3 Ways to Combat Inflation With Manufacturing Costing Insights
Key Takeaways:
- Early identification of design issues reduces product development costs, helping curb inflation by bringing innovations to market more economically and quickly
- Utilize manufacturing insights software to identify cost-saving opportunities, optimize production processes, and combat inflationary pressures
The Full Article:
The adage “time is money” has never been more relevant, especially given the persistent inflationary challenges facing manufacturers. To help manufacturers navigate cost increases, we will examine the inefficiencies and challenges that organizations are currently facing. We will also provide insights into effective manufacturing cost analysis and outline strategies to navigate inflationary expenses and maximize profit margins.
How Does Inflation Affect Manufacturing Decisions?
The decisions made during the early stages of product design have a significant impact on the total manufacturing cost of finished products. In fact, they account for about 80% of the overall expenses of a final product. This not only affects direct costs but also creates a ripple effect that leads to other costly issues, including:
- Shortages and increased demand for raw and direct materials can lead to rising costs, which can challenge manufacturers’ breakeven points.
- Delays, shortages, and higher costs can easily compromise conversion (the cost of turning a material into a part) and routing (the path followed in each stage of the production process).
- Supply chain and direct labor shortages can lead to slower times to market (TTM).
- Supply storage upcharges can occur due to offshore container ship delays and longer storage cycles resulting from supply chain disruptions.
- Higher fuel prices can be passed on to manufacturers on both the receiving and delivery ends.
- Missing product launch dates result in losing shelf space to competitors, pushing the need for faster production at increased costs with reduced profit margins.
Fortunately, an automated manufacturing insights platform can alleviate most, if not all, of the ways that inflation affects manufacturing.
Why Are Manufacturing Insights Crucial for Manufacturing Costing Processes?
Manufacturers are increasingly using manufacturing insights technology to mitigate part and component costs. According to Deloitte’s “2024 Manufacturing Industry Outlook” report, more than 76% of manufacturing businesses have adopted digital tools. This adoption enables manufacturers to lower costs, enhance supply chain transparency, improve decision-making, and increase agility and resilience.
Many forward-thinking companies are adopting digital manufacturing insights to assess the cost, manufacturability, and sustainability impacts of real-time design choices. Automation-driven software like aPriori can analyze the 3D computer-aided design (CAD) model, which is the digital twin of the product. Once the CAD model is checked into a product lifecycle management (PLM) system, manufacturers can receive valuable and actionable feedback.
aPriori takes it a step further with its digital factories, which offer a digital representation of a physical manufacturing facility down to the machine level. These factories enable manufacturers to select preferred manufacturing regions based on labor costs, specific machines, materials, and methods for their digital factory, whether it be in-house or with a supplier. The software provides a 3D CAD geometric analysis of single parts in complex assemblies, enabling manufacturers to make cost-effective design decisions from the outset.
Moreover, aPriori generates recommendations to improve the manufacturability of the design through reporting and metrics. For instance, if a specific design feature is too complex to manufacture, design engineers can redesign or choose an alternative manufacturing method to reduce the complexity and cost early in product development. If there are any issues related to design for manufacturability (DFM) or tolerance, such as raw material substitution due to a semiconductor chip shortage, design engineers will be notified. Designers can also optimize designs to enable production in different factories.
To manage revisions or design changes, engineers use the digital thread to collaborate with sourcing and other teams, maintaining a single source of truth from the design file through production.
Learn how aPriori’s real-world regional data and process models tackle manufacturing overhead costs, production costs, and more.
3 Ways Product Manufacturers Can Combat Inflation
A Boston Consulting Group (BCG) report indicates that inflation continues to be a top concern for C-suite executives in 2024. However, manufacturing insights software, such as aPriori, can help alleviate inflationary concerns in the following three ways:
1) Accelerate TTM Outcomes
Manufacturers can bring their finished goods or products to market faster by identifying design flaws earlier in the product development process. This allows teams to be more proactive, helping them to develop, refine, and create parts more quickly. Moreover, the time saved can be used to iterate on new products and maintain competitiveness in the market.
2) Reduce Engineering Change Order (ECO) Delays
Manufacturing insights technology can help companies reduce iteration cycles and minimize expensive late-stage ECO requirements. For instance, a solution like aPriori can provide actionable feedback in the early design phase. This guidance enables design engineers to quickly redesign parts for maximum value and cost efficiency from the outset.
