Video
aPriori for Should Carbon: Fuel Cell Energy
In this video, we delve into the concept of should carbon alongside should cost, focusing on how aPriori aids in understanding carbon emissions during manufacturing processes. FuelCell Energy’s journey with aPriori began four months ago, aiming to predict carbon emissions and enhance sustainability efforts. By utilizing aPriori’s capabilities, FuelCell Energy seeks to streamline design iterations, optimize procurement decisions, and ultimately reduce environmental impact while maintaining competitiveness.
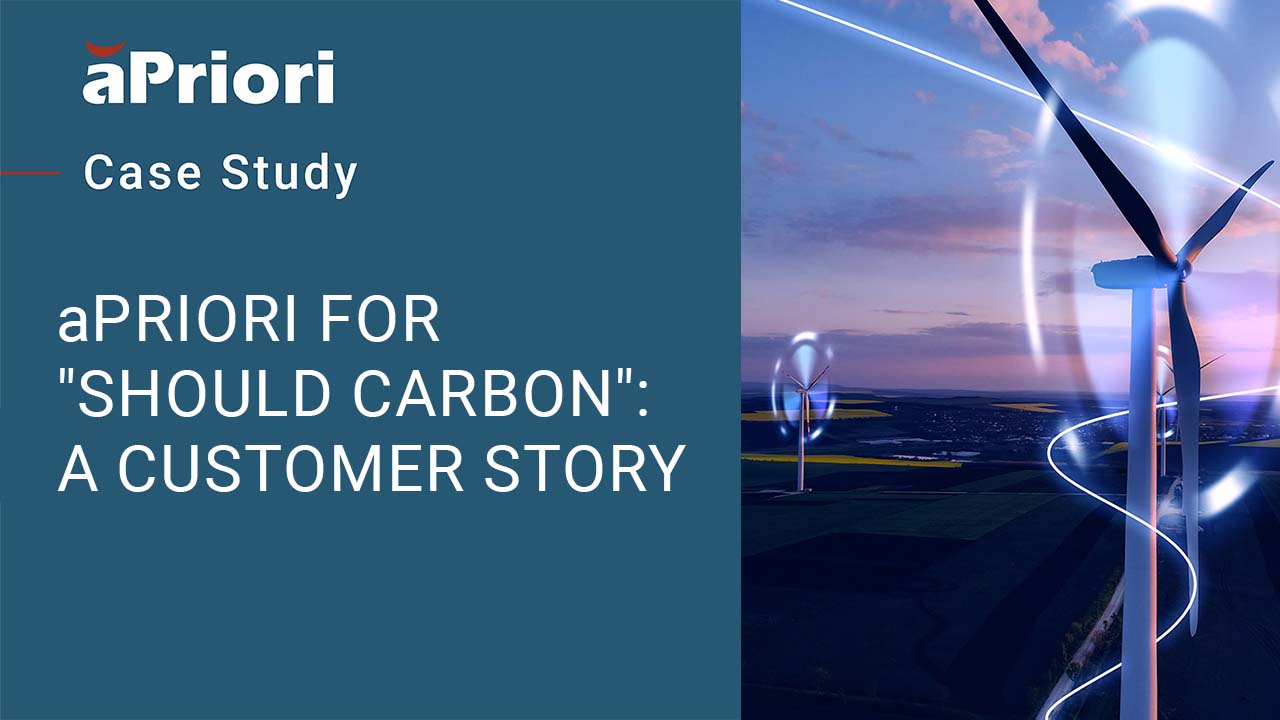
Transcript
Mark Rushton: So I’m really excited to be part of this session and a big thanks to Ben for being a part of it as well. When FuelCell Energy became a customer, I was really excited because the technology that they’ve got is quite exciting, very closely linked with sustainability. So it’s a really nice example that we can talk about today. But what we’re gonna talk about, Ben’s gonna give you an introduction to FuelCell Energy, what the product is, the company and then some of the challenges faced, so why they look to aPriori to help with that. Then we’ll look at should cost and what we call should carbon. So we’ll have a little explanation of that and then we kind of put together a bit of a case study to look at some of the opportunities identified using the aPriori. So with that, I’m gonna hand over to Ben to take us through FuelCell Energy. Thanks, Ben.
Ben Aldrich: Thanks. All right, all right. Hi everyone. As I’ve said, Ben Aldrich. I’ve been with FuelCell Energy for about 17 years, and we’ve been with aPriori for about four months now I think so it’s been pretty exciting. I’m really looking forward to digging into the software and getting a lot out of it. Just real quick, go through sort of what FuelCell Energy is and what we do. We’re here to enable a world empowered by clean energy. We have four core values. We really see aPriori fitting in for accountability and innovation, but we also prioritize integrity and safety.
