Capital Expenditures: Where Your Industry Stacks Up & How to Offset with Product Cost Reductions
Key Takeaways:
- Industries with the largest capital expenditures are the most capital-intensive.
- Manufacturing insights can offset capital expenditures by reducing product costs.
The Full Article:
Automotive, energy, transportation, and semiconductors are all industries with large capital expenditures. Typically, capital expenses are significant one-time investments such as purchasing manufacturing technology or upgrading a factory to enable new capabilities.
Once you agree to purchase new capital equipment, it’s a fixed cost for your business. And this should not be confused with operating expenses, which are variable expenses and overhead costs to run your operations such as rent, product design and material costs, IT services, and staff wages. For the purposes of this blog, we will focus solely on how manufacturers can reduce operating costs associated with product development to offset capital expenditures.
How Does Your Industry Stack Up for Capital Expenditures?
The U.S. Census Bureau reports that between 2010 and 2019, U.S. businesses (not including farming) increased their total capital structures and equipment expenditures by 70% during the decade, totaling $1.15 trillion.
And industries that are pivoting to address the customer’s needs continue to invest heavily in capital equipment. According to American Automakers, domestic and foreign automakers invested $117.3 billion in their U.S. assembly, engine, and transmission plants, R&D labs, headquarters, administrative offices, and other facilities from 2009 through 2019. Roughly 70% of them were made by Ford, General Motors, and Stellantis. As of January 2022, the U.S. auto industry had capital expenditures of $43.9 billion.
Here is a breakout of structures and equipment capital expenditures by industry between 2010-2019, according to the U.S. Census:
Eliminate Product Cost Challenges, Go Digital
Today’s manufacturers need every possible advantage to keep costs down, improve their operational efficiencies, and offset capital expenditures. Conventional costing methods such as spreadsheets required for new designs and redesigns are time-consuming and vulnerable to human error. What’s more, they are not effective in sharing real-time costing data throughout the entire product development lifecycle.
Businesses lacking digital solutions face additional challenges. For one, data is not integrated with their product lifecycle management (PLM) systems. Without a single source of product design information, teams often work with outdated information or are delayed because they can’t access siloed information. Manufacturing insight software such as aP Pro automates, streamlines, and optimizes the product development process. More importantly, aPriori’s digital thread ties multiple digital twins together and connects product data to a centralized PLM system.
Offset Capital Expenditures with aPriori’s Product Cost Solution
Though you may not be able to eliminate capital expenditures, you can offset them with product cost-saving solutions like aPriori to contain operational expenses. The benefits are plentiful and include the following:
- Reduce costly redesigns. With the right manufacturing insights solution, you can reduce redesigns in the late stages of product development. Late-stage redesigns and engineering change orders (ECOs) result in delays and higher costs. A manufacturing insights solution can identify design issues that can impact product performance, cost, and manufacturability – and improve product value.
- Detect cost outliers. Manufacturing insights like aPriori also can pinpoint cost outliers. Product development teams can then quickly and accurately get product costs in real-time – regardless of the volume. Additionally, sourcing can utilize should cost analysis to ascertain cost outliers for raw materials, components, etc. Sourcing teams can use accurate cost data for effective supplier negotiations. Then the team can determine the most cost-effective design and manufacturing methods – all while ensuring product lifecycle collaboration.
- Collaborate and facilitate faster data sharing. Effective manufacturing insights solutions enable greater collaboration and data sharing, which accelerates product development. With aP Workspace, product teams can produce and share cost estimation reports in a centralized location. This collaboration simplifies how design and sourcing teams can identify where products can be optimized early in product development (e.g., identify alternative materials, revise designs to reduce cost, etc.).
- Automate and accelerate product costing. Cost engineers are responsible for a continuous stream of projects that each include multiple design iterations, and multiple moving parts (i.e., sourcing, production, etc.). A manufacturing insights solution like aPriori automates these functions and streamlines product costing – often for many products at once. It also facilitates faster more efficient new product designs since costing bottlenecks are removed. Now cost engineers can estimate faster and more accurately with real-time data on labor rates, manufacturing processes including energy usage, and more.
To increase the performance of your capital investments, digital factories enable companies to optimize their capital expenditures, configuring the most optimal machines for manufacturability, profitability, and sustainability. Learn how to optimize product design and accurately calculate your manufacturing cost estimation.
For capital-intensive industries such as the automotive or transportation sectors, high capital expenditures will continue. However, they can be offset by lowering overall product costs. A manufacturing insights solution like aPriori is crucial to supporting cost engineering teams in this effort.
Small Steps Add Up to Big Changes
Improving and automating product costs can have a big impact on productivity and, more importantly, the bottom line. By arming product engineering teams with the right tools, small product cost-cutting steps can cumulatively add up to big changes for the bottom line.
This approach is integral to finding the sweet spot between generating profits today and ensuring the necessary capital for tomorrow. As a result, manufacturers can manage their operational expenses more efficiently and accelerate operations to improve profits and support long-term growth.
Improve Profitability and Get to Market Faster
aPriori can show you how to build a costing department.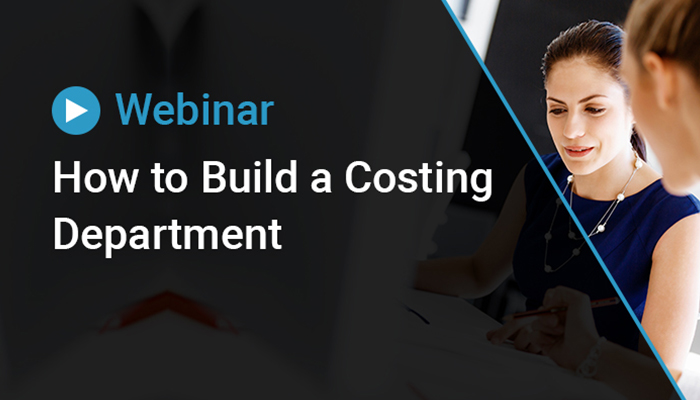