Case Study
Rafael Meets Design to Cost Goals with aPriori
Introduction
Rafael made a business decision to invest heavily in design to cost as part of their company roadmap. The ultimate goal was to manage cost from the design stage all the way up to manufacturing – including initiatives related to procurement, project management, system engineering, and requirements management.
The manufacturing insights provided by aPriori was the perfect technology to meet their strategy. Learn why in the following case study.
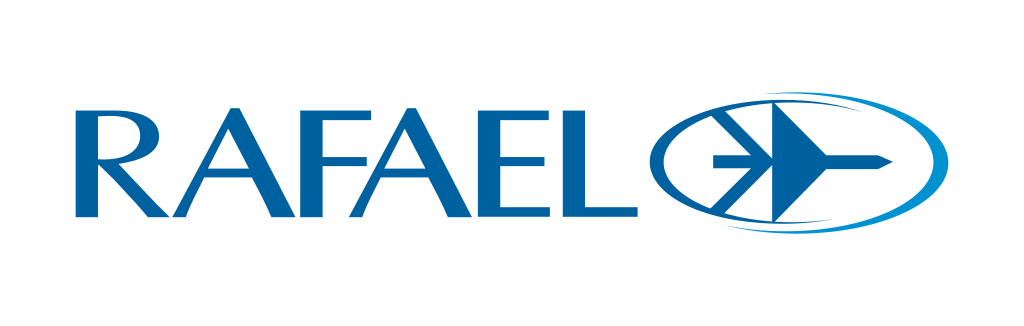
Company Details
Industry
Aerospace & Defense
Number of Employees
8,000
Revenue
$3 Billion
Website
aPriori Product
aP Pro
The Problem
Rafael had challenging design to cost targets to meet, and needed the right tools and technology to achieve themThe Solution
Provide all product development engineers with aPriori to collaborate across departmentsRafael's Design to Cost Goals
For more than 70 years, Rafael has pioneered advances in defense, cyber, and security solutions for air, land, sea, and space.
Rafael engineers involved in the product development process are typically expected to have vast amounts of expertise and knowledge.
In an effort to achieve cost targets and design to cost initiatives, these teams needed a technology that they could rely on to work together efficiently, seamlessly, and collaboratively.
Rafael chose aPriori as their technology partner to see their design to cost goals to fruition.
Successful Design to Cost with aPriori
By utilizing the digital factories and manufacturing simulation in aPriori, not only have the lines of communication opened up between the engineers at Rafael, but also they have been able to achieve up to 50% cost savings on parts by modifying design for cost.
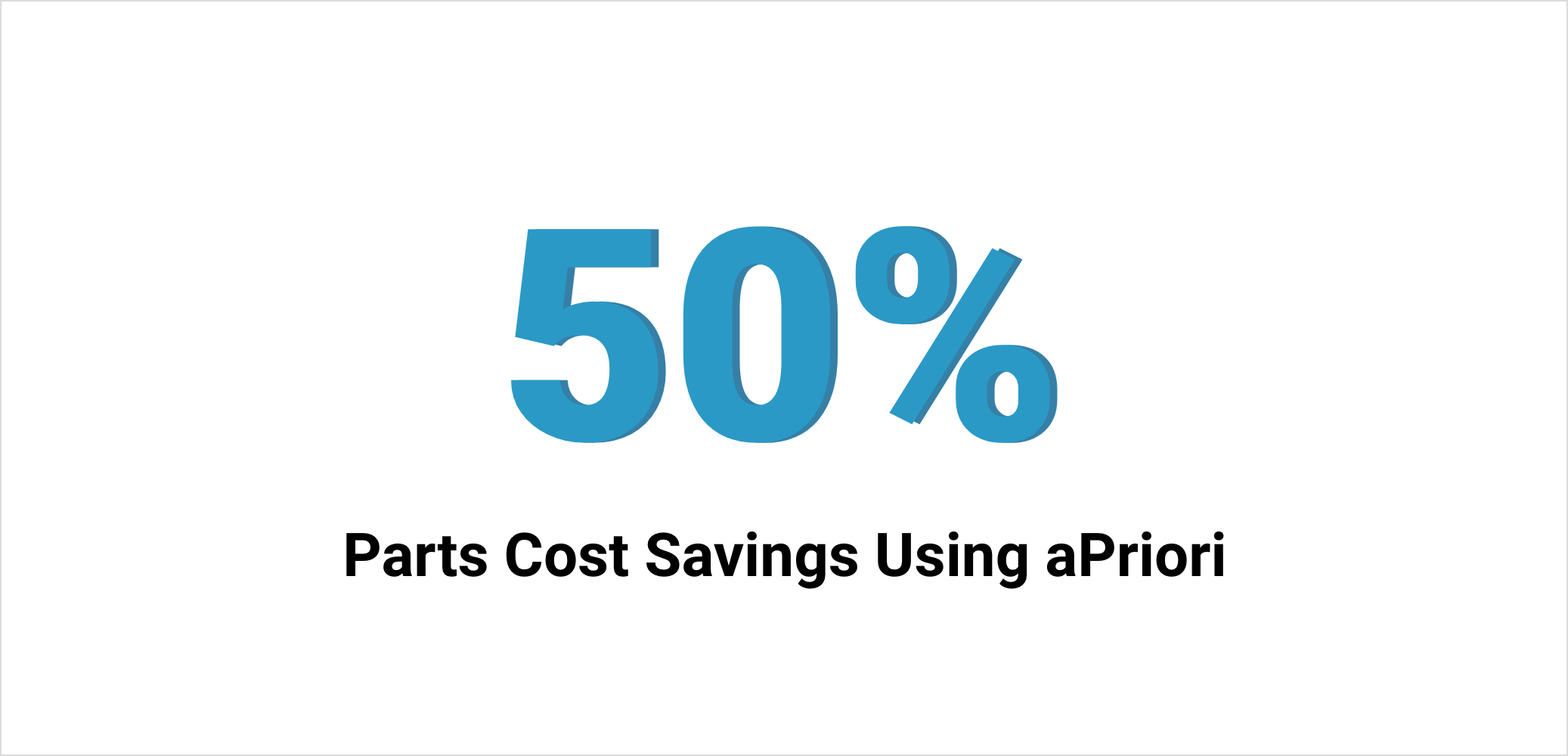
Results
In the video below, Eyal Siryon, MCAD Technology Team Manager at Rafael, presents at an aPriori Insights Conference. He shares a story about designing a part to cost with aPriori. The original design of this part was coming in at around $1,400. Using aPriori, they were able to simplify the design to achieve a modified cost of $650. But what’s even more interesting is the conversation that happened as a result of looking closely at the design through the aPriori lens. Take a listen:
Experience aPriori in Action
Meet with an aPriori expert and learn how we can help you to eliminate product costs, improve productivity, and reduce your carbon footprint.