Strategies for Sustainable Product Design & Manufacturing
Business strategies to navigate today’s dynamic economy vary significantly. But there’s a united call for a meaningful reduction of CO₂ equivalent (CO₂e) emissions from institutions that typically don’t see eye to eye. National and global policymakers, regulatory organizations, financial institutions, investors, and c-level executives share an unprecedented commitment to track and reduce their environmental impact.
But shifting from sustainability intent to implementation is complex. And many manufacturers are struggling to understand where to start and how to implement changes to satisfy regulators and customers. To address sustainability challenges, we’ve highlighted business drivers and outlined a framework to establish product benchmarks, evaluate trade-offs, and measure results:
- What is sustainable product design?
- Why poor visibility hinders manufacturing sustainability
- How to incorporate sustainability into product design & production
- Take actionable steps toward sustainable product development
Watch how aPriori Empowers Manufacturers to Reduce their CO2e.
1. What is Sustainable Product Design?
Sustainable product design considers the environmental, social, and economic impact of product development – from the initial concept phase through production and end of life*. To achieve sustainable design, manufacturers are expanding their traditional product development criteria to also address how to reduce resource consumption and increase material reuse/recycling. Primary sustainability design considerations are:
- The product design (digital twin): This includes specifications for weight, energy consumption, emissions, efficiency, expected product life, etc.
- Sourcing: Identify and procure materials that have a low CO2 footprint, are recyclable, etc.
- The manufacturing process: Evaluate production based on energy consumption, material waste, emissions, etc.
- Shipping and logistics: Compare shipping costs from factories in different regions and compare delivery methods.
What is the Circular Economy?
Sustainable manufacturing underpins a broader circular economy initiative to increase recycling, eliminate waste, and use natural resources safely. In our traditional linear economy, materials are extracted, processed, used, and become waste at the end of their life. And companies create value by producing and selling as many products as possible.
By contrast, the circular economy model:
- Maximizes the value of materials, products, and other resources (e.g., water and energy)
- Minimizes material consumption – especially virgin materials, hazardous substances, and the generation of waste
The Ellen MacArthur Foundation notes that a circular economy “seeks to rebuild capital, whether this is financial, manufactured, human, social or natural. This ensures enhanced flows of goods and services.”
Support for the circular economy can provide up to $4.5 trillion in economic benefits by 2030, according to the World Economic Forum. The electronics industry, for example, could develop new capabilities for material recovery and e-waste management.
How Do You Measure Manufacturing Sustainability and Emissions?
Product design and manufacturing are the linchpins of successful sustainability efforts. Companies determine more than 80% of a product’s environmental impact during the design phase, according to the EU Science Hub. Similarly, up to 80% of product cost is also defined during this early phase.
The Greenhouse Gas Protocol is a leading method for companies to measure their carbon footprint. The company provides three levels/scopes of CO₂ measurement for manufacturers:
- Scope 1 addresses direct emissions from owned or controlled sources.
- Scope 2 includes indirect emissions from purchased energy generated, along with the emissions tracked in Scope 1.
- Scope 3 – the Corporate Value Chain Standard – includes all upstream and downstream emissions along with emissions tracked in Scope 1 and 2.
See how aPriori addresses product sustainability across Scope 1-3.
2. Why Poor Visibility Hinders Manufacturing Sustainability
Consulting firm McKinsey found that the majority of product managers surveyed don’t have the tools or framework to define a sustainable product. And none of McKinsey’s survey participants are using Scope 3 standards to monitor carbon output. This is a critical gap because Scope 3 includes all indirect emissions throughout the reporting company’s value chain.
IBM’s 2022 sustainability survey of 3,000 c-level executives revealed similar challenges. Forty-four percent of respondents said that they lack sustainability data to take meaningful action. And only 23% of executives are implementing sustainability strategies across their entire organization.
3. How to Incorporate Sustainability into Product Design & Production
Manufacturing brands are acutely aware of their customers’ unyielding demands for new features, dependability, fast service, and delivery – all at a compelling price. Now companies need to add sustainability to core new product development requirements without ceding significant value in other areas.
