Alleviate Extreme Pressure: Manufacturing Simulation for Design Engineers
Key Takeaways:
- Today’s manufacturing companies and their engineers must innovate faster, ensure quality, reduce costs, and accelerate time to market, with fewer resources
- Manufacturing simulation for design engineers can identify manufacturability issues, reduce late-stage design iterations, and help reduce costs, carbon, and supply chain risks
The Full Article:
In the fast-paced world of engineering, the pressure to innovate, reduce costs, maintain quality, and deliver on time is immense. For engineers, these goals are constant, regardless of the company or industry. Moreover, there are over 241,977 currently employed manufacturing engineers, and 115,384 active manufacturing engineering jobs in the U.S. remain open. Demand is projected to grow by 10% between 2018 and 2028.
The increasing demands and complexities of today’s engineering projects can be overwhelming. In addition to being short-staffed and under pressure to accelerate time to market, engineers are tasked with learning and utilizing new tools that will help improve product development processes. Unfortunately, universities do not equip design engineers with these skills, which makes it challenging to create manufacturable designs. And, if a manufacturer’s suppliers are remote, this skill can become even more difficult to learn.
However, manufacturing simulation software emerges as a powerful solution to alleviate this pressure and enhance productivity for engineers and manufacturing operations.
Four Primary Engineering Goals
Engineers are expected to achieve four consistent goals: innovation, cost, quality, and on-time delivery. These engineering pillars are crucial for remaining competitive:
- Innovation: Engineers are focused on creating new and improved products. Examples of innovation include developing new and better features and meeting customer demands and needs. It requires a deep understanding of your audience, competitors, and the market. True innovation also pushes the boundaries of what you thought possible and simultaneously solicits customer feedback and tests concepts.
- Cost: Cost is central to product development and ensuring profitability. Engineers must find ways to reduce production rates without compromising quality. This involves selecting the optimal manufacturing process and minimizing material costs, labor costs, and the cost of logistics.
- Quality: Delivering high-quality products is non-negotiable. Quality assurance processes must be rigorous to ensure that products meet or exceed customer expectations. This includes thorough testing and validation to prevent defects and ensure reliability.
- On-Time Delivery: Timely delivery is critical, especially in industries where product launches are tied to specific dates. It’s also key to maintaining a competitive advantage. Delays can have a cascading effect, disrupting marketing plans, sales, and customer satisfaction. Engineers must stay on schedule with projects and address potential delays promptly.
The Correlation Between Engineering and Financial Performance
If the above goals weren’t challenging enough, engineering executives must be able to achieve and substantiate financial performance. Tying engineering objectives to the overall financial performance of the business ensures alignment with the company’s strategic goals.
This often involves setting top-line (the company’s gross sales or revenue) targets, ensuring that engineering efforts contribute directly to achieving them.
The Challenge of Capacity and Prioritization
One of the biggest challenges in engineering is balancing capacity with project quantity. Engineering teams often operate at full capacity, making it difficult to take on additional projects without compromising product quality or timelines. This necessitates a careful prioritization process to determine which projects to pursue and which to defer.
The conversation often revolves around what not to do rather than how to do more. It’s about making strategic decisions to focus on the most essential projects that will deliver the highest value to the organization.
The Need for Manufacturing Simulation for Design Engineers
Given these challenges, manufacturing simulation becomes a vital tool for engineering teams. Manufacturing automation solutions can help reduce manual effort and human error, streamline workflows and processes including those on the assembly line, and increase efficiency.
Here are some ways automation can address the pressure engineers face:
- Automated Manufacturing Analysis of CAD Model:: Using manufacturing simulation to evaluate design manufacturability and cost-efficiency, engineers get real-time notifications for potential issues, enabling them to optimize designs early and streamline product development cycles. aPriori runs in the background, automatically analyzing CAD models when they are checked into the Product Lifecycle Management (PLM) system.
- Bulk Cost Analysis:: Bulk costing enables quick, accurate cost estimates that align with new designs. With aPriori, engineers can assess product designs to identify any manufacturability issues from both a Design to Cost (DTC) and Design for Manufacturability (DFM) perspective. Cost and design issues can be addressed in the most critical stage – early in product development.
- Project Management: Simulation tools can help manage project timelines, track progress, and identify potential bottlenecks. This enables engineering managers to make informed decisions and keep projects on track.
- Resource Allocation: Automated systems can optimize resource allocation by analyzing project requirements and team capacity. This ensures that resources are used efficiently and that projects are staffed appropriately.
The Benefits of Manufacturing Simulation & aPriori aPriori offers capabilities that can significantly aid engineers in managing these pressures:
Feeling the Pressure To Innovate Faster with Fewer Resources?
Automate 3D CAD analysis for parts and assemblies early in the product development process, identifying risks, reducing costs, and accelerating time to market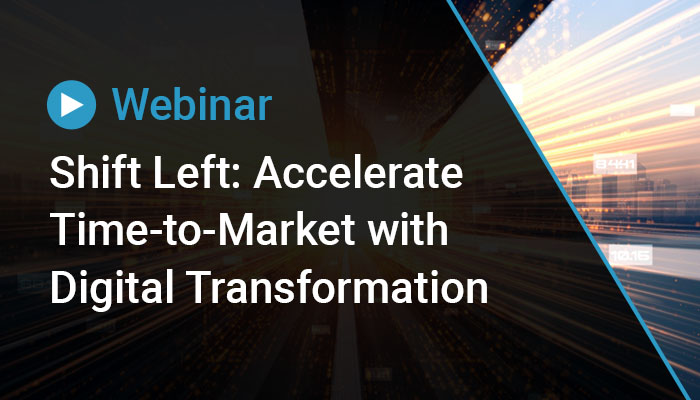