Resources
aPriori
Customer Success
aPriori solutions transform your business with digital insights that optimize manufacturability, profitability, and sustainability.
Forrester’s interview of four aPriori customers quantifies our 603% ROI. Hear why our customers – ranging from aerospace and automotive sectors to industrial and high-tech electronics – rely on aPriori.
20 Years
of better manufacturability & improved costs
$76M+
supplier negotiation savings for customers
87%
reduction in new product design time
>$100M
expected 5-year savings with aPriori insights
Filter by
Explore our case studies
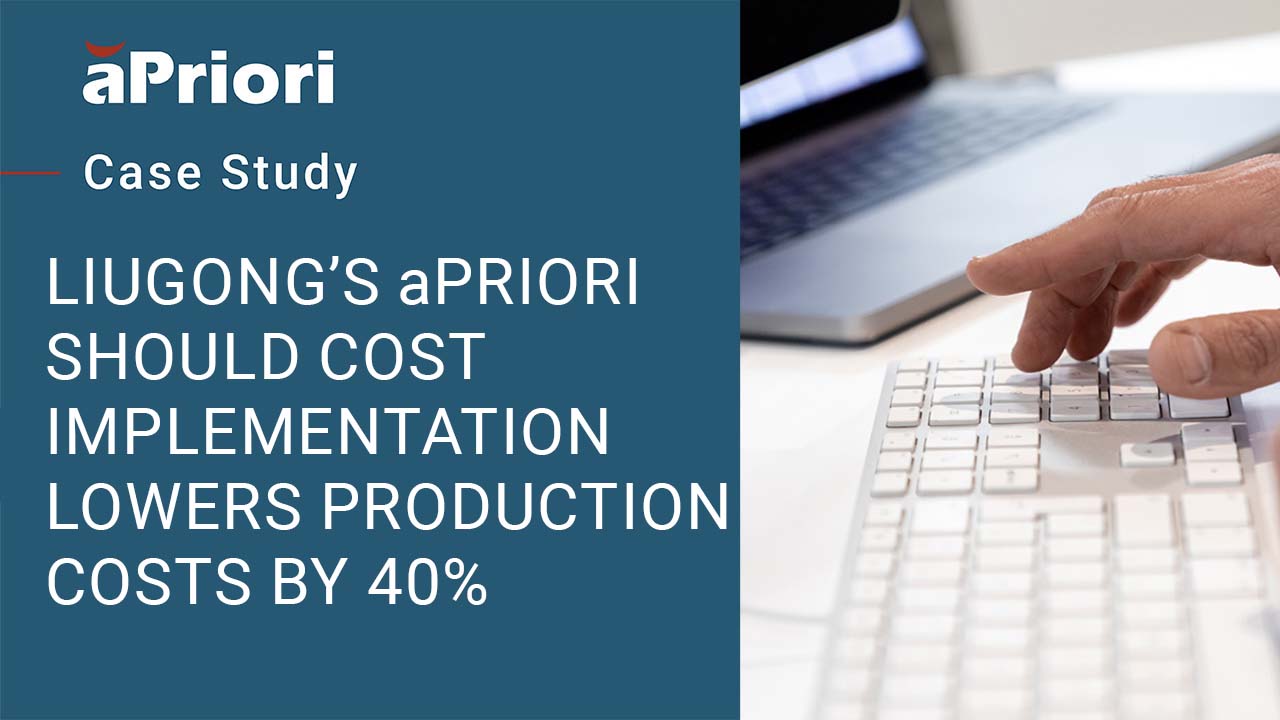
LiuGong’s aPriori Should Cost Implementation Lowers Production Costs by 40 Percent
