Designing for Manufacturability is a Game Changer
Designing for manufacturability is proving to make a significant difference in cost reductions at a global agricultural and construction equipment company.
Tom Lefebvre, Product Cost Manager at CNH Industrial (a global leader that designs, produces, and sells agricultural and construction equipment) shared his recent experience implementing design for manufacturability processes alongside design for manufacturability (DFM) software early in the design process at CNH.
Tom originally presented these findings at aPriori’s annual Cost Insight Conference as a case study to show other manufacturers the benefits that designing for manufacturability has on both resources and time to market. The following article highlights important facts from Tom’s presentation. You may also access the full 20-minute case study presentation video here.
A little more about Tom Lefebvre: Tom has a long and accomplished background in manufacturing starting as a machinist at a large heavy industrial equipment company. Over the years, he continued his education and received both his bachelor’s and master’s degrees in industrial engineering while advancing his career. After many roles working for a handful of manufacturers and suppliers, today, he is a Product Cost Manager at CNH Industrial. Tom has years of hands-on experience that make him a credible thought leader on this topic.
Design and Manufacturing Engineers: Creating Their Happily Ever After
If there is one thing that both design engineers and manufacturing engineers can agree on when it comes to new development projects, it is that they all have limited resources.
CNH is always developing new products. The company mantra is “collaborate, collaborate, collaborate.” But the truth of the matter is that design engineers are under a brutal time schedule, and manufacturing has to take care of daily production including putting out fires. So, getting those two groups to collaborate can prove very difficult.
It is Tom’s job to help all of his engineers accomplish what they need to with the resources they have.
“I don’t know how many times I’ve identified a cost reduction, brought it to the manufacturing engineer and said, ‘Hey, we found this gigantic savings. Can’t we make this change?’ And he’s told me, ‘Well, I don’t have enough time,’ or ‘We tested this design, and you can’t do that because we’d have to go back and retest.’ Once you’re further down the design cycle, you’re literally handcuffed in regards to what can be changed and the impact you can have on cost reduction.”
CNH recognizes that the better the information they receive upfront, the better the design will be, which will result in fewer problems down the road when developing a new product. If all the issues are resolved upfront, then there are no late engineering change orders (ECOs) to consume precious resources which, ultimately, keep programs on track and on time.
