Digital Manufacturing & Design Engineering: The Secret to Cutting Cost
Key Takeaways:
- Design engineers are a critical foundation in reducing product cost and ensuring manufacturability and sustainability
- Digital manufacturing solutions provide automated insights to onboard new designers faster, share institutional knowledge, and increase savings and DFM
The Full Article:
Forbes reports that 57% of surveyed manufacturers found students were prepared for CAD. However, 65% of students were not equipped to create manufacturable designs. And because 80% of a product’s cost and environmental impact is determined in the design stage, that’s a significant shortfall in the incoming workforce. It also is a challenge for product manufacturers already facing a shortage of design engineers.
Today’s design engineers have cost implication awareness about the products they are creating. However, there has not been a true cultural shift on the part of most manufacturers to prioritize it early in design and ensure that design engineers have the necessary knowledge and tools. The good news is that both design for manufacturability (DFM) and cost issues are easily remedied with the right digital manufacturing solution.
The Design Engineer: Key to Analyzing Cost and DFM
An Accenture report surveyed 1,200 industry experts to investigate their organizations’ speed to market. It notes that, on average, these industry leaders reduced their speed to market from 56 down to 42 weeks over the last five years. And they were focused on further reducing that number down to 29 weeks within the next five years. What’s more, the report found that 81% of these time reductions between 2016 and 2021 were achieved through technology.
Design engineers must expand their scope, leveraging digital manufacturing solutions, to factor cost, sustainability, and even sourcing into their design and enable faster time to market in the process. However, the reality is that 80% of products in production are often stuck with designs that could have realized significant cost savings if early design stage decisions were made. The result is a manufacturer that lags behind the competition, loses substantial market share, and experiences a revenue drop.
Many design engineers work in a silo, with little to no true collaboration with other product development teams. As a result, there is no single source of truth that is standardized and repeatable. Furthermore, design engineers don’t always have a clear, comprehensive understanding of the full project scope or the organization’s end goal. It can create a domino effect if the design does not align with the other project parameters or overall strategy.
Three Keys to Ensuring Design Engineering Prioritizes Cost
By the time a product launches, most decisions are already locked in. Again, it emphasizes the importance of identifying and remediating cost and manufacturing outliers early in design. However, it requires a change in the design engineer’s mindset and the right digital manufacturing solution. These three strategies can support this important shift:
- Keep cost top of mind. This strategy should start from the top down. The earlier design engineers have cost KPIs, the more likely they are to achieve them. If retail is your channel, you have to ensure that your new products are ready for seasonal store resets. If you miss the delivery window due to a late design/component change, your revenue stream could take a huge hit. The design engineer is key because early trade-offs and decisions not only increase cost savings but reduce later design iterations as well. There also is better facilitation to meet crucial milestones and ensure the product launches on time.
- Know your competitive position. Internal and competitive costs can be difficult to know. For example, some manufacturers are concerned design engineers will try to negotiate such costs with suppliers. In situations where the parts might be cost-prohibitive for the design, manufacturers might forgo sharing such cost data with the design engineer. In other cases, factory and other overhead charges on a component or assembly might not be transparent. These charges confound many design engineers since the purchase price and the internal cost can vary widely. Instead, the design engineer should focus on how their product/design stacks up versus the competition’s. Competitive product tear-downs and a like-for-like comparison of should-cost data – derived from part and manufacturing analysis using a tool like aPriori – should be a driving force in product development. Using this approach, the internal designs can be evaluated relative to the competition to determine if there are more cost-effective material substitutions, better design approaches or tradeoffs, and/or more efficient manufacturing processes.
- Use digital manufacturing solutions to achieve cost and manufacturability goals. Most of a product’s cost is embedded in the design. However, those costs are not always so obvious. A spreadsheet cannot reveal all variables including market volatility, competitor product development, or the unintended consequences of not understanding a process or location’s impact on sustainability. That is why a digital manufacturing solution is a design engineer’s best friend. It can provide insights early in the design stage to reveal the cost drivers that impede manufacturability and slow time to market.
Three Major Design Cost Drivers
Digital manufacturing can address these design cost drivers:
- Manufacturability: Cycle times, overhead, and other factors drive up manufacturability costs. Without a digital manufacturing solution, it is nearly impossible for a design engineer to consider all what-if scenarios that could impact manufacturability. aPriori weighs such scenarios. Should you die-cast or forge a part? Where is the most cost-effective place to manufacture? China? Mexico? Can we get the parts we need at a good price and on time? If not, what alternative parts should we consider? Carbon is another cost consideration. Most designers don’t take energy usage and material waste into account. Design for Sustainability can compensate for this knowledge gap.
- Late changes: Without the ability to communicate and collaborate across all product development teams, design engineers run the risk of late-stage iterations. The digital twins (product, process, and factory) empower the design engineer and other teams to collaborate and test design feasibility and affordability early. Early design, fact-based discussions drive the right product development decisions – starting with design.
- Time to market: Testing designs early also allows product development teams to fail fast in order to innovate. The earlier and faster the innovation fails, the less time to market is lost. And slower time to market equates to revenue losses. Conversely, digital manufacturing simulation affords design engineers the ability to validate their designs early and often, shift gears when necessary, and have the tools to do so effectively.
