How to Improve DFM via Enterprise Digital Twins
- Market pressures push companies to optimize products for cost, CO2e, and performance
- Enterprise digital twin solutions unlock actionable cost, manufacturability, and CO2e insights
- Learn how digital twins can improve cost collaboration and negotiation with suppliers
Global manufacturers struggle with supply chain constraints, labor shortages, and inflation challenges. These disruptions delay product development timelines and impact a company’s profitability and competitive position.
Organizations are leveraging Design for Manufacturability (DFM) analysis to address these issues. DFM is the practice of designing or optimizing a product for manufacturing cost, performance, and carbon footprint requirements. DFM analysis enables companies to identify and solve design issues early in the product life cycle to save time and money.
Historically, product design teams rely heavily on their experience to optimize products for DFM. The process is typically manual and time-consuming (e.g., iterating a 3D CAD model to improve manufacturability based on a cost engineer’s experience). Using this approach, a company may not identify a design issue until the end of the development process, which results in expensive, late-stage engineering change orders (ECOs).
Companies can improve DFM performance today using advanced digital transformation capabilities. As digitalization has evolved, McKinsey and other industry leaders are coalescing around the idea of connecting multiple digital twins to provide end-to-end visibility, insights, and responsiveness. Specifically, companies are thinking beyond the traditional product digital twin to gain new insights from digital manufacturing process twins, and digital factory twins.
Connect Digital Twins to Unlock Value Throughout the Enterprise
Companies can leverage manufacturing simulation software to thread three digital twins together and unlock actionable, real-time data for better decision-making. Here’s how the digital twins connect across the product development life cycle:
- Digital Product Twins refer to 3D CAD models or virtual representations of physical assets or products. Companies often only focus on this first step rather than the following two phases of a complete, end-to-end enterprise digital twin solution.
- Digital Process Twins determine the most effective way to manufacture a product. Companies simulate manufacturing processes using the digital twin to identify the most appropriate production process for cost, sustainability, and manufacturability.
- Digital Factory Twins represent virtual factories. Detailed factory specification data includes region, and associated costs such as labor, electricity expenses, material costs, and overhead rates. And it can also include specific production capabilities per factory.
How Digital Twins Transform the Product Manufacturing Life Cycle
The digital twin model eliminates siloed information, enabling manufacturers to unlock data residing in product lifecycle management (PLM), enterprise resource planning (ERP), and other systems.
Centralizing product data via digitalization is only one step. Manufacturers that can simulate scenarios rapidly are well-positioned to anticipate new opportunities and sidestep potential roadblocks. And using the digital twin model, companies can simulate the product design, manufacturing process, and factory specifications simultaneously.
And, it enables companies to run “what if” scenarios regarding product cost, carbon, and manufacturing process and location – and make informed decisions quickly and accurately. This is especially critical as companies are focused on integrating carbon reduction into their manufacturing operations to increase their sustainability.
By connecting the three twins, manufacturers can simulate how real-world production processes and global factory conditions affect a product’s cost, CO2e, and manufacturability. The right manufacturing simulation software maximizes manufacturers’ DFM strategies and enables them to break down organizational silos and save time.
Exploring Digital Factory Twin Capabilities and Benefits
Organizations using aPriori only need to open their design models and run simulations for the digital factory to extract the critical insights automatically, including:
Additionally, manufacturers can leverage Regional Data Libraries (RDLs) so that digital factories reflect different labor rates, material costs, energy mixes, and more. Companies that use aPriori can benefit from the platform’s accurate, economic-specific data and RDLs for 87 regions across the globe. It is now easy for manufacturing companies to determine the best region to source components or manufacture a given product.
Case Studies: Cost-Saving Victories
An automation-driven, end-to-end digital twin solution optimizes the sourcing and evaluation process, allowing for faster cost reductions and product launches.
One European-based aerospace parts manufacturer faced increased supplier pricing due to energy price inflation. With aPriori’s should costs, this manufacturer successfully negotiated a 14% reduction in the supplier’s quote.
Rafael Advanced Defense Systems, an Israeli manufacturer, has provided air, land, sea, and cyber defense solutions for over 70 years. The organization received many “no bid” responses from strategic suppliers for a component. Rafael Advanced Defense Systems turned to aPriori’s simulation-driven costing capabilities to unify teams and make highly informed, cost-effective redesigns. As a result, the company saved up to 50% on parts while increasing competitive bids from suppliers.
Accelerate Product Development with End-to-End Digitalization
Today’s manufacturing companies need end-to-end digitalization to extend the value of their existing investments, such as 3D CAD and PLM systems. Digital transformation, as shown, enables organizations to work more efficiently and collaboratively to meet their manufacturability, cost, and sustainability targets.
According to McKinsey, advanced digital twin technology helps manufacturers increase revenue by 10% and accelerate time to market (TTM) by 50%. Further, companies can leverage end-to-end digital twins to improve the quality of their products by up to 25%.
An end-to-end digitalization solution provides automated, granular insights, allowing less-senior engineers to work on projects formerly reserved for technically skilled colleagues. All product team members can make informed business decisions to get to market faster, remain competitive, improve innovation, and increase profitability.
Digital Factory Guide
Learn how manufacturers are using digital factories to optimize products for profitability, manufacturability, and sustainability.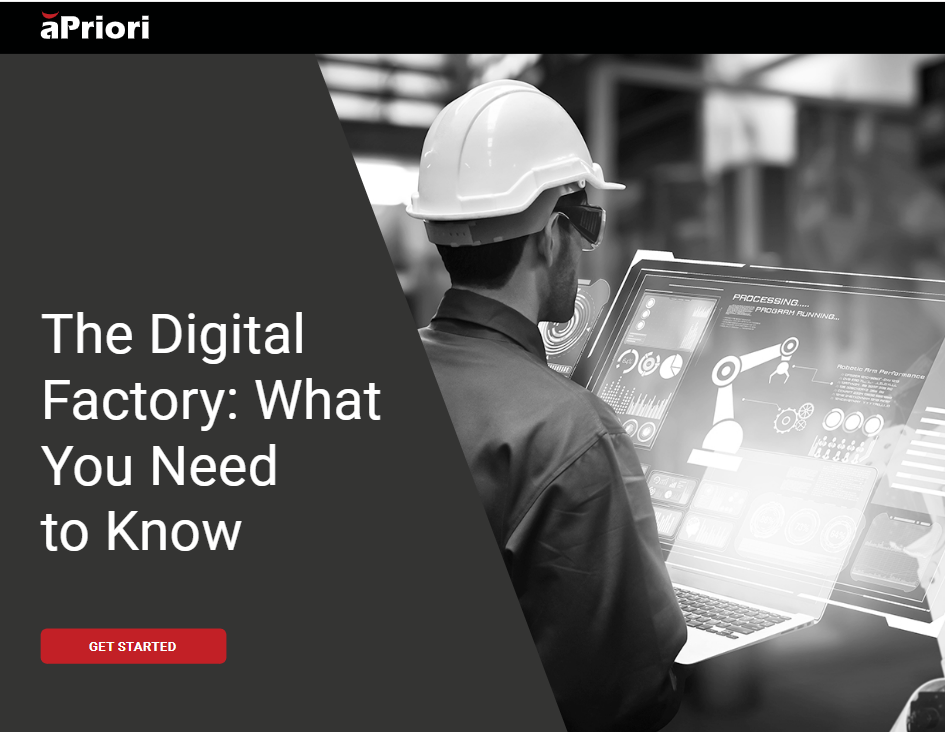