One of the things that we do is we decarbonize power. We do this by producing decarbonized power or by capturing carbon to decarbonize other power production. The other thing that we can do with our product is produce hydrogen both to supply it or to store it for later use in some of our products. To some quick company highlights, we have over 220 megawatts currently in our field across 95 different platforms. We have a lot of patents for intellectual property for the technology that we have. We’re currently at 500 plus employees. We’ve been around for quite a while since 1969 and we have locations all across the world both in Canada. There was some Canadian jokes earlier, so I’ll refrain, Connecticut, Germany, and Asia with South Korea and Japan.
Just a real quick background on our history. We have been around for a while. We started out as a energy research company mainly looking at batteries and fuel cells. As we fast forward into the 2000s, we demonstrated our first distributed hydrogen plant, which is important because we just recently demonstrated our first commercial product which is in the 2023 bubble there. Last year we introduced our solid oxide electrolyzer in FuelCell products. So that goes back to the storage and reuse of hydrogen as a way to store energy and then utilize that energy later through solid oxide fuel cell. This is our leadership team. We’ve had people here who have been with the company since almost its inception to few months. This is actually the important one that I want to get to, the ESG strategy.
We’ve been talking about that a lot, and it directly relates to the CO2 and carbon and this is very new to FuelCell. We just recently added a group that’s responsible for this. It was very timely that we had launched aPriori since probably about a month ago. I got asked some questions like, “hey, can we figure out how much carbon is in our product?” And I was like, “I think I can.” So it was very good timing. So I really look forward to leveraging that portion of aPriori to help our ESG team in producing some of these numbers and analysis of our product. All right. And actually this was mentioned earlier as well with similar numbers, but electricity is gonna be big in the future and as a company that produces a product that generates clean electricity, that’s gonna be big for us. So I’m really, really looking forward to the bright future that energy has.
Let’s see. Yeah, I talked about this, decarbonizing power and producing hydrogen. And then so just a real brief overview of sort of our different product platforms. We have our solid oxide fuel cells and electrolyzers for producing and storing hydrogen. Our carbonate platform, which is the one that I’m mainly working on is capable of capture tri-gen as well as separation and both our carbonate and solid oxide products work to decarbonize power.
We have a lot of different applications that we can use our product for both from just generating power, generating hydrogen for transportation. A lot of our products are installed in onsite for heat and power and we also are able to utilize waste energy to create biogas, which then we can run through our fuel cell and create electricity and heat and, yeah. All right. These are actually links, so if you come up and push your finger on ’em, you can get ’em to work. No. [laughter] So yeah, we’re all about producing clean power and decarbonizing power, and we have a couple of products to do that and then again, hydrogen supplying and storing that hydrogen for later use. And I think if I click next, will it show all the answers?
MR: Oh, yes, it will actually.
BA: It will? Wow.
MR: So yeah, I will hand you the tag. Yeah. So on FuelCell Energy’s website, they’ve got a figure on there of almost 15 million megawatt hours that have been generated by FuelCell Energy’s plants. So I wanted to ask, and I’ve got some sustainable notepads with aPriori on to give out. So I went on to Bard, which is the Google version of ChatGPT and asked what you could do with 15 million megawatt hours. So they’ve got a big list on the next slide of potential answers. Does anyone want to hazard a guess what you can do with 15 million megawatt hours? Any guess.
Speaker 3: Miles.
MR: Miles, miles driven in a Tesla?
Speaker 4: You could propel yourself to the moon.
MR: Do you know how far that is? Just say… [laughter] Any answers at all? No, no such thing as a bad answer.
Speaker 5: 5000 flights, 5000 flights around the world for me.
MR: 5000 flights. That’s a good answer.
S6: Bitcoin mining.
MR: How many Bitcoin?
S6: A lot.
MR: Come on, we got to quantify it. We’re all about quantifying stuff at aPriori.
S6: Do I get a notepad?
MR: Yeah. Just hazard a guess. How many Bitcoin can you make? 15 million megawatt hours.
S6: One million.
MR: He’s pretty good. So there’s the list. So we’re in Florida. 1000 Florida homes for one year. And Florida uses more than the average in the US, ’cause of all the AC. 3.5 million miles in the Tesla Model Y. I think that’ll get you to the moon and back a couple of times. 100 million Tesla Model Ys, 1.5 million Bitcoins. So pretty significant amount. So yeah, I thought that was a really impressive figure and that was why I really wanted to have Ben tell FuelCell’s story. I’m going to hand back to Ben now ’cause in the news recently was how FuelCell’s tri-gen production system has really made a difference in your partnership with Toyota.