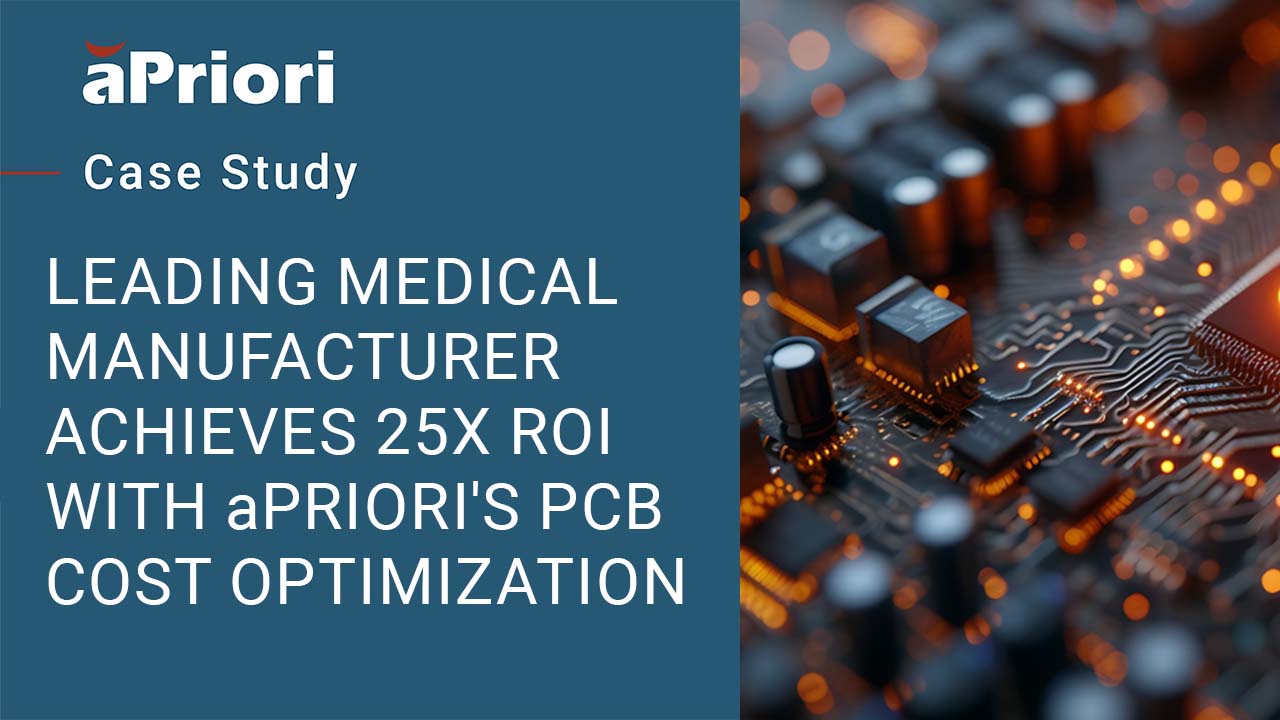
Leading Medical Manufacturer Achieves 25x ROI with aPriori’s PCB Cost Optimization
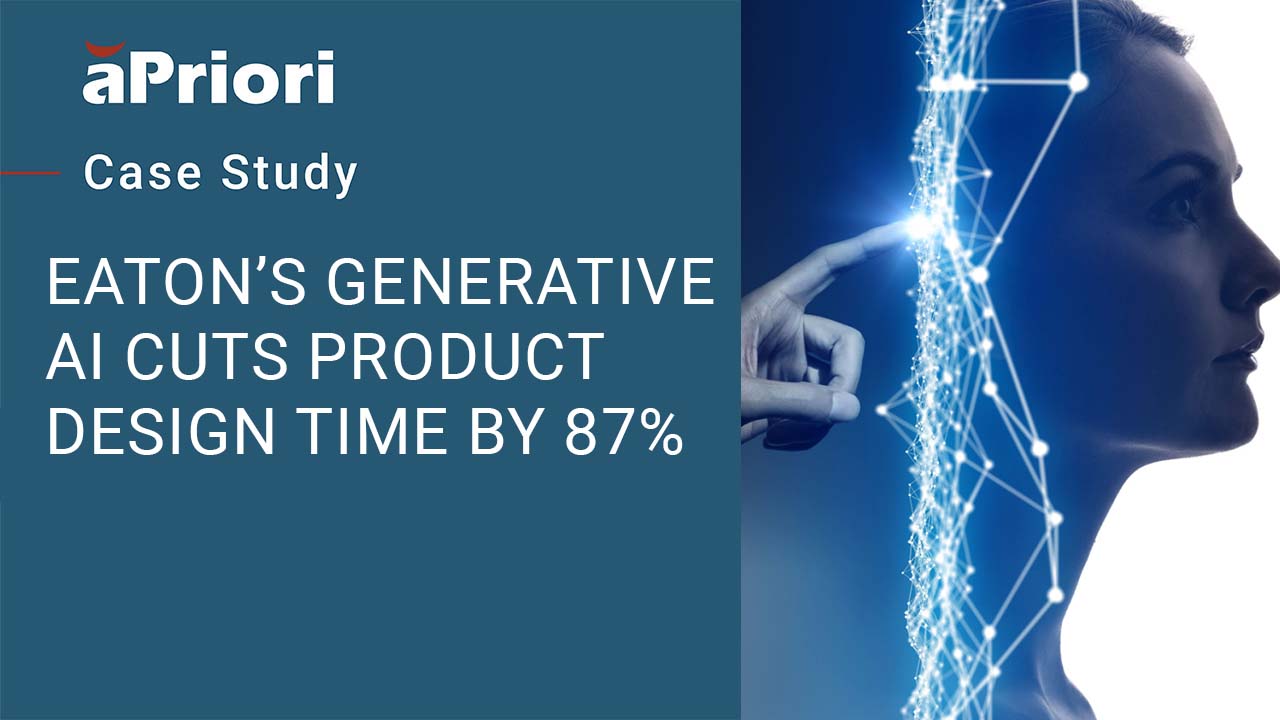
Eaton’s Generative AI Cuts Product Design Time by 87 Percent
