Resources
Resources Hub
To sort by type, role, industry, and/or products, use the filter navigation on the left.Filter by ()
Clear Filters
Featured Case Studies
Filtered Resources
Page 1 of 4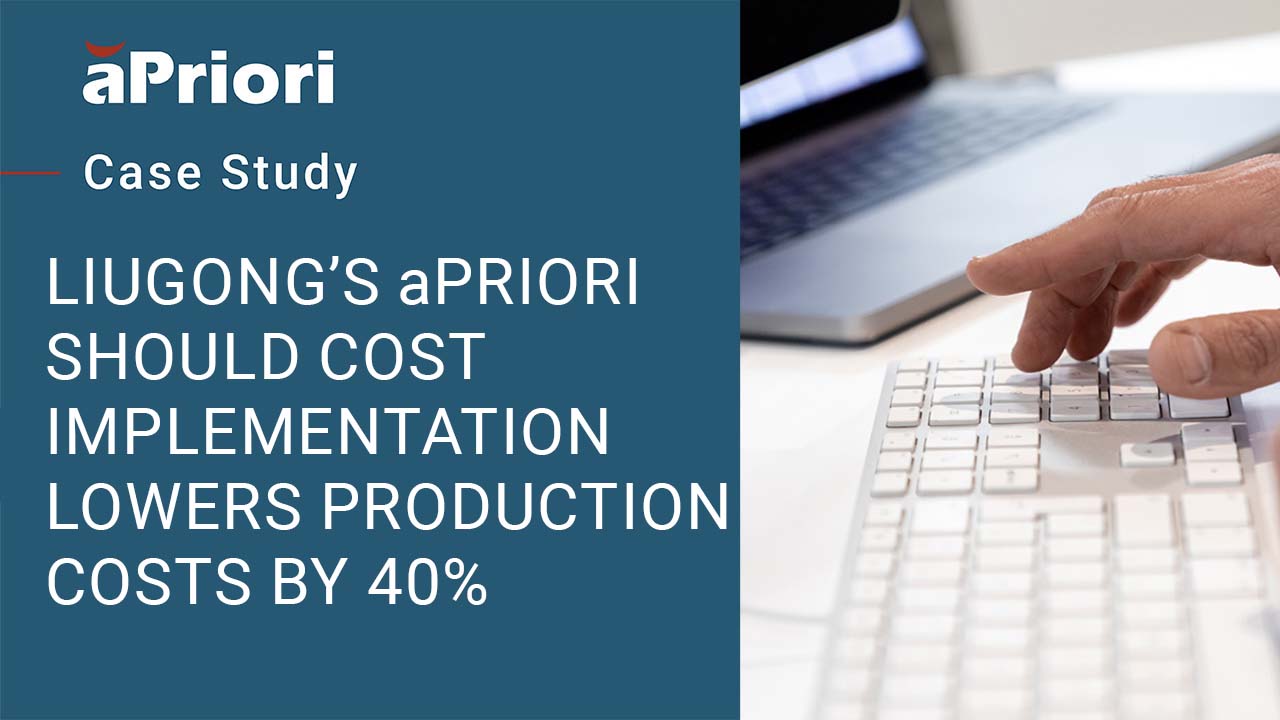
