Video
What Happens When You DON’T Design for Manufacturing
With aPriori’s manufacturing simulation software, you can rapidly identify key cost components and drivers for products you quote for your customers.
aPriori automatically detects potential manufacturability issues for a single part or for an entire bid package.
aPriori analyzes cost variances across a range of manufacturing different routings, materials or regions of the world – all in a matter of minutes.
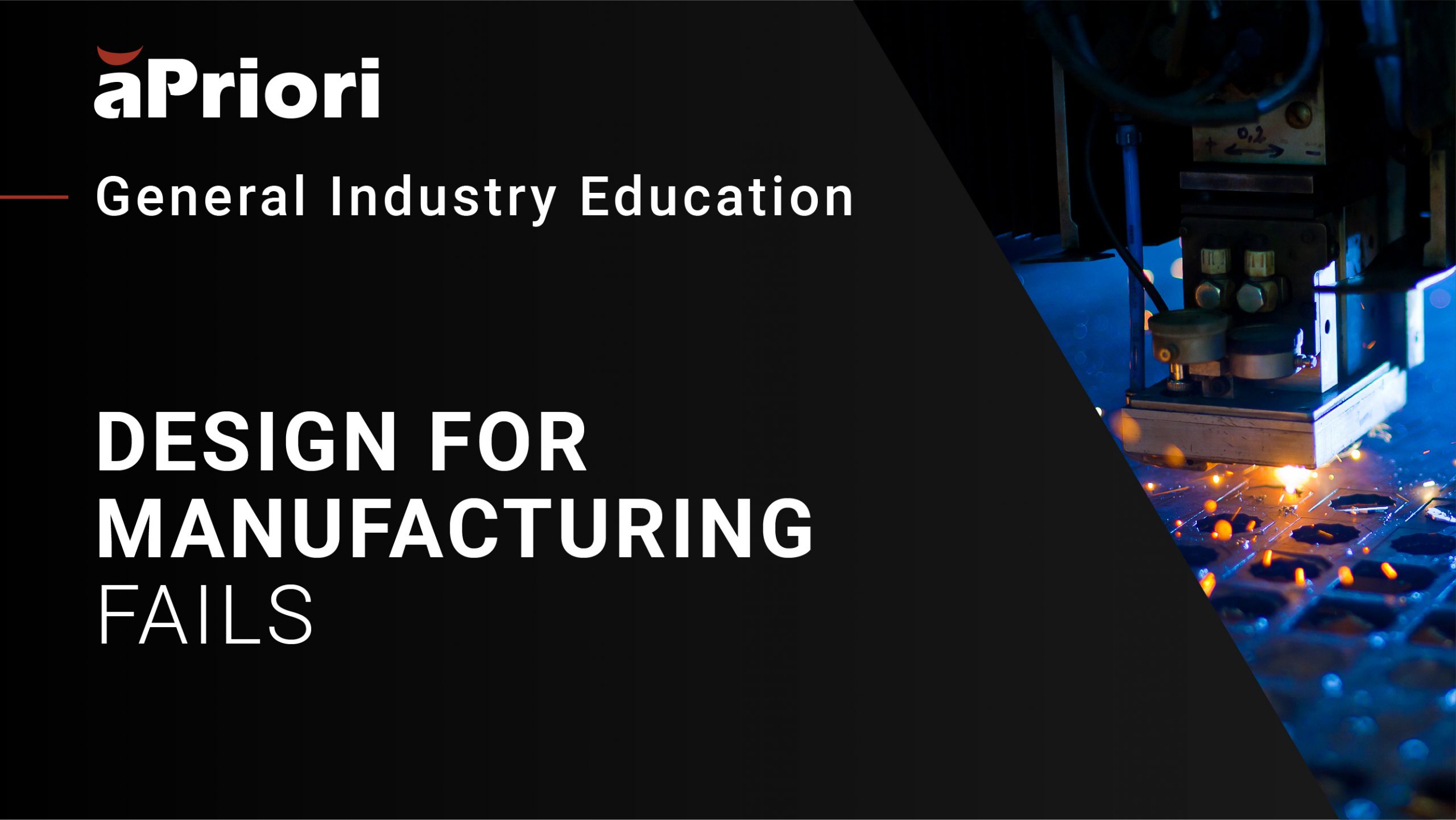
Transcript
Good morning. Welcome to this presentation entitled Go On, I Dare You To Ignore DFM. My name is James Ferguson and I’m the aP Design and DFM project manager here at aPriori. Before joining the team, I was an engineering manager at an automotive firm where I worked mostly in body engineering. I worked on a wide range of products ranging from VIP cars for heads of state through to two seater sports cars. And I was in doing this role that I really became passionate about getting designing for manufacturing right from the start. But being honest, that passion didn’t come straight out of the gates. It was kind of a learned behavior. I basically got tired of getting it wrong. I got tired of parts not turning up the build ’cause the tools were being reworked. I got tired of costs rising to the point where I had to trade feature for content and I just got tired of spending days, weeks, hours of my time and my engineers’ time fixing the issues that could have so easily been engineered out at the start of the process. The point of today’s presentation is to take you guys through some of that learning and hopefully impart some of that, the wisdom without you guys having to go through it and hopefully see the benefits of using design for manufacturing.
