Mitigate Production & Cost Risks with Manufacturing Simulation
With inflation increasing, supply chains continuing to drive up costs, and other issues, many manufacturers grapple with more pressure to meet production schedules and profit expectations. Should they pass the cost on to customers? Absorb it themselves to retain customer loyalty? Compromise materials and quality to ensure profitability? While these tactics may work temporarily, there is a better, long-term solution that will ensure profitability, agility, faster time to market, high-value products, and customer retention.
In this article, manufacturing executives and other decision-makers will learn the benefits of industry 4.0 and how manufacturing simulation software can mitigate many of the issues, such as the supply chain, inflation, and material and labor shortages that affect the bottom line. We’ll highlight specific areas that manufacturers can leverage to be more productive, profitable, and competitive.
A more proactive, sustainable approach to managing costs will result in a healthier bottom line without compromising quality, size, or quantity for the customer. The key is to leverage technologies that can pre-emptively mitigate disruptions, better streamline processes, identify cost outliers faster, and detect risks earlier in product lifecycle management (PLM). Manufacturing simulation software can work around these and other issues in myriad ways without sacrificing quality, customer trust, or profits.
Lower Costs without Sacrificing Quality or Profitability
Rather than absorb the higher cost of goods sold or pass a price increase onto the customer, some manufacturing operations are working around these issues with “shrinkflation” – reducing the size or quantity of a product, while maintaining the same price as the original. Additionally, some manufacturers will downgrade product quality, even though the cost of it remains the same to the customer.
Low-cost manufacturing or lowering cost of goods sold should not be an either/or proposition. Manufacturers can mitigate costs without sacrificing quality or profitability with the right tools and a proactive approach rather than a “watch and worry” one. Moreover, you won’t have to compromise value or your customer’s trust by passing the cost onto them or downgrading quality. Consider how the following areas can help you avoid “shrinkflation” and ensure profitability.
Simulate Product Design
The first step in mitigating production costs, supply chain issues, and material shortages starts with design. Manufacturing simulation offers two opportunities to work around and/or reduce the risks involved with such disruptions. The first is through early design visibility. An effective design software provides insight into design flaws or issues in the initial stages that might influence cost, product quality, and time to market. The second allows for design resiliency. For example, designs can be reconfigured to bypass material shortages or reduce reliance on parts and assemblies affected by supply chain issues, identifying and remediating these issues through a redesign.
Conversely, design can play a crucial role in reducing scrapped parts and materials since manufacturability analysis can improve – and even simplify – design and pinpoint cost-reduction opportunities. As a result, there are more significant cost savings, supply chain bottlenecks become a non-issue, and manufacturers remain competitive without compromising quality, profitability, or customer trust. aPriori helped one aerospace company save more than $3 million over the lifetime of one of its parts.
Identify Manufacturing Cost Outliers
Inflation and shortages have driven up costs for manufacturers. It has forced many to sacrifice profits or take a “shrinkflation” product approach. These options create a lose-lose proposition for the manufacturer and the customer. Manufacturers can rely on manufacturing cost simulation rather than ding the bottom line or compromising product size, quantity, or quality. Digital manufacturing software can identify cost outliers, pinpointing areas where costs can be reduced or eliminated.
For instance, manufacturing simulation allows design engineers to enter their design into the PLM. If there is a design anomaly, the software will notify the design engineer, who can evaluate the identified component in question. Design variants, different materials, processes, or sources can be identified and remediated, collaborating with the entire team. Cost engineers can then refine the results, recommending the best course of action moving forward and often without passing that cost onto the customer or absorbing costs.
Reduce Cost of Goods Sold with Regional Data Libraries
In today’s climate, material shortages, supply chain issues, and inflation significantly impact manufacturers’ ability to procure the necessary materials cost-effectively and quickly. However, these disruptors can be reduced and/or worked around when manufacturers can quickly and accurately explore options globally. For example, suppose your regular suppliers are experiencing higher fuel prices and extra storage fees due to the supply chain. In that case, the Regional Data Libraries can provide more affordable options unaffected by these issues.
Such software leverages the component’s geometry to determine what is required to manufacture the component, interpreting time and cost implications. Manufacturers can identify suppliers in other regions with greater supply availability and/or lower prices – further reducing the cost of goods sold. More detailed cost comparisons over a broader range of suppliers can also be leveraged to negotiate better prices, thereby decreasing costs.
Streamline Manufacturing Operations
Digital manufacturing streamlines production, enhancing time to market. Additionally, automation can help compensate for labor shortages or costs associated with staffing. According to a Deloitte report, although 84% of manufacturing jobs lost during 2020 were added back to payrolls, turnover remains high. To retain them, manufacturers should involve existing employees, providing upskilling opportunities as well as implementing more technology-focused training and education. Employees will be better engaged, boosting performance and enterprise-wide success.
