Kearney Insights: How to Build a Modern Costing Department
The recent aPriori and Kearney co-hosted webinar provided insight into new challenges and shifting conditions faced by a costing department. Attendees learned how to build a costing department that could facilitate procurement negotiations and accelerate the launch of new products. The webinar offered best practices to create a successful cost team even when considering macro-level disruptions.
This post presents key insights and takeaways from the webinar “How to Build a Costing Department That Meets Today’s Manufacturing Demands.” We also discuss the role of cost engineers during times of inflation and supply chain disruption.
What is a Costing Department?
A costing department consists of cost specialists who assess, control, and reduce the cost of new product designs. They employ a cost-first approach across the product life cycle to ensure that products are optimized for cost and manufacturability. At its core, the cost function is responsible for:
- Meeting target costs. Manufacturing costing teams must assess multiple alternative designs, materials, and production processes to ensure that cost targets are reached.
- Reducing engineering change orders (ECOs). Manufacturing costing teams may use manufacturing simulation software to evaluate products and identify issues early in the design stage. Cost teams that spot design issues early can lower the risk of late-stage, expensive ECOs.
- Accelerating time to market (TTM). Manufacturing costing teams can ensure that product launch dates are not delayed or missed by eliminating ECOs. They collaborate with the design team to ensure the right product is delivered on time and at the right cost.
- Should-Cost Analysis. Manufacturing costing teams can find discrepancies between the current cost of components and a projected should-cost produced by manufacturing software. The sourcing team can use these should-costs to begin fact-based negotiations with strategic suppliers and achieve savings on components.
The classic costing department assists the entire product team by delivering product cost transparency and identifying direct savings opportunities. While cost teams need to perform these conventional tasks, they must also be modernized to achieve success in today’s environment.
Three Ways to Design a Modern Cost Team
The aPriori and Kearney webinar revealed three critical insights that firms must understand when designing and organizing their costing departments. The three insights are as follows:
Insight #1: Changing Environments and New Challenges
Dominik Leisinger, a manufacturing costing expert from Kearney and webinar guest speaker, identified seven macrotrends to keep an eye on. Leisinger believes these trends will stay relevant for the next 10–20 years and will impact the way manufacturing firms work. The seven key macrotrends include:
1. Digital Ecosystem
Digital business models will continue to drive organizational growth, efficiency and productivity across industries such as manufacturing.
2. Caring for the Planet
Manufacturers must prioritize and adopt “green” business practices. The importance of environmental sustainability is becoming more widely recognized by modern organizations. Alternative natural resources must be considered by businesses if they want to protect the health of the planet.
3. Resource Impacts
More businesses are using a reskilling strategy to train employees for new job roles due to a shortage of talent.
4. Nationalism and Social Constructs
Rising nationalism and social unrest are affecting international trade relations, such as those between the U.S. and China.
5. Consumer Expectation Shifts
Businesses are now held to a higher standard of accountability by the public. Consumers will only buy from companies that deliver on their promise, purpose, and product quality. They also leverage environmental, social and governance (ESG) reports to assess how honest firms are with their green activities.
6. Competing for Talent
Many companies struggle to replace their highly qualified and experienced workforce. Talent is scarce and has a significant impact on how companies will do business going forward.
7. Global Disruptions
The COVID-19 outbreak and the crisis in Ukraine remain two notable disruptions that have impacted manufacturing. These events have disrupted Asian supply chains and increased the demand for materials or commodities, albeit at higher prices. These disruptions also continue to influence and promote today’s high inflationary market.
According to Leisinger, most businesses face at least one of the seven key challenges in their own workforce. When assembling cost teams, businesses must ensure that cost engineers understand how these challenges may affect and influence cost decisions.
For instance, cost engineers must consider CO2 variables and incorporate them into their product optimization process. They can weigh the trade-offs between sustainability and design to cost (DTC) and collaborate with designers to strike a balance between both areas.
Insight #2: Supply Chain Disruptions and What It Means for Cost Teams
There are several external variables that have raised the price of commodities and challenged the current supply chain environment. Commodity price increases can be attributed to factors such as the COVID shutdown, supply chain congestion and the Texas freeze.
Cost engineers must focus on multi-sourcing and changing the nature of demand to mitigate the impact of commodity price increases. First, they can assist firms with multi-sourcing to control supply and cost risks better than in a single-sourcing strategy. Second, cost teams can alter the nature of their demand by being flexible and quickly changing the specification of materials. This allows their colleagues in procurement to exchange specific components for similar and more readily available alternatives.
Manufacturing costing teams must prioritize the three areas below to assist the entire product team in combating supply chain disruptions:
- Providing cost transparency. When considering material alternatives, cost engineers must provide timely cost insights and share them with the product development team. That way, cost engineers can provide actionable design guidance to the product team based on high levels of cost transparency.
- Scenario building. Cost engineers can run scenarios using manufacturing simulation software to calculate the costs of different product designs and supply chains.
- Automate to respond quickly to market changes. Cost teams can reduce their manual efforts and save time when calculating product costs by using automated and simulation-driven software. A costing department can use the software to provide accurate cost projections based on changing and real-world manufacturing conditions.
Leisinger states that the three aforementioned areas work together to improve cross-team collaboration to solve supply chain issues. This means better coordination among key stakeholders in engineering, procurement, and manufacturing to manage the issue of rising commodity costs.
Insight #3: Raw Materials and Inflation
Since the start of the COVID-19 pandemic, prices on major commodity markets have risen to a record high. The Ukrainian crisis alone is expected to raise metal prices by 16 percent this year before stabilizing in 2023.
As commodity prices rise, Leisinger recommends that costing departments work with other product team areas to manage the economic issue. The costing department can provide product teams with insights into three key pillars, including:
- Risk assessment. Determine the level of risk exposure on raw materials and commodities. It is also crucial to determine the value of each part and how halting its delivery might affect company revenue.
- Cost analysis. Examine the entire cost structure of key components and the impact of price increases on that cost structure. Cost engineers must also assess the current state of suppliers who may go bankrupt due to a higher risk exposure.
- Market analysis. Identify the gap between pre-COVID material prices and the supplier’s current commodity prices. Cost analysts can use manufacturing simulation to generate should-cost estimates for sourcing to use during fact-based supplier negotiations. The objective is to leverage factual cost estimates to only to pay for what is fair.
Conclusion
The aPriori and Kearney co-hosted webinar offered invaluable information to build a highly effective and modern costing department. Businesses can ensure that their cost teams are prepared for rising challenges and changing environments by considering these key insights.
HOW TO BUILD A MODERN COSTING DEPARTMENT
See how to organize and develop a costing team to get products to market faster and with greater profits.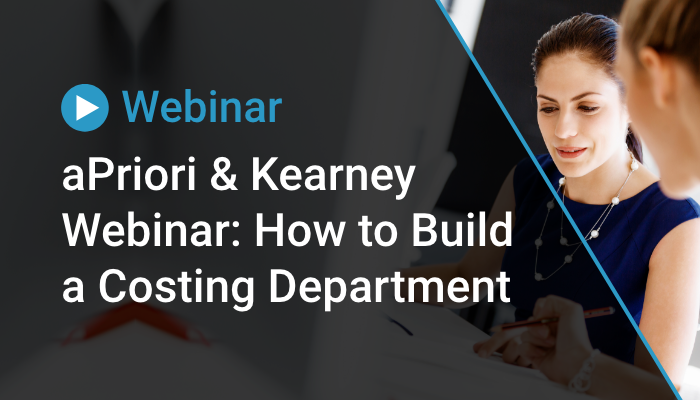