How to Transform Product Cost Engineering for Today’s Future
Product cost engineering has been moving away from traditional costing operations to meet the needs of the cost function today. Outdated tools do not fit the requirements of cost teams looking to speed cost estimates and support time to market plans. To bring cost engineering into the future, teams must have advanced software with the right capabilities to achieve these tasks and more.
Gone are the days of ineffective tools and operating models that have hindered the true potential of cost teams. The future of product cost engineering is now, and functional transformations are required to bring some teams up to speed.
In this post, we will highlight three key factors that cost teams need to address to transform their operations for today’s future. It will also present how manufacturing simulation can reduce the rising pressures of the cost function.
Why It is the Right Time to Embrace the Future of Product Cost Engineering
The future of manufacturing is already here due to the rise of the fourth industrial revolution (Industry 4.0). Since the emergence of Industry 4.0, companies have digitized the way they operate to increase the efficiency of their life cycle teams.
According to McKinsey, more firms are now implementing automated and data-driven technology across all their functions to boost the productivity of their teams by 26 percent. And Deloitte says that 80 percent of companies claim to have digitally transformed their operations to reap the true benefits of Industry 4.0. However, this implies that there are still 20 percent of manufacturing firms that have yet to enhance their functions.
Functional areas such as product cost engineering need automation to reach new levels of efficiency in today’s future. Traditional costing approaches fail to keep pace with the ever-growing needs of modern cost teams. The cost engineer must be able to spread their costing knowledge throughout all stages of product development.
Manufacturing Simulation Software Brings Cost Engineering Into the Future
Prior to the advent of manufacturing simulation, cost teams used traditional spreadsheets to calculate the cost of new or redesigned products. These manual, time-consuming calculations were inefficient and prone to human error. Further, cost teams were responsible for the upkeep of the spreadsheets which was often a labor-intensive endeavor.
Along with spreadsheets, there were companies that either underutilized or kept their product life cycle management (PLM) systems in silos. The data stored in these PLM systems were at times redundant or missing key attributes. This made it difficult for product cost engineering teams to locate relevant product data in a timely manner.
As cost engineering evolved, so did the tools cost specialists employed to perform their tasks efficiently. Industry 4.0 has enabled firms to use manufacturing simulation software such as aP Pro to automate and speed the way their cost teams assess product costs. The powerful software allows today’s future-ready cost teams to:
- Estimate product costs based on real-world manufacturing conditions.
- Assess the cost of thousands of products quickly and accurately.
- Integrate their PLM systems to automatically cost stored 3D CAD files.
Address Three Key Factors to Reach the Next Level of Cost Engineering
Cost teams must address three key factors to ensure their shift from outdated to future-proof operations is successful. At its core, cost teams must use these factors as a guide to meet the needs of the new age of product costing. Below are the three areas that need to be considered and addressed to advance the cost function:
1. Reduce Time to Market (TTM) for New Products
Reduce costly late-stage redesigns that prolong development cycles and launch dates for new products. Manufacturing simulation software gives cost teams the means to quickly find product cost and manufacturability issues early in development. As a result, product cost engineering can guide design teams to create low-cost, high-functioning designs right from the start.
Unlike manual product costing, manufacturing simulation can automatically deliver accurate, timely and real-time cost data for large volumes of products. This level of automation enables cost teams to speed their estimates to help influence a 50 percent reduction in TTM.
2. Enhance Cross-Functional Collaboration With Data Sharing
Give the product cost engineering team access to current and historical cost data through a single automated platform. With this level of data sharing, the team can quickly focus on key cost outliers and enhance how they collaborate with other departments to minimize product costs.
Forward-thinking companies equip their cost teams with manufacturing simulation software, allowing them to generate and maintain cost estimation reports in one location. These detailed reports can be accessed by cost engineers to identify the products the design team needs to optimize for cost first. The software enables cost engineers to exert their influence not only with designers, but also with the entire product team, ensuring that each function is in line with design to cost (DTC) goals.
Digital manufacturing software makes it easy for cost teams to get the data they need without having to spend time looking through disparate, siloed systems. This ensures that cost teams have the insights needed to provide fast cost-reduction feedback early in the product development cycle.
3. Use Simulation to Increase the Bandwidth of Cost Teams
In most companies, the design team outweighs the product cost engineering team’s headcount, making it difficult for cost specialists to keep pace with the flow of new product designs. To alleviate this issue, cost teams need simulation-driven cost models to evaluate the cost of many product designs at once.