Graph #1 below depicts the timing when a profitable and competitive cost for a design is possible: in the concept and development cycle. Cost reduction opportunities diminish rapidly, once past the development phase. At this point, manufacturing would be trying to tweak labor because the design is already set, and major changes to the design at that point are impossible.
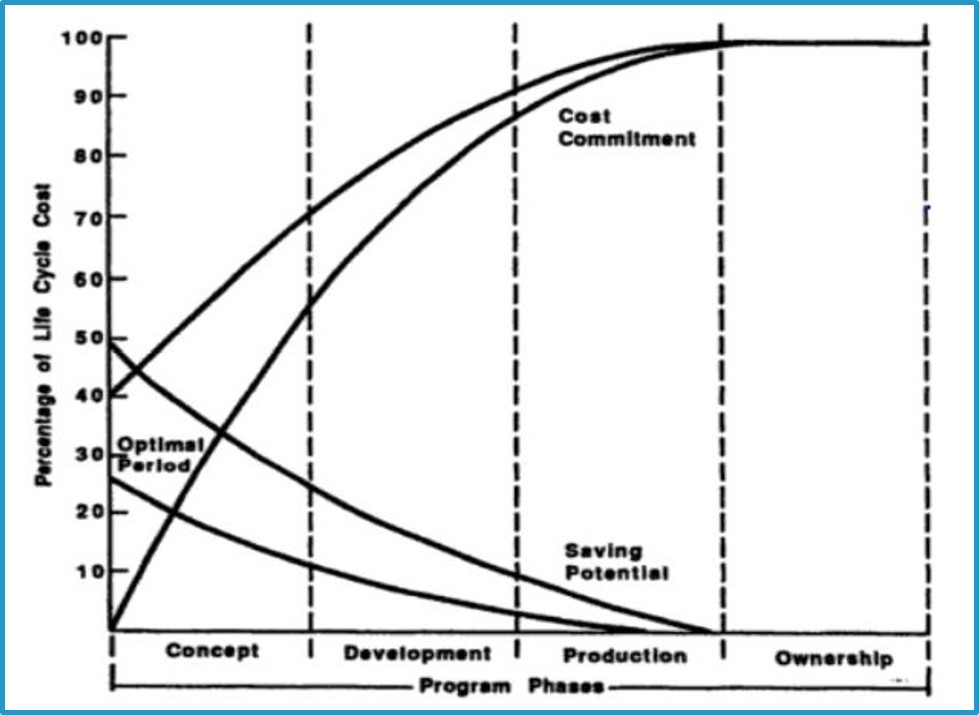
So, to significantly reduce future ECOs, the design and manufacturing engineers at CNH have teamed up. They recognize that having both teams on board with using the DFM software will result in maximum results. Using DFM software allows the design engineer not only to get immediate cost feedback while designing but also to become more cost sensitive as time goes on. This helps to forge the relationships between the two teams. In this sense, DFM software helps to remove friction between engineering and manufacturing.
Before & After Design for Manufacturability at CNH
In a design engineer’s world, the more robust the design, the better. Their job historically has not been to remove cost but to build the most magnificent design they can. The problem is that the most robust design usually has the most robust cost.
A typical situation at CNH before DFM might look like this:
A manufacturing engineer would have report back to the design team the utilization for a sheet. Because the manufacturing engineer wasn’t typically concerned with cost, the design team didn’t receive important feedback such as:
“Trim 1/8” off this part, and you will gain another row per sheet.”
Instead, he just did what he was told and gave the designer the utilization. After after implementing DFM software at CNH, a design engineer can now just look at the file and say, “Wow. I have a lot of room on the end of my sheet. If I cut the size of my part down, I can get better utilization.”
How it works: as a design engineer creates a design in CAD, the software recognizes manufacturability issues AND provides him with a cost breakdown for each step in the process. Manufacturability issues could include a “too-short” leg length or a pocket that is too small to get into the machine. The software alerts him automatically during the design process that there’s a problem.
Initial DFM Results at CNH
Two months after implementing a design for manufacturability (DFM) mentality coupled with DFM software, the CNH design team identified a number of opportunities for improvements to designs that they thought could immediately result in more effective manufacturability AND cost savings.
The following are the initial results from the first two projects.
1. Rethinking the Turnbuckle
Almost every machine CNH makes has a turnbuckle. Image #1 below depicts the previous design:
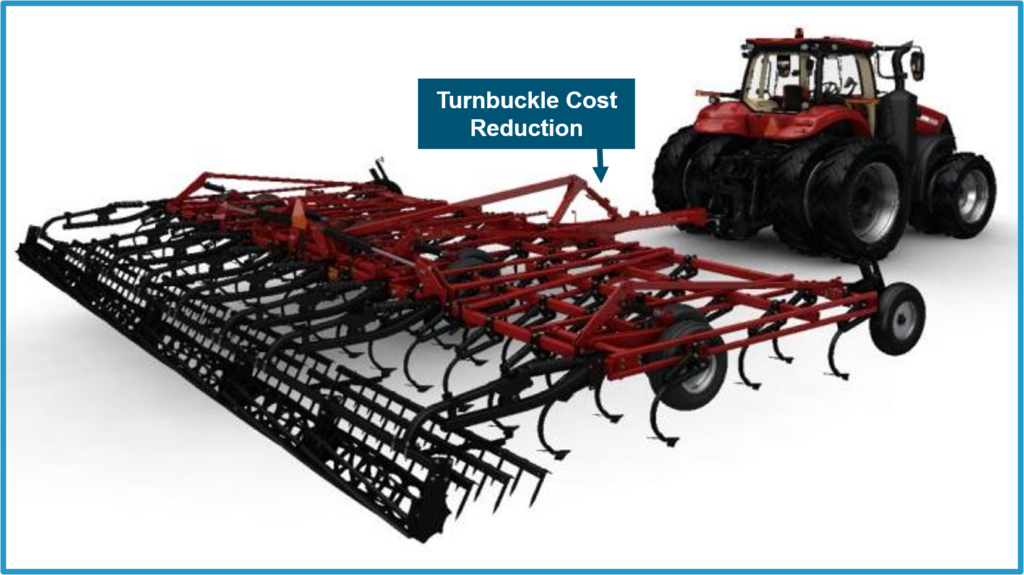
This welded design was 10+ years old and high in cost. The DFM software produced a new streamlined design with a manufacturing cost of $68.28 (see screenshot #2 below). CNH was paying $111.54 (see screenshot #1 below). They asked their manufacturing team to look at the results from the software. The team agreed that they should in fact be using the new streamlined design. See image below.
