5 Best Practices for a Product Manufacturing Cost Analysis
Key Takeaways:
- Conducting product manufacturing cost analysis can improve profitability, manufacturability, and sustainability
- Implementing these best practices in conjunction with aPriori ensures organizations are mitigating supply chain, inflation, and material and labor shortage challenges as well as optimizing product development
The Full Article:
It’s a perennial quandary. How can manufacturers make cost reductions without sacrificing product quality, competitiveness, and time to market? What are the best strategies for effective product manufacturing cost analysis?
Deloitte’s 2023 Manufacturing Industry Outlook reveals that 90% of surveyed executives agreed that the frequency of supply chain disruptions has increased over the past decade, and the pandemic has exaggerated the impact. Fifty percent of surveyed executives agreed that these disruptions significantly affected their productivity and profits.
With a comprehensive product manufacturing cost analysis, issues such as supply chain disruptions, inflation, labor gaps, and material shortages are mitigated, and costs are lowered. aPriori’s solutions can play a pivotal role in addressing them.
Why Product Manufacturing Cost Analysis is Important
Product manufacturing cost analysis helps organizations identify and optimize raw materials and supply chain savings. A cost insights solution like aPriori empowers supplier negotiations with fact-based analysis. It also allows for faster, better decision-making regarding how to prioritize cost drivers.
It also helps align costs to product strategy or company objectives, such as:
- Cost reduction and increased revenues
- Potential market share/growth
- Product differentiators and capabilities
- Project success probability (to measure risk or complexity)
Additionally, product manufacturing cost analysis enables organizations to forecast the total cost of manufacturing a product, from design to production expenses, including raw materials, labor, and manufacturing overhead. Examples of overhead include energy and manufacturing facility costs. They no longer must rely on laboriously entering numbers into a spreadsheet manually. Instead, they have an automated manufacturing cost analysis in minutes and with much greater accuracy. As a result, manufacturers benefit from:
- Cost outlier identification early in the design stage, reducing cost inefficiencies including time-consuming redesigns and engineering change orders (ECOs), and accelerating time to market.
- Current, highly accurate supplier pricing data with should cost analysis, enabling greater negotiating power. Should cost analysis breaks down cost components (material, labor, overhead, profit margins) to determine a product’s “should” cost so they can better inform and optimize design.
- Pre-emptive insights into the most efficient manufacturing processes and routings, mitigating issues in the production process, meeting target costs, and weighing carbon vs. cost.
However, the way to ensure these benefits is to implement solid product manufacturing cost analysis best practices.
5 Product Manufacturing Cost Analysis Best Practices
Manufacturing cost analysis best practices are only as effective as the tools employed to execute them. The right manufacturing insights solution with real-time cost analysis can provide invaluable support. Consider these five best practices:
- Automate functions with digital twins. Digital twins facilitate greater automation throughout the product development lifecycle. aPriori’s solution integrates seamlessly with an organization’s existing product lifecycle management (PLM) tools to analyze its 3D CAD files automatically. Unlike other solutions, aPriori understands the power of all three digital twins (product, process, factory) to create a digital thread that unlocks highly detailed, accurate cost insights. Manufacturers can make products better, faster, and more sustainable without having to iterate design, wasting time, money, and resources. Thanks to greater automation, issues such as skills shortages and energy usage can be mitigated, saving even more money. Rudimentary, repetitive assembly line tasks can now be automated, freeing up workers to focus on more complex, technical functions. More streamlined product development decreases energy usage in the production phase since insights can provide more efficient ways of manufacturing a product as well as detect potential manufacturability flaws early in the design process.
- Use solutions that provide cost transparency. A solution with cost transparency ensures that all members of product development – from design and sourcing to production – understand the cost implications, particularly as they relate to their role. aPriori provides cost transparency at the most critical stage – design. It accounts for approximately 80% of a product’s cost. Cost insights allow design engineers to modify the product to meet targets upfront. If a particular material or component is driving up costs, designers can explore alternatives that meet the product’s requirements but are more cost-effective. Sourcing can get a better handle on true supplier costs, using fact-based data to improve negotiations. Transparency remediates price issues collaboratively and more effectively. For instance, a design might require an elusive and often, more expensive, material. Sourcing can work with designers, exploring readily available yet affordable alternatives. Supply chain issues also are circumvented, accelerating time to market. Component material types, batch sizes, actual or estimated annual production volumes, etc. can be calculated quickly, resulting in more accurate cost projections.
- Create real-world, what-if scenarios. aPriori’s manufacturing cost modeling software delivers consistently accurate supplier cost estimates that reflect real-world scenarios. In combination with a comprehensive should cost analysis, they can compare supplier pricing projections. Parts offering significant savings opportunities can be identified.
- Work from a centralized reporting dashboard. A solution like aP Analytics fosters greater collaboration across the product development team. It ensures that detailed, accurate data is in one central location, facilitating cohesive cost decision-making. Finally, regardless if it is the design team, sourcing, or the cost engineer, all team members receive data updates in real-time so everyone is on the same page, working from the same information.
- Respond quickly to market changes. A KPMG report cited that 71% of global companies believe raw material costs are their number one supply chain threat for 2023. aPriori Regional Data Libraries are dynamic with global reach. Updated four times per year, manufacturers receive up-to-date material, labor, and machine data from 87 international regions, providing a manufacturing cost analysis advantage.
Benefits of Successful Product Manufacturing Cost Analysis
Reducing material, labor, and other overhead expenses and improving profitability are achievable amid higher material prices, increased labor costs, and supply chain issues. The difference between successful manufacturing cost analysis best practices and those that come up short lies in leveraging the right manufacturing insights solution. Doing so will provide critical, highly detailed feedback to identify and remediate all cost outliers throughout the product development lifecycle.
The payoff? A robust, agile manufacturing business that can take a more proactive stance on the challenges of today. In the process, they will lay the foundation for a more sustainable, profitable, and competitive advantage tomorrow.
Is Your Design In Line With Cost Targets?
See How aPriori Can Identify and Reduce These Costs Early in Design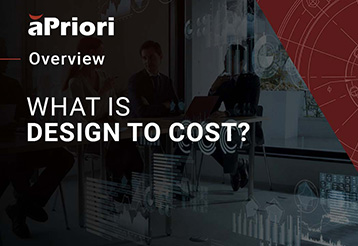