LiuGong’s aPriori Should Cost Implementation Lowers Production Costs by 40 Percent
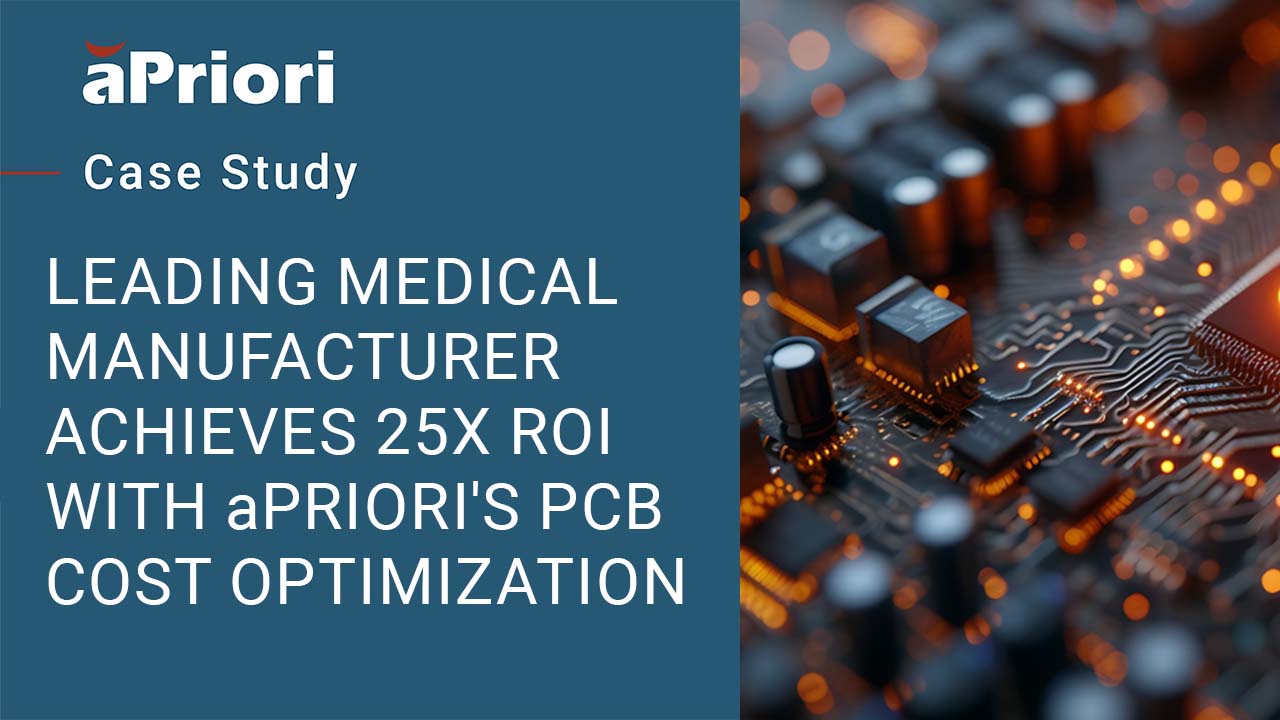
Leading Medical Manufacturer Achieves 25x ROI with aPriori’s PCB Cost Optimization