However, that alone is not enough. Manufacturers must implement effective manufacturing simulation software that can maximize output with fewer resources and regardless of current disruptors. A single software platform can improve processes across the PLM while mitigating costs, dealing with a reduced workforce, and working around and through supply chain issues, and material handling or shortages.
Weather the Cost Rollercoaster with Manufacturing Simulation
Manufacturing simulation provides an exceptional opportunity to shore up cost and pricing strategies to weather any storm and any scenario. It enables organizations to take a more proactive and agile approach to reduce their production and cost risks while remaining profitable and competitive.
The Deloitte report outlined four potential inflation scenarios, ranging from blue skies (inflation’s effects are minimal and temporary) and sun showers (interest rate increases are moderate and short-term) to stormy weather (inflation rises quickly as interest rates increase to offset inflation) and downdraft (lower growth, more unemployment, and reduced corporate profits). Manufacturing simulation is equipped to handle any weather at a moment’s notice, while creatively and effectively addressing the higher cost of goods sold.
Production & Cost Risk Case Study
Danfoss improves pricing. Gains a competitive edge with aPriori.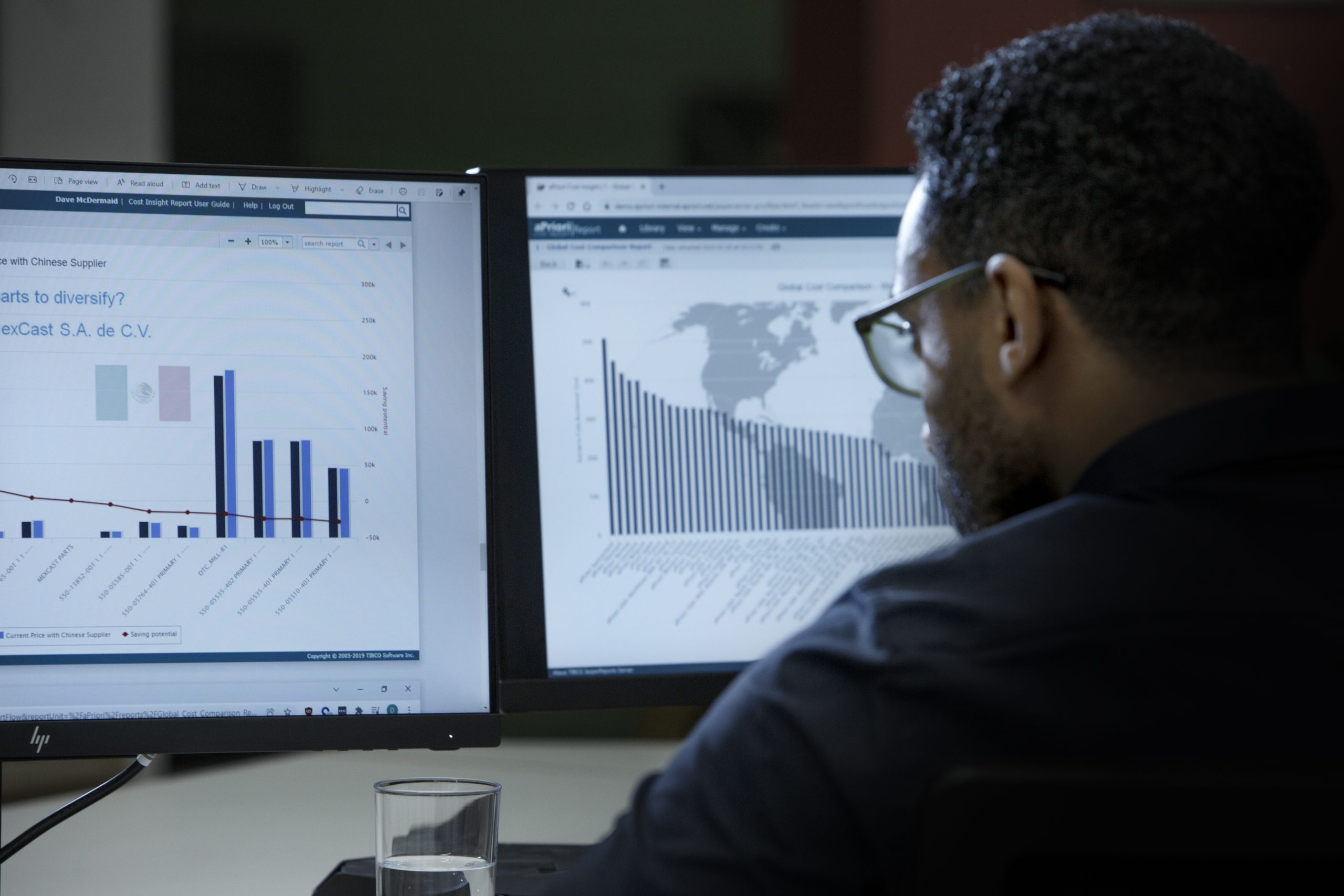