Cost teams can use the simulation capabilities of manufacturing software to make faster estimates based on real-world labor rates, manufacturing processes and more. These highly accurate estimates allow cost teams to boost the credibility of their cost projections for all the product designs presented to them.
Conclusion
Industry 4.0 has brought about a paradigm shift in the way cost engineering teams estimate product costs. It is no longer enough just to rely on long-established costing methods and tools to meet the demands of the ever-changing cost function. Instead, product cost engineering teams require the power of manufacturing simulation to make the cost analysis process fast, accurate and fit for today’s future.
Want more insight into design to cost?
Learn about the tools every product team needs to save their companies from cost overruns and engineering change orders.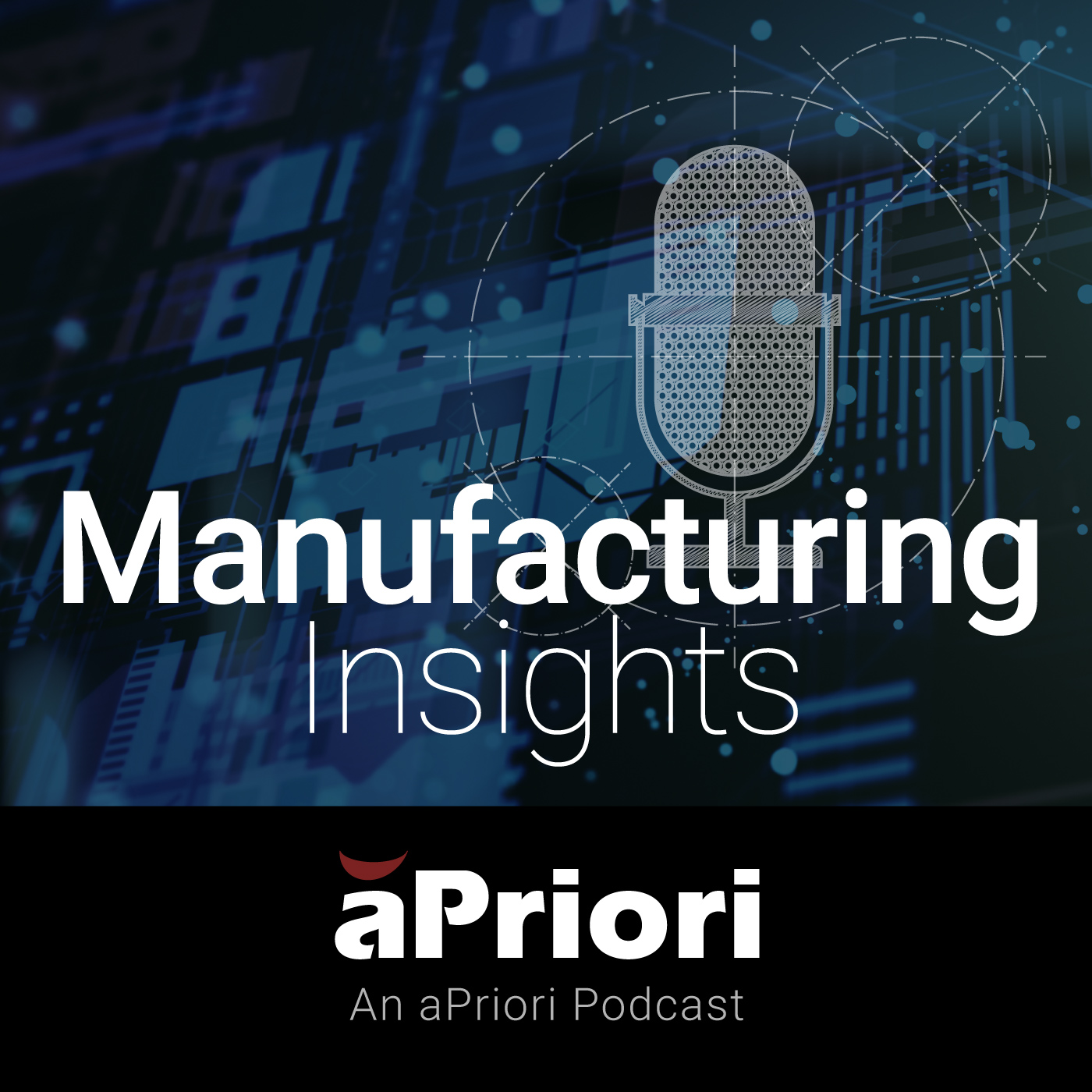