Digital Twins: A Powerhouse to Transform Business
Key Takeaways:
- Today’s digital twins are interconnected throughout the product development lifecycle
- aPriori digital twins improve carbon emissions, profitability, and visibility
The Full Article:
How can manufacturers accelerate product development, improve collaboration and decision-making, meet sustainability initiatives, and remain profitable? The answer, according to an increasing number of manufacturers, is digital twin capabilities. aPriori covers this evolving technology from multiple vantage points – from core definition to practical applications and manufacturing digital twin examples.
- The New Digital Twin Definition
- Advantages of Multiple Digital Twins
- aPriori Digital Twin Capabilities
- How aPriori Digital Twins Power Product Manufacturing
- Case Studies: Digital Twins in Action
The New Digital Twin Definition
As next-generation digital transformation capabilities evolve, the definition of a digital twin is expanding beyond “a single virtual representation of a physical product.” Today, it encompasses multiple interconnected digital twins that can provide powerful product insights instantly.
Multiple digital twins are required to optimize a single product across various dimensions – including manufacturability, sustainability, and cost. And companies need to use multiple digital twins because product engineering is too complex for a single model (digital twin), according to the July 2022 Journal of Manufacturing Systems.
Companies are increasingly using model-based design to accelerate product development and reduce risk by simulating the behavior of a product. It requires multiple digital twins (e.g., one for finite element analysis [FEA], a second to optimize the manufacturing process for cost and performance, etc.).
With the growing call for more sustainable products, manufacturers require a “sustainable digital twin” capability from “cradle-to-gate” (nurturing a design concept from its infancy or the “cradle” through production or the “factory gate”).
Delve deeper into how digital factories improve manufacturability, cost, and sustainability.
Advantages of Multiple Digital Twins
There is a symbiotic nature between manufacturability, cost, and sustainability. Therefore, it makes sense for manufacturers to use multiple, connected digital twins to gain product insights for each product goal (e.g., cost/profitability) and holistically address them.
An estimated 80% of a product’s early design determines its environmental impact. It highlights the importance of gaining early feedback on a design’s potential carbon footprint. Changes in design, material selection, manufacturing process, and factory location can impact product sustainability – as well as cost and manufacturability.
For instance, when evaluating cost, a supplier in India may be less expensive than one in the U.S. However, the lower cost could expose a longer supply chain route, leading to higher fuel usage. These examples highlight the product development lifecycle’s interconnectivity.
Product development teams conduct “what if” scenarios and analyses to evaluate the impact of design changes on key product goals for cost, carbon, and manufacturing process and location. It enables them to make informed decisions quickly and accurately. Companies use insights from multiple digital twins to unlock actionable, real-time data for better decision-making.
aPriori Digital Twin Capabilities
Today’s complex business environment requires digital twin technology. It provides a framework to address challenges and new requirements as well as incorporate new applications. Connected digital twins can enable robust features throughout the product development lifecycle including:
- Simulation: Speed and agility are essential in today’s business environment. Rapid simulation is central to determining if a product is manufacturable and cost-effective. It also is essential in understanding the carbon impact as well as exploring alternative, sustainable materials. Simulation can answer other product design questions, necessary to make effective decisions. aPriori provides product design simulation for cost, manufacturability, and carbon footprint. Other simulation software addresses structural analysis (FEA), fluids, and electromagnetics. Typically, simulation does not extend to the manufacturing process or factory location (or specific capabilities). To address this market gap, aPriori enables companies to simulate a variety of manufacturing processes as well as specific factories and/or manufacturing locations. By extending simulation capabilities throughout the product development lifecycle, manufacturers have the visibility to ensure manufacturability, capture additional savings, reduce carbon emissions, and address supply chain risks proactively.
- Integration (digital thread): The digital thread ties multiple digital twins together and connects product data to a centralized product lifecycle management (PLM) system. The digital thread enables a “single source of truth” for product specification and bill of materials (BOM) data. Digitalization also connects PLM data to enterprise resource planning (ERP) and other systems. It can also extend business processes across traditionally distinct operations (e.g., product design and sourcing).
- Automation: Improve employee productivity and accuracy by automating key tasks. With aPriori, manufacturers gain automated design guidance for each product design change. Additionally, automated reports that pinpoint specific design issues are available to review and remediate. Teams can also configure automated workflows and set alerts to appear only when individuals are assigned tasks. Management and product teams can access automated reporting of key performance indicators (KPIs) to see progression of cost, carbon, and manufacturability goals.