This one design change has resulted in a $100,000 savings for CNH.
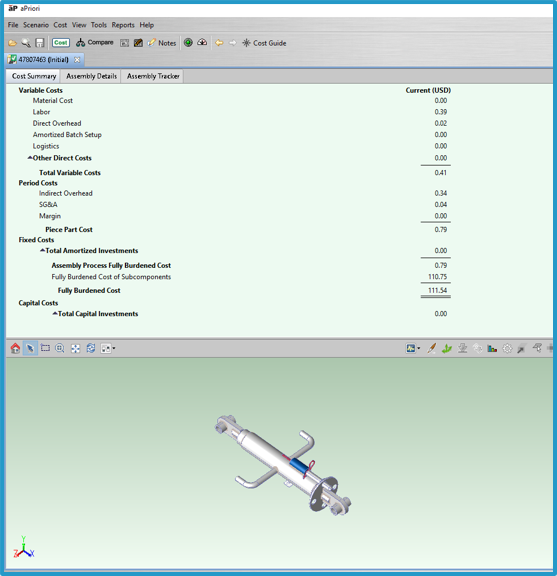
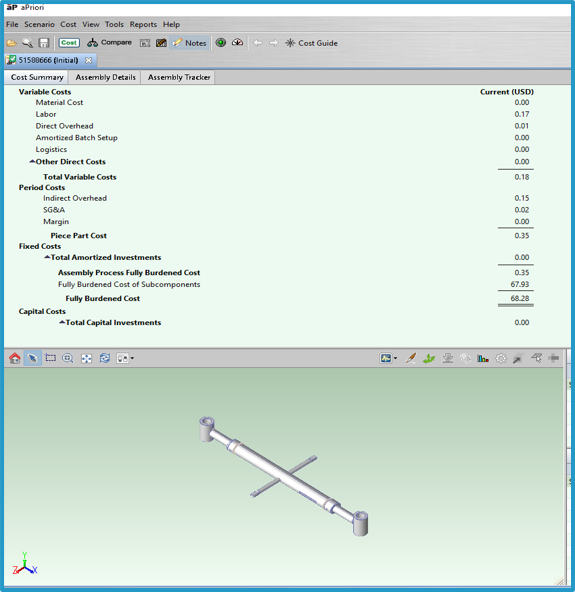
2. Wing Cylinder Guide and Rest
This next part is a washer (screenshot #3 below) made out of 1” material and cut on a laser – which is not cheap. The supplier was charging CNH almost $40.
When they put the design through their DFM software, they learned that instead of using laser cut process for this part, they could take a round piece of bar stock, saw it to the appropriate length, and drill the hole. This has resulted in a $14 per part cost savings (screenshot #4 below).