So the agenda today, we are going to take a quick introduction. We are going to look at some common reasons people put off DFM. We’re gonna look at the effect that ignoring DFM may have, and then we’re gonna run through some hypothetical case studies just to articulate that message a little bit more. Design for Manufacturing, or DFM, if you haven’t heard called that before, is very simply put the optimization of a part, product or a component to make it easier to produce or cost less. It’s absolutely vital to consider DFM during early concept development, although it can be done at any product design stage. The reason for that is basically trifold, the cost of change increases, so how much it costs to make the same thing at the start of the process versus the end of the processes are dramatically different.
Manufacturing Costs Understood at the Design Phase Have a Huge Impact on the Bottom Line and Time to Market
The effect of the change increases, that is to say you can change much more for much less effort at the start of the process than you can towards the end when perhaps interfacing parts or components have started to firm up their designs and their tooling routes. And then the ability to change decreases for much of the same reasons. You can change far less towards the end of the release. Common reasons to put off DFM, I’ll be honest, these are phrases that I’ve either myself said or heard, and I get it that nobody starts out to do a bad job, but what we can’t do is lose sight of what we should be doing versus what we are doing. And that’s one of the reasons that I constantly hear is that we’re too busy, we’re swamped, we’re stretched in our roles, and we just can’t take time out to do design for manufacturability in its own. For this product, time to market is more important. That’s often the case when we’re trying to reach a spring deadline or a fall deadline to try and be the first to market or get a new model year released before the end of the year. But we often forget that DFM entitles us to get the design right the first time through. So doing it directly contributes to how quickly we can get the product to market and the design team says they need that feature.
Why You Should Implement a DFM Process Early in the Design Stage
It’s sometimes hard to see people’s priorities for your own priorities, and sometimes we need to make sure that we’re telling the likes of the design team or the product development team the impact of what they’re asking for. So have we went back and told that design team that hey, you might want that split line there, but it actually makes the size of the tool three times bigger or it limits us to one production route, or it limits us to one or two suppliers in the world. So it’s really about conveying the impact that their direction may have on our designs. Just building on that a little bit more, these are what I’ve called engineers’ confessions. And again, these are phrases that in the past life I have definitely said or heard said in reviews regarding design decisions, it’s widely regarded that we can contribute up to 80% of a design’s cost savings within the early stages, the first 20% of the time spent designing it.
We can machine those parts. We can use stainless steel, fit this part before that part, welding, it looks better. These are all phrases that we can say with such freedom in early new product design reviews, but we can inadvertently or accidentally drive so much manufacturing cost into that product that we can never engineer out. Similarly, I’ve also been involved in projects where right before release, right before you’re about to cut the final draft of this product, incentives come in to cut cost, save 1% of your cost, reduce your fixings by one. These are all cost reduction work streams usually instigated when we realize we’re not trended towards the piece price that we needed to pit in the first place or to maintain pricing. It’s absolutely the right behavior to do. We should always make sure our designs are as lean as possible. But if we spent that same time upfront instead at the end of the program for the reasons highlighted on that first slide, we can influence more for much more less effort and for much bigger rewards as well.
