Reduce Redesigns with Early Cost and Manufacturability Feedback
Product design is the seminal step in forecasting manufacturability and profitability success. If there are product design issues, it can set production back significantly as well as impact the bottom line. Manufacturability feedback can ensure that the traditional design obstacles and bottlenecks (i.e.-supply chains, materials, and costs) are mitigated.
In this article, design engineers and manufacturers will learn how Engineering Change Orders (ECOs) can be reduced with early cost and manufacturability feedback that a reputable manufacturing insights software, such as aPriori, can provide. We will explore five features and benefits that underscore why the manufacturability of a product is important and how it can improve productivity, time to market, higher-value products, and profitability.
Implement Manufacturability Feedback for Greater Efficiency
With many components and variables, the manufacturing design process can hit a few speed bumps. First, there is the design concept. How do you know if it is feasible? How can you anticipate the potential cost? What can you do to ensure that your design department does not run into manufacturability constraints?
Now, let us assume that the concept has passed the litmus test. Do you have the knowledge to create the part? In enterprises that have not made a digital transformation, manufacturing the part could be based solely on history or their people. (It has been said that 80% of a company’s knowledge resides with their employees, with only 20% of it actually documented.)
Once the manufacturing design has been approved and you’ve determined that the knowledge is available to produce the part, the following factors must be considered:
- Will you be able to source and procure the necessary materials?
- Will cost or the supply chain hinder that process, delaying production and time to market?
- How will you know if supplier quotes are accurate and reasonable?
- What if things are progressing, and you find that the seemingly harmless tip of the iceberg hides a larger, potentially damaging one beneath the surface?
The above scenarios are avoidable with the right technology. Manufacturability insights software can ensure that time, cost, and labor can be saved, operations become more streamlined, bottom lines more profitable, and time to market accelerated.
Here are five features and benefits of utilizing manufacturing insights technology:
1. Forgo the Need for Redesigns
Design for manufacturability (DFM) is available in some CAD applications but is it usually unquantified. DFM, coupled with Design to Cost (DTC) feedback, allows design engineers to tailor designs to meet two critical benchmarks: price and performance.
If manufacturing feedback indicates there are issues, engineers can make design changes in the early stages and in the digital twin rather than finding out much later, in the real world, when it may be too late and much more expensive to address.
2. Break Down Design Silos and Receive Real-Time Feedback
Manufacturing insights software breaks down design, cost, and sourcing silos, enabling teams across the enterprise to collaborate more efficiently and cost-effectively. They can now communicate and collaborate in real-time.
As a result, everything from design and cost to sourcing and production feedback enhances product lifecycle management and, ultimately, the feasibility and cost of creating the product. Redesigns are mitigated or eliminated altogether, reducing labor and costs and accelerating time to market.
3. Foster Better Supplier Relations
Suppliers are an integral part of the product lifecycle. A design cannot become a product without the essential components. Assuming your parts or materials are available, securing them at an optimal price point is another issue. Rather than using a supply chain, the ultimate goal should be a supplier network.
With manufacturing insights and collaboration in the cloud, you can optimize your supplier network. For instance, if your usual supplier is running into delivery issues, your supplier network can provide quick access to other options to meet your timeline. Is it down to raw materials supply? Can an alternate material be used? Perhaps your go-to supplier has raised prices significantly. Utilizing manufacturing insights technology, equipped with a regional data library, enables you to compare quoted prices and begin fact-based negotiations. Collaborating more closely with your supply network reduces your risk and helps in understanding why there are issues and how to work around or overcome them.
One enterprise paused product development due to the proposed design being over budget. With a tight two-week deadline to significantly reduce costs, aPriori’s solution enabled them to quickly achieve that goal, retooling the parts production through other manufacturing methods and identifying suppliers in lower-cost regions. As result, $275,000 in potential savings was identified in the first two weeks. The customer achieved approximately $1500 in cost-per-part savings (more than the $1200 per part requested reduction). They also identified $150 savings per unit by making more cost-effective design changes.
4. Assess Product Volume Versus Value
Manufacturing insights technology can assess different processes based on required volumes. For example: If a product is low volume, you will want to ensure there is low capital investment. A $100,000+ injection mold is not unheard of in manufacturing. Design engineering solutions can verify if an injection mold is necessary by considering viable alternative processes, potentially delivering significant cost savings.
If the volume to be produced is low, it might not be worth producing tooling for that part at all. Additionally, early cost and manufacturability feedback can be used to determine the feasibility and cost of ancillary tools and processes. CAD tools cannot easily accommodate this function. aPriori can show you the breakeven point of where volume and cost intersect in more specific areas, as this cost curve chart illustrates.
5. Leverage Design for Manufacturing Checks
Typical CAD applications are incapable of providing a comprehensive design for manufacturing checks. Just one aspect of DFM is usually available to assess and verify. For instance, you may be able to check the uniformity of wall thickness for injection moldings or die casting. However, it may not be possible to verify if that wall is too thick, too thin or if there are other potential problems.