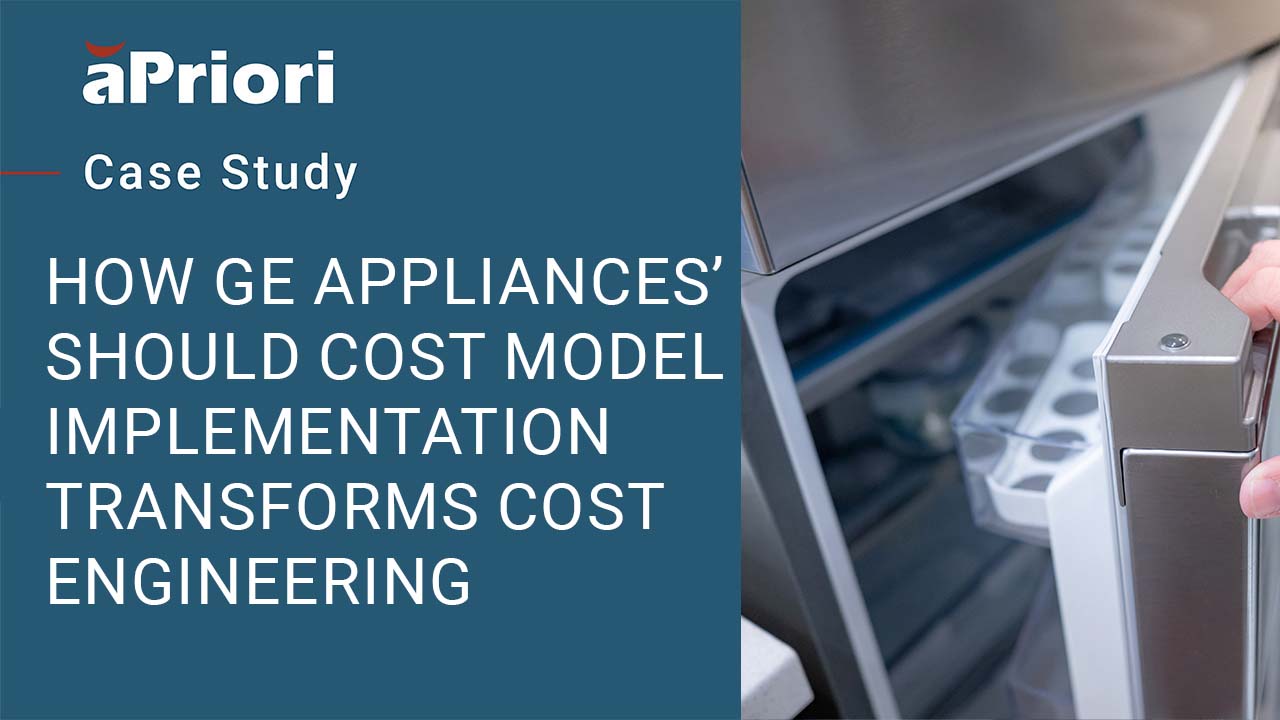
How GE Appliances’ Should Cost Model Implementation Transforms Cost Engineering
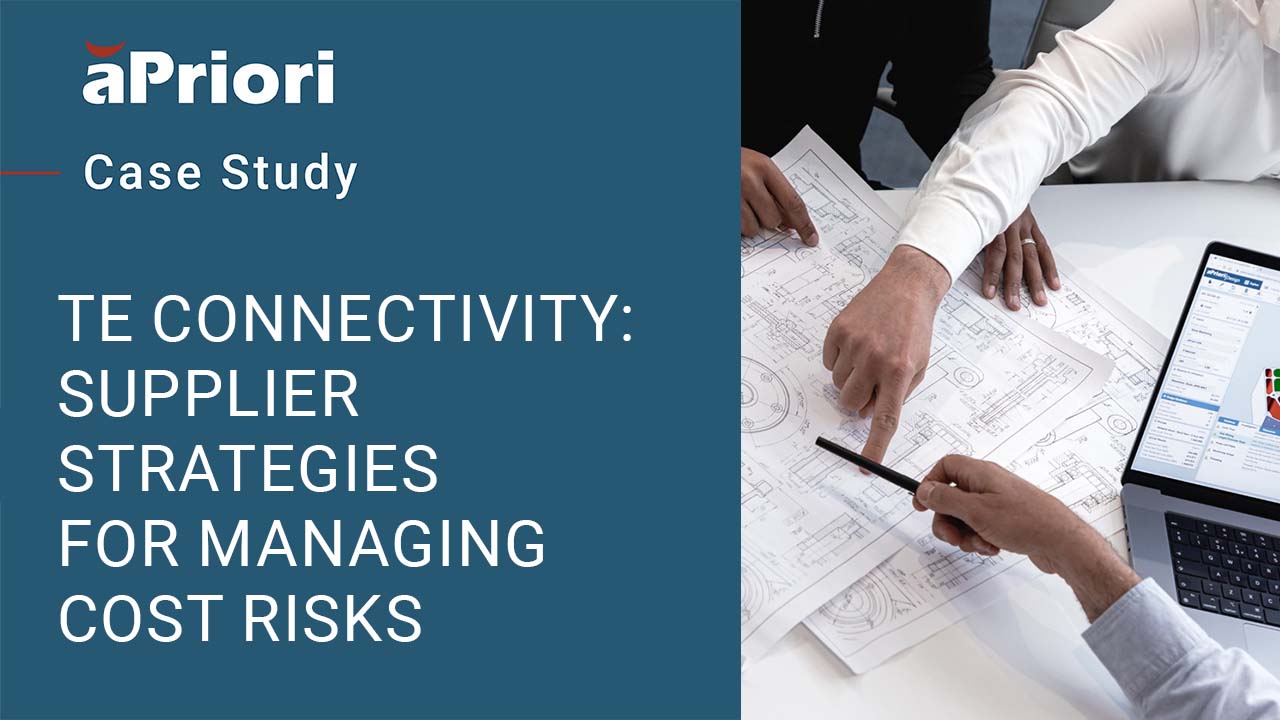
TE Connectivity: Supplier Strategies for Mitigating Risks and Fostering Collaboration
