Video
Leverage the Digital Thread to Reduce Product Costs
Each member of the product development team can play a key role in reducing manufacturing costs for improved time to market and faster time to revenue. With aPriori, each of the key constituents involved in the product development lifecycle, including design engineers, sourcing professionals, cost engineers, and manufacturing leadership can collaborate together, proactively identifying manufacturing defects, generating and refining cost estimates and analyzing the data.
In this video “skit,” aPriori team members play the role of each of the stakeholders listed. Watch, listen, and learn how to use aPriori to reduce manufacturing costs in this fun, interactive role-play video.
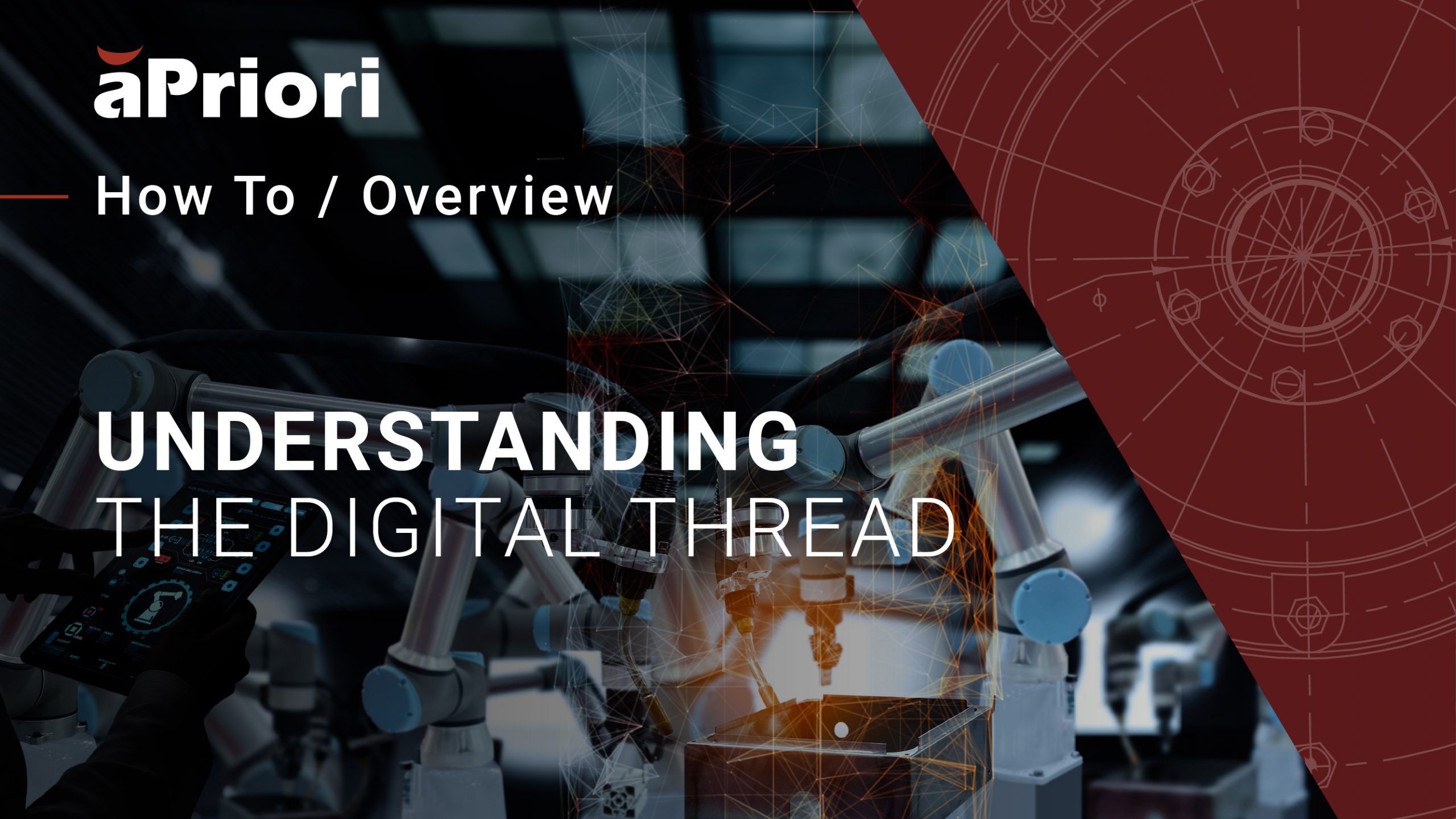
Transcript
Hello everyone and welcome to this session titled Cost: Collaborate From Check-in! My name is Samantha Scaglione, and I’m an Associate Product Manager at aPriori. I am joined today by Senior Cost Modeler, Mark Dignum, Senior Customer Success Manager, Nikita Shah and Product Manager, Barton Phinney. Our session is a little different than anything else you might have attended so far at this year’s Cost Insight Conference. We’ve prepared a short skit where we assume the roles of key constituents involved in the product development cycle. In this skit, you’ll see us using aPriori to collaborate amongst the team and across departments, proactively identifying manufacturing defects, generating and refining cost estimates and analyzing the data.