Moreover, if a supplier determines that a design cannot be manufactured from a request for quotation (RFQ), it can result in significant delays. This is particularly true if a required design iteration has a knock-on effect on other critical components. Consequently, manufacturing insights technology is crucial as it creates a link between effective designs and manufacturing feasibility.
3) Achieve Manufacturing Cost Targets
Manufacturing costing software is valuable in evaluating onshoring or reshoring decisions. By running various “what-if” scenarios, companies can gauge the real-time impact of several types of costs, including regional labor rates, material expenses, and manufacturing overhead (e.g., direct and indirect overhead costs, tool shop rates, etc.).
These insights are critical for identifying where a company is vulnerable to specific materials or regions, which can be useful when a product design relies on expensive or hard-to-find suppliers. Consequently, manufacturers can explore alternatives, such as sourcing from low-cost suppliers or redesigning parts to mitigate supply chain delays and expensive component utilization.
Moreover, a solution like aPriori provides granular reporting dashboards and ad-hoc analysis capabilities that are accessible to the entire product development team. With its out-of-the-box reports, aPriori can identify the materials most frequently used in designs and those more susceptible to price volatility.
Despite potentially higher labor costs associated with onshoring, these expenses could be negated or balanced by the rising costs of offshore operations. Additionally, the convenience of onshoring can further diminish risks, making it a critical strategy for manufacturing companies aiming to optimize their operations.
Key Benefits of Automated Manufacturing Costing Processes
Manufacturing insights software can help reduce inflationary manufacturing costs and drive the following results:
- Greater profitability through actionable manufacturing costing insights that uncover more opportunities for cost savings and bottom-line excellence.
- Improved agility to pivot as necessary, making decisions quickly and confidently to stay ahead of the competition and capture market share faster.
- Real-time collaboration and enhanced communication through shared visibility from the design team to production.
- Reduced design churn with suppliers and elimination of wasteful feasibility loops.
- Increased design productivity with an intuitive, easy-to-use platform.
- Effective management of cost, sustainability, and manufacturability initiatives before any time-consuming and costly downstream activities occur.
- Detailed design scenario comparisons enable teams to compare designs, materials, environmental impacts, and production and manufacturing costs. These detailed comparisons can be used to make informed trade-off decisions.
Counter Inflation While Achieving Your Profitability, Manufacturability, and Sustainability Goals
Automated manufacturing costing software, such as aPriori, can help design engineers and project stakeholders work faster and more efficiently. This manufacturing costing technology can identify cost-effective manufacturing processes and provide useful feedback on economical design and material options. aPriori also enables companies to make informed “make vs. buy” decisions, helping them determine if in-house production has lower manufacturing costs.
CNH Industrial, an agricultural equipment manufacturer, was able to identify $312,000 in annual savings within the first two months of implementing aPriori’s manufacturing costing technology. This highlights aPriori’s ability to uncover manufacturing cost-saving opportunities and increase cash flow, even during dynamic inflationary conditions.
By combining a manufacturing insights platform like aPriori with your team’s design expertise, you can effectively manage and achieve your cost, manufacturability, and sustainability goals. As a result, your innovative organization can produce high-value products, reduce TTM, and combat rising manufacturing costs with confidence.
This post was originally published on Sept. 6, 2022, and updated on May 14, 2024.
How to Glean Manufacturing Data from Your Digital Twins
Uncover how to optimize the data from your digital twin model into an immediate and long-term strategy.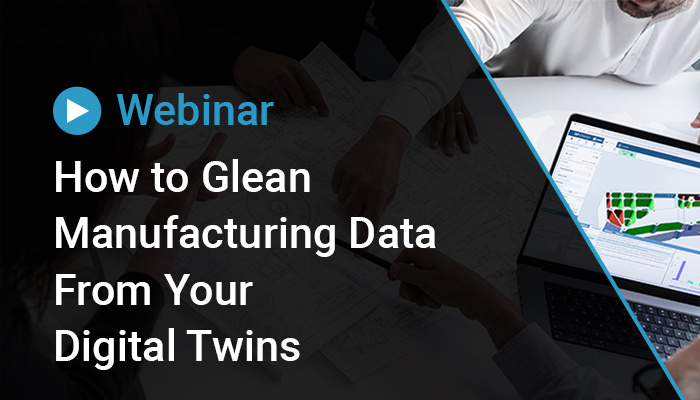