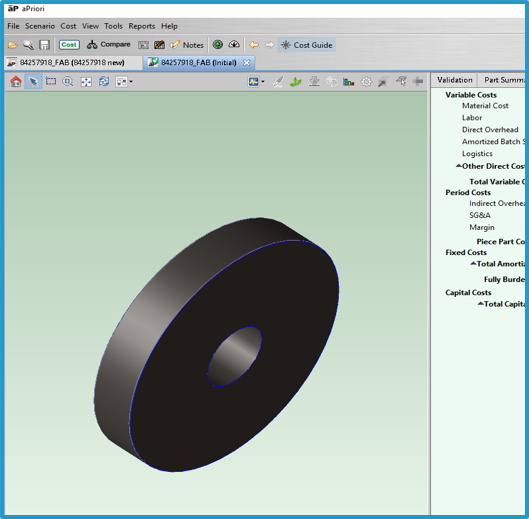
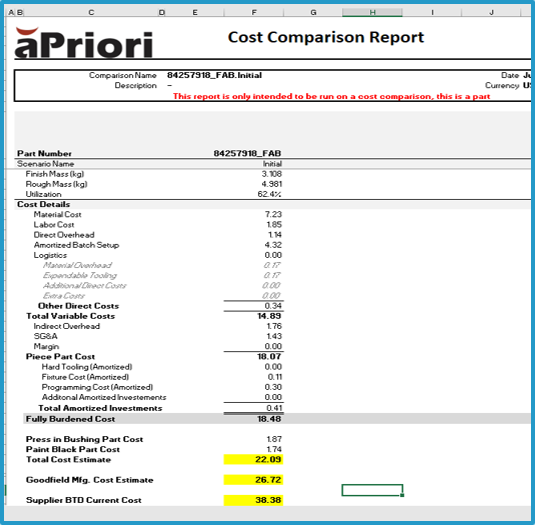
In just a two-week time period, CNH identified a potential $300,000 in savings by using DFM software.
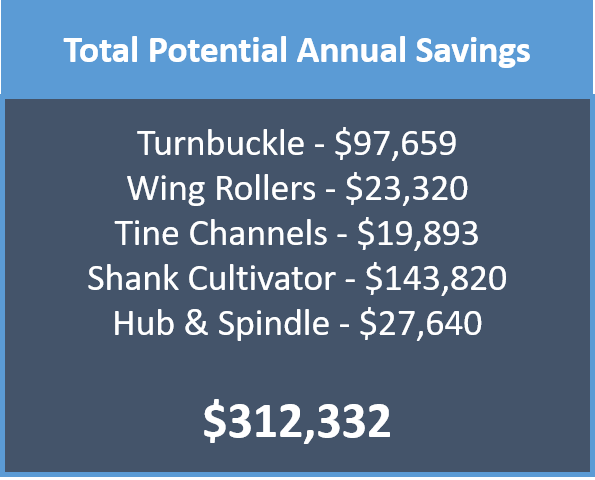
Benefits of using DFM software for purchasing parts
The use of DFM software also provides CNH with accurate should-cost data. This allows them to have data to go to their suppliers and ask:
“This is what the process in our DFM software says. Why is your cost different? Can you help us to understand your process?”
These discussions promote better negotiation with suppliers and result in healthier relationships in the long term.
For a more in-depth look at how to improve supplier negotiation discussions, get our article How to Use Fact-Based Discussions to Improve Supplier Relations here.
What to look for in DFM software
- Software that quickly identifies potential savings – Designers can tweak designs as they go, and can take cost out early in the design phase.
- Ease of use – Look for a tool that is easy for both manufacturing and design engineers to utilize and get up to speed quickly.
- Sourcing comparisons – The ability to easily identify sourcing regions that will provide greater cost savings is something that there is never time to do as a cost manager. A good DFM tool will do this automatically.
For more great tips on designing for manufacturability and manufacturing costing software, check out our article, What to Look For in Manufacturing Costing Software here.
Summary
Limited resources are an issue for all manufacturers, and CNH is no different.
CNH has recognized that because design engineers are the first to touch the product, the design phase presents the biggest opportunity in creating the most significant cost benefits.
Putting the right processes and tools in the hands of design and manufacturing engineers at CNH has fostered an atmosphere of collaboration. If you’d like to learn more about how DFM can help your company, feel free to contact us.