Create High Quality, Low-Cost Designs Early in the Product Development Process to Streamline Redesign Needs Later
So it’s important to remember that we’re applying the same amount of effort throughout the design process. We’re just front loading it so we have an easier time towards the end of the release, ignoring DFM and in this work stream, we’re gonna focus on the the cost effect that that might have. Easiest way to articulate this I think is through a hypothetical model. So say that our department, our team, our company has won a contract: supply a basic bracket. We’ve received a basic sort of design spec. We want to do 10,000 units a year for a couple of years. It needs not to rust, it needs to operate in reasonable high environments. And there’s also pressure for possible in-house production. This is a pressure that I’ve felt myself when perhaps you’ve spent £2 million or £3 million on a new three axis mill or a CNC router or any number of parts.
There’s sometimes internal pressures and pulls that we feel that we need to design with that in mind. So say in this instance, say the first draft of this, we decide that we’re gonna use a three axis mill to push the utilization up. And because it’s a new toy and it’s a new machine, we want to use it, we can see that we can make this bracket through a machined route. We can see that the piece price is $105, which is obviously significantly high. But it does have very little tool set up and lead time. So we can see that if we flashed this out, we would have £105,000 project cost for the duration of this. That might be enough in this instance. We maybe make enough money there or there’s more economical pressures that say that we would go with that route. But if we don’t look design for manufacturing, or look at other options, we can walk away from huge cost savings over the product lifecycle. So if we had decided to cast this part or make it sheet metal or plastic molded, we’d stand a very good chance of still meeting that design brief but for astronomically lower costs. So if we plastic molded this part instead of machined it, we could have saved $103 per part, which obviously over the product lifecycle is a huge amount. This is something that I’ve seen and witnessed firsthand. And when we make a small mistake thinking that it might be okay on reflection. However, something changes, perhaps this bracket is more popular than we first suspected and the unit lifetime goes up to 45,000 units a year instead of the 10,000.
Design for Manufacturing Methodology Improves Time to Revenue
That means that if we’d stuck with that machined route, we would’ve been staring down the barrel of a multimillion pound commitment instead of with the plastic molding, which is just over 380,000. So obviously it’s just that idea of always looking at the alternatives and the different ways to make stuff to maximize the profit and still meet the design brief. Just for completeness, I was able to do all those studies using aP Design and DFM and the cost analysis tool within that. So I was able to run the same part in multiple process groups to give detailed cost breakdown. The good thing about aP Design is it also allows us to create this comparison view and we’re able to evaluate one design against the other. Making this DFM comparison is so easy. This next section builds on that idea of ignoring DFM and the effects it might have.
Cost-Effective DFM Example
In this instance, we’re gonna look more at the knock on effects from getting DFM wrong, not just drawing the line underneath the piece price and tooling routes. Again, I figure the best way to do this is to talk around a hypothetical or fictitious model. So again, in this instance, we’ve been asked to design and develop a raised node inside of casting that’s gonna be applied within a vehicle. It could be a ship, it could be a car, covered with a plastic cap, and we’re gonna develop it with and without DFM through aPriori, just for context. So if we take the initial design developed without DFM, we’ve got the requirement for a raised block surface with two precise holes and a matching capper finisher. We’ve run some early CAE and it shows that ribs are needed to strengthen it.
So we add some draft, we add some fillets, so it looks like it’s been properly engineered. We add the ribs as per the CAE’s simulation suggested, and we design the cap and finisher to suit the raised node and cap aligned perfectly in CAD. It has nice rounded corners, it has nice draft angles. We’re pretty happy that that’s a job well done. Bear in mind that this is a small element of what might be a massive casting. However, if we look at the concept design with DFM through aPriori, we have the exact same design brief, so it’s still the requirement for a raised block surface with two precise holes in a matching cap finisher. We still get the suggestion that CAE suggests that we need to have ribs. So we sketch the part up, adding that same initial fillets and draft angles and we run through aPriori’s DFM. We’re immediately told that the holes are a different size, which is needless, so we can align on those and make them precisely the same. We’re also told that the tolerance we’ve added in the PMI data suggest a particularly high tolerance. So we’re able to relax that and reduce tooling costs further. And we’re told that the ribs that we added based on the CAE simulation will sink and will not fill, so they must be made thinner.