Before we jump into our skit, I just want to take a moment to walk you through the cost savings workflow that we’re going to outline.
Automation Can Positively Affect Cost Reductions in the Manufacturing Process
We can start with the design engineer. Through Cost Insight Generate, the parts the design engineer is working on are automatically retrieved from the PLM system for aPriori’s analysis. He receives an email notification with a summary of this analysis and can click through part links to open those parts in Cost Insight Design, a role-based application with guidance and insights curated for design engineers. After reviewing this guidance and revising his design, the design engineer can update the part status and assign it to the cost engineer for refinement.
The cost engineer can open the part in aP Pro to review the manufacturability details, refine the process routing and set machines. She can recommend design changes and assign the part back to the design engineer or update the part status and assign it to an individual in strategic sourcing. The sourcing professional would use the cost engineer’s refined estimates for analysis and negotiation in the supply chain, labor costs, overhead costs, production costs, and so much more.
Today, the sourcing professional can leverage matrix costing through aP Pro and targeted reports through Cost Insight Report to identify where and how much to source. Jumping back into our collaborative workflow, the team lead or project manager can be involved throughout the project to analyze the data from the team’s work. She can leverage Cost Insight Report to track value and how cost targets are being met, to identify outliers with severe manufacturability issues and high cost impact, and to understand the team’s progress throughout this process. I know I’ve mentioned several applications, aPriori Professional, Cost Insight Report, Cost Insight Design and Cost Insight Source. These applications share a single global database that supports secure collaboration so you can access the same scenarios and the same data. This really gets your team the opportunity to take advantage of the curated content and targeted features in our role-based application suite.
Now that you have a little bit of background, I’m pleased to present you with our skit so you can see this workflow in action.
How to Streamline the Collaboration Process Between all Product Development Stakeholders
Welcome team! We’re getting ready to kick off our next big project. This time will be working on a drill engine, so if we want to take the time just to introduce ourselves to one another and tell each other a little bit about our roles and how we’ll be working on the project. I’ll start. I am Samantha and I am the manager for this project, so I’ll be overseeing the project and the process as we go from designing the CAD models to refining our estimates and passing it on to sourcing.
BP: My name is Barton Phinney. I’ll be our strategic sourcing manager on this project and I’ll be looking at how we can use aPriori to determine what regions we should source our product within.
NS: My name is Nikita Shah. I’m a senior cost engineer. I’ll be taking the design once our designers are finished working on it, making sure that the cost estimate has been refined and getting it over to our sourcing team.
MD: I’m Mark Dignum. I’m a design engineer responsible for form fit and function and responsible for some manufacturing too, by working with Nikita.
SS: So we’ll be using aPriori for manufacturability guidance and cost management throughout this project, so I went ahead and set up a workflow through Cost Insight Generate to pick up all of the parts as we check them into the PLM system. I know, Mark, you’ve been doing some initial design work already, so I did set up a dashboard to monitor the progress on this project. Let me pull it up and share my screen so you all can see. I did notice that aPriori detected some major manufacturability defects associated with the manifold specifically, so I think, Mark, if you don’t mind prioritizing that as you continue your work.
MD: Yeah, absolutely. Makes sense.
SS: Perfect. And as you go through the process, make sure that you are assigning your reports to Nikita once you feel like you’ve addressed the bulk of the manufacturability defects and set that status to “analysis” so we can have some visibility into where we’re at in this process.
MD: Okay. Sounds good, Samantha. I’ll get on that.
SS: Perfect. Thank you so much. And I think we’re all set. Thank you all for coming to this kickoff today.