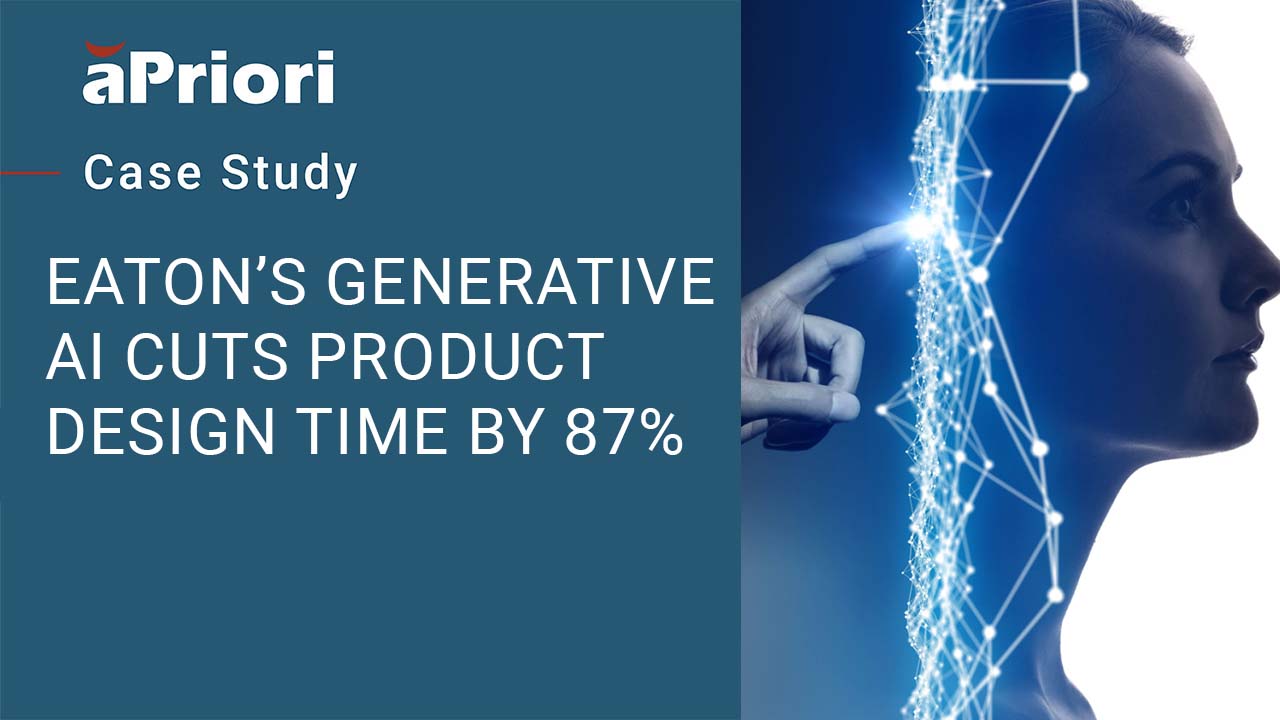
Eaton’s Generative AI Cuts Product Design Time by 87 Percent
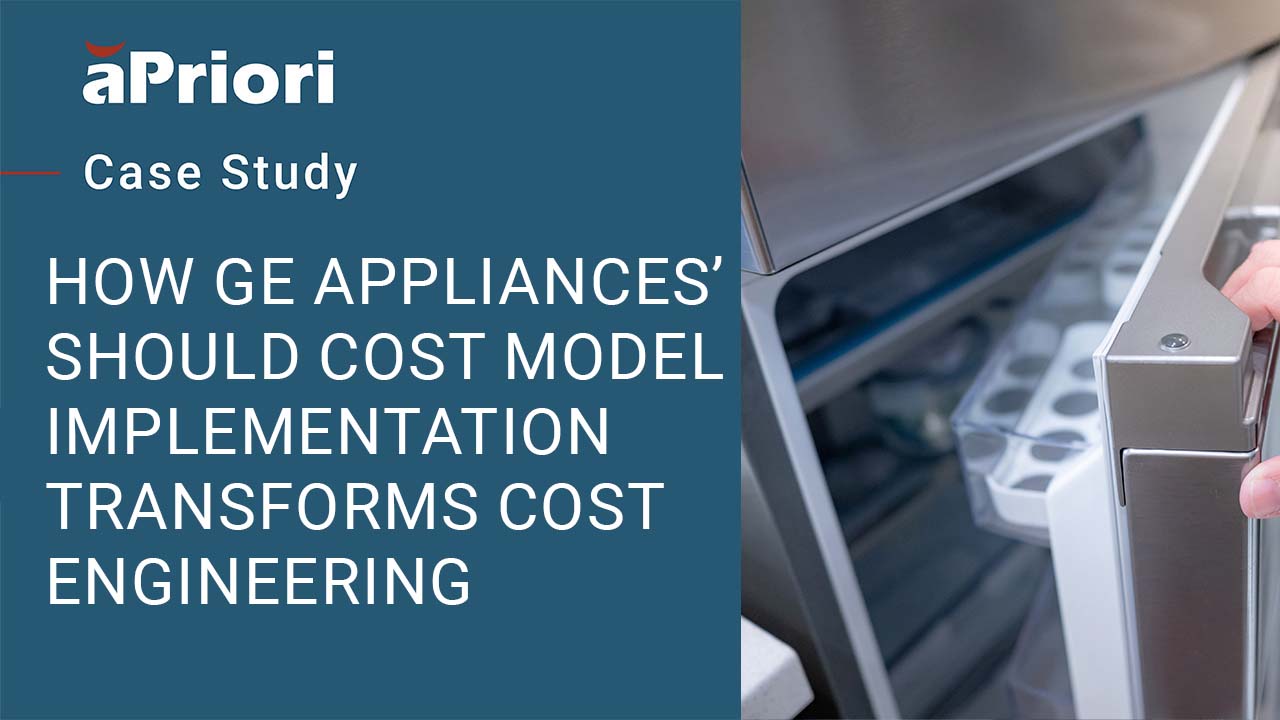
How GE Appliances’ Should Cost Model