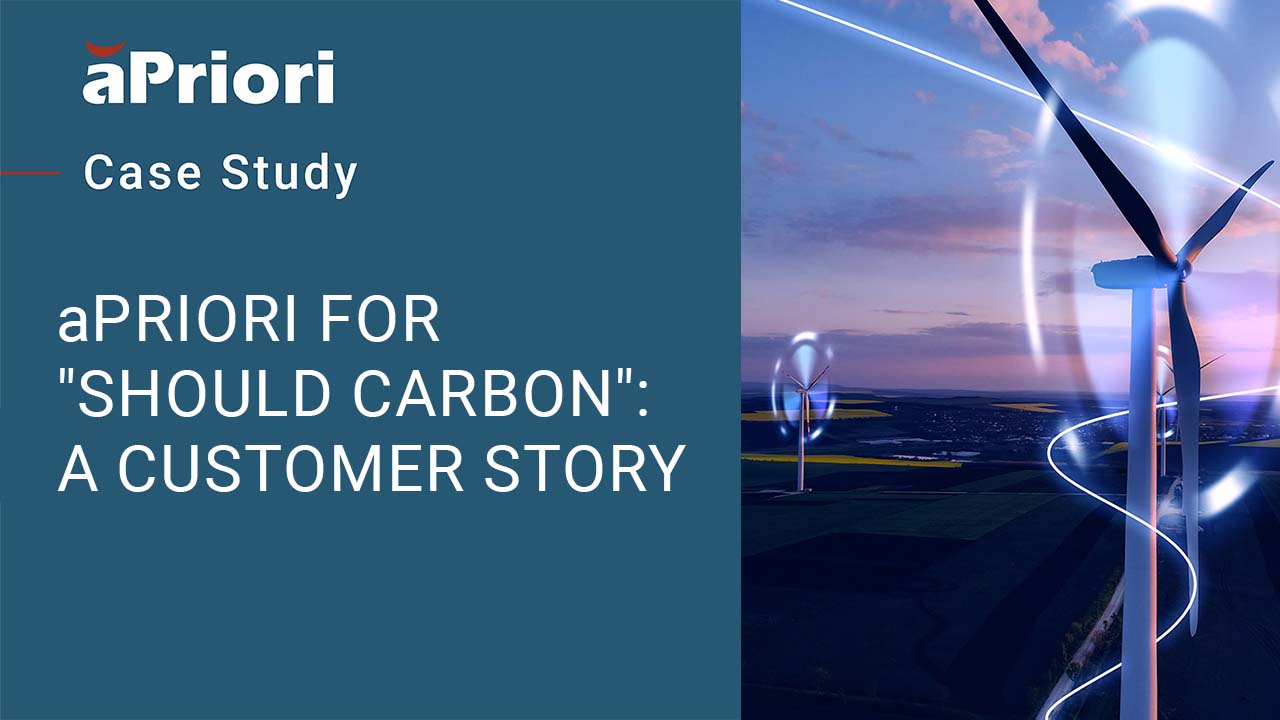
aPriori for Should Carbon: Fuel Cell Energy
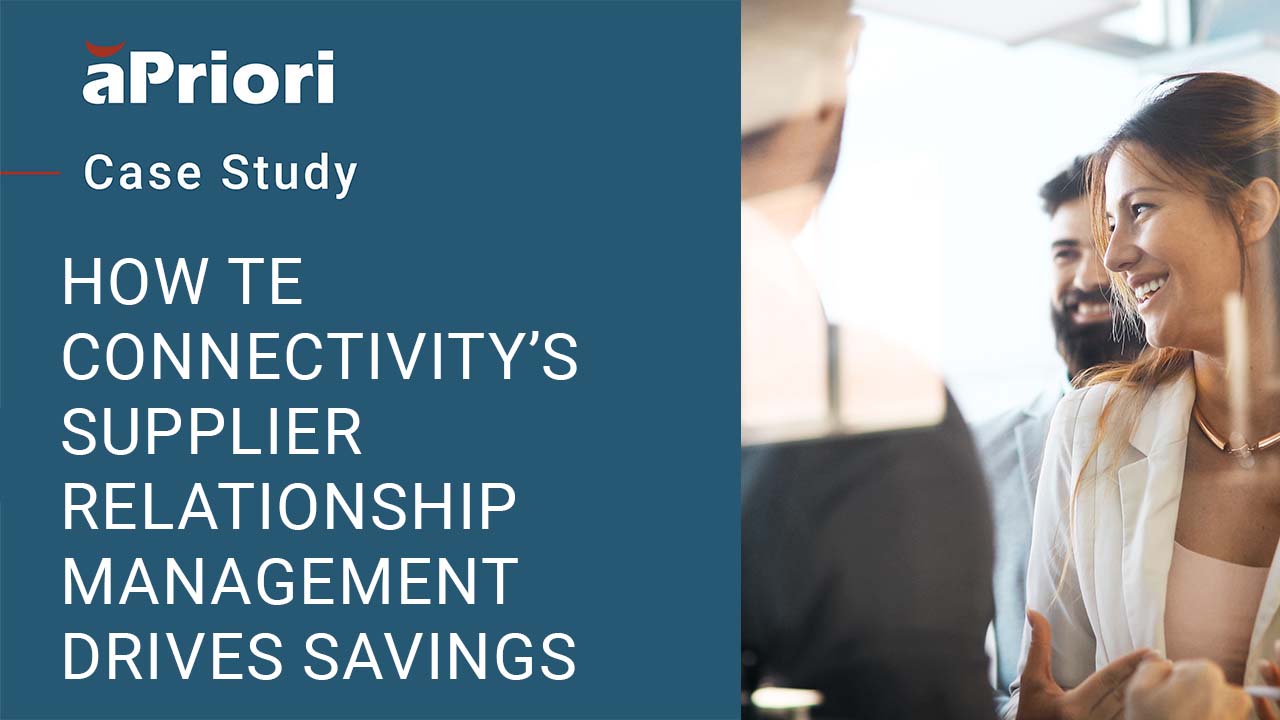
How TE Connectivity’s Supplier Relationship Management Drives Savings
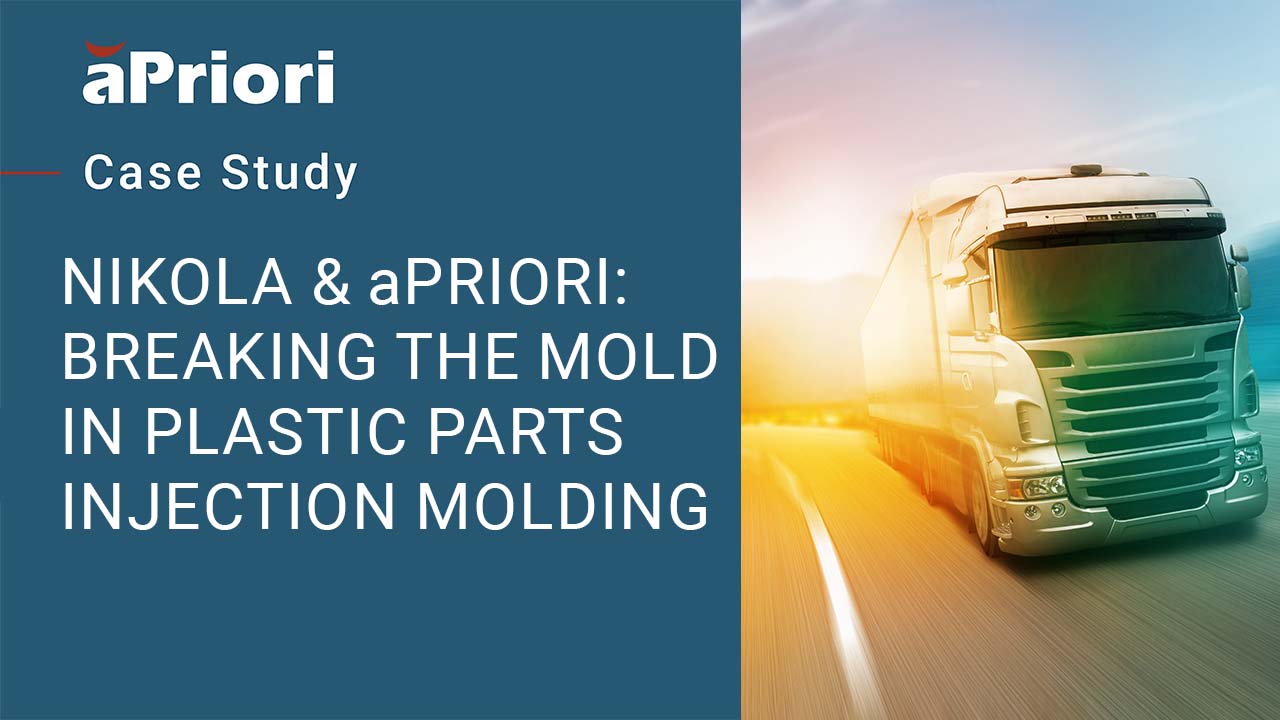