Start with the Design Engineer to Identify Early Cost Savings
MD: Alright, so this is the drill engine that we’re working on. It’s a pretty small engine. Obviously, it’s just powering a drill. And it looks like I did just get the email that Samantha was referring to from Cost Insight Generate, and it has a summary of all the parts that I checked in recently for this drill engine, and it does look like the manifold is the only high manufacturability risk. So I’m going to take a look at the feedback that I’m getting there and see why this is a high risk component. Okay, so that link opened up for me and I now see my part in aPriori. I’m just going to explore these 37 guidance issues. And okay, it looks like I have some sharp corners and some contoured surfaces. I understand contouring but sharp corner, just to refresh my memory of what that means, I take a look at this help. Okay, that makes sense. Looks like places where our cylindrical tool can’t make some geometry choices. See where this happens on my part. Oh, okay. This is pretty obvious to me. It looks like it’s in a few of these corners that I modeled. I really just made a simple mistake and forgot to add my rounds in these corners. So this will be an easy change for me, really has no impact on my overall design. I just really need to make sure that there’s clearance for the mounting bolts to go through and clear these areas, so I should be able to add around there. No problem.
And then I’m going to take a look at these contoured surfaces because I’m a little surprised that I have so much contouring. Oh, this makes sense to me too now. So I added these perimeter rounds really just because it looks kind of good, and also I was working from a previous casting. We’re going to try to make this part out of a billet now, since it’s pretty low volume, so I just kept these around, but I don’t need them for my design, so I can remove those external rounds. But these internal surfaces of the manifold, this geometry is really critical to make sure this manifold mixes air and fuel properly. So I’m going to keep those around, I really need them so but this is good feedback from me. I hadn’t realized that these should be such problems. So I’m gonna go back into Creo and just make those changes really quickly. We can get some new results from aPriori. Okay, that’s that perimeter contouring that I had the artifact from this previous casting, so I’ll get rid of that. And then on my sharp corners, I’ll just add around it. Let’s just go in and add it. That’s a little bit too small. Let’s go with a two millimeter and that should be pretty decent size actually. Go with a five. And I’ll just go around and add these quickly.
Alright. So those changes look good. Got rid of those contoured surfaces, added those rounds. I’m happy with this. So I’ll check this in. Alright, and I should get an email from aPriori soon with new results, and looks like from the summary my risk rating is back to well, but let me just to take a peek at what the results are and understand fully what I got rid of. And okay, as this is loading, my guidance issues are down to four. That’s good. I think that was all those internal features on the manifold but let me just check. Yeah, so it’s just those four internal faces that we really need to make sure this works properly. So this looks good to go. I’m gonna assign this to Nikita and I’m pretty happy that I caught these before passing it over to Nikita, because I don’t like to waste her time and she does get frustrated at me when I make these silly mistakes. So she’ll be happy I resolved those. I’ll pass this over to Nikita and she can do some further analysis on it and really drive into cost drivers to make sure cost is fully captured. That’s really what she’s good at and what she should be focusing on.
SS: Okay, it looks like we’re making some great progress here. The last time I looked at the scenario status report, everything was still in new with Mark, the design engineer. It looks like he must have sent everything except for that manifold with the bulk of the manufacturability defects on to Nikita early on, so she was able to refine those cost estimates and pass them on to Barton in sourcing. Looks like the manifold is the last piece she has left to refine.
Cost Engineers are Focused on Cost Reduction Strategies and Continuous Improvement
NS: Hey everyone. This is Nikita, the Cost Engineer. I’m gonna start my day by checking into aPriori to see if there’s anything assigned to me. So we’ll go to the search panel here. Assignee has already been set to me, so I just need to click “Find”. Alright. So it looks like there’s two things assigned to me. Let me just go to this manifold. Alright, so it looks like this has already been costed successfully, which is great. Let’s just check the validation panel. Looks like all the GCDs costed appropriately. If we go over to design the cost, great, no machining issues! So looks like this is a pretty manufacturable design. I’m going to make a few changes to the cost here. So I’m gonna go to the routing selection. We’ll need to add some inspection as well as the heat treatment process, and we’ll also need to add another secondary process. Let’s add some ultrasonic cleaning and we’ll apply that.
Alright, looks like I’ve got my secondaries added. I’ll go ahead and also just make a quick change to the manufacturing process setup options because I know for this to work, the routing strategy will be a little bit different, so we’ll change this so that heat treat happens in between roughing and finishing. We’ll go ahead and recost.
