4 Steps to Reducing Manufacturing Risk for Design Engineers
Today’s everchanging environment requires forward thinking and the ability to pivot quickly. Design engineers can play an integral role in lessening or circumventing manufacturing sector risks such as supply chain disruptions, the Ukraine war, inflation, material and labor shortages, and more. Combining the design engineer’s expertise with insights afforded by manufacturing simulation, many risks can be eliminated, or at least lowered.
In this article, design engineers will discover how their expertise, combined with manufacturing simulation, can reduce – even eliminate – risks such as supply chain disruptions, inflation, and material and labor shortages. As a result, they can improve their operations, meet cost targets, address many labor shortfalls, and mitigate other manufacturing sector risks.
A Deloitte 2022 Manufacturing Industry Outlook report found that despite the pandemic and other significant challenges, the US manufacturing industry is poised to recover – even surpass – pre-pandemic midyear industrial production and capacity utilization. Additionally, the uptick in new orders among all major subsectors indicates continued growth in 2022. However, there are more manufacturing risks than ever. How can manufacturers mitigate or eliminate them altogether?
What is a Manufacturing Risk?
Manufacturing risk is any factor that can disrupt a manufacturer’s day to day operations and ability to produce parts and assemblies cost-effectively and on time. As the pandemic illustrated, one risk can create a domino effect. Labor and material shortages impeded the supply chain throughout the world. Other manufacturing risks that have surfaced over the last year include the impact of the Ukraine war on critical materials and supply chains for many manufacturers. Inflation and higher fuel costs also have put a crimp in manufacturing risk management.
Types of Risks in Manufacturing Industry
Risk impacts manufacturers’ time to market as well. Manufacturing sector risks can affect the entire enterprise. If the supply chain is disrupted, sourcing and procurement will have an uphill climb to secure the necessary materials. Labor shortages surely will impact all facets of an organization but particularly, production. Inflation and higher fuel prices will require cost engineers to further crunch the numbers.
The good news is that design engineering can play a key role in reducing manufacturing risks. Design engineers can be the first line of defense against rising product costs, but only if they’re empowered by real-time data-driven models.
How Can Manufacturing Risks Be Reduced?
Though the horizon looks bright, there are ongoing manufacturing risks that – if not properly addressed – will hinder the growth trajectory. The strength of an enterprise lies in its operational efficiencies and profit margins.
Design engineers can reduce the manufacturing risks by taking these four steps.
- Design to Cost and Mitigate Inflation
Inflation, higher fuel costs and supply chain delays have driven up costs, placing them at the forefront of manufacturers’ production decisions. Manufacturers must research whether choosing to manufacture locally will cost more or less. It’s also time to re-evaluate whether outsourcing is still the most cost-effective approach.
Reputable simulation software can provide manufacturing risk assessment including weighing outsourcing versus in-house production and offshoring versus onshoring. Designing to cost ensures that inflation and other price surges will not unduly influence your customer’s ability to purchase. It also will keep your profits from eroding. Manufacturing risk management can target costs for every part.
- Design for a More Efficient Supply Chain
The nemesis for many enterprises, supply chain has played a major role in manufacturing risks. Avoid shipping delays, thefts, and costs by designing parts for local manufacturing processes. Global political and environmental challenges like the Ukraine war and foreign currency exchange rate fluctuations can be bypassed by designing to a more local supply chain. Manufacturers no longer have to rely on foreign suppliers and their associated risks such as liability exposure and uncontrolled inspection practices.
Instead, designers can collaborate with their internal supply teams, procurement, and local suppliers. Manufacturing risk analysis can aid in this process, making onshoring or reshoring a real possibility. Manufacturing simulation software, used to manage manufacturing risk, can analyze the cost of shipping versus higher fuel prices and shipping delays. Although labor costs might be higher with onshoring, they could be negated or evened out due to higher offshoring costs and the convenience of onshoring. Micro factories also can offset higher costs with lower volumes and fewer shipping channels to navigate.
Trade off analysis – as illustrated above – allows designers to see the cost and supply chain impact of making material, manufacturing (i.e.-machining instead of casting), volume, and design changes.
- Design to Collaborate with Suppliers and Sourcing Teams
Reliance on materials, processes and practices that negatively impact the environment are pressuring manufacturers to move towards sustainability. As consumers become more socially aware, they might opt out of a manufacturer’s product or boycott any organization that negatively impacts the environment. Additionally, regulations may force manufacturers to design with sustainability in mind. This Gartner chart on workforce issues substantiates this sustainability push.
Engineers can leverage sustainability’s design-centric influence – both from an environmental and organizational standpoint. The right manufacturing simulation software can lower manufacturing risks and facilitate sustainability efforts like:
- Collaboration earlier in design with sourcing and suppliers to seek more environmentally friendly materials and methods for producing them
- Less reliance on one specific supplier, material, or process (reducing exposure if any of them fail or disappear)
- Reduction of carbon footprints by finding more local suppliers
Traditionally, engineers created designs without considering cost. Now, manufacturing simulation enables them to work with all teams throughout the product lifecycle to design to cost and more sustainably.