Implementation Transforms Cost Engineering
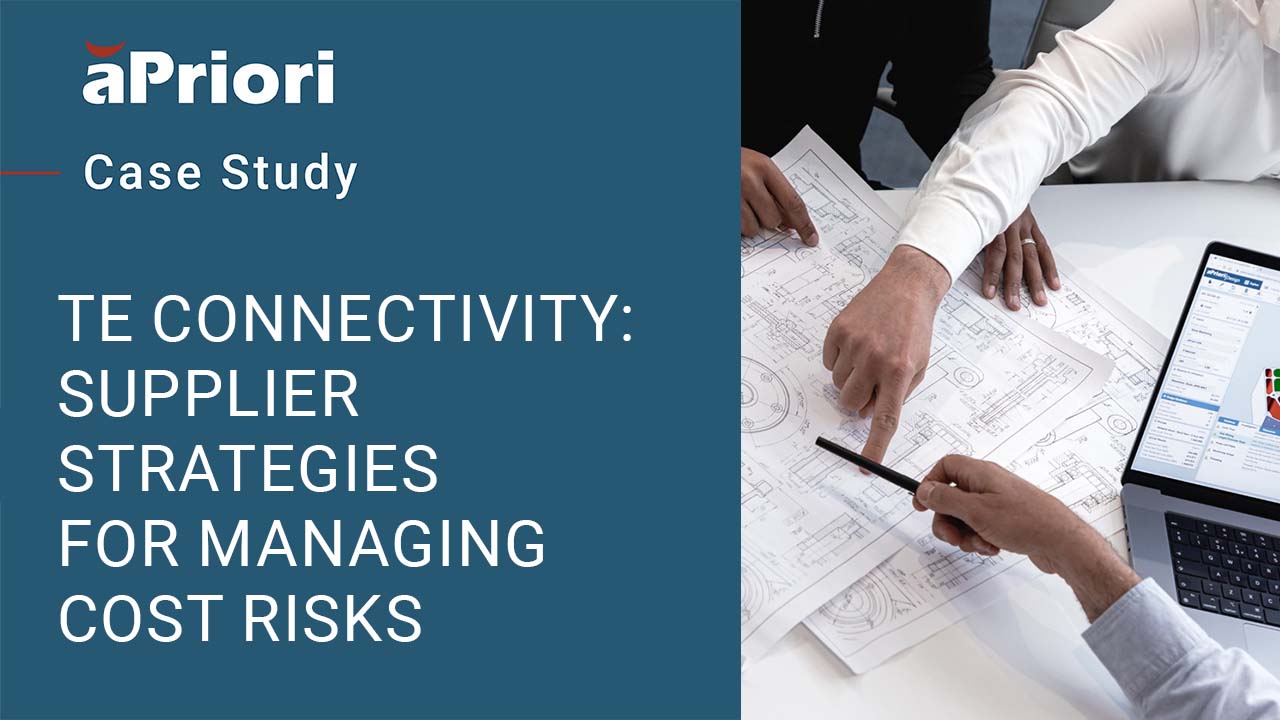
TE Connectivity: Supplier Strategies for Mitigating Risks and Fostering Collaboration
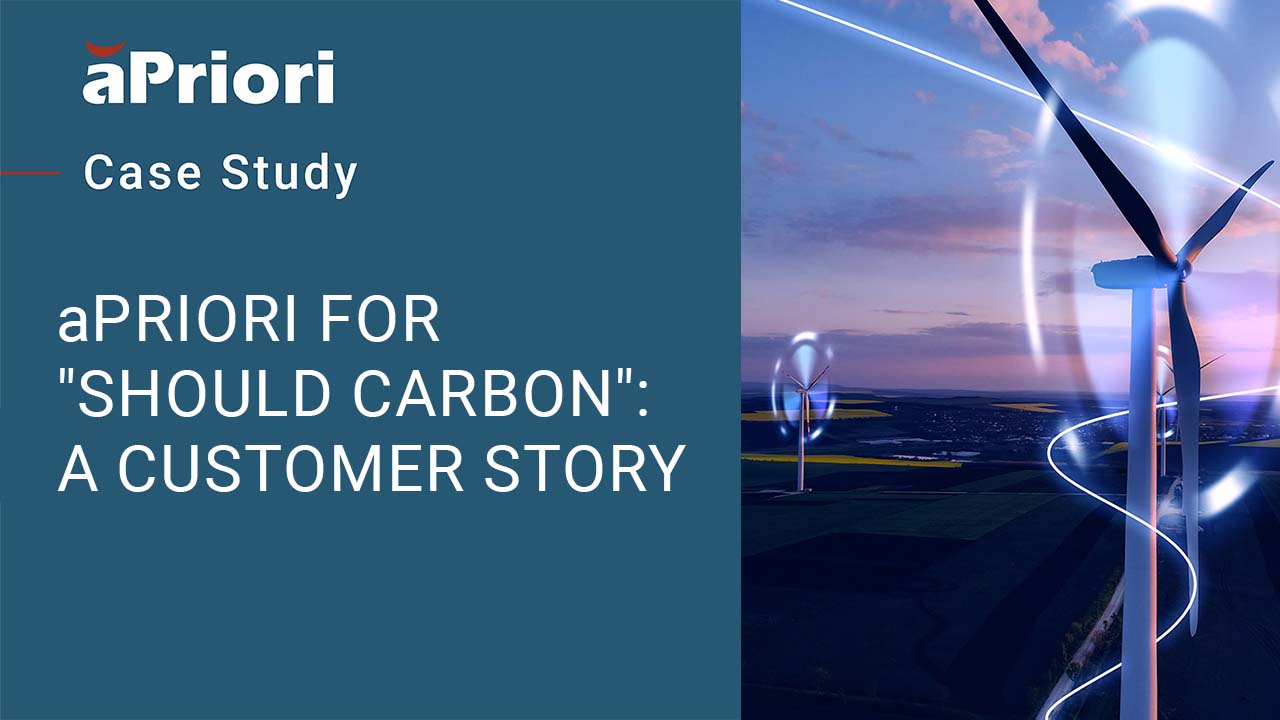
