How ‘Shift Left’ Accelerates Time to Market for Advanced Manufacturing
Key Takeaways:
- Product delays can significantly reduce profits, with some setbacks cutting anticipated revenues by 50%
- Shift-left strategies use Agile methodologies and AI-driven solutions to address cost and risk early in hardware product development
The Full Article:
Even short product delays can have a long-term impact on revenues and cash flow. The Journal of Management Science estimates that a consumer product launch setback by nine-to-12 months can cut the product’s anticipated revenues by 50%.
And PwC reports that postponing a new car release in North America by one year can cost the automotive brand (OEM) up to $200 million and key suppliers up to $15 million each. That’s because product delays typically shorten the product’s growth stage, which generates the highest profit margins and annual cash flow.
To move faster, manufacturers are looking beyond linear phase-gate (waterfall) product design methodologies and adopting iterative models such as Agile and holistic product design. These methodologies are designed to address cost, performance, and other potential issues earlier in the product hardware development process. (Read more about Agile and holistic product design methodologies.)
In short, manufacturers are “shifting left.” Learn more about the keys to a successful shift-left strategy in the following sections:
- Common challenges with a phase-gate development process
- Keys to adopting a shift-left strategy
- Apply shift-left to hardware product development
- Use digital twins and AI to shift left
- Take firm steps to accelerate time to market
1. Common Challenges with a Phase-Gate Development Process
Figure 1 illustrates where new product development (NPD) projects typically miss their cost, carbon, and launch targets. The black cost curve often increases during the later stages of development when cost/value engineering, procurement, and manufacturing engineering experts engage in the process. And that’s when a project receives a more detailed review of actual costs and design for manufacturability (DFM) risks.
For example, procurement may identify a significant material cost increase or supply chain risk that designers were unaware of during the early design phase. Similarly, pilot production may uncover quality issues or assembly challenges to address.
Figure 1: Manufacturers often miss cost and target launch dates due to late-stage problems
2. Keys to Adopting a Shift-Left Strategy
Because up to 80% of a product’s cost and carbon footprint is set during early-stage design, manufacturers benefit from identifying potential issues earlier in the development process.
Taking a page from the software development playbook, hardware product manufacturers are using Agile and other methodologies to break down project phases into smaller “sprints.” These shift-left models tend to establish cross-functional teams to examine cost, DFM, sustainability, and other potential risks holistically.
A robust shift-left model provides teams with solutions and workflows to work quickly and confidently – including collaboration and automation.
Collaboration is Key
A successful shift-left model provides cross-functional teams with accurate data across the product development lifecycle to work effectively. But according to the Advanced Manufacturing Report by Hexagon and Forrester, 97% of manufacturers surveyed face collaboration and employee productivity challenges.
Companies can use digital twin and digital thread technology to connect teams, data, and enable collaboration. For example, using collaboration applications such as aPriori’s aP Workspace, cross-functional teams can use automated insights to identify problems in real time and streamline their workflows. aPriori’s interactive workspace also enables teams to comment on design updates while maintaining traceability and design history.
Remove Bottlenecks to Accelerate Design and Costing
The shift-left methodology, coupled with automated insights, can also help eliminate workflow and process inefficiencies.
Traditionally, the largest bottleneck is between design engineering and cost engineering. Relying on one department, cost engineering, to capture cost savings isn’t optimal or scalable – especially when manufacturers have a 25:1 ratio of designers to cost engineers (or more).
Figure 2: Apply an Agile, holistic design methodology to remove bottlenecks between designers and cost engineering
Because cost engineers are flooded with requests from product design, they don’t have time to tackle the major cost drivers dragging down profits. To address this bottleneck, product designers are using automated insight to address some cost issues on their own. This approach frees cost engineers to focus on bigger, more strategic cost issues. Using this model, cost engineers can adopt a “trusted advisor” role across the entire product development lifecycle.
3. Applying Shift-left to Hardware Product Development
Manufacturers are increasingly establishing small teams to iterate quickly. In figure 3, the core working teams image on the left includes design, cost, sourcing, and manufacturing professionals.
These teams have the cross-functional expertise and the tools to make decisions rapidly via collaboration, automation/artificial intelligence (AI) solutions, and quick feedback loops to accelerate workflows.
On the right, you see how these teams share information quickly with other key contributors and stakeholders. Using this workflow, key contributors spend less time iterating because the core working team has already addressed some key issues.
