greater profitability and growth into your organization.
Join Our February 26 State of the Industry Webinar
Do your products launch on time? Are you among the few meeting cost targets without compromising quality or performance? If not, learn what you can do to mitigate these issues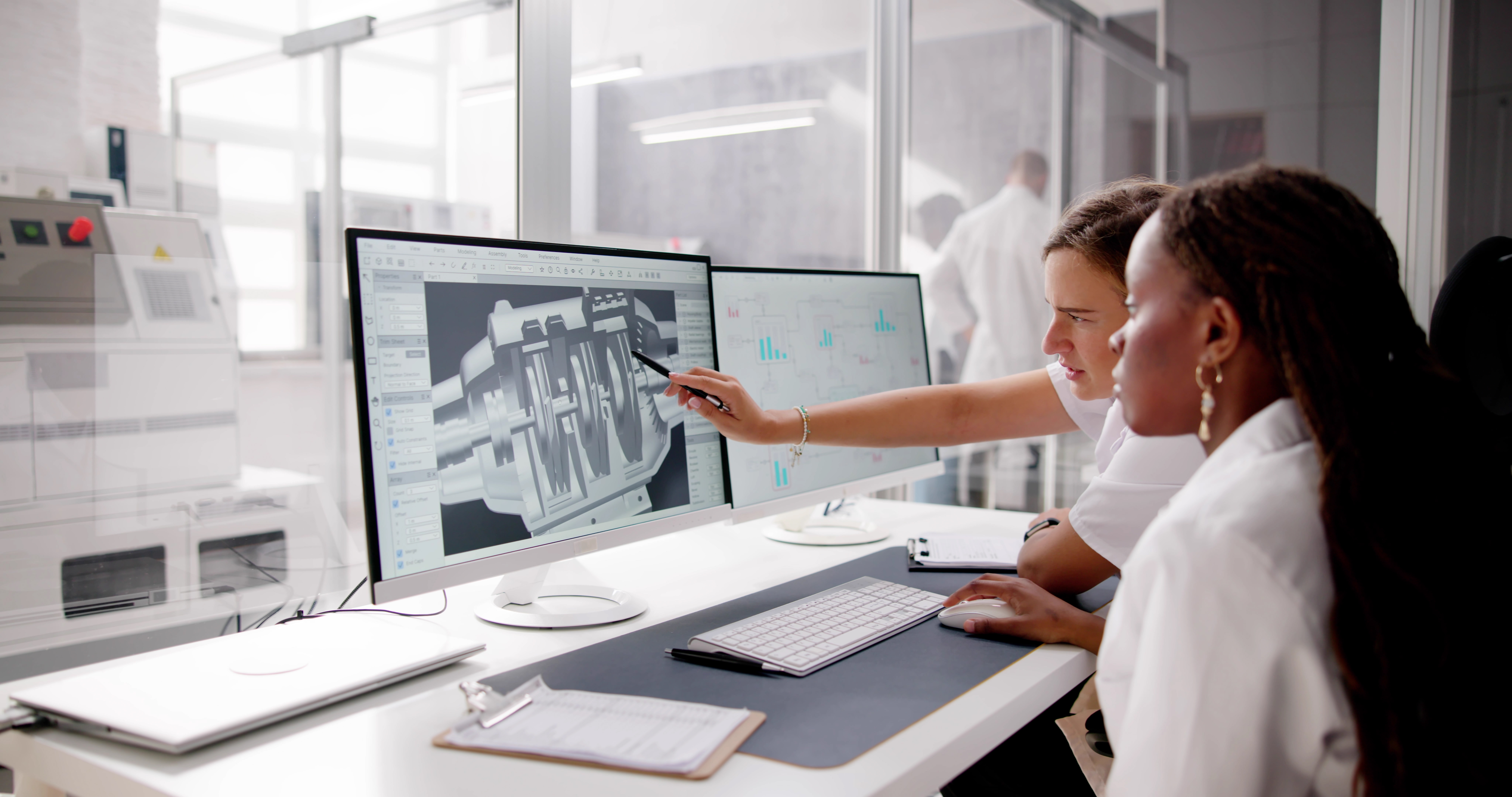