aPriori for Should Carbon: Fuel Cell Energy
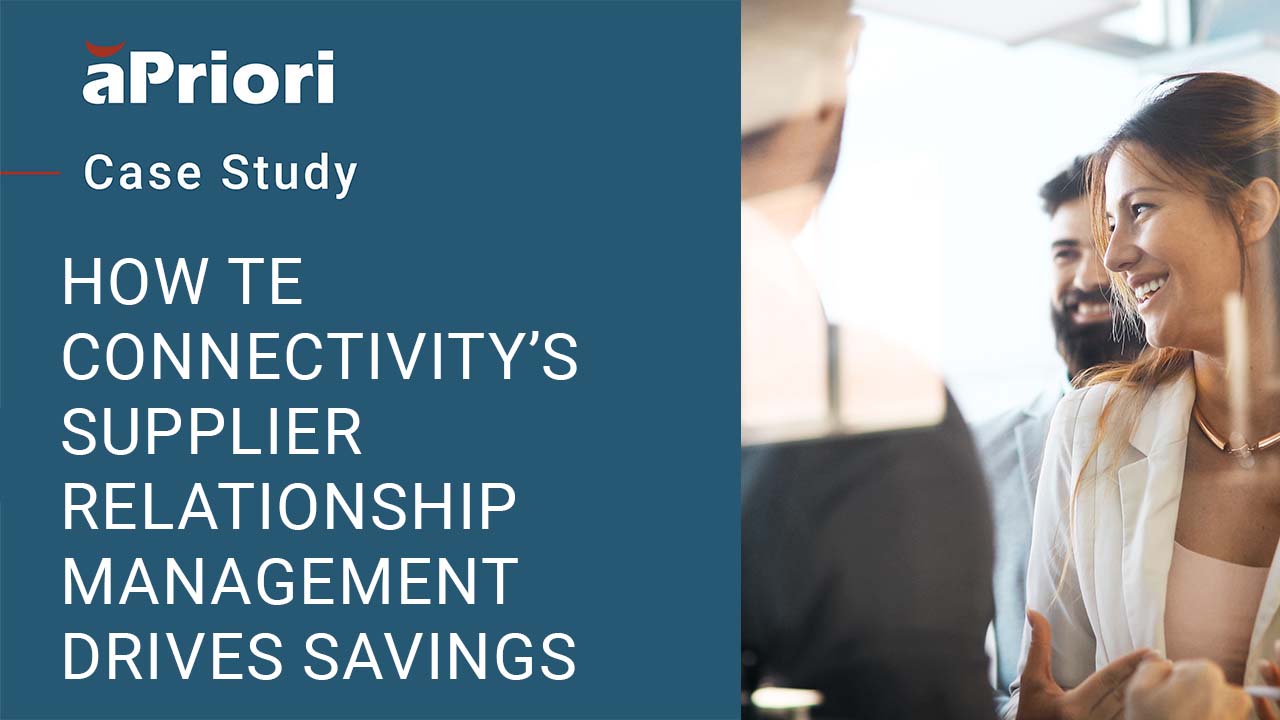
How TE Connectivity’s Supplier Relationship Management Drives Savings
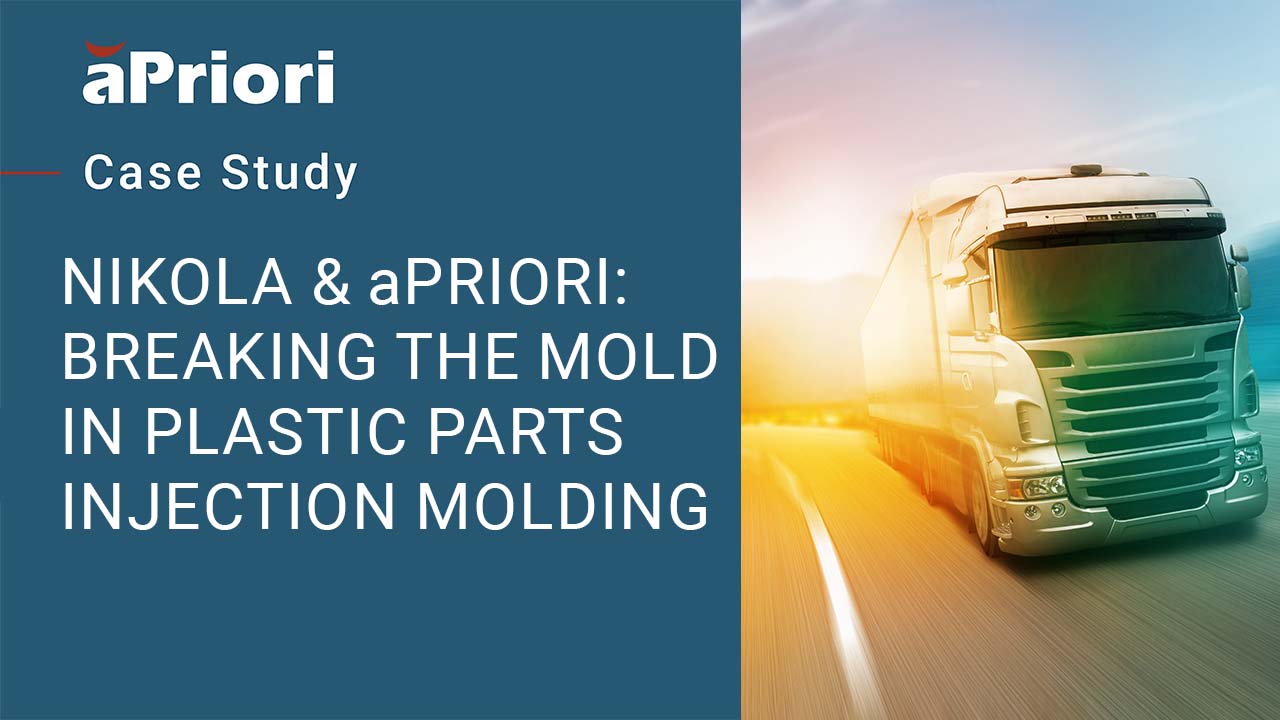
