6 Areas Design Engineers Can Minimize Manufacturing Risk
Key Takeaways:
- Design engineers can play a significant role in mitigating manufacturing risk
- aPriori manufacturing insights provide a guide to reducing design iterations, costs, supply chain, labor, and sustainability risks, and improving production and collaboration
The Full Article:
How can you, as a design engineer, minimize manufacturing risks while ensuring manufacturability, profitability, and sustainability?
The right manufacturing insights solution gives design teams real-time visibility via their native CAD environments. Such a solution provides insight into the design engineer’s ability to drive innovation while simultaneously reducing manufacturing risk. aPriori works seamlessly in their native CAD environment to identify potential manufacturability, sustainability, and cost issues, while optimizing product value.
The design engineer, armed with an effective manufacturing insights solution, can play an integral role in minimizing manufacturing risks. This powerhouse combination can optimize product value, reduce costs, enhance sustainability, and accelerate time to market.
6 Ways to Mitigate Risks and Reap Rewards
A design engineer’s technical expertise cannot be the end-all in risk mitigation. It requires a team effort throughout the product development lifecycle. However, design is the most influential point in product development. Manufacturing insights can enhance the design engineer’s knowledge and ensure the most cost-efficient, sustainable, and optimal product. Consider six areas where the design engineer and manufacturing insights can mitigate risk:
1. Cost Overruns: Approximately 80% of a product’s cost is determined in the design stage. A solution like aPriori can analyze a product design before proceeding to the next product development stage. Early design stage feedback can identify and remediate cost outliers. Design iterations and engineering change orders (ECOs) are reduced, saving time and money.
For instance, insights might reveal excessive and unnecessary machining steps. Reduced cycle times save energy, labor, material, and utility costs. Trade-off analysis can offer material selection, production volume, or manufacturing method (i.e., casting vs. machining) options via design, further reducing costs.
A Forbes article notes that nine out of 10 manufacturers intended to raise their prices in the second half of 2023 in anticipation of further inflation hikes. Fifty-seven percent had already increased prices by 5% this year. Designing to cost can eliminate such price hikes without compromising product quality, consumer trust, or profitability.
2. Supply Chain Risk: A Deloitte survey found that only 25% of firms believed they could identify and predict supply disruptions in a timely manner “to a large extent.” Using a product like aP Design, designers can generate should costs, understand the ideal manufacturing process, and get the right information to help support negotiations. A digital factory is created using manufacturing cost models. In conjunction with Regional Data Libraries (RDLs), manufacturers can target the right suppliers, accurately forecast costs, and receive redesign suggestions to reduce risk. Analysis can inform material and production alternatives, accelerating time to market. It also helps mitigate the number of design iterations and ECOs, which can lead to further delays.
Design engineers also have a prime opportunity to improve product quality at this juncture. Cost engineers and sourcing can further lower costs through fact-based negotiations with more detailed supplier data. Because all team members work with the same data in real time, sourcing teams are getting supplier quotes based on the latest designs and product requirements, which can accelerate procurement.
3. Sustainable Products: A McKinsey article revealed up to four-fifths of a product’s lifetime emissions are determined in the design stage. Design for sustainability can help lower a product’s carbon footprint. It considers raw materials and manufacturing processes’ environmental impact, from product inception to its end of life. The design engineer can help determine if recycled materials can be used to make the product or at a minimum, be recycled, reused, or repurposed beyond the product’s life.
aPriori calculates CO₂ equivalent emissions, using geometry-driven analysis of 3D CAD data. Design engineers can reevaluate and identify more environmentally friendly materials. They also can reduce material waste and energy usage via the product’s manufacturing processes, and work with sourcing to find local suppliers with the right parts to further decrease the carbon footprint.
4. Skills Shortages: Deloitte revealed as many as 2.1 million manufacturing jobs will go unfilled by 2030, leaving manufacturers struggling to find skilled people.
Our solution provides automated design guidance and can proactively identify and prioritize Design for Manufacturability (DFM) issues and cost outliers. They provide knowledge-based training to the next generation of design engineers. These automated, highly accurate insights also reduce human error and product recalls. Design engineers can create high-value, cost-effective, and sustainable products quickly, reducing iterations and boosting time to market.
5. Time to Market: Gartner found just 55% of all product launches occurred on schedule. Forty-five percent of delayed product launches were overdue by at least one month, with 20% on average failing to meet internal targets.
Design is where production can see the greatest gains in getting to market faster. Cost outliers and manufacturability issues can be identified early in design, decreasing iterations, ECOs, and product development speed bumps. Designs can be reconfigured around material shortages, using RDLs to find alternative suppliers. Sourcing and quoting can be expedited, reducing potential production problems.
6. Multi-team Collaboration: Information siloes create product development vulnerabilities and slow time to market. A solution like aP Workspace centralizes knowledge-sharing and problem-solving across product development. Teams can collaborate, comment on data and 3D models, and configure their information view to align necessary data with their roles.
Product development teams receive real-time updates to quickly remediate issues. aP Workspace brings designers, cost engineers, sourcing, sustainability, and production to more efficiently communicate and collaborate.
Optimize Design Insights and the Benefits Will Come
Today’s risks can be tomorrow’s opportunities…if you have the right tools and roadmap in place. Design engineers have a prime opportunity to significantly impact the bottom line, meet sustainability initiatives, and mitigate many manufacturing risks. By leveraging manufacturing insights like aPriori, they improve product value and ensure resilience and a competitive advantage in the marketplace.
What Can Digital Twins Do for You?
Discover How to Mitigate Risk Across Product Development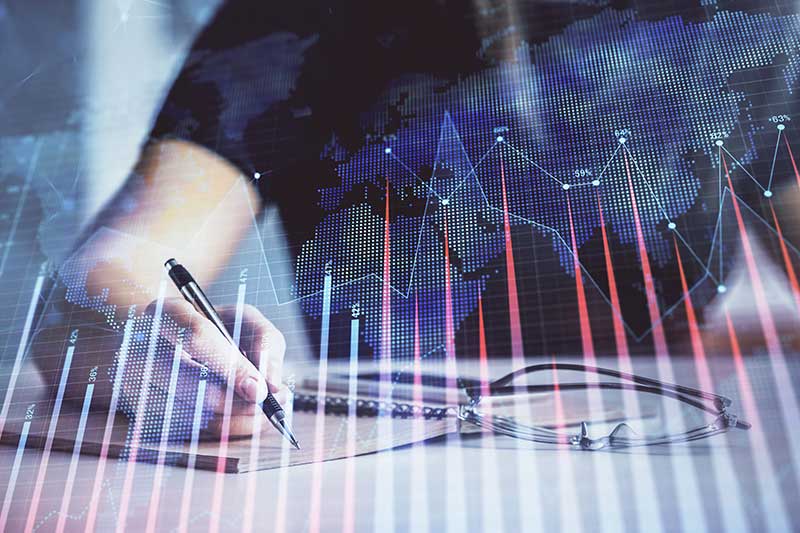