We’ll just go over to the cost summary here. Alright. So that looks about right. I guess it’s time to get this over to our sourcing and procurement department and see if they can figure out where to source this part. I’ll go ahead and assign this department. Press okay, and just need to save, and we’re good to go.
SS: This is great, it looks like the design work is done, the cost refinement is also finished. Now, the entire drill engine assembly is over with Barton in sourcing, so we’re really moving along quickly with this project. This is awesome.
Sourcing: Direct Labor Costs, Energy Costs, Material Costs, and Manufacturing Overhead All Affect the Bottom Line
Barton Phinney: Okay, hi everyone. Again, my name is Barton Phinney. I’m going to be the strategic sourcing manager on this project. And my primary goal is to figure out where we’re going to source this drill engine assembly. So the first thing I’m going to do is go to my search window and see if Nikita has finished her analysis. I’m going to do that by searching for my user name as the assignee, B Phinney, and then I’m going to search for a status of waiting. Okay? Alright. So I can see that this drill engine assembly right here is assigned to me so it’s ready for me to try to figure out where I’m going to source this thing. So I’m going to open that guy up and then the first thing we need to do is see what regions I potentially might want to source this in. So I’m gonna go to cost and then matrix costing. And I’m going to select a few different regions for me to look at. The first one I’m going to do is aPriori China, East Shanghai and then I’m also going to take a look at aPriori India, and I’m also going to look at our suppliers in Mexico. And for just good measure, I’m going to also select aPriori USA so that I have a baseline to compare against.
Okay, great. I’m going to keep our annual volume at 3000, and batches per year, I’m going to keep at 12. Click Add. And now I’ve got this matrix of regions, VPs, annual volume and batch size. And so aPriori will go ahead and take the root scenario and copy it has all these different scenarios with these inputs and then go through and cost them. Okay. So I’m going to click Okay and go do that. Okay, so now that I’ve gone through and done my matrix costing, I can see I have an assembly in each of the four regions that we specified in the matrix costing, and to better compare these costs of the assemblies and then their components, I’m gonna go into aPriori Cost Insight. So I’ve run this report in Cost Insight, and it’s called the regional cost comparison report. This is one that I built in our ad hoc views. And what it’s showing is our relative annual spend on the y-axis here, and then each part on the x-axis, and each one of these bars represents one of the regions that we costed in. And so obviously, my parts with higher spend are on the left here, and the parts with my much lower spend that I’m probably not too concerned about are on the right.
And so, if we look at each one of my higher-spend parts, we can see that in most cases, this red bar is the lowest, which is aPriori Mexico. In a couple of different parts you know, the cost might vary a little bit, but since these are really my high-spend items, this is where I’m going to want to spend my focus. And so, I’m going to decide that we’re going to try to source this assembly in the Mexico region. So, if I go back to aPriori, I’m going to open up my drill engine assembly that was costed in Mexico. And I’m going to save a new scenario just so that it’s a little easier to compare. Right now, it’s got the default matrix scenario, which can be a little cumbersome to work with. So, I’m going to do Scenario, Save as New Scenario and Children, and then I’m going to do Mexico Region. So, right now, it’s going to go through and save off a new scenario for the overall assembly and then all the other parts that are under it. Okay. So, if I go into my assembly details, let’s pull that down a little bit, I can see that now I’ve got a Mexico Region scenario for all of my different parts in here.
So, now I’m ready to go off and try to quote this in Mexico with some of our suppliers. So, after getting my quotes back, what I did is I put them into this assembly quotes spreadsheet, and I’ve just created a simple BOM structure with some of the costs that I did get back from my suppliers, material costs, total variable costs, which is a sum of material costs, manufacturing costs, and secondary process costs, SG&A, piece part costs, hard tooling, and then fully burdened costs, which is a sum of the amortized tooling and piece part costs. And so, I’ve gone ahead and loaded this into aPriori using the BOM loader, and what I’m going to do now is create a comparison so that I can look at my aPriori should cost estimate across my supply base. I’m going to go to File, New Cost Comparison, and I’m going to call this Comparison Drill Engine, and then I’m going to call this Mexico Suppliers. Click Okay. So, I’ve got my comparison set up, and now I just need to add my components. So, I’m going to go to here, and I’m going to say Drill Engine, and here’s my Mexico region, and then my suppliers, A, B, C, and D that I imported.