Nikola & aPriori: Breaking the Mold in Plastic Parts Injection Molding
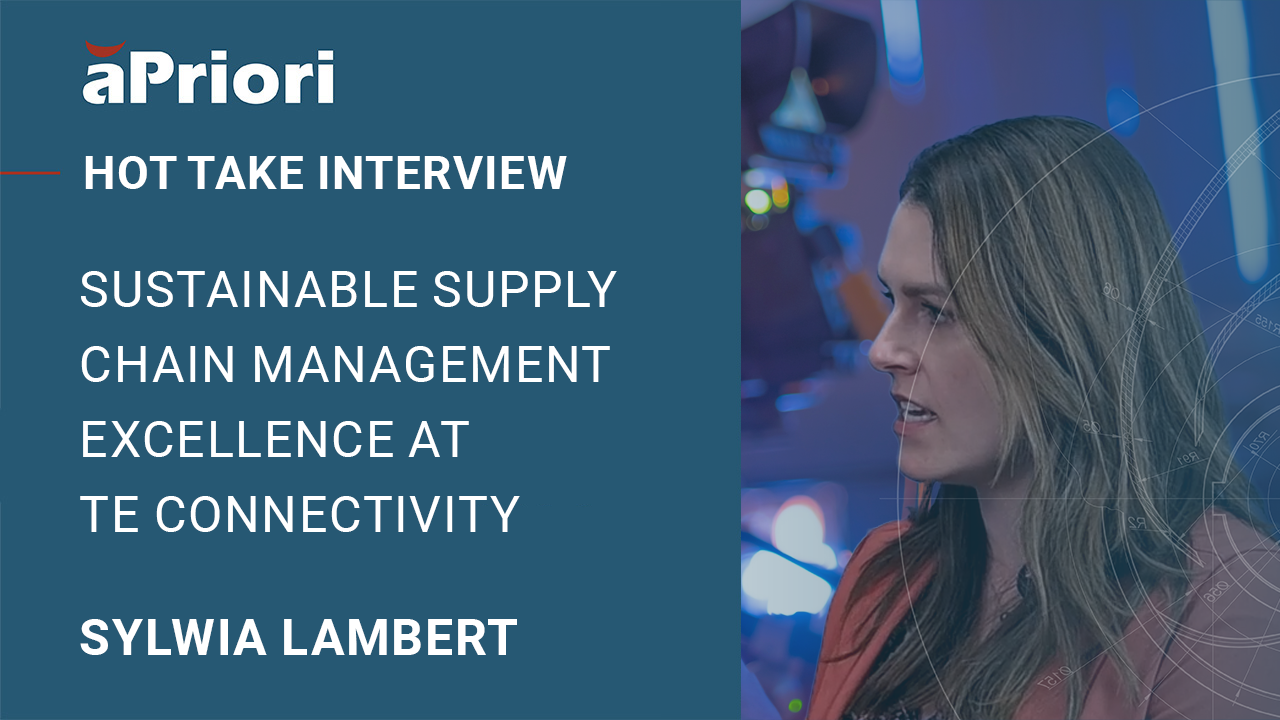
Sustainable Supply Chain Management Excellence at TE Connectivity
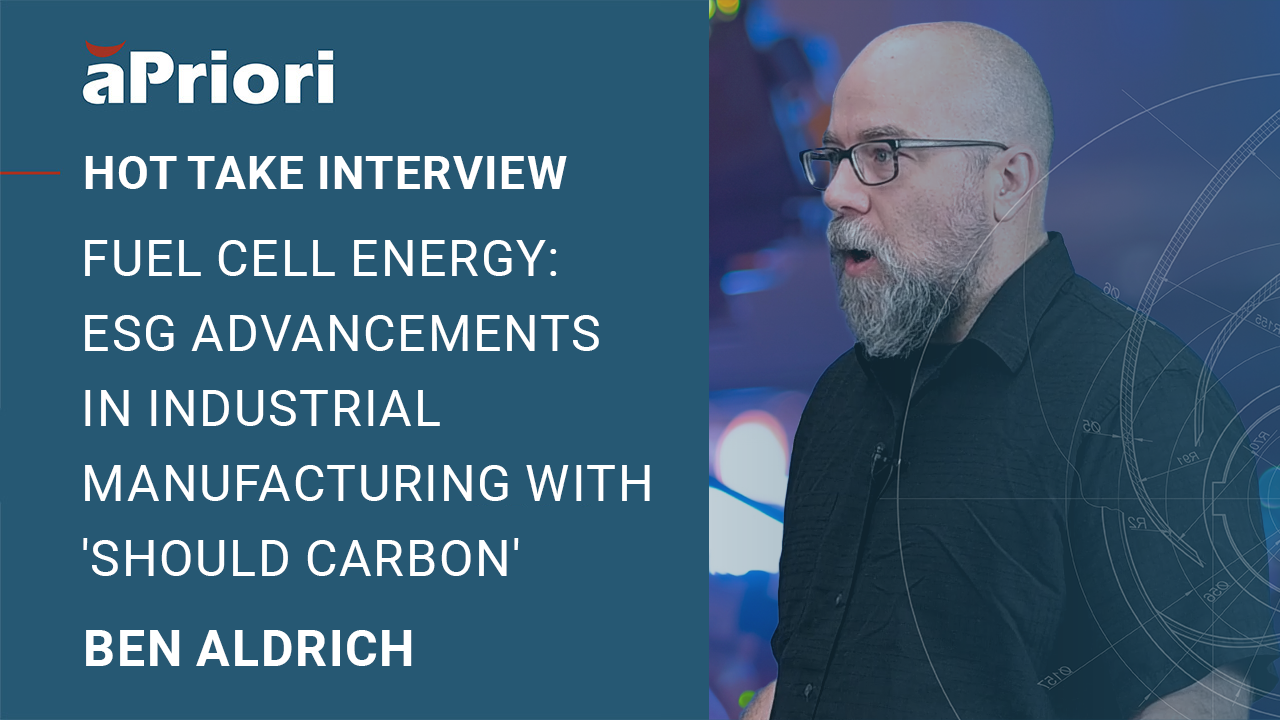
