Product Should Cost Software Turns Novices Into Cost and Manufacturing Experts
Key Takeaways:
- Antiquated, disparate costing tools slow the process, lead to underestimating or overestimating, and reduce win opportunities
- Product should cost software quickly and precisely determines cost from Design-to-Source, and leads to agile management processes that create a cost-conscious culture aligned across the company
The Full Article:
Cost management has been an executive priority for more than 10 years, growing in importance every year, to become the top priority by 2025, according to BCG. Some of the reasons rely on key challenges such as cultural resistance to cost-saving measures, and the difficulty of changing a company’s structure and processes.
It’s no secret that too many manufacturers continue to rely on outdated methodologies and systems for product costs including manual/Excel tools. As a result, they face a time-consuming and arduous costing process that could compromise efficiency, time to market, and product margin – particularly if they are analyzing and costing high volumes of parts and complex products. According to BCG, only 48% of manufacturers surveyed achieved their cost-saving targets in 2024, and most say their companies struggle to maintain cost efficiencies beyond two years after the initial effort.
For example, without the right data-driven, digital product costs solutions, a $4 part can take as much as four weeks to cost. And should it really cost $4? It’s a little like trying to dissect the meaning of Dr. Seuss’s book One Fish, Two Fish, Red Fish, Blue Fish. It takes time, and there may be variances in interpretations.
By utilizing advanced product should cost solutions, engineers of all skill levels can estimate and understand product costs and manufacturing processes quickly and precisely. This data can also be shared and foster collaboration across the product development team and organization-wide, from Design-to-Source. Best of all, it can nurture a more cost-conscious culture.
Fostering A Cost-First Perspective
Manufacturing companies understand the importance of applying cost engineering principles across the product life cycle. By bringing a cost-first perspective to design and sourcing, product teams can help ensure they meet new cost targets.
However, companies fail to create a cost-first culture when their cost engineering teams use outdated systems and manual processes. Moreover, cost is the responsibility of all product team members, so access to those systems should not be limited to cost engineers. Without modern technology, cost engineers need enough expertise and time to analyze high volumes of new or redesigned products. This prevents them from providing fast cost-reduction feedback to design and sourcing teams.
Today’s cost engineers need simulation and data-driven product costing software. Advanced costing solutions help engineers of all skill levels estimate product costs, including direct and indirect costs, and share insights quickly and accurately across the company.
Examples of Product Costs
These are the expenses incurred to create a product that is ready for sale. They typically include:
- Direct Materials are raw materials used in the product’s production process
- Direct Labor includes wages of workers directly involved in the product’s production
- Manufacturing Overhead Costs are indirect costs related to production (utilities, equipment depreciation, factory rent, and supplies)
They are considered inventory on the balance sheet until the product is sold. Then they are expensed as cost of goods sold (COGS) on the income statement.
Hidden product costs can significantly impact a company’s profitability. Here are examples of such costs:
- Supply Chain expenses related to logistics, transportation, and warehousing. Delays, inefficiencies, or disruptions can also lead to unexpected costs
- Quality Control can incur costs related to inspections, testing, and defective product reworks
- Regulatory Compliance to satisfy industry regulations and standards including certifications, audits, and compliance management
- Environmental costs related to waste management, recycling, and impact mitigation
Understanding and managing total product costs from Design-to-Source (factory overhead, indirect labor, indirect materials, number of units, depreciation) is changing the game and improving overall profitability.
What is Product Should Costing Software?
Product should cost software, such as aP Pro, estimates and captures new product costs early in design. Using a unique 3D Model Geometry Intelligence module, it leverages digital factories, manufacturing process cost models, and regional data libraries to run precise cost simulations in real-time. Paired together, the data help identify and reduce design cost impacts.
At its core, it delivers manufacturers insight into optimizing new product costs to maximize margins and achieve product cost optimization goals via design for manufacturability and design to cost. It also provides a detailed view of the manufacturing processes, arming the sourcing teams with critical questions to ask when negotiating with their suppliers to deliver significant cost reduction through a win-win agreement.