- Collaboration: Centralizing product data across departments has limited value if the relevant teams are siloed. A digital thread ensures that all teams in the product development lifecycle can analyze data and collaborate more efficiently. A coworking space to assign and manage tasks and provide traceability ensures better communication and seamless collaboration. It is especially important as teams grow (e.g., product design, cost engineering, sourcing, sustainability, and manufacturing).
However, features are only as good as the benefits that they provide. While each digital twin has its merits, together via the digital thread, they are a powerhouse that can transform business.
How aPriori Digital Twins Power Product Manufacturing
The whole is greater than the sum of its parts. aPriori’s digital twins connect across the product development life cycle to gain a holistic view of product manufacturability, cost, and sustainability:
aPriori Digital Product Twins refer to 3D CAD models or virtual representations of physical products that include components and assemblies, along with overall product size and shape. It serves as the design optimized via simulation and additional modifications. It becomes the framework to analyze the current product design, using simulation to see how design changes will affect sustainability, cost, and manufacturability. Discover how Carrier saved millions with aPriori’s digital product twin.
aPriori Digital Process Twins determine the most effective way to manufacture a product by simulating manufacturing processes and routings (e.g., injection molding and additive manufacturing). Our physics-based manufacturing process models allow engineering, manufacturing, and purchasing professionals to explore production alternatives down to the machine level. Companies simulate manufacturing processes using the digital twin to identify the most appropriate production process for cost, sustainability, and manufacturability. Learn how AGCO used aPriori’s digital process twin to gain manufacturability and cost insights in just a few clicks.
aPriori Digital Factory Twins represent physical factories. This virtual model includes precise factory-specific production capabilities along with detailed costs – including labor, electricity, materials, and overhead rates in 87 regions globally. Manufacturers use digital factory twins to help evaluate their supply chain CO2e across the value chain (Scope 3) by creating a virtual representation of supplier factories and their own manufacturing locations. Get a glimpse into how AGCO built an internal digital factory, covering processes and routings, configurations, and production.
It is important to remember that the most optimal results come from utilizing all three twins. Each serves an essential role, and collectively, enhances manufacturability, cost, and sustainability across the product development lifecycle.
Case Studies: Digital Twins in Action
Not only do digital twins address current disruptions and issues, but they build in higher value, greater profitability, sustainable practices, faster time to market, and more agility to pivot while remaining competitive. Here’s how:
- Mitigate inflation and margin pressures: Streamline cost analysis processes via simulation-driven cost estimates, cost transparency, and real-time reports. Listen to Soucy explain how aPriori helped them get rid of the Excel spreadsheet, run a rapid cost analysis, improve collaboration with engineers, and negotiate better with suppliers.
- Address labor shortages and skills gaps: Break down silos, collaborate more efficiently and cost-effectively, and do more with fewer resources. Hear how Woodward used the digital factory to improve their supply chain and address labor challenges via the digital factory.
- Streamline supply chain and quoting: Reduce quoting timelines. Ensure OEMs and suppliers have accurate product cost information. Walk through how a digital factory can build a better supplier relationship.
- Eliminate late-stage redesigns: Accelerate new product development and value engineering. Find out how Eaton cut product development times from months to hours with aPriori.
- Reduce material waste, high energy use, and carbon: See how a digital process twin like aPriori’s takes the guesswork out of the carbon footprint. Dig deeper into how aPriori supported Grundfos’ sustainable sourcing efforts.
The Digital Twins Yield Exceptional Returns
By connecting the three twins, manufacturers can simulate how real-world production processes and global factory conditions affect a product’s cost, CO2e, and manufacturability. The right manufacturing simulation software maximizes manufacturers’ DFM strategies and enables them to break down organizational silos and save time.
McKinsey confirmed that successful digital transformations yield exceptional returns. Across many manufacturing sectors, it is common to see 10 to 30% increases in throughput, 15 to 30% improvement in labor productivity, and 85% increase in more accurate forecasting.
Navigate Economic Headwinds with Digital Twins
Optimize digital twin data to improve profitability.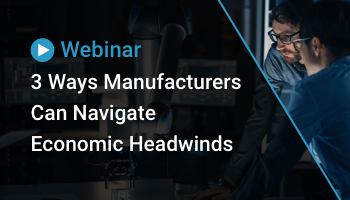