- Design to Work and Circumvent Labor Shortages
According to Deloitte, as many as 2.1 million manufacturing jobs will go unfilled by 2030. This shortage will create a void and manufacturing risks for many struggling to find skilled people.
- How experienced is your design team? Are you encountering a shortage of skilled designers who truly know how to design for manufacturing? Could automated design validation for manufacturability help them to focus on adding value?
Automated Manufacturing Insights, with quantified design guidance, can compensate for fewer or less skilled design engineers through design for manufacturability (DFM). These solutions attract more technology-focused workers as well. It can fill the labor gap with intelligent, automated DFM tools to catch human errors or suggest design improvements without needing experts to check everything.
Conclusion
Design engineering is no longer confined to a napkin sketch, hoping on a wing and a prayer that it will come to fruition or that it won’t go over budget. With the right simulation software, it can identify potential manufacturing risks. Moreover, design engineers can address them early in the process further reducing their manufacturing sector risks. More importantly, it enables manufacturers to create a high value, cost-effective product that they can bring to market quickly.
Manufacturing simulation enables organizations to learn digitally, rather than physically, providing an invaluable tool for risk reduction.
Want more tips to reduce your manufacturing risks?
Learn how design to cost and design for manufacturability can reduce or eliminate manufacturing risks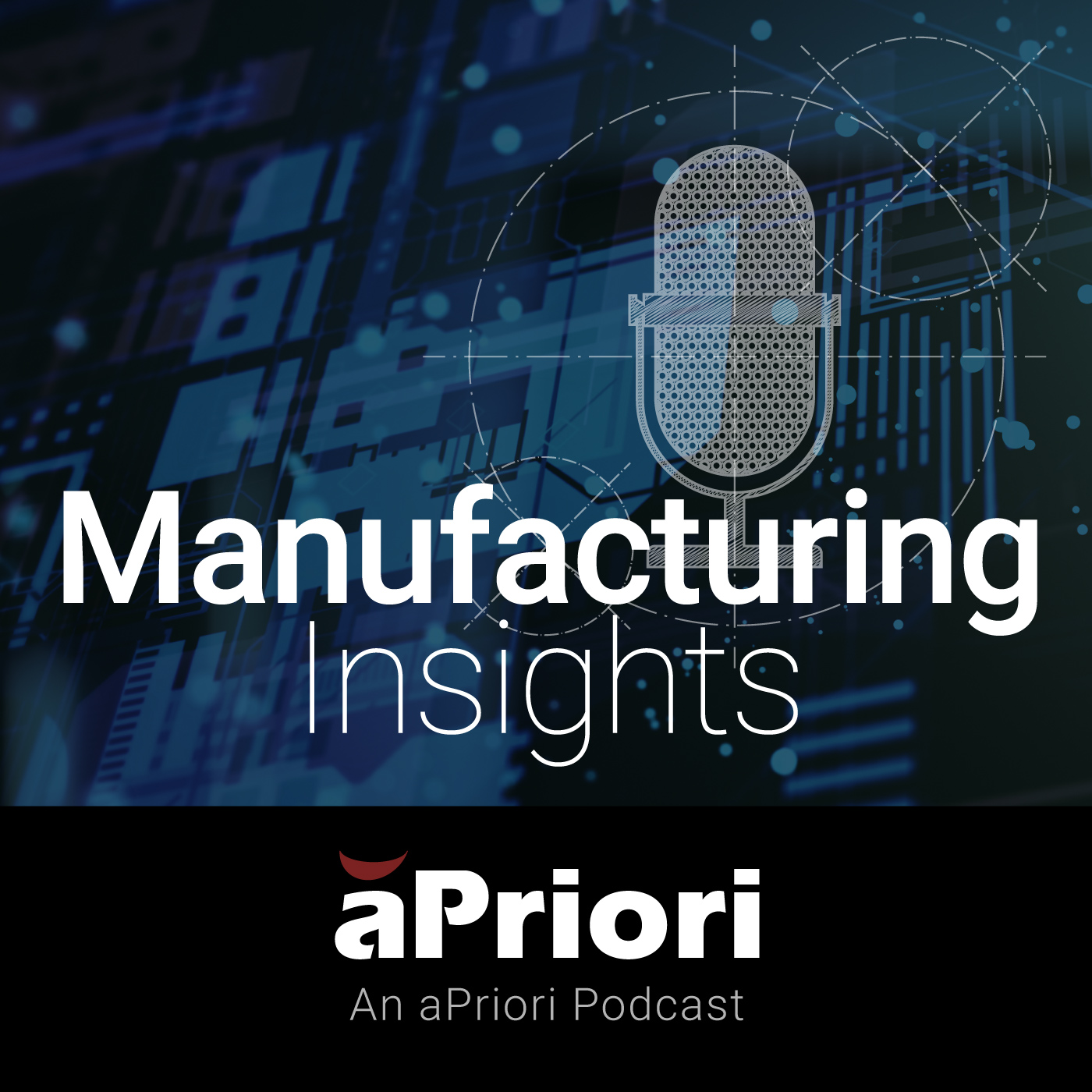