Lack of Software Challenges
When using spreadsheets for product costing, companies sacrifice speed and transparency, effectively closing the door for a new and innovative approach to product should costing. For instance, cost engineers often rely on files (which must be updated to maintain accuracy) and spreadsheets to perform calculations, leaving them prone to human error. This manual process wastes time and prevents design teams from getting quick cost insights into their designs.
Traditional spreadsheets cannot keep pace with modern product development timelines. Product teams must have accurate, real-time costing feedback to meet cost targets and time-to-market (TTM) objectives.
Alongside spreadsheets, some companies may use product life cycle management (PLM) systems to store product data. Others have siloed, underutilized PLM systems, complicating the ability to find relevant data quickly. Disconnected data often leads to higher design costs.
Without the right tools, cost teams lack a baseline level of transparency to identify and prioritize cost outliers. Additionally, they are unable to analyze and manage large volumes of products as their role requires. This is especially challenging for under-resourced novice teams that are expected to make quick cost estimates.
Key Benefits of This Software
It is reported that 80 percent of product costs are determined in the first 20 percent of the product development process. This reaffirms the importance of having a design-to-cost (DTC) strategy that is supported by data-driven product costing software. Companies that modernize processes such as product costing can boost their team’s productivity by 26 percent.
Product should costing software algorithms modernize the cost analysis process for all cost engineers. Algorithms use the digital twin or 3D CAD virtual representation of a product, extracting design features for manufacturability analysis. Digital factories derived from real-world manufacturing conditions are also used to provide more accurate cost estimates.
Costing software can help seasoned cost teams achieve greater accuracy and efficiency and scale to handle higher workloads. It is designed to support the expertise of veteran cost engineers.
More novice teams no longer require outdated systems that are prone to human error. Instead, they can make quick, accurate estimates through advanced software with minimal configurations. Below are four ways product costing software can turn novices into highly skilled cost experts:
Modernize Product Costing to Create a Cost-First Culture
Modernizing the cost of a product analysis process is key to creating a cost-first culture in manufacturing. This software is a key enabler for manufacturers to strengthen their unique competitive advantage, including optimizing supply chains and streamlining product portfolios for greater cost efficiency. Companies must have this type of software to automate and simulate the way costs are estimated in the design stage. As a result, cost engineers of all skill levels can streamline the process, make accurate projections, and provide timely cost-reduction guidance to product teams. In doing so, manufacturers will drive an aligned culture and agile management from Design-to-Source.
Just as One Fish, Two Fish, Red Fish, Blue Fish encourages thinking outside the box and taking an investigative approach to things, solutions like aPriori enable product development teams to view costs through a different lens. As a result, they can quickly and accurately get closer to the true cost and optimize each stage of product development.
Do You Know What Your Should Costs Should Cost?
Our report shows how should cost analysis enables more accurate product costs, empowers fact-based negotiations, and accelerates time to market.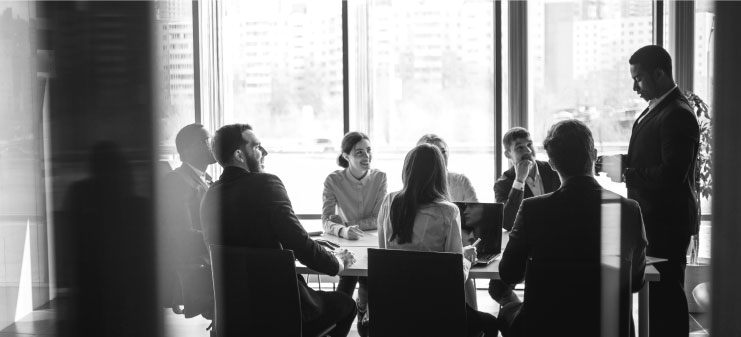