Case Study
How GE Appliances’ Should Cost Model Implementation Transforms Cost Engineering
Discover the transformative outcomes of GE Appliances’ journey with aPriori, highlighting the manufacturer’s four-step change management approach to effective should cost implementation.
This case study explores the challenges, strategies, and results achieved by embedding a should cost analysis tool within the organization.
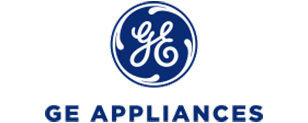
Company Details
Industry
Home Appliance Manufacturing
Number of Employees
16,000 (Based in the U.S.)
Revenue
$2.6 billion
Website
aPriori Product
aP Pro; aP Analytics
The Problem
Difficulty in implementing a should cost model solution due to the need for change management across various departments and stakeholdersThe Solution
Embedding aPriori should cost models to improve cost estimation and communication throughout the product development processWho is GE Appliances?
GE Appliances, headquartered in Louisville, KY, is the fastest-growing appliance manufacturing company in the United States (U.S.). The company is majority-owned by Haier and has nine manufacturing facilities throughout the country. These facilities enable GE Appliances to continuously launch new products, such as dishwashers, dryers, ovens, refrigerators, and more.
At the 2023 Manufacturing Insights Conference, Jill Snyder, GE Appliances’ Cost Engineering Director, provided insight into the company’s yearly operations. She revealed that the company procures 3 billion parts, builds 2,500 units per hour, and delivers an appliance every 13.8 seconds through its robust nationwide delivery network. GE Appliances is also committed to sustainability as it recycles more than 100 million pounds of cardboard, wood, and plastic to ensure a greener future.
The manufacturer’s impact on the U.S. economy cannot be underestimated. According to GE Appliances’ annual report, the company contributed a total of $24.5 billion to the U.S. gross domestic product (GDP) in 2022. The report also highlights the following:
- Between 2016 and 2022, GE Appliances helped create 89,000 additional jobs in the U.S.
- The manufacturer spends $4.9 billion with 6,300 suppliers across the country.
- Over the past five years, the company has invested $2 billion in its U.S. operations.
Problem: Difficulty Implementing Should Cost Modeling Software in a Large Company
GE Appliances needed to source 3 billion components for its diversified and complex product portfolio, which includes various finishes. However, traditional and manual tools, such as spreadsheets, were inadequate for such a large cost estimation responsibility.
As a solution, the company turned to aPriori’s automation-driven platform for a streamlined and detailed cost breakdown analysis. But, like most large organizations, GE Appliances faced challenges in embedding new technology across various departments, including design engineering, product cost engineering, sourcing, and procurement.
Solution: Utilizing a Four-Step Approach to Embed aPriori Should Cost Modeling
To overcome its aPriori implementation challenges, GE Appliances followed a four-step change management process. Learn about these steps in the company’s 2023 Manufacturing Insights Conference session in the video and descriptions below:
1. Prepare the Organization
This phase involves activities such as creating awareness about aPriori within the organization and obtaining leadership support for its implementation.
2. Craft a Vision and Plan for Change
In mid-2020, GE Appliances adopted aPriori’s advanced should cost estimation platform. This was during a time that significantly impacted business and people. The manufacturer dedicated the latter half of the year to a series of aPriori sprints aimed at leveraging the tool’s raw material libraries.
GE Appliances’ four-member costing team supports 1,600 design and manufacturing engineers located in the U.S. The company’s goal was to cost as many purchase parts as possible using additional aPriori cost models and surface treatments before implementing the tool organization-wide.
To ensure the successful utilization of aPriori, GE Appliances conducted a Before-Action Review (BAR). The BAR methodology addressed questions about the company’s intended culture, goals, and metrics. It enabled the company to identify potential challenges and consider the available aPriori training plans for its cost engineers.
After completing the BAR process, the manufacturing company focused on creating a vision and plan for change in three critical areas:
- Organization-related changes. GE Appliances identified the skills, knowledge, and experience required for its cost engineers. Additionally, the company selected aPriori administrators and established cross-functional collaboration between technology, sourcing, and computer-aided design (CAD) teams. This enabled the organization to improve data transparency, increase process optimization, and align cost management goals across the business.
- Project-related changes. The company has evaluated its product development process to ensure the successful integration of should costing into the organization. By effectively implementing should cost, GE Appliances will be able to regulate its internal cost estimation activities. To achieve this, the company has developed training plans and communication strategies to increase alignment and buy-in for using aPriori. Additionally, GE Appliances has established regular reporting updates to ensure that should cost analysis remains a top priority within the organization.
- System-related changes. The changes made by GE Appliances focused on data management optimization. This included standardizing data inputs from various sources, such as CAD models and product lifecycle management (PLM) systems. As part of these efforts, the company has developed plans for managing its raw material library and established access control measures. The aPriori solution has also been configured to meet the company’s needs, and mandatory fields have been defined to ensure consistency and accuracy in cost estimation, leading to enhanced decision-making.
3. Implement the Changes
During this phase, GE Appliances focused on implementing the changes defined in step two, which involved making improvements to the organization, projects, and systems.
To ensure the success of organization-related changes, GE Appliances communicated its end vision to both its aPriori and internal teams regularly. The company made sure that all stakeholders were using the same costing terminology, for instance, explaining that aPriori is a CAD-based solution, not a traditional spreadsheet tool. Further, the organization reviewed competency changes to guarantee a seamless transition.
As for project-related changes, GE Appliances made adjustments to its product development process. The manufacturer also held meetings with its internal Pulse team, which comprised key organizational leaders such as the CEO and profit and loss (P&L) owners. These discussions were crucial in ensuring that aPriori’s should cost models were utilized effectively throughout the product lifecycle.
Finally, GE Appliances implemented system-related changes by establishing defaults to increase the number of parts that could be costed, ensuring accuracy when using aPriori. The company also focused on achieving consistency in costing by defining raw material library management, access control, and data sources. Moreover, it defined standard operating procedures (SOPs) to ensure that all users can cost the same part, identify cost drivers, and generate consistent results.
4. Embed Changes Within the Company Culture and Practices
GE Appliances conducted an audit to identify any regression and re-evaluated its goals to ensure that changes in the company culture and practices were sustained. Necessary adjustments were made to maintain the growth achieved by implementing the aPriori platform and leveraging its should cost insights.
Results: Increasing Cost Estimation Accuracy and Return on Investment (ROI)
GE Appliances experienced a significant improvement in its cost accuracy after implementing aPriori. However, the exact magnitude was not quantified. The company also observed consistent annual growth in its ROI. With aPriori, GE Appliances’ cost engineering team gained the ability to cost more parts quickly and accurately, leading to increased productivity and time savings.
Moreover, aPriori provided transparent cost structure details that have improved communication and collaboration across GE Appliances’ supplier relationships. This allowed the manufacturer to capitalize on more cost-saving opportunities. aPriori has also been integrated into the company’s e-RFQ tool and design process, resulting in earlier cost considerations throughout the product life cycle.
What’s Next?
GE Appliances will continue to incorporate aPriori into its workflows, aiming to maximize the platform’s benefits, including enhanced cost savings and efficiency.
Experience aPriori in Action
Meet with an aPriori expert and learn how we can help you eliminate product costs, improve productivity, and reduce your carbon footprint.