Nikola & aPriori: Breaking the Mold in Plastic Parts Injection Molding
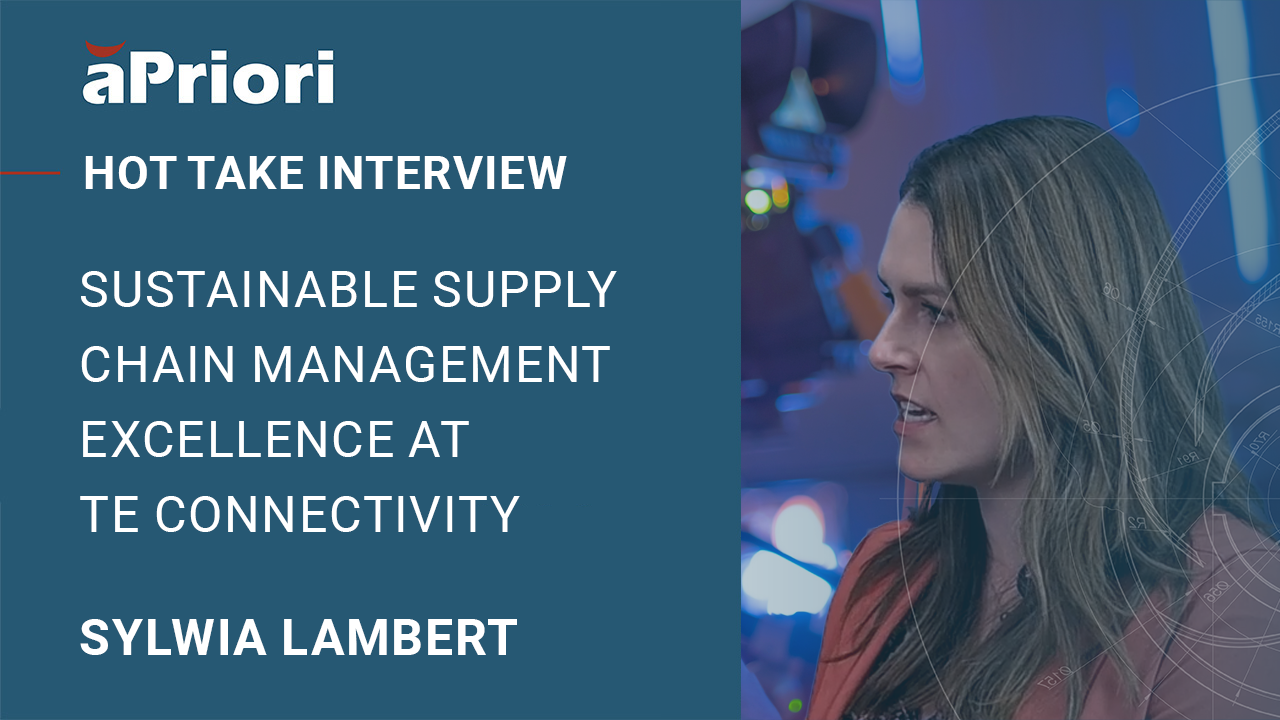
Sustainable Supply Chain Management Excellence at TE Connectivity
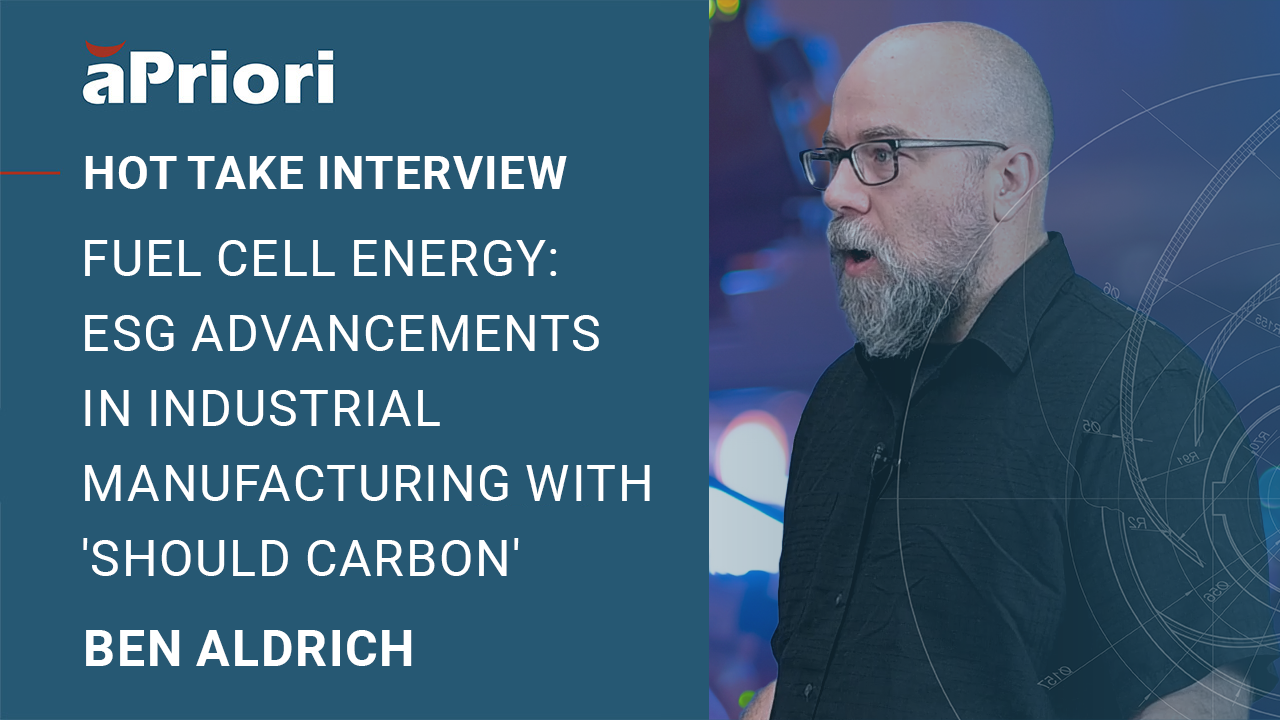