Design-to-value (DTV) is a popular methodology to determine a product’s competitive advantage beyond just price. Successful DTV initiatives incorporate market research (e.g., identify unmet market needs and customer insights) and capitalize on new engineering and manufacturing technologies. Suppliers are central to this process, and their importance will continue to increase as manufacturers incorporate sustainability measures.
Steps that manufacturers are taking to measure and manage their sustainability efforts include:
Establish a Carbon Emissions Baseline: You can’t manage what you can’t measure. Adopt visibility for Scope 3 emissions to eliminate sustainability blind spots and measure carbon emissions throughout the supply chain. Manufacturers typically use product life cycle assessment (LCA) software to collect sustainability information once a design is complete. But this manual process is cumbersome, and sustainability information isn’t integrated into other systems.
Additionally, some manufacturing brands may need to secure carbon emission data from their suppliers and their suppliers’ suppliers, and take other steps to gain full visibility regarding supply chain sustainability.
Evaluate Cost vs. Sustainability vs. DFM Tradeoffs: Once there is a baseline for a product’s current carbon footprint, manufacturers can work to reduce CO2 emissions and meet their other product requirements simultaneously. Teams can analyze tradeoffs among cost, sustainability, and design for manufacturing (DFM), and make decisions accordingly. Manufacturing simulation scenarios include:
- Using alternative materials to reduce CO2 emissions, weight, etc.
- Selecting an alternative manufacturing process to save electricity, reduce scrap, etc.
- Updating CAD designs to cut manufacturing times, incorporate alternative materials, etc.
Evaluate Nearshoring and Onshoring: In addition to assessing reshoring strategies to mitigate supply chain disruption, manufacturers are also weighing the impact of sustainability in their decisions. A U.S. manufacturing brand that moves production from China to Mexico, for example, could reduce transportation emissions to America. And there could be more viable transportation options to further reduce emissions (e.g., road, maritime, rail, and air).
Use Suppliers for a Strategic Advantage: Effective manufacturing brands are using suppliers’ expertise throughout the new product development process and ensuring access to critical materials and components. And this level of collaboration is essential for manufacturers to capitalize on new sustainability-related advances. Businesses that adopt strategic supplier relationships can outperform their industry competitors by nearly 2X, according to McKinsey.
Drive Real-time Communications: Collaboration among design engineers, cost engineers, sourcing, and suppliers is critical to meet cost, carbon, and other targets for new product development (NPD) and value engineering projects. Manufacturers that enable teams to access current product design and project specification information can work faster, more effectively, and with a greater degree of confidence than teams working in siloes.
Implement Digitalization Capabilities: Streamline and centralize product design and manufacturing information. Digitalization initiatives can integrate previously siloed data and enable teams to make decisions quickly using the latest product, sustainability, sourcing, and manufacturing information. Digital transformation capabilities – including the digital twin, digital thread, and digital factory – can integrate seamlessly with digital enterprise solutions and business processes.
4. Take Actionable Steps Toward Sustainable Product Development
Companies that use the digital thread and other digital transformation (DX) capabilities to simulate changes to product design, bill of materials, and manufacturing processes are well-positioned to incorporate sustainability insights into their analysis.
With a unified view of the product development and manufacturing process, businesses can understand a product’s CO2 impact during early design phases, and then evaluate opportunities to reduce a product’s carbon footprint. Importantly, teams can simulate design alternatives using different materials and manufacturing processes to meet CO2 emissions, cost, and performance targets. Learn how to evaluate cost, carbon, and manufacturability trade-offs with aPriori.
Select companies are gaining these insights by integrating sustainability, design, sourcing, and manufacturing data. One multinational commercial vehicle manufacturer worked with aPriori to extend its digital factory capabilities to include sustainability insights. And we are using this proven solution as a framework to commercialize this capability.
*We adapted the sustainable product design definition from Disrupt Design.
Get aPriori's Exclusive Guide to Reducing Product Emissions
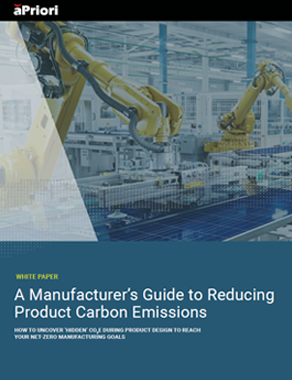