Reducing Delays through Design for Manufacturing Guidance
The manufacturing sector continues to face disruptions. Although many of these issues have dissipated to some extent, many still linger.
As a design engineer, your main focus is on creating high-performance products. Though supply chain issues and other disruptions may not be top of mind on a regular basis, they can impact the product lifecycle – from design and costs to sourcing and production.
However, you can play a critical role in reducing supply chain issues and other delays. Design is a seminal point in mitigating product development issues. Leveraging design for manufacturing guidance is the gateway to alleviating such pressures and resolving these issues.
In this article, we will highlight several delays manufacturers face today. We also will define design for manufacturing and explain how aPriori helps mitigate such delays.
What is Design for Manufacturing?
Design for Manufacturing (DFM) is a process by which product design engineers tailor their designs to meet two crucial manufacturing metrics: a) feasibility, and b) cost. It can identify and solve design and cost issues early in the process, saving time and money.
Many variables influence costs. For instance, removing sharp edges from a part and replacing them with rounded edges can save a substantial amount of money. Another example might be a product design that necessitates the manufacturing of a number of parts, which might not be feasible. DFM can provide insight into cost reduction with design feedback and help determine manufacturing feasibility insights that might not be obvious.
One aPriori customer discovered the benefits of DFM and our manufacturing insights. Rafael Advanced Defense Systems is a pioneer in advanced defense, cyber, and security solutions for air, land, sea, and space. The company was not receiving any bids on RFQs because their designs were too complex and needed specialist tooling/equipment to manufacture. Subcontractors were reluctant to take on the project.
Rafael turned to aPriori. By employing our manufacturing insights, Rafael enhanced their DFM. As a result, more people were willing to take on the project, which meant more competition that created more options and lower costs. Rafael has more than 127 active aPriori users and a waitlist of those who want to use our platform. With each passing month, Rafael has increased the number of components that are costed through aPriori. In one example, Rafael was able to reduce the original design cost from $1400 down to a modified design cost of $650. Read Rafael’s case study.
Examples of Manufacturing Delays
Global supply chain disruptions, labor shortages, and the Ukraine War continue to impact manufacturing operations worldwide. The financial impact has been profound, as the Interos survey indicated.
Although reshoring can alleviate some supply chain delays, on its own, it won’t eliminate them entirely. As the Ukraine war rages on, the area’s supply and transportation channels continue to face disruptions. Then there are the material shortages in this region as well. Raw materials such as aluminum, nickel, and rubber that come from the Ukraine/Russia area are now bottlenecked by war.
Couple the above with ongoing labor shortages. A shortage of skilled workers impedes not only the supply chain but the design process and production as well, leading to further delays. How can these issues and their associated delays be mitigated? What influence can design have over them?
How aPriori Design for Manufacturing Guidance Mitigates Delays
Product design delays are a perennial issue. A 2019 Gartner Survey found that just 55% of all product launches occurred on schedule. Of the 45% of delayed product launches, most were overdue by at least one month, and on average, 20% failed to meet internal targets.
Design for manufacturing guidance can dramatically reduce delays. It also can reduce costs and environmental impacts. In fact, 80% of a product’s cost is determined in the design stage. Additionally, 80% of a product’s environmental impact also is determined in the design phase.
Let’s explore several ways design for manufacturing guidance can reduce delays:
1. Reduce redesigns late in the product lifecycle to get to market faster. If manufacturers focus on a single area to reduce delays, it should be to reduce design changes. As the previous statistics indicate, product design has a huge impact on manufacturing costs, sustainability, and more. Time-consuming redesigns and design engineer change orders (ECOs) account for significant delays and costs, resulting in time-to-market lags of several months and to the tune of hundreds of thousands – even millions – of dollars.
Design for manufacturing guidance plays a compelling role in reducing redesigns. By utilizing them, the need to go back and forth to today’s version of the drawing board (the 3D CAD) is eliminated. Now, all cross-functional team members can communicate and collaborate faster and more accurately, breaking up siloes that often contribute to design decision delays.
With manufacturing insights, design engineers and other key players receive early design stage feedback, identifying potential issues – be it prohibitive costs, hard-to-acquire materials, expensive additional production steps, and more. Now, design features can be modified quickly, in the early stages, and cost-effectively.
Additionally, detailed models and clear, accurate data and recommendations mean that less senior design engineers can take on projects once exclusive to only the most technically skilled design engineers, thereby mitigating labor and less skilled worker shortages that also contribute to product launch delays. Rectifying DFM issues early in the product lifecycle means parts will be easier to manufacture. As a result, lower skills are required on the shop floor, alleviating labor shortage issues that lead to delays.
2. Gain critical insights into production issues and cost outliers in a matter of seconds vs. days or weeks. Manufacturing insights enable design issue remediation as early as possible. For example, additional machining steps, such as tool changes, can be identified and addressed quickly, reducing cycling times. Another example might be a part that has a tight tolerance or a part design that might require additional and unnecessary steps, slowing time to market. Manufacturing insights can help assess alternative materials or evaluate another production method to accelerate the product development process and time to market. Figure 1 provides an illustration of design feedback in action.
