How to Navigate Economic Headwinds with Digital Twin Manufacturing Data
Manufacturers have a lot to account for when developing a successful strategy for today’s turbulent business environment. Get insights to navigate economic headwinds with the use of digitalization with highlights from our recent webinar featuring:
- Adam Robbins, Accenture Principal Director
- Bernard Hensey, aPriori’s Executive Advisory Board Member and former CEO of Boeing Shanghai, VP Fleet Manager, and VP for Commercial Businesses of Boeing Global Services
- Phillippe Adam, aPriori Chief Marketing Officer
Highlights from each presenter follow below.
1) Evaluating Digital Maturity Across Manufacturing Industries
Adam Robbins, Principal Director, Accenture
“Permanent volatility” refers to today’s constant challenges including supply disruption, geopolitical, labor, or shifting customer needs. Companies need to manage these constant changes internally and externally. And that’s where the digital thread comes into play.
There’s a pronounced difference in how manufacturing industries are adopting new capabilities. Many organizations put together a proof of concept as a first step. Then, they move to the piloting phase, but these initiatives aren’t always connected across the different functional areas. So, a company may have each of its five functional areas running independent pilot programs. But understanding the potential value of each pilot can be limited because the project isn’t spanning departments or business processes, and the systems aren’t speaking to each other. This is just one example of the benefits of adopting more of an enterprise-wide mindset.
At Accenture, we surveyed 900 companies to evaluate the status of the digital transformation of manufacturing operations globally. We also evaluated manufacturers on the extent of deploying ~40 key digital capabilities across their operations. The survey covered companies in North America, Europe, and Asia for a good cross-section of what’s happening in the market.
Industries that are in continuous production, such as automotive, are a bit further along in that digitization curve because they recognize that it’s a requirement to survive but also thrive. And industrial manufacturers are also starting to scale their digital capabilities.
Common Manufacturing Digitalization Challenges
Our surveys have shown that many companies do have digital tools, but they may be smaller or homegrown. And the digital tools aren’t being scaled to transform how teams work in a meaningful way.
True value comes from applications that address multiple functions across multiple groups. This could include an enterprise application that enables product development, engineering, manufacturing, and procurement to work together. Bringing departments together as a group can allow them to build, design, and cost products collaboratively. And it enables the group to effectively manage and react and be proactive to the market needs.
2) How Manufacturers Can Navigate Economic Headwinds
Bernard Hensey, aPriori’s Executive Advisory Board Member and former manufacturing executive leader
As we look at the current economic situation and we look at the context of the investments we’ve made within the digital twin and digitizing our operations, the question then is how does that change our approach to a downturn? Traditionally within the industrial manufacturing sector, we’ve looked at making changes with headcount, capacity, and general discretionary expenditure. Given the maturity of the digital twin technology, there are actions we can take to improve our approach to a downturn.
Break the Silos
Traditionally, as industrial companies increased efficiency they also tended to operate within silos. But if you are going to exercise the investments we’ve made within this area, integration across systems and departments is the key issue. And it requires leadership to break down siloed functions and mindsets. Leadership can come from business management, program management, or product management. Manufacturers looking to expand their digital infrastructure need clear leadership identified across the different silos and the different areas we have within a business.
Adopt Digital-driven Procurement
If we are going to use our digital twins to change our financial outcomes for a downturn, the procurement area is going to drive most of the wins. To achieve these wins, here are four focus areas for manufacturers.
First: Understand your procurement categories and make sure you have different actions identified for each category.
Second: Use the digital twin (and digital thread) to support teamwork among design, manufacturing, and the supply chain.
Third: Use data science. In many industrial companies, it’s not part of the culture to use data science for early-stage problem-solving. This requires upskilling and focusing on the people who can within data science.
Fourth: Focus on action. Once you utilize available data, you’ll see manufacturers can apply insights to change financial performance quickly.
Stay Close to Your Customers
As you head into the downturn, the most important thing you can do is to stay close to your customers and understand their requirements as you make strategic decisions. For example, understand your customers’ perspectives as you evaluate value vs. cost decisions. Digitization gives us an opportunity to get closer to our customers and understand how they are being affected by changes in our product or within their own cost environment.
3) Establish an end-to-end Manufacturing Digital Thread
Phillippe Adam, Chief Marketing Officer, Priori
The product is a good starting point for the digital twin, but what about the manufacturing process? What about the way you’re going to manufacture and where you’re going to manufacture? When we talk with manufacturers, they usually have a lot of digital transformation projects in progress. But manufacturers typically aren’t using digital twins to simulate manufacturability. This includes evaluating if a manufacturer should produce a component in-house or outsource it to a supplier, and selecting the best manufacturing process for a specific part.
The digital twin (or digital thread) data can help you reevaluate the way you’re going to build. And it enables manufacturers to evaluate cost vs. carbon footprint, or cost vs. manufacturability because those parameters are linked with each other.
Cost is one design priority and sustainability is another. And the main question that customers ask is the cost or tradeoff of reducing a product’s carbon footprint. All of this data can be linked, which is why manufacturers are increasingly adopting an end-to-end digital twin digital model.
Specifically, industrial manufacturing companies can now implement an end-to-end digital simulation process – from design to production. And they can estimate as many insights as they want for each product, such as cost, manufacturability, and carbon footprint.
Webinar Replay: Navigate Economic Headwinds with Digital Manufacturing Data
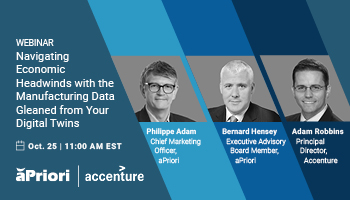