Need to Better Understand Manufacturing Cost Drivers During the Design Process?
We show you how in this demo video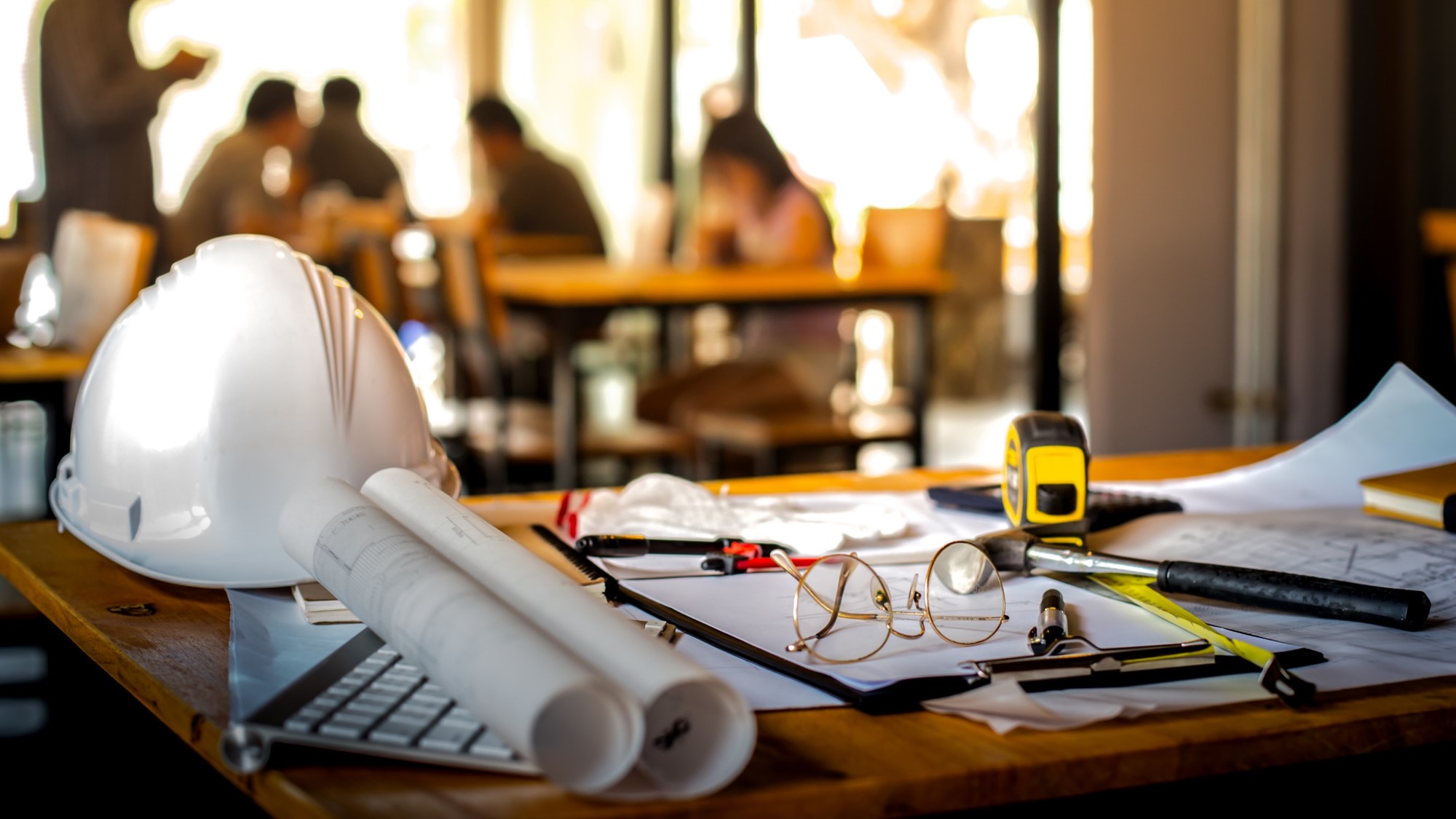