Skilled Manufacturing Labor Shortages? 5 Digital Twins Solutions
Key Takeaways:
- Leveraging digital twins can compensate for skilled manufacturing labor deficits
- Digital twins provide a fertile training ground for newer manufacturing personnel while mitigating other issues
Full Article:
A NAM Q4 2023 survey of small manufacturing companies with fewer than 50 employees and medium-sized firms with 50-499 employees found that more than 71.4% cited the inability to attract and retain employees as their primary challenge. Compounding the issue is a rapidly retiring baby boomer workforce, leaving large labor and critical skills gaps. And it’s not just a problem in North America. Geopolitical strategist and keynote speaker Peter Zeihan noted in an interview at aPriori’s 2023 Manufacturing Insights Conference (MIC) that Europe is only second to China with the fastest aging population.
What can be done to stem these manufacturing labor skills gaps? How can manufacturers develop more skilled personnel, while simultaneously doing more with less?
The key to replacing this experience lies in automation via digital twins. Connected by the digital thread, digital twins empower manufacturers to unlock critical information that can serve not only as a teaching tool but also compensate for skilled labor shortages in the short term. In the process, manufacturers can transform their businesses with greater agility, time to market, and profitability.
5 Opportunities to Compensate for Skilled Manufacturing Labor Shortages
Leveraging digital twins empowers manufacturers to shore up their skilled labor force and address critical product development issues. Let’s explore five opportunities:
- Support faster design engineering upskilling. In an ideal world, new design engineers would have the luxury of spending several weeks or months learning every facet of production to ensure the manufacturability of their designs. While it provides a valuable experience, it is no longer practical for most manufacturers. Perhaps their production facilities are not within proximity of the design engineer. Additionally, more time in the field means less time designing. Providing digital solutions that enable design insights early in the process helps newer design engineers build experience faster. These insights give them a clearer understanding of the production aspect of their design including sourcing, cost, and production implications. The result is a better product, more innovation, and reduced iterations and time-to-market delays.
- Streamline the cost process and build institutional knowledge. A recent Boston Consulting Group (BCG) survey found that 65% of global executives rated overall cost management as very important and were prioritizing it in the areas of supply chain and manufacturing with 52% prioritizing labor/non-labor overhead. Cost is at the core of product development. Traditionally, it has been executed by many people and with time-consuming, disparate spreadsheets. What’s more, the costing institutional knowledge that has accumulated over the years often leaves with the exiting skilled worker. Automation yields greater should cost accuracy and ensures that the entire product development team is working from a single data source as well as gaining crucial experience in each facet of product development to build their knowledge. Discover how Carrier automated costing and in the process, saved millions of dollars and onboarded its product development team in utilizing aPriori.
- Source more efficiently and profitably. Sourcing materials requires back-and-forth negotiations and time to identify the right suppliers at the right price. It typically is an acquired skill. Digital solutions help uncover such opportunities as well as foster stronger supplier relationships for greater efficiency, collaboration, and negotiation. Novice sourcing teams can use digital twins to get a deeper understanding of the product development lifecycle to have a clearer picture of what and how to source materials and components more efficiently and profitably.
- Reduce quoting time and streamline the RFQ process. Quoting is a laborious and time-consuming process; often managing myriad customers, designs, and components. Without an automated, streamlined quoting process, manufacturers are left to reinvent the wheel with each quote. Utilizing digital twins (namely digital factories) enables manufacturers to quickly simulate manufacturing in a digital factory configured to match its unique capabilities and cost structure. Greener quoting teams can easily customize simulation inputs to reflect specific customer product parameters, allowing cost models to be readily tailored for new RFQs and building a streamlined supplier quoting process. See how one aPriori customer’s overall win rate has improved from 15% to 68%.
- Automate to replace experienced manufacturing engineers in short supply. The pandemic highlighted how quickly labor shortages can impact business. Automating rudimentary, repetitive tasks relieves seasoned personnel to focus on more complex, technical jobs. With a mass exodus of retiring baby boomers, the need to automate becomes more critical. Moreover, the digital factory can replicate what is on the physical production floor, giving less experienced design engineers and other product development teams essential data to simulate the design, explore all factors such as toolings and routings, adjust where necessary, and correlate in the digital factory what they will see on the actual shop floor. Learn how one company used digital manufacturing simulation to standardize manufacturability and cost modeling.