We’re able to quickly digest that information, go back to our CAD model and edit it. We make the holes the same size, we relax the tolerances and we make the ribs thinner and longer, rerun the CAE to make sure it all validates and it carries on. Again, we end up with a part that looks slightly different, but we’re pretty confident now that we’ve done a good job and that part isn’t gonna give us any further problems. So if we build on that and we take these two concepts to launch, we can see that during the first crash test, the part on the left without DFM doesn’t perform as the CAE suggested. We kind of run around for two or three days figuring out why it’s not performing, what’s going wrong. We look at every aspect of that cast and remember I said it was quite a complex, quite a big casting, and after a couple of days we conclude that it’s actually due to the ribs not filling on this cast and note that it’s not performed as the CAE suggested. So we quickly take the model back through CAD. We update the ribs, so it does fill, we ascertain supplier quotes, which it tells us it’s gonna be 8000 pounds to amend that and we’re told it’s going to take 42 days.
We tell the component engineer who’s responsible for the plastic cap that they need to update, otherwise it won’t fit. And they’re told that it’s going to be a time-consuming 70 day lead time for a brand new tool and cost us $14,000. On top of that, we can’t just stop testing. This vehicle has a release deadline, so we need to get correct condition prototypes made. So we’re going to do that through soft tooling routes so we can carry on with the correct or as it should be condition model. We’re told that that’s going to have a 21 day lead time and it’s going to incur a significant tooling bill of around $67,000.
If we compare that to the final design with DFM, the part performs as CAE predicted, no further changes are required and parts are signed off and approved within the T2 parts. So just side by side summary of that part with our DFM is going to incur a minimum 21 day delay to testing, a 70 day delay to part sign off, almost a £90,000 tooling bill. And this for me is one of the more important things that we often ignore. It’s going to save us or cost us 65 hours of engineers’ time. That’s time spent revising CAD drawings, time spent doing studies in the root cause analysis, time spent in change management meetings where we’re explaining the new tools and managing that part in and all the work that goes with managing in prototype tools they have build or a test environment. We can absolutely see that not only is getting the design right the first time cost-effective, but it also gives the engineers so much time back, it just gives them an easier ride.
DFM Automation Results in Time Saved for Design Engineers
And that for me is the real benefit of DFM. Yes, it means that we’re always paying the bare minimum for piece price on the most appropriate tooling route, but this time back, this gift of time is so precious. And if we reflect back to some of the reasons that we’re often told why engineers can’t do DFM or take time out to do DFM, we can see that getting it right actually answers all of these questions for us. So using aPriori’s automated DFM early results in time saved fixing issues, ultimately reducing engineering change orders or engineering change requests, whatever we might call that, which means that we get a direct support of a faster time to market. aPriori also gives that information through the comparisons and allows us to see side by side models so we can easily and quickly articulate the design changes to the wider team.
The feedback is consistent, as in it doesn’t matter how many times you run that CAD model through it, aPriori is going to give you the same feedback. So it’s not subjective to whether you’ve had your coffee or if you’re doing this on a Friday afternoon versus a Monday morning. It’s always gonna be that consistent, reliable model. It’s also available from the moment that CAD is around. So as I said, it didn’t draw out that design process. As soon as we had that first casting node with some manufacturability constraints applied such as draft angles and fillets, we were able to just quickly run it through DFM and also through aP Design and we got that instantaneous feedback.
This is the point of today, to highlight that yes, design for manufacturing means that we are producing slicker and leaner models, but it’s also this gift of time and this tool that we can use to articulate design changes in our, why we need to make it, when we need to make it so we have a much easier time and we get back that time that we could spend doing other projects or fixing other mistakes. But it’s just that idea of doing DFM early will reap rewards later on down the process that we sometimes ignore or forget about. Thank you all for listening. Have a very good day.