So, now I’ve got my comparison of my Mexico region base against all my different suppliers that I went out and quoted against, and if we look at piece part costs first, I can see that I’m about 5%, 6% lower for these ones here, and this one’s about the lowest at 4 1/2 percent-ish. If I look at my tooling at the bottom here, I can see that this supplier is much higher than me, it’s almost 40% more in the tooling. This supplier is definitely a lot better, about 2%, and then the other ones are much higher, too, at 45% and 65%. And so, if we look at how that plays into the overall cost of the part, if we look at our fully burdened cost, our middle supplier, supplier C, is about a little less than 5% over, while the other ones are at 6% or more. And so, because of that, I’m going to decide to go with supplier C in Mexico. So, now I’ve decided what supplier I’m going to go with, I’m going to go back to my original scenario and close it out. So, I’m going to go to Find, and I’m going to search by assignee, by name, and status on weighting. And I can see I’ve got my supplier scenarios and then my initial scenario that I started with. So, I’m going to go ahead and open that up.
Okay. So, I’ve got a couple things I want to do. I’m going to say in the description, decided to source in Mexico with supplier D. I’m going to go to assignee, and I’m going to just clear it. And then, for status, I’m going to mark it as complete. And I’m going to click cost there so that those get updated. Okay. So, the last thing I’m going to do is just mark the quoted costs on this part. So, I’m going to go to my production info and look at my quoted costs here. My total costs, I’m going to put the piece part cost of $126.32. And my tooling was $77.60. I’m going to click okay. And so, now that will be stored on the part. And from this point, I’m done.
Cost Engineering Reviews the Project Again in Real-Time to Determine Cost of Production
NS: Everything looks like it’s now complete for the project. The whole assembly is over in the complete status. Now, it must be assigned to me actually. So, let me jump back to my dashboard and just take a look. Now, I am here in my top level dashboard that I built out at the beginning of this project. And it looks like everything is just about finished. All of the parts in the drill assembly are in the complete state as far as my scenario status goes. And then taking a look at this heat map again, it looks like pretty much everything that we were seeing in red and orange to indicate those severe manufacturability defects is now pretty much green. Even that manifold that I had to point out to Mark at first. So, this is awesome work. And I’m looking forward to catching up with the team to discuss how they felt the project went.
SS: Thank you, team, for your great work on this project. Now, as we’re coming to a close I just… Welcome, team, we’re getting ready to kick off our next big year. Great work on this project.
The Product Development Team Collaborates Together with aPriori to Improve the Cost Reduction Opportunities on Each Project
So, let me just jump ahead and cover some of the key takeaways from this session. So, Cost Insight Generate’s automated analysis allowed Mark, the design engineer, to continue his design work while aPriori validated the design for manufacturability in the background. When Mark was ready to review the results from aPriori’s analysis, the DFM risk rating helped him prioritize his work so he could focus on parts with the most severe manufacturability risk rating. Cost Insight Design guidance helped Mark understand how to fix the issues that aPriori detected so he could optimize his design before passing it along to Nikita, the cost engineer. If you’re interested in digging deeper into the Cost Insight Generate solution, you may want to check out the recording of yesterday’s 1120 session, Reinventing the Product Design Process. Nikita, the cost engineer, took advantage of aPriori’s shared central database to pick up right where Mark left off. She could search the database to only look at the parts that were marked as ready for her review, and since critical manufacturability issues had been found and flagged to Mark previously, Nikita didn’t have to send the part back for redesign. She was able to refine the cost estimate and send it right along to Barton in Sourcing.
SS: Barton in Sourcing also leveraged the shared central database. He used it to start from Nikita’s finalized estimate. He used matrix costing and targeted reports to identify the optimal region for sourcing. Barton, like the rest of the team, leveraged status and assignee fields to easily convey progress to management. In his case, what was closed versus still in progress. If you’re interested in the sourcing workflow that Barton walked through, check out the recording of yesterday’s 12 o’clock session, How to Quickly Evaluate Multiple Sourcing Options. If you’d like to more specifically dig into the matrix costing that Barton showed, our technology showcase today from 11:45 to 12:45 has a matrix costing boost. Finally, in Project Management, I used dashboards and reports in Cost Insight Report to identify outliers, track progress, and assess profitability. If you’re interested in learning more about building out similar views in Cost Insight Report, there’s also a Reports and Dashboards booth at the technology showcase today from 11:45 to 12:45.