Early visibility allows engineers to identify design flaws, saving time, effort, and cost. Early visibility might reveal that a product has a sharp corner where there should not be one. Internal sharp corners are more expensive to produce. However, identification of this type of design flaw is critical early in the process because the unintended sharp corner could lead to cracks or fatigue in the product. The result could be a snowball effect or, worse, a product recall.
Turn Your Enterprise into a Manufacturing Powerhouse
Ensuring that your design engineers have the right tools maximizes product design and manufacturability of a product. Not surprisingly, costs are lower, products are of higher value, and time to market is accelerated, bringing greater agility and profitability to the enterprise.
As a McKinsey report substantiates, an organization’s cross-functional teams can more accurately and effectively benchmark product lifecycle metrics, resulting in significantly higher levels of performance success. It is a good thing – not just for design but throughout the lifecycle and organization – positioning your operations as a manufacturing powerhouse ready to compete no matter what scenario comes your way. Check out aPriori’s design engineering solutions and request a demo.
What Can aPriori Do for You?
Learn how to reduce redesigns and costs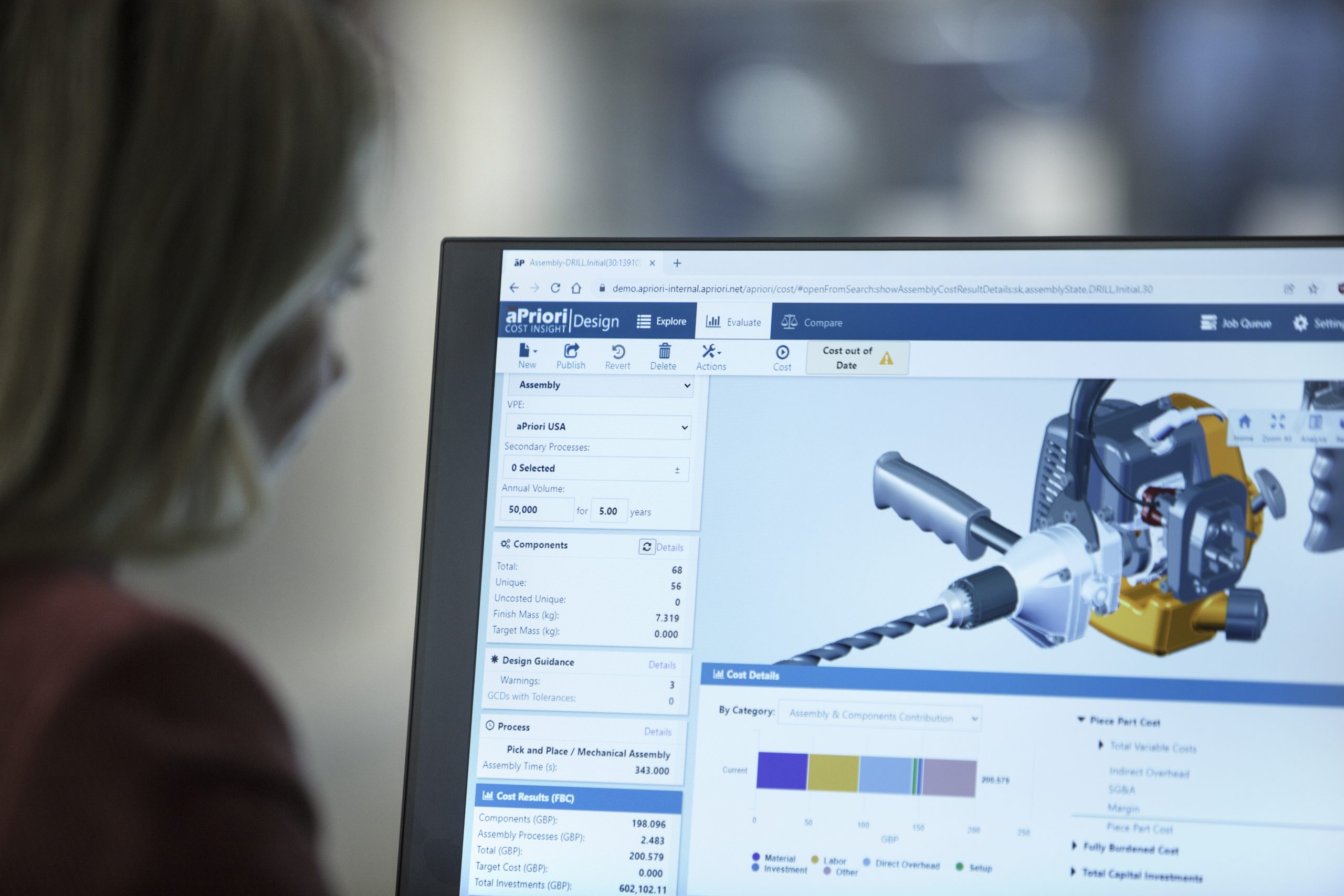