Digital manufacturing solutions encourage questions and also provide answers. What can you change today to improve your manufacturing design processes? How would you go about making those improvements? What has been overlooked in the product development lifecycle?
aPriori’s solution allows manufacturers to input their CAD with a simple click. The result is cost, manufacturability, and carbon insights, yielding the greatest reductions and optimizing the product – all in a clear, implementable manner.
Digital Manufacturing Can Create a Better Design Engineer
The average age of an experienced design engineer is now over 50. Today’s design engineers cannot afford to focus solely on design. However, a gap still exists between experienced design engineers and less seasoned ones. Manufacturers need to close it.
Digital manufacturing solutions can close gaps, enhancing communication and collaboration. They also provide valuable insights and recommendations that build a design engineer’s knowledge base. Conversations can be facilitated between all product development teams and suppliers. It can bridge geographical distances between the design engineer and where production actually resides too.
With each successive conversation, the information base builds both within the design engineer and the organization’s institutional knowledge. The latter serves as the single source of truth for the organization, enabling decision history access and traceability. aPriori’s aP Workspace simplifies task management, improves real-time collaboration, ensures fast scalability, and provides a checklist of considerations for manufacturers. When more experienced design engineers retire, less seasoned ones will be able to get up to speed faster.
Digital manufacturing doesn’t just create a better design engineer. It enables a more holistic design approach and greater agility and scalability throughout the organization.
Deep dive into maximizing profitability through design in this video.
Is Design at the Expense of Your Bottom Line?
Design for Manufacturability Mitigates Costly Issues Early in Product Development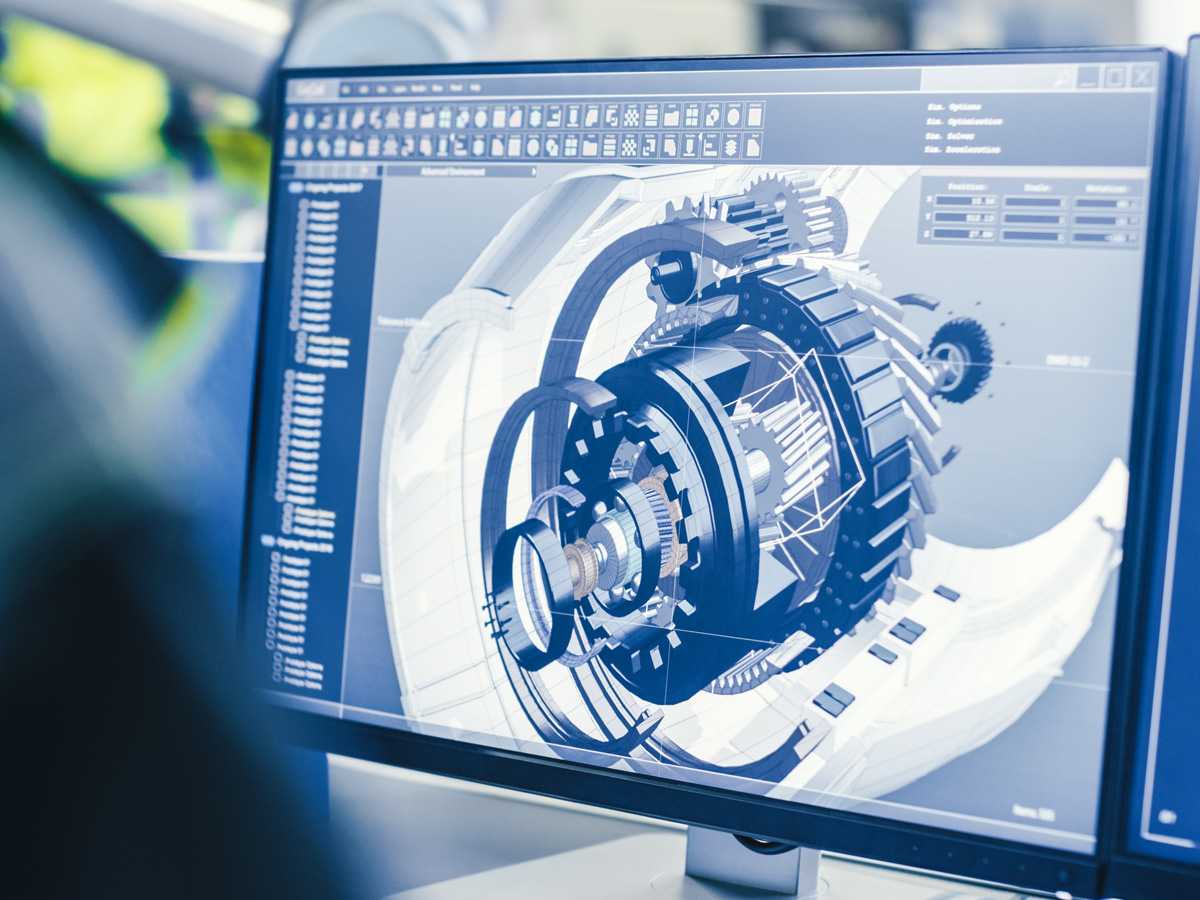