Renewable Energy Initiatives and the Auto Industry
BA: All right. So yeah, so I alluded to this earlier with our tri-gen product offering that we have. We just recently announced that we finished this product with Toyota. It’s currently in the Port of Long Beach in California. We’re able to utilize our product to use, I believe, to say, redirected biogas, but we use redirected biogas to generate electricity for Toyota. We also generate hot water that’s used to wash new cars as they come off that ships from Toyota. And then finally we also extract some of that hydrogen that we would normally convert into electrical power. We just keep it as hydrogen and we pipe that to the adjacent refueling station where they can refuel their fuel cell Mirai cars.
BA: So it’s pretty exciting. I was involved with going to the plant, making sure that the modules were fine, but it’s actually interesting the modules are pretty much our standard technology with just a little bit of a tweak. It was everything else there for the plant that was new. So that was a pretty cool thing that we had just done. And then there’s just some data. So we produce megawatts, 2.3 megawatts of renewable electricity up to 1200 kilograms of hydrogen every day and it also generates 1400 gallons of water, which in California, southern California is a pretty big deal, so.
Why Fuel Cell Chose aPriori to Predict Carbon Cost
MR: So yeah, as Ben mentioned, FuelCell took on aPriori about four months ago. Some of the challenges that were identified are listed here. There was no way to predict carbon at the current time, and really we were relying on suppliers for insights around cost. So there’s a significant opportunity for carbon and emissions reduction to be a competitive advantage and attract additional investment, streamlining design iterations, as we saw, being able to try out different things, getting that early manufacturing feasibility. Do you wanna comment on any of those, Ben?
BA: Yeah, I think so the issues identified at the detailed design phase. So for us and it’s come up a lot actually in all the sessions that I’ve been sitting in that if your engineering team comes up with a design in the hands to procurement to go out for a quote, it’s way too late. So for us being able to identify a lot of those manufacturing issues earlier in the design process is a really big deal for us because it’ll help speed up that design process and ultimately produce better designs. The other factor that we have to consider is that a lot of the engineers in our team are pretty new. So having a tool like aPriori also helps assist in looking at sort of design for manufacturability issues that a new engineer might not necessarily be able to identify. And then the last part there is the CO2 manufacturing footprint, like I said, is very timely because I just started getting asked questions about that. So it would be nice to have answers.
MR: So from identifying the challenges and then seeing what opportunities can bring, the next logical step is obviously seeing what capabilities you need to realize those opportunities. And these are some of the ones we kind of jointly identified. Were there any that stood out for you?
Procurement Teams and Carbon Pricing
BA: I think what I’m looking forward to and we really haven’t started exploring a lot yet is the improved collaboration, especially with our procurement team getting… It’s always been a challenge to get them involved earlier in the process, and with a tool like this, I think it’ll definitely help give them something that they can either start looking for suppliers for, or even start going out for bids if they need to. So I’m looking forward to that.
MR: And then we just got a brief kind of timeline of how you intend to work with aPriori. So obviously you onboarded a couple of months ago. The first workshop, that’s really where you identified the first potential savings. Is that right?
BA: Yeah, yeah, yeah. It was interesting as we started rolling our designs in and looking at having a tool where we could look at casting versus machining or welding and identify carbon emissions at the same time. Before we would have to make a design, hand it to our procurement team and get a quote. Now we can run the two designs side by side in the software and get results much faster. So yeah, there were a few items like that where we definitely identified some things that we can look at.
Should Carbon Metrics with aPriori
MR: So yeah, obviously aPriori has been known for should cost analysis for a very long time. So taking the material cost and the amount of material, so the rough mass of the material, all of the tooling required, the manufacturing process, assembly process, and the labor rate based on the regional labor rates to give a should cost which is not always the same as quoted cost. And we see customers using that a lot to have the fact-based negotiations, and facilitate a sustainable, financially sustainable relationship with all your suppliers. And so the next logical step was really should carbon and it’s essentially the same process. We just added on a couple of extra data points, so the local electricity mix and the carbon factor of the material, to give us the total manufacturing carbon based on those. So why should carbon is the next question. Well, with aPriori, we have a really in-depth knowledge of the manufacturing process. So we can give really an unparalleled understanding and level of precision when it comes to carbon. A lot of LCA tools just rely on assumptions, averages. They’re not looking at specific geometry ’cause they don’t read in any 3D CAD or anything like that. So they’re usually working on the finished mass. They’ll also look at the average power consumption of a machine. So they’ll say, “Okay, our CNC machine uses this much.”
The average power consumption is around 30%. It’s not necessarily related to a specific part, but this shows the power curve for injection molding. And we simulate this and actually use this power time curve to work out the carbon really precisely. So you can see the energy level’s really high when it comes to injection. You’ve got the clamping, but then energy drops right down when the part’s cooling. There’s still power being used ’cause the machine’s still on. It’s still heating the granules in the hopper. And then when it comes to ejections, there’s another bump of power consumption there. And this is true for all the different sizes of machines. So you’re going to really get a much greater understanding of where the carbon is and what level of carbon. And having price and/or cost and carbon in the same place just gives you that extra layer of fidelity to be able to compare what makes the most sense for your business.