Fuel Cell Energy: ESG Advancements in Industrial Manufacturing with ‘Should Carbon’ and aPriori
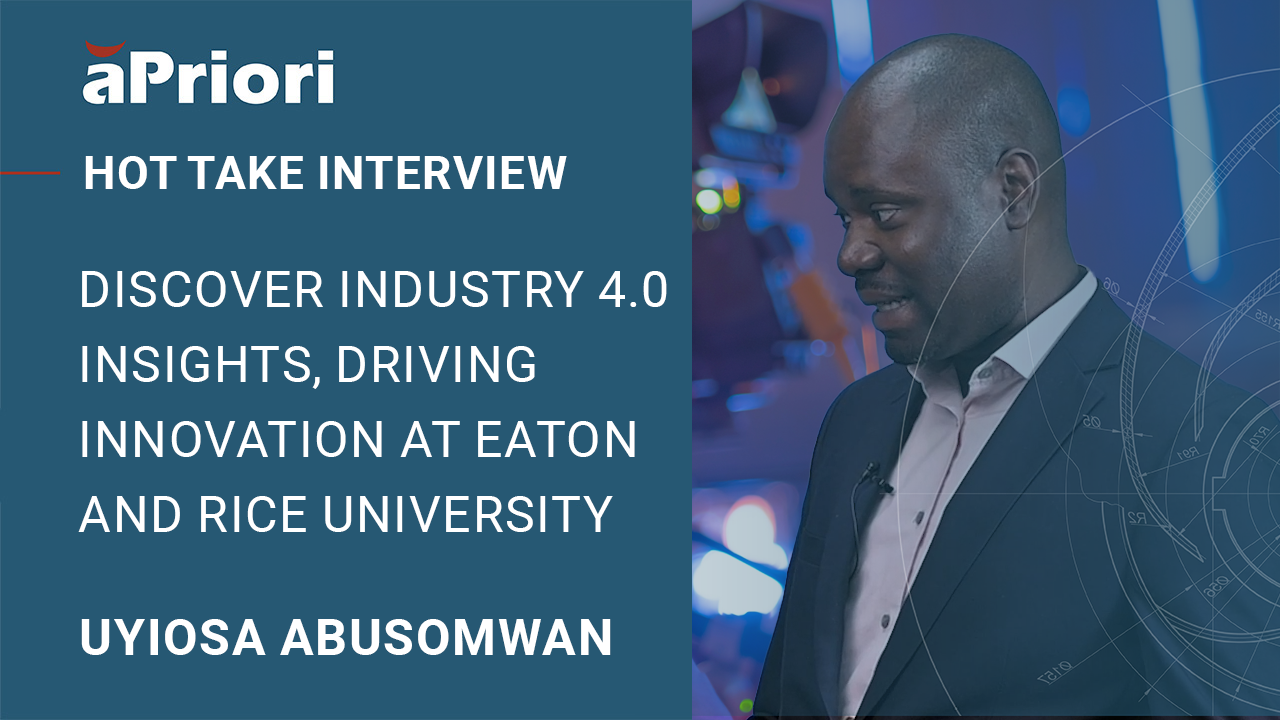
Industry 4.0 Insights: Driving Innovation at Eaton and Rice University with aPriori
