How to Unlock Speed and Savings with DFM Software
Key Takeaways:
- World Economic Forum notes many manufacturing executives struggle to successfully scale beyond single product production processes
- Design for Manufacturability (DFM) software can address the above in addition to optimizing manufacturability, costs, and sustainability
The Full Article:
The World Economic Forum surveyed more than 1300 manufacturing executives and found that just 39% were able to successfully scale beyond single product production process.
Traditionally, product development has leaned heavily on design engineers to develop a product that meets performance and manufacturability specifications. (Cost engineers then review the designs to help eliminate cost.)
Despite time dedicated to meeting these performance and cost benchmarks, a product design could still run into manufacturability issues, which can lead to costly and time-consuming engineering change orders (ECOs). Design for Manufacturability (DFM) software can bridge the gap between design, costs, and manufacturability.
What is DFM Software?
DFM software replicates real-world manufacturing environment conditions including obtainable raw materials, labor, tooling costs, available machinery and process routings, machine cycle times, overhead costs, and more. It typically uses a 3D CAD model as a primary input. Additional information such as production volume, manufacturing location, and preferred primary manufacturing process can be entered by the user. The software then simulates the actual manufacturing operation combinations available in that factory to identify the most optimal approach.
Highly advanced DFM software can provide manufacturability guidance to walk the user through diagnosis and problem resolution. Often, making small changes in the CAD model is all it takes. For example, changing the tolerance of a drilled hole can enable the manufacturer to use a less expensive and faster process. As a result, material waste and cycle times also can be reduced, improving sustainability efforts and further lowering costs.
Image 1: Determine the breakeven point, using aPriori
DFM Software Offers Clear Advantages
DFM software is valuable to the entire product development team. It should be viewed as a critical tool to optimize a product’s quality, price point, manufacturability, and sustainability. Consider the following benefits:
- Reduce design iterations and late-stage ECOs. Since manufacturability and cost insights are available early in the design stage, many performance, cost, and production issues are remediated quickly and cost-effectively. As a result, designers don’t have to repeatedly go back to the proverbial drawing board, and late-stage ECOs are eliminated.
- Lower costs and faster time to market. DFM software works directly with your CAD model. Design engineers can access their design and input basic part and/or assembly information (i.e., annual volume, location, material). The software then analyzes the CAD geometry for its cost drivers within a given manufacturing process group. Within this process group, the software evaluates which routings are suitable to manufacture the part as well as the best cycle time and material utilization. Finally, trade-off analysis allows designers to see the cost and supply chain impact of material, manufacturing (i.e., machining instead of casting), volume, and design changes. This trade-off analysis also can be leveraged to meet sustainability goals – whether it is minimizing supply chain routes or reconfiguring designs to lower the carbon footprint in the production phase. Discover how CNH leveraged DFM software to realize $312K in savings in the first two weeks.
- Improve sustainability. DFM insights help reduce unnecessary design features, decreasing the need for additional materials and manufacturing processes. Processes and different routes can be changed to reduce energy usage and cycle times in the production phase. DFM software can simulate dozens of different manufacturing processes based on design-level inputs like 3D CAD files. Although there may be an initial investment upfront, the ability to measure cost vs. carbon not only reduces your environmental impact but also lowers costs in the long run. Hear how you can calculate your carbon footprint.
- Strengthen performance. DFM software allows manufacturers to compare design options to improve quality. Early visibility can identify cost-prohibitive or potentially defective issues. For example, a product may have an internal sharp corner where there shouldn’t be one. These corners are more expensive to produce and could lead to a product crack or fatigue. Discovering such issues early in design is critical to improving the product’s quality, safety, and cost-effectiveness. Consequently, manufacturers gain opportunities to continuously improve their products. A good example can be found in electric vehicles. The ability to use DFM software to make them lighter and faster makes them more fuel-efficient and more environmentally friendly.
- Add scalability and flexibility. Since DFM software enables virtual iterations, manufacturers have greater product development flexibility and can scale faster. They also can pivot quickly to meet ever-changing requirements. Even better, they can take a proactive stance, simulating various production scenarios at different and/or the required volumes to determine whether to scale up or down their operations. If you have a low-volume product, you want to ensure there is a low capital investment in it. A $100K injection mold is not unheard of in manufacturing. Design engineering solutions can verify if it is necessary by considering viable alternative processes, potentially delivering significant cost savings. Moreover, early cost and manufacturability feedback can be used to determine the feasibility and cost of ancillary tools and processes. Stand-alone CAD tools cannot easily accommodate this function. Solutions like aPriori can show you the breakeven point (where volume and cost intersect) in more specific areas. It allows manufacturers to meet market demands faster and more cost-effectively while removing production bottlenecks.
- Enhance sourcing and procurement collaboration. An IndustryWeek State of Procurement Report noted that 68% of survey respondents agreed that connecting data systems was very important. Of those, 64% of OEMs and 63% of suppliers believed sharing specifications via model-based design (e.g., component manufacturing and inspection information included in Computer-aided Design [CAD files]) was very important. DFM software supports this priority, fostering communication and collaboration, and breaking down traditional product development siloes. Since all teams can collaborate and information share in real-time, product development is accelerated and optimized, saving time and money. DFM software that integrates into a broader platform like aPriori’s Manufacturing Insights Platform furthers collaborative opportunities. For instance, aPriori’s regional data library compares quoted prices and fosters fact-based negotiations. Collaborating more closely with your supply network reduces your risk and helps in understanding why there are issues and how to work around or overcome them.
- Greater innovation opportunities. DFM software is fertile ground for making continuous improvements to manufacturing operations. Moreover, it encourages innovative solutions and product optimization throughout all product development teams via detailed analysis and insights.
WIIFM = What’s in it for Me?
To get a full return on investment from your DFM software, you must consider and address “what’s in it for me?” (WIIFM) at all organizational levels. Executives must lead by example, conveying the power of change management’s ability to positively impact the bottom line.
No team or employee is insignificant in this process. When you help each player understand how their job will improve, how it will leave them more satisfied, and how they can positively contribute to the company, then you are more likely to get complete buy-in from them.
DFM software is a goldmine for manufacturers. When combined with a clear and measurable strategy, it can transform your business. As a result, you’ll design more efficiently and innovatively. Product quality will improve without compromising cost targets. Manufacturing processes will be streamlined and more sustainable, and collaboration enhanced. Best of all, you will be a competitive and profitable force.
Have You Unleashed the Power of DFM Yet?
See DFM in action, improving manufacturability, cost, and sustainability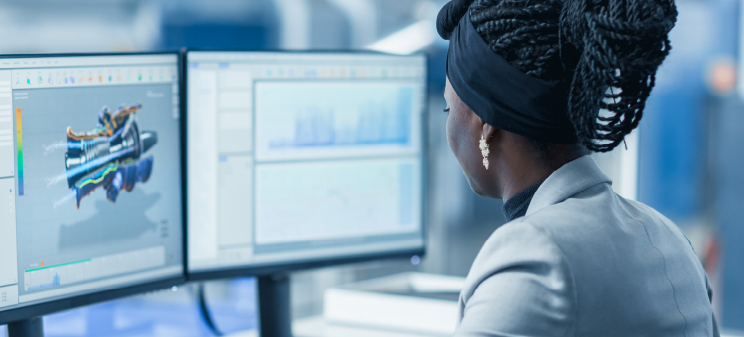