And this was covered in the last session, but really there’s four levers for sustainability when we’re looking at embodied carbon and what goes into the product, and the geometry and the shape actually makes a huge difference in global emissions. And lifecycle assessments can’t deal with that. They don’t have any way of knowing what the shape or geometry of the part is ’cause all that’s fed into an LCA tool is the mass, the amount of material that goes in. So the same mass of material could have a hugely different amount of manufacturing process carbon because there’s more kind of a thicker section that takes longer to cool or really long and thin, different size machine as a result. So there’s a really complex kind of set of levers to work on and we do give that level of granularity. Then when it comes to regional C02 emissions, it’s often from the power grid and there’s a huge range from different countries as to where that electricity is generated. So whether it’s hydro electric, nuclear, coal, natural gas, we heard that a lot in Peter’s keynote this morning. That’s gonna really make a big difference to your manufacturing process carbon.
Demo: Running a Fuel Cell Part Through aPriori for Should Carbon Savings
And so because FuelCell are kind of just starting along the road, I decided I would take one of their examples and test both myself and aPriori. Worked with Ben on what would be a good example to use and look at how you can leverage aPriori to make decisions around cost and carbon. So we took one of the components and ran it through a bunch of different iterations, and then looked to different sourcing decisions as well. So we needed a baseline to start with. Can you just explain what this part… This assembly does just briefly?
BA: Yeah, sure. So this is the inner base for our FuelCell module. This is what we would build our FuelCell stack on. So it needs to hold the weight of the stack as well as provide some anchor points for some compression systems and things like that.
MR: And it’s in a quite corrosive environment. Is that…
BA: Yeah. So it’s hot and wet. So it’s fairly corrosive. Yeah.
MR: Okay. Excellent. So in the workshop, this was analyzed, so we’ve got our cost for assembly and all the components at around $2000. And the C02 was around 1500 kilograms or 1.5 tons so we had our baseline to start from. So bear in mind, I’m just the marketing guy. So don’t laugh at my CAD models too much. So took the same material. I thought, well, let’s see if we can consolidate it as a single part that’s gonna remove the assembly operation. Let’s just try it so quickly knocked up a part that could be machined. We kept the annual volume the same, kept the location the same, and my cost went through the roof. So it wasn’t a very good start as a good representation for marketing.
And the carbon also went up a lot, so that wasn’t so good. So I thought, well, maybe it’s the material. So tried a different material, went for a different steel, but powder coated ’cause of that corrosive environment. I stuck with machining, same volume, same location. Still a slight reduction in cost from my previous situation, but still a lot higher than Ben’s original design. So it didn’t look like I could do much to improve upon that. So kind of went back to the drawing board a little bit and decided to go for a cast design. So you can see I’ve updated the design, so there’s a bit less material. You can see I’ve actually thought about the DFM a little bit, remove some of the material and straightaway we’ve got a cost improvement over the original and also a fairly significant saving on carbon as well.
And so I was quite happy with that design. I thought I’d leave it there. Didn’t wanna do too much further to it. So I thought next thing to do is leverage the supply chain that FuelCell’s got and look at different locations around the world to see if we can further reduce it. So I took the American supply chain, Mexico, China and India and I ran it through aPriori and got some cost results for the part and some different carbon figures. So you can see quite a big variation in those four. But just to summarize what I ran through, so six different iterations after the original design, and you can see by choosing different locations, there’s a huge variation. So it’s just not intuitive. You do need to kind of run through and figure out where the costs are and where the carbon is. But they’re all data points and you can make decisions from these. So whatever’s most important to you and the business, you can use these data points to drive decisions, which is really the key.
Reducing Your Environmental Impact Leads to Happy Customers
So in summary, it really enables innovation because you can just try things out and no one’s gonna laugh at the results. It just gives you an idea of what’s gonna be the right direction. So you can really fill the funnel for strategic opportunities for carbon dioxide reductions, greenhouse gas reductions, energy transition incentives, and it just gives you really clear insights on what’s good, what’s bad from quite a high level and look at whole assemblies and where to focus using the analytics. So when it comes to reducing cost and carbon, that’s what we expect. You can determine lower cost, reduce the environmental impact and reducing the environmental impact is going to increase the value of the product. More consumers are going to want to choose it, more customers are gonna want to choose it. You’re gonna maintain a higher status with who you are supplying to. And it gives you that extra agility just by being able to validate different options. Try what if we do this? Just means you’re gonna make better decisions earlier and stay competitive. So really the crux of it in my mind is it’s data-driven decision-making and that’s what we all want to do. We wanna remove the emotion, the intuition from it and make decisions on data. So I wanna say a big thank you to Ben and for FuelCell Energy for coming and sharing their story and thank you all for attending this session.