Figure 1
3. Break down siloes and foster communication and collaboration across the product lifecycle. Two-thirds of all siloed digital manufacturing initiatives fail to show a return on investment. Manufacturing insights break down siloes. They foster better communication and collaboration across the product lifecycle, which is essential to reducing redesigns and other delays.
Moreover, it is not exclusive to design either. Cost engineers can immediately gain insights into projected design and production costs. They can identify part cost outliers and work with the associated teams to eliminate or, at least, mitigate them. Quoting can streamline and respond faster. Sourcing can discern the best suppliers to use to work around supply chain issues and reduce delays and costs with tools like aPriori’s Regional Data Libraries covering 87 global regions. What’s more, fast access and comparisons to supplier prices position them to work with their preferred suppliers and negotiate more effectively. Production can consider possible manufacturing process issues at the design stage rather than months and at great expense later. Each phase, from design through production line, can play an integral role in reducing many manufacturing delays.
4. Identify manufacturability issues with highly visual and impactful insights that also provide remediation tactics. It’s one thing to identify manufacturing, sustainability, or cost issues. It’s quite another to come up with an effective solution quickly. Design for manufacturing guidance helps shorten production process times and circumvent product flaws or recalls by noting on your 3D CAD where potential issues lie (refer to Figure 1). More importantly, these insights offer practical alternatives without compromising value or cost.
It truly is a game changer in producing high-value, cost-effective products that can get to market faster so your organization maintains productivity, a competitive position, and profitability. In one aPriori customer case, their cost visibility lead-time was reduced from nine days down to two and a half, thanks to such insights. Another aPriori customer shortened time to market by 20%, using our insights.
5. Skirt supply chain issues by identifying key cost drivers. As previously mentioned, supply chain disruptions prove very costly for manufacturers. And, even in the best scenarios where there are no disruptions, manufacturers might be paying more for supplies than necessary. For instance, with greater material scarcity comes higher premiums on supplier prices. DFM can play a pivotal role in ensuring price comparison opportunities to secure the lowest price possible.
Manufacturing insights remove these burdens. Being able to assess manufacturing feasibility can help skirt supply chain issues. Perhaps parts bottlenecked in the supply chain can be substituted with similar parts. Manufacturing insights will provide such recommendations. A product that requires specific and, unfortunately, unattainable raw materials can be redesigned to work around them. Additionally, more comprehensive supplier knowledge and pricing improve relations (likely prioritizing your organization when it comes to obtaining supplies) and lead to more meaningful fact-based negotiations. The results speak for themselves. As noted above, Rafael enjoyed a 50% reduction in a part’s price. Another customer, Alstom, saw a 40% savings on recurring costs by implementing Zero-RFQ.
Get to Market Faster with Design for Manufacturing Guidance
Competition isn’t waning. It’s accelerating. Those who remain siloed will be left behind.
Accenture noted that industrial enterprises are reducing the product development lifecycle and shortening the time to market. Furthermore, their research indicated that these “speedsters” not only consistently performed at superior levels but also gained a distinct advantage by leveraging technologies like machine learning, cloud collaboration, digital twins, and agile engineering.
Need we say more?
Avoid Costly Product Designs and Delays
With aPriori's Design for Manufacturability, you can.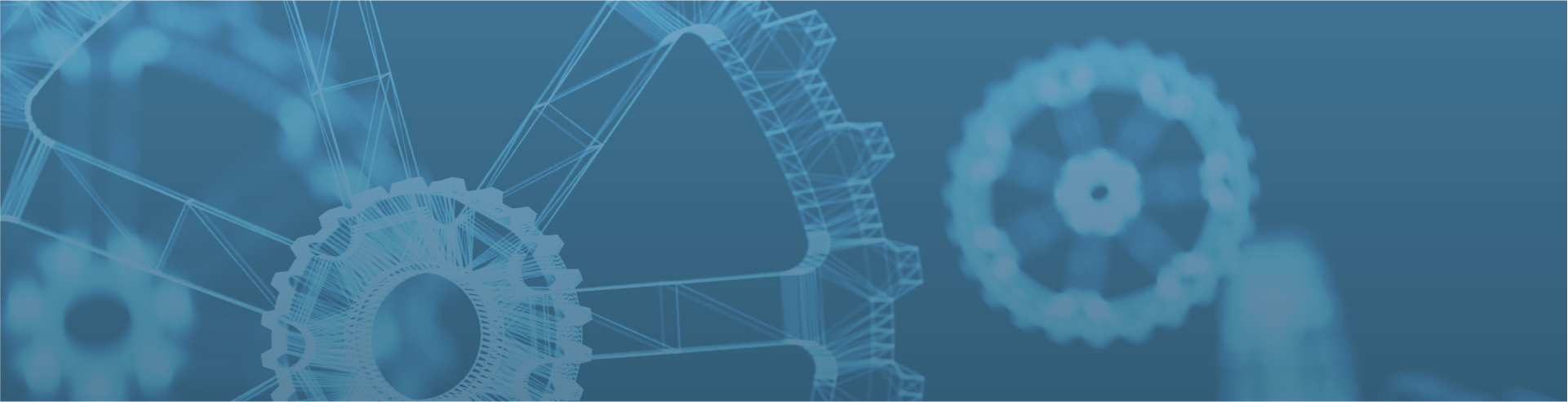