Figure 3: Shift left examples for hardware product development
Shift-left Benefits for Product Design Stakeholders
Let’s examine team roles in a shift-left model:
- Design engineers want to focus on form, fit, and function. But failure to address cost and other issues at this stage often requires time-consuming design updates later during product development. That’s why this group is beginning to use AI and automation to identify cost, carbon, and DFM issues in real time. The result: a net time savings because validated product designs don’t require rework for cost or other risks.
- With design engineers addressing some early-stage issues, cost engineers have more time to focus on significant cost outliers and assume more of a consulting role across the product development process. This provides manufacturers with more flexibility to address critical issues as they arise.
- Earlier visibility into design requirements allows sourcing and procurement teams to select new suppliers strategically – and address supply chain risks associated with the product’s bill of materials (BOM). More time also affords greater opportunities to negotiate with the right suppliers in regions that meet target cost and risk requirements.
- Sustainability teams work with other stakeholders to reduce cost and carbon emissions through material selection, production processes, and factory location. Cost and carbon are increasingly linked as manufacturers work to achieve their sustainability goals and navigate carbon reduction initiatives such as the European Union’s “carbon tax.” (Learn how manufacturers are addressing the EU’s CBAM.)
- Manufacturing engineers can apply early design specifications, production volume goals, and other information to improve planning. This includes determining how to machine and nest parts optimally and simulate cycle times for capacity planning. Manufacturing and sourcing teams can use this data to evaluate “make vs. buy” options and other considerations
4. Use Digital Twins and AI to Shift Left
Manufacturers can apply their digitalization capabilities to shift left via digital twins and the digital thread. Using digitalization to remove data silos, cross-functional teams can collaborate around a single set of accurate, up-to-date 3D CAD design files and associated product specifications.
Companies are also using the digital thread to connect multiple digital twins across the product development lifecycle to access and centralize a robust set of data. And with digital twins, companies can simultaneously simulate the product design, manufacturing process, and factory specifications down to the machine level. (Discover how the digital thread ties design, sourcing, and manufacturing together.)
To manage large volumes of data, companies are using co-pilot guidance and automated insights to make decisions quickly and effectively.
aPriori’s AI-Powered Design & Sourcing Insights empower manufacturers to improve product profitability, manufacturability, sustainability, and time to market. aPriori’s intelligence enables users to simulate multiple variables simultaneously to make data-driven decisions amid increasing design, supply chain, and manufacturing complexity.
Product designers can use AI insights to automatically pinpoint opportunities to address cost, sustainability, and DFM. Sourcing teams can apply aPriori’s AI-powered insights to assess material choices, factory options by supplier or geography to identify the most cost-effective options, and more. What used to take weeks or months can now be completed in seconds with aPriori’s AI technology.
Importantly, automated insights and collaboration also help to curb the need for additional staff, which is critical because there’s a shortage of qualified design and manufacturing experts available to fill open positions.
5. Take Firm Steps to Accelerate Time to Market
Adopting a shift-left strategy is essential to accelerate design to manufacture. By involving cross-functional teams early in the design process, manufacturers are poised to reduce costly redesigns and delays.
Digital transformation solutions and AI tools like aPriori foster quick, confident decision-making. These automated technologies streamline workflows and enable manufacturers to identify and resolve a range of costly and time-consuming risks during the earliest stages of development.
Companies that combine collaboration with automated insights are well-positioned to succeed in the increasingly complex manufacturing ecosystem.
Are product delays and costs mounting?
Get practical tips to remove design bottlenecks with confidence – and fast-track time to market.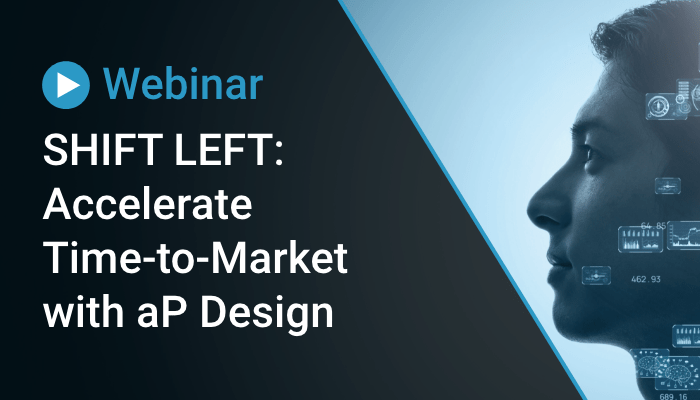