Fuel Cell Energy: ESG Advancements in Industrial Manufacturing with ‘Should Carbon’ and aPriori
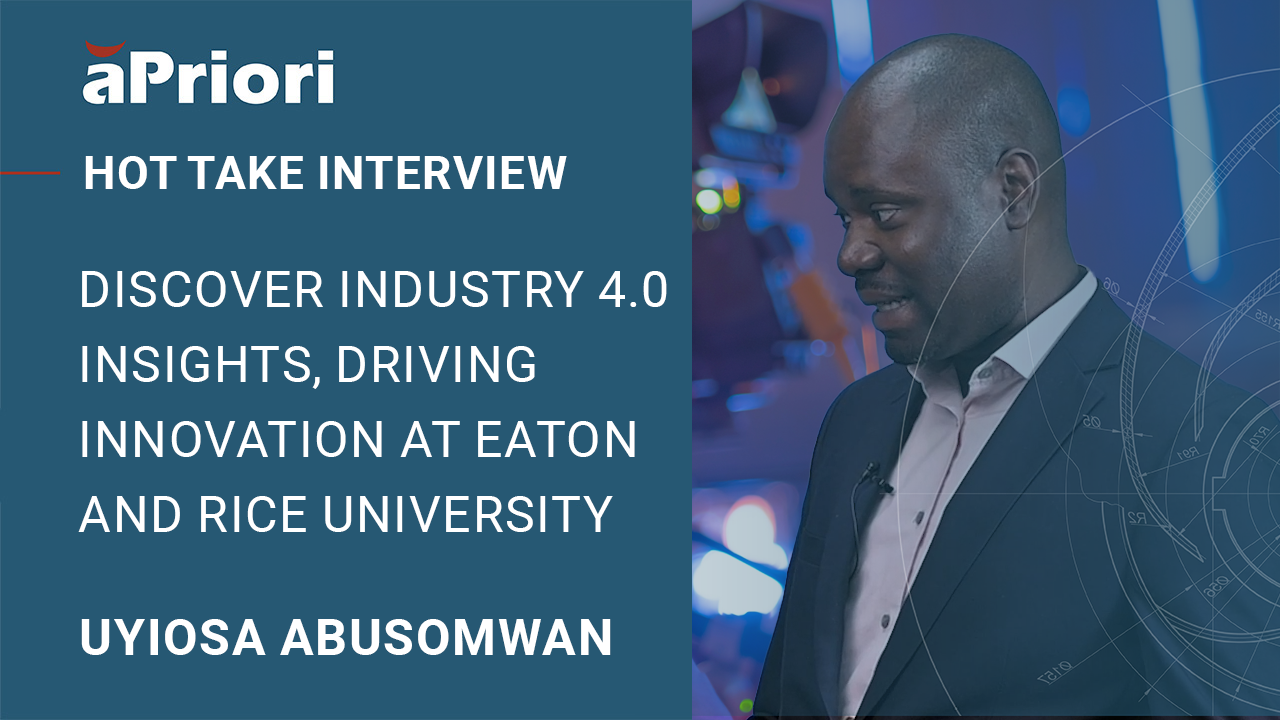
Industry 4.0 Insights: Driving Innovation at Eaton and Rice University with aPriori
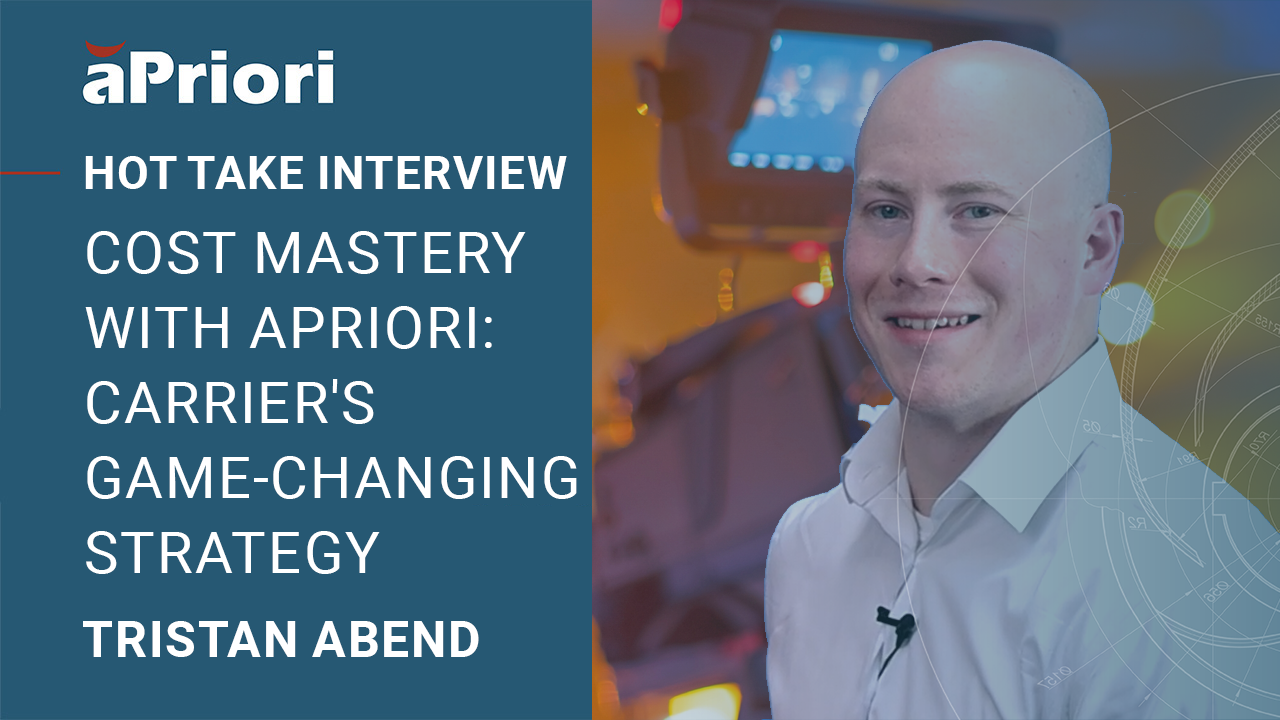