Design Engineers: What You Don’t Know About Simulation Software Can Hurt You
Key Takeaways:
- Design Engineering is a highly time-sensitive, pressure-filled balancing act to meet a range of KPIs and ensure a performant but profitable design. Since time to market is critical, simulation ensures that the balance is achieved the first time.
- Simulation software streamlines the process, reducing iterations, ECOs, material waste and cycle times, and carbon emissions, and improves time to market, manufacturability, profitability, and sustainability
The Full Article:
“Form follows function.” This expression was coined by architect Louis Sullivan, the father of skyscrapers. It is a design principle built on the premise that the shape of a building or object should primarily relate to its intended function or purpose.
However, today’s design cannot be reduced to this expression. It must now factor in an increasingly disruptive landscape. Doing more with less is a common refrain in a highly competitive marketplace. Design engineers (and the executives who drive digital technology adoption) can no longer focus solely on form and function. They must ensure product performance in an increasingly competitive marketplace where doing more with less is the common refrain. Additionally, they must take into account manufacturability, profitability (for which executives must answer to stakeholders), product performance, and, more recently, an additional pressure, sustainability. Nevertheless, a significant number of manufacturing executives have not incorporated manufacturing simulation into their organizations.
And if you don’t think design impact has a ripple effect, consider these statistics:
What You Don’t Know About Simulation Software Can Hurt You…and Your Organization
It is not uncommon for professionals to worry about their job security when a new technology is considered. Will it replace them? Will they lack the technical expertise to use it? Will the implementation process be arduous? All reasonable questions.
When the term “simulation” is used in engineering, most will look to technologies like finite element analysis (FEA) and computational fluid dynamics (CFD), which focus on the product’s performance by virtually testing how it will work. However, a lesser-known simulation software is manufacturing simulation, which evaluates and optimizes the manufacturing process virtually.
Manufacturing simulation provides myriad product development advantages. The most obvious is that teams can leverage digital twins, such as digital processes and digital factories, to determine the feasibility and manufacturability of a product, part, or component before going into production.
Unlike FEA or CFD, which can take hours and require technical expertise to interpret the results, manufacturing simulation can validate both feasibility and manufacturability from a cost perspective in mere seconds and does not rely on experts to deduce the results. Then time and effort can be used to fine-tune performance. As a result, raw material and production process costs can be reduced and time to market accelerated.
Regardless of the simulation software, the benefits are the same, but manufacturing simulation will evaluate cost, manufacturability, and sustainability, as opposed to considering factors of safety or maximum stress.
Yes, implementing them takes time and resources, and there is a learning curve with some technologies. But the benefits far outweigh any temporary inconveniences.
McKinsey confirms that successful digital transformations yield exceptional returns. Across many manufacturing sectors, it is common to see 10 to 30% increases in throughput, a 15 to 30% improvement in labor productivity, and an 85% increase in more accurate forecasting.
They also facilitate more value-driven product development. Additionally, digital technologies like simulation software:
- Allow design engineers to “test drive” a product design before moving it to the next development stage, reducing iterations, late-stage ECOs, and overall costs and carbon
- Streamline processes across all product development stages
- Mitigate bottlenecks and other disruptions such as the supply chain, accelerating time to market
- Identify cost-saving opportunities and validate the true cost of a product
- Optimize product design faster, affording more time to further innovate
- Lower design to manufacturing cycle times, saving time and reducing CO2e
What’s more, understanding and leveraging simulation software strengthens your risk management and builds greater resilience in the organization overall.
How aPriori’s Simulation Software Can Help Your Design…and the Product Development Lifecycle
In the past, leveraging simulation software was left to technical experts. Today’s best simulation software is easy to use, intuitive, and provides data-driven results.
Simulation modeling allows design engineers to run real-world scenarios in a virtual, reduced-risk environment.
Since design engineers are the pivotal point of product development, it is essential that they use simulation tools to ensure optimal designs. For instance, design engineers can run aPriori’s AI-powered design and sourcing insights through their 3D CAD. They will receive crucial manufacturability and cost feedback. Additionally, aPriori provides recommendations for alternative, more cost-effective, and manufacturable materials and processes to ensure manufacturability, cost, and sustainability goals are met – all before the design even hits the factory floor.
A key component of aPriori’s simulation software is the digital twins. Each digital twin (product, process, and digital factory) is a virtual representation of a physical asset or process used to analyze and optimize product designs, manufacturing processes, factory efficiency, and other operations. The digital thread ties together multiple digital twins and data from related digitalization applications. It connects the digital twin and product information, including sourcing, manufacturing, and field service data. More informed, quality-driven decisions can be made faster, and more cost-effectively and sustainably.
Moreover, aPriori’s simulation software improves workflows and enhances collaboration across all product development teams, removing siloes and bottlenecks, and reducing costly delays.
Although it is imperative that the design engineer leverage manufacturing simulation software to optimize product development, it is equally critical that design executives ensure that the design team has access to these capabilities. Forgo them and you could find yourself at a competitive disadvantage.
Simulation Software Allows Design Engineers To Push The “What-If” Limits
No longer can design engineers or senior executives assume that spreadsheets and drawings are enough. Relying solely on a 3D CAD model will not suffice. What’s more, simulation software in manufacturing enables design engineers to level up their skills by allowing them to push the boundaries of design and consider more innovative methods of using materials and processes.
However, most are not aware that AI-powered design insights can help achieve the above.
Although it is imperative that the design engineer leverage manufacturing simulation software to optimize product development, it is equally critical that design executives ensure that the design team has access to these capabilities. Forgo them and you could find yourself at a competitive disadvantage.
It is the only viable route to remaining a competitive force in the manufacturing landscape. Because it offers a big-picture perspective that design engineers were not required to have in the past. Product design and process simulation results in a granular understanding of how each product development phase, material, and process is interconnected. It places a spotlight on system or production constraints, required resources, and what-if scenarios before going into physical production, all of which are vital to a timely, cost-effective, value-driven product launch.
Your Most Costly Mistakes Will Likely Occur In The Design Stage
Read our DFM guide to avoid costly mistakes that can impact profitability and slow time to market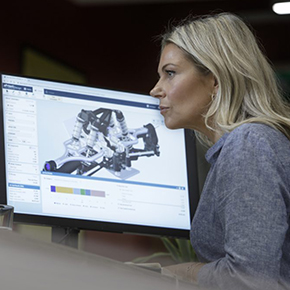