3 Tips for Creating a Powerful Cost-Transparency Culture
Global manufacturers with granular, accessible cost data on hand are better positioned to make cost-effective and profitable product development decisions. They may distribute meaningful and timely cost data across the product team to eliminate silos and foster a cost-transparency culture.
A culture of cost transparency allows each product team function to understand how their design and sourcing decisions affect cost. Further, it encourages collaboration among internal functions and ensures that their activities or efforts are aligned to reach target costs.
This post will explain why cost transparency is crucial to the success, performance and overall profitability of a manufacturing company. We also present three tips for creating and implementing a manufacturing cost-transparency and awareness culture in your organization.
Defining a Cost-Transparency Culture in the Manufacturing Industry
A powerful cost-transparency culture introduces and implements a cost-conscious approach to a manufacturer’s product development process. The culture drives cross-functional product team collaboration in reducing costs at the point of origin and during strategic sourcing activities. For instance, design engineering teams must consider the underlying cost drivers of a product design rather than merely its aesthetics. Sourcing, on the other hand, requires visibility into “should cost” estimations to initiate fact-based supplier negotiations and capitalize on cost-saving opportunities.
Organizations with a cost-first culture understand the importance of product cost management in developing innovative product designs that drive profitability. The culture ensures that internal stakeholders or personnel collaborate and make decisions that positively impact their organization’s bottom line.
Challenges of Developing a Cost-Transparency and Awareness Culture in Manufacturing
When developing a cost-first culture, many organizations face a significant barrier in obtaining cost data that reflects changing market conditions. Manual, time-consuming spreadsheets cannot be relied on to generate and deliver real-time, up-to-date cost estimates to the product development team.
Organizations that lack advanced product design cost estimating, and data generation resources or technologies are unable to:
- Acquire early cost visibility during the product design phase.
- Automate the cost estimation and analysis process.
- Produce error-free, timely, and highly credible product design cost estimates.
- Deliver accurate and data-driven should cost estimates for fact-based supplier negotiations.
- Improve new product time to market (TTM) by getting cost right the first time.
Today’s organizations require a costing process with sophisticated tools that keep up with real-world manufacturing conditions and key cost contributors. That way, internal product development teams can make informed cost-based decisions relative to material selections, regions, production processes and more.
Key Tips for Developing and Implementing a Robust Cost-Transparency Culture
Manufacturing companies must take a strategic approach to managing product design costs and developing a cross-functional culture of cost transparency. Companies can do so by addressing and focusing on three key areas: (1) leadership, (2) organization, and (3) technology investment. In the sections that follow, we offer and present three helpful tips for each of the three areas.
1. Senior Management Must Identify the Missing Pieces
Executives and senior leaders must be accountable for assessing their organizations’ current cost estimation resources and internal, cross-functional processes. Leadership must identify the organizational factors that prolong cost projections and stymie the entire product team’s cost-reduction efforts.
Management, for example, may think about adopting greater digitalization into its internal manufacturing operations, particularly in product cost management. According to a McKinsey study, companies that digitally transform their functions can increase revenues by 23% and productivity by 26%. Investing in digital tools is only one option for management to consider when attempting to implement a new organizational culture.
Leadership must also examine their teams to identify whether critical business units or personnel that influence a cost-first culture are missing. The ideal product team roster should consist of stakeholders with experience managing costs and unifying teams through shared cost data. This can include a dedicated, highly experienced cost engineering department that spearheads all cost modeling and product cost management endeavors.
Once the missing pieces are identified, executives can strategize and create a roadmap that aligns with their cultural transformation goals.
2. Break Down Barriers and Organizational Silos Within the Product Team
The performance and cross-functional collaboration of the product development team is crucial to the success of any manufacturing organization today. Indeed, organizations with high levels of inter-team productivity are more likely to reach their cost-reduction objectives and target costs quickly.
When developing a cost-transparency culture, cost should be at the center of all collaborative efforts across the product development team. For instance, cost engineers strive to produce quick, accurate cost estimates as well as actionable cost-reduction guidance for design and sourcing. This enables all members of the team to collaborate and support one another in their respective product cost optimization responsibilities.
It is also critical to remove any impediments to cross-functional collaboration, such as non-value-added activities and disparate technologies or tools. The goal is to streamline the product development process by breaking down roadblocks and enhancing visibility into important manufacturing data.
3. Replace Archaic Costing Tools With Digital Manufacturing Simulation Software
Traditional costing tools, such as manual spreadsheets, do not account for the present and ever-changing conditions of the manufacturing world. As a result, the product development team is left with outdated and error-prone data that cannot be utilized. Further, product team members cannot waste time seeking access to several spreadsheets and combing through the files for relevant data.
Unlike spreadsheets, digital manufacturing simulation software like aPriori automates product cost analysis and consolidates all cost data in one location. The software leverages the digital twin to produce highly accurate, real-world cost estimates that enables the product development team to:
- Identify and eliminate early cost and manufacturability design issues.
- Achieve cost-saving wins during supplier negotiations.
- Improve collaboration to meet target costs as soon as possible.
- Eliminate the risk of late-stage engineering change orders (ECOs) that slow down TTM.
Organizations that invest in the software have the technological means to eliminate silos and deliver highly transparent cost data internally.
Take the First Step
Building a culture of cost transparency and awareness is not an impossible task for manufacturing companies to achieve. Organizations can take the first step in developing a cost-transparency culture by tackling three critical areas: leadership, organization, and technology. Companies that address each area effectively can benefit from lower costs and higher profitability while boosting cross-functional collaboration.
Get your ROI in 6 Months
But don’t just take our word for it: read Forrester’s impact study.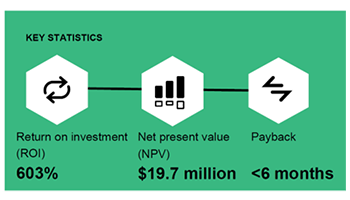