How to Calculate the Additive Manufacturing Breakeven Point
Key Takeaways:
- 3D metal printing, other advances drive applications for printed parts
- Learn how to determine when it’s profitable to use additive manufacturing
The Full Article:
The additive manufacturing market is projected to grow nearly 21% CAGR by 2030, according to Grand View Research. Industrial manufacturing is fueling this demand based on Grand View’s projections that metal 3D printing will overtake polymer as the additive material of choice by the end of the decade.
OEMs, contract manufacturers, machine shops, and other suppliers can use additive manufacturing for a competitive advantage if they have the insights to determine when to use 3D printing vs. traditional manufacturing. Learn how companies are using 3D printing effectively and how aPriori enables manufacturers to evaluate trade-offs between additive and traditional (subtractive) production processes.
(New to additive manufacturing? Read our quick primer blog post that explains how 3D printing works and its benefits.)
3D Printing Trade-offs
There are multiple factors to consider when evaluating 3D printing vs. subtractive manufacturing options. Traditional manufacturing methods may produce cheaper, but heavier parts at high volumes. But using machining, casting, or related manufacturing processes for low-volume production runs will significantly increase per-unit costs.
Additive manufacturing is moving beyond R&D and prototyping, although the cost advantages for small production runs and quick manufacturing times are central for additional applications. This includes evaluating additive manufacturing to reduce weight and part count (complexity), produce complex components (e.g., designs with mesh instead of solid structures), and increase performance.
Additive Manufacturing Process Examples
It’s important to consider the most appropriate manufacturing process for your additive manufacturing needs/use case. We’ve highlighted how popular 3D printing processes vary by technology, applications, and materials.
Products Made with Additive Manufacturing
Here are examples of how companies are using additive manufacturing to gain an advantage in one or more key areas:
- Access and Availability: How do you get replacement parts in the middle of the ocean? The US Navy equipped the US Bantam with a metal 3D printer to produce standard components and unique parts.
- Cost: The economic advantages for small production runs is a pillar of additive manufacturing. In one example, A supplier cut the cost of a door hinge arm by 50% thanks to 3D printing.
- Complexity: BMW uses the SLM metal 3D printing process to produce mountings for a sunroof mechanism. Due to design complexity, the automaker could not manufacture the component with a traditional casting process.
- Part Consolidation: Examples abound, including an aircraft engine fuel nozzle that was reduced from 20 components to a single part.
- Speed: Boeing used additive manufacturing to produce a bracket for its 787 Dreamliner that reduced the “buy-to-fly” ratio by 85%.
- Sustainability: All of these examples are sustainable. The additive process is inherently more sustainable than tooling or other traditional methods because it generates less waste. Learn more about applying additive manufacturing to reduce CO2e.
- Weight: High-end sports car company Divergent produces its ultra-lightweight chassis using additive and aims to design all car parts using 3D technologies.
Find the Additive Manufacturing Breakeven Point with aPriori
Manufacturers use aPriori to gain precise cost insights by analyzing the 3D CAD design, production volume, materials, manufacturing process, production quantity, and production considerations (based on either specific factory specifications or regional, fully burdened production costs).
aPriori’s precise insights enable users to simulate design and production variables such as 3D CAD design (including tolerances and layer thicknesses), material cost trade-offs, primary and secondary machining options, and nesting to reduce waste. Users can compare their design changes against aPriori’s default settings based on project parameters, or multiple design and manufacturing process iterations.
Steps to Comparing Additive vs. Traditional Manufacturing Options
When is it cost-effective to use additive manufacturing? Here’s how aPriori enables users to determine the cost options for producing a bracket in additive (DMLS) vs. traditional (sand casting). For this example, we compare the cost to produce 30 brackets via each process. And we identify the cost crossover point for the two manufacturing options.
1. Open the 3D CAD model in aP Pro, then select production volume, material selection, and additive manufacturing process.
Use aP Pro to set parameters for the : (1) manufacturing process group, (2) material selection, and (3) production volume. Users can further refine their manufacturing specifications and identify cost drivers using additional features during this step.
2. Adjust default settings, such as layer thickness, to address specific product requirements. Increasing 3D printing layer thickness reduces the number of passes required to manufacture a part. This modification can reduce cycle time significantly without impacting performance. For this example, we reduced cycle time by nearly one-third by doubling layer thickness.
This comparison also requires product developers to address the design support structure (highlighted in pink below). In this case, we edited the design support structure default setting to exclude it from the cost model. This change alerts cost engineers that they do not need to conduct a cost analysis on this element of the design and manufacturing process.
Finally, nesting is the last process component to check. aPriori nests 3D printed parts based on the selected machine’s bed size to minimize the number of printing runs. For traditional manufacturing, aPriori’s nesting minimizes waste and optimizes machining utilization.
3. Compare manufacturing processes to see the number of units that can be produced profitably via 3D printing compared to sand casting. aPriori analysis determined:
- It is 33% less expensive to produce 30 units via additive manufacturing
- The breakeven point is 60 units (see the following cost analysis report)
Benefits for OEMs, Suppliers & Contract Manufacturers
The ability to identify when it’s advantageous to use additive manufacturing provides companies with added flexibility to contain costs, forecast effectively, and respond quickly to changing market needs. Large product manufacturing OEMs can typically adopt more manufacturing processes – including additive – due to their size advantage over some suppliers.