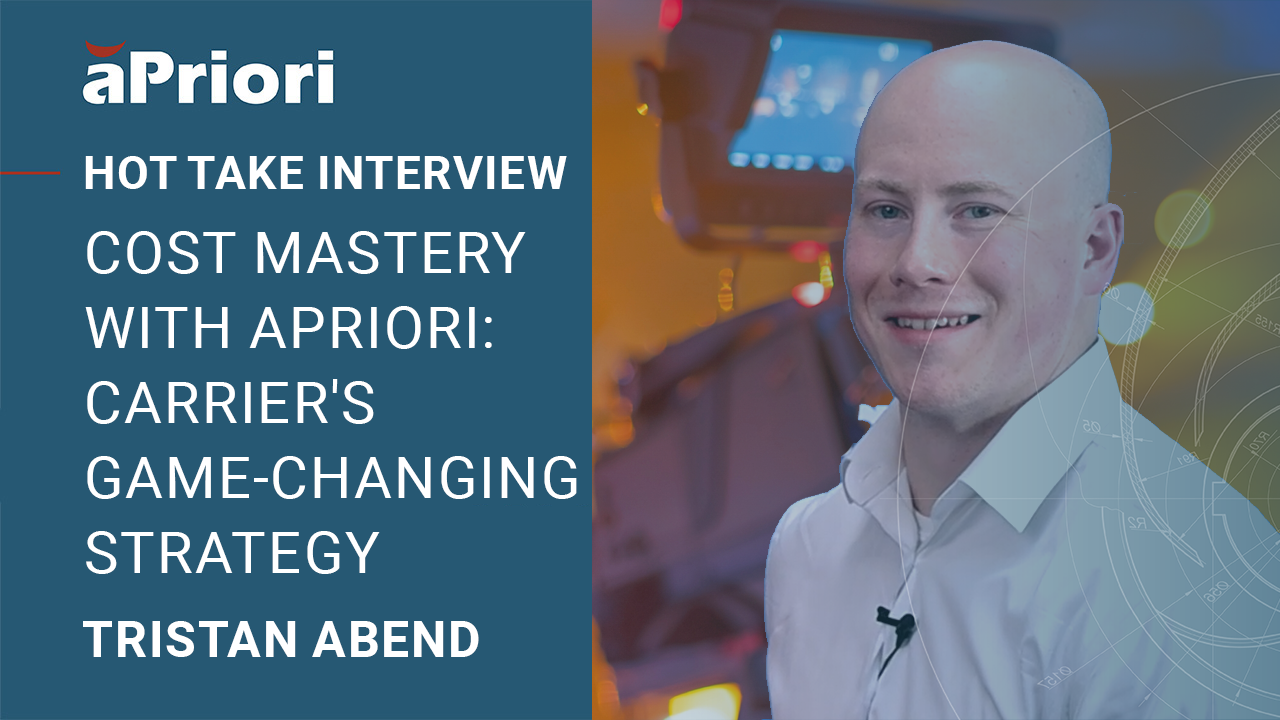
Cost Mastery with aPriori: Carrier’s Game-Changing Strategy
Want to experience aPriori in person?
Let's schedule a meeting.TALK TO AN APRIORI EXPERT