Digital Twins’ Ability to Onboard Manufacturing Labor Faster
Digital solutions can onboard less experienced manufacturing personnel faster. For example, digital twins can be used in part estimation to help product development teams adjust parameters to align with how it will actually be manufactured. As a result, they learn and get answers from the solution. Consequently, they will begin to trust the solution throughout product development.
Regularly updating data (cost, sourcing, manufacturing processes, etc.) for timeliness and greater accuracy is also critical. Newer personnel attain more knowledge and experience faster, and all product development teams will have a standard, common data set from which to work. The result is faster upskilling, greater operational efficiency, minimized risk, and increased profits.
Are Labor Shortages Impeding Productivity?
Discover how Woodward leveraged digital technology to address the problem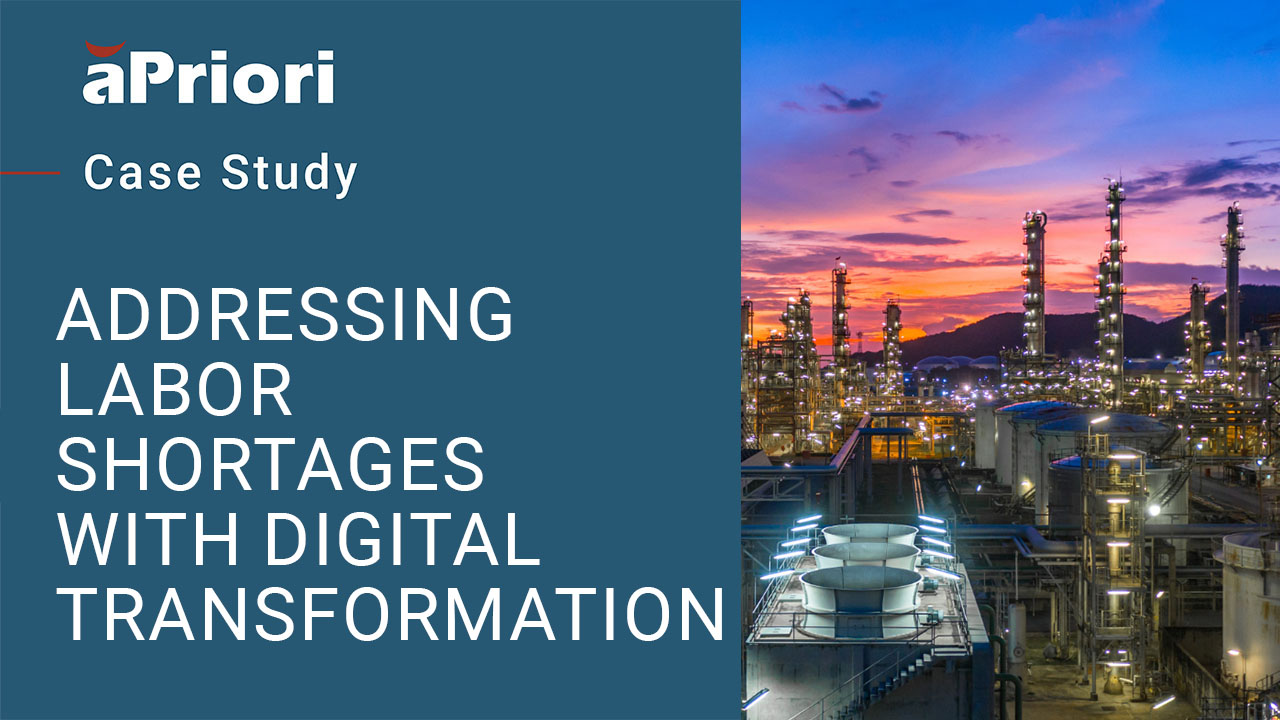