There are also business cases for contract manufacturers (CMs), machine shops, and other companies to incorporate additive technologies into their services. Specifically, additive allows CMs and other suppliers to begin working on projects during the design stage. As noted, product development teams refining their designs are more likely to use additive manufacturing during this phase. So, a supplier with both additive and traditional manufacturing offerings can use 3D printing to work with clients on the design and prototyping. Once product specifications are finalized, the supplier can use conventional manufacturing for machining, tooling, post-processing, etc. to scale production rapidly.
Additionally, with aPriori, manufacturers can conduct extensive break-even analysis to understand the profitability of production runs via additive machines and other options. To build on this point, Modern Machine Shop outlined how machine shops can use polymer 3D printing to increase economic efficiency (profitability) across all machines. A CM could use 3D printing for various jobs and free up CNC machine tools for higher-margin work as needed.
Apply Insights for Growth
Margin pressure, supply chain instability, a lack of skilled workers, and sustainability requirements are just some of the challenges facing manufacturers today. Businesses that can optimize their product designs and manufacturing processes – and shift rapidly to address market needs – are well-positioned for growth.
Innovative companies across the globe use aPriori to make manufacturing decisions quickly and confidently. And aPriori’s visibility helps to ensure that they are capitalizing on their resources – including additive manufacturing – to increase speed and profitability.
Find the Additive Manufacturing Breakeven Point with aPriori
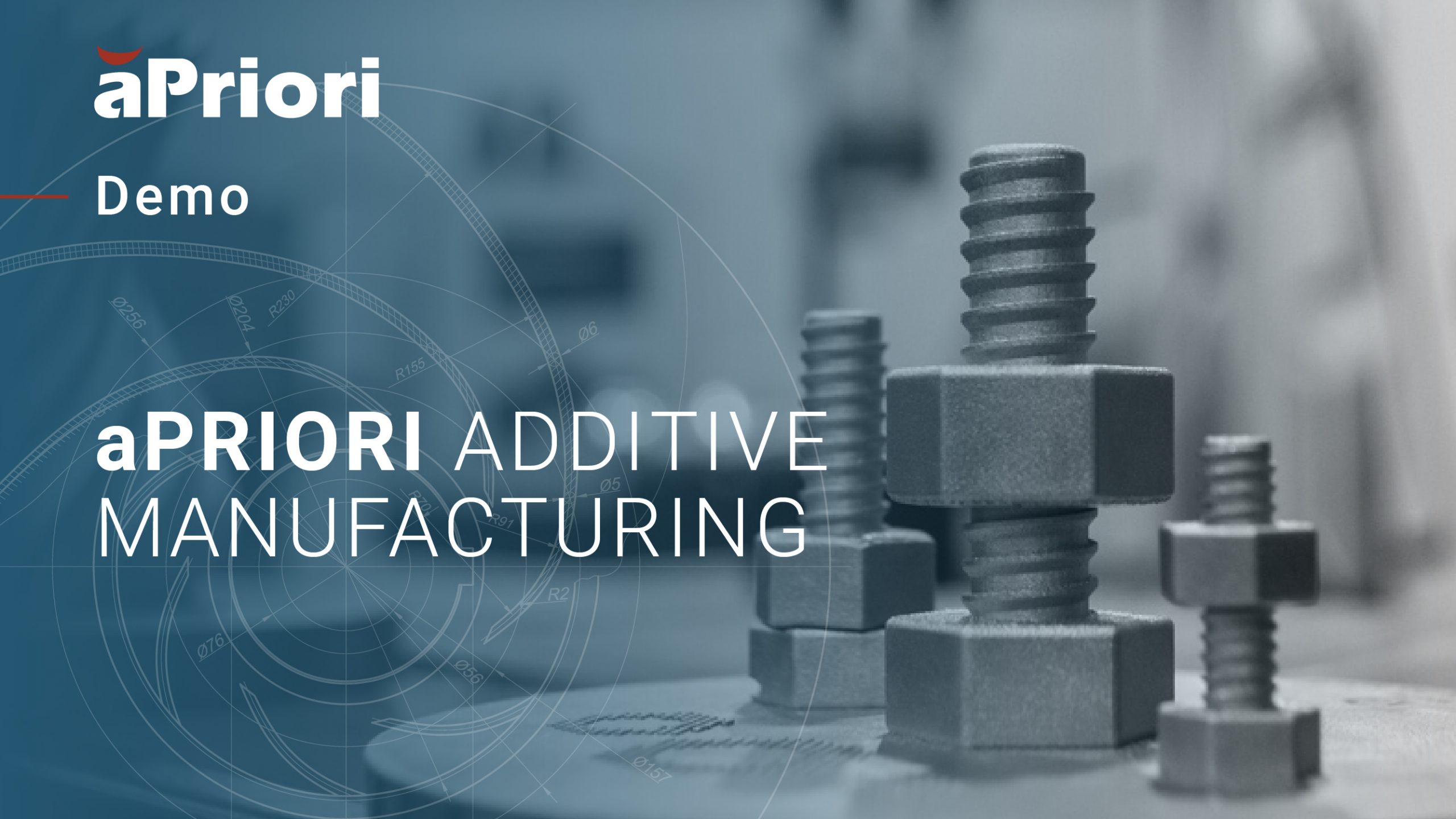