4 Steps to Optimizing Sustainable Design and Manufacturing
Key Takeaways:
- aPriori’s four-phase sustainability maturity model integrates sustainable practices into manufacturing while balancing profitability and environmental impact
- This framework guides manufacturers toward environmental stewardship using data-driven insights to make effective design, sourcing, and production choices
The Full Article:
Designing products that balance profitability and sustainability is essential in today’s market. This requirement is driven by a growing consumer demand for greener products, stricter environmental regulations, and a collective push to achieve carbon reduction targets.
Manufacturers must integrate sustainable practices into their existing operations without compromising on efficiency or competitiveness. This raises a pivotal question: How can manufacturers align their operations to promote environmental stewardship and spur growth?
To address this critical issue, aPriori has established a sustainability maturity model as a strategic roadmap for manufacturers to assess their current capabilities and the effectiveness of their green supply chain management initiatives. By monitoring their sustainability maturity performance, manufacturers can establish clear steps to reduce their carbon footprint.
The following figure illustrates how product development teams can assess and pinpoint their position across the four stages of sustainability maturity.
Manufacturers that don’t advance their sustainability maturity to the fourth and final stage risk falling behind their competitors and being saddled with additional operational costs due to incurred carbon taxes and other regulatory policies enacted to spur the reduction of greenhouse gases (GHGs).
Stage 1: Create Precise, Auditable CO2e Emissions Baselines
Creating an accurate carbon emissions baseline is the first step in achieving a sustainable and green supply chain. This baseline empowers sustainable manufacturers to measure and quantify the carbon footprint of their existing supply chain operations, enabling them to:
- Use their current “state of sustainability” as the starting point to plan and track their progress
- Identify and focus on the areas with the highest cost and carbon reduction potential.
- Set realistic cost targets that guide and influence product teams’ supply chain decisions.
- Adhere to environmental, social, and governance (ESG) standards and regulations.
- Benchmark and compare their sustainability performance against industry competitors.
Life cycle impact assessments (LCIAs) are a standard method to establish CO2e baselines and provide manufacturers with standardized emissions estimates for product lifecycle areas that are impossible to measure accurately.
Carbon assumptions for a product’s in-use phase can be entirely different from reality. A car, for example, could burn fossil fuels for 300,000 miles within the range of established fuel consumption values, or it could be written off in an accident after 1,000 miles. Similarly, a product designed for 90% reuse could still end up in a landfill and not achieve its optimal contribution to the circular economy.
An LCA is a great tool for making assumptions and using averages. However, the manufacturing process doesn’t require that level of guesswork, so a more precise baseline would be beneficial for that phase.
aPriori’s automated sustainability insights solution closes the gap by integrating data from ecoinvent, a leading third-party LCA and inventory database tool. aPriori utilizes ecoinvent’s database to quickly establish environmental baselines and GHG emissions at the product level. With automated and more precise baselining, teams can quickly move to the second phase of sustainability maturity: evaluating and selecting sustainable suppliers.
Stage 2: Select Sustainable and Responsible Global Suppliers
Next, evaluate and select suppliers based on their local electricity mix, material supply, and processes (Scope 3). Procurement teams can create digital factories for each supplier to see each vendor’s carbon impact, and then compare vendors using the same production criteria (e.g., the same production volume, manufacturing process and equipment, etc.). Digital factories will also show how the energy mix and energy consumption of a supplier in India, for example, compares with production facilities located in Mexico and China.
Product teams aim to enhance the sustainability of existing innovations through informed supplier selections instead of resorting to costly design or material changes.
Sustainable sourcing offers the most straightforward approach to reducing CO2e by minimizing the need for extensive design changes, and therefore can be implemented at any time. However, it is difficult for product teams to capitalize on this opportunity without a dedicated and standardized tool such as aPriori.
aPriori provides manufacturers with complete visibility into the sustainability of their supply chain, through a digital twin of the manufacturing facilities at their disposal, empowering them to make data-driven sourcing decisions. By utilizing aPriori for sustainable sourcing, companies can:
- Explore various “what-if” scenarios (regions, routings, materials, volumes/batches, suppliers, make vs. buy).
- Reduce iterations and negotiation by digitally connecting buyers and suppliers.
- Fill skills gaps with exposure to granular, actionable, real-world sourcing data.
- Identify sustainable procurement strategies to support internal ESG goals and initiatives.
Stage 3: Optimize Existing Products for Cost and Carbon
The path toward greener products involves optimizing existing product innovations. In stage three, product teams can consider alternative materials with lower carbon or higher recycled content. And they can also make processes more efficient to improve cost and environmental sustainability, or look to utilize renewable energy sources.
The objective is to minimize cost overruns and release products at target costs to maintain profitability and competitive advantage. However, this is difficult to achieve when cost engineering teams are limited to conventional, labor-intensive costing tools like manual spreadsheets. And the complexity of this challenge heightens when the situation extends to CO2e emissions. This is because spreadsheet-based solutions cannot:
- Evaluate the complex interrelationships between direct and secondary cost & carbon drivers in real time
- Accurately manage cost & carbon variables in an ever-changing global supply chain
- Identify and capitalize on cost & CO2e reduction opportunities during early product design phases
aPriori provides a precise, real-world product cost optimization solution to make highly informed and effective manufacturing decisions. aPriori’s cloud solution can simulate production based on product design (geometry), manufacturing overhead costs, direct labor hours, machine hours, and more. This capability can be fully automated through PLM integration. (Learn more about the three levels of CAD automation in our new webinar.)
Additionally, aPriori enables companies to navigate and manage rising material costs, inflationary pressures, and other external risks to build cost-effective products. aPriori also automatically notifies and provides actionable feedback to design, manufacturing, and sourcing teams when products exceed cost thresholds. This facilitates seamless collaboration among product development teams, enabling them to eliminate cost drivers early and maintain corporate profit margins proactively.
Stage 4: Remove Embodied CO2e Through Data-driven Product Design
The final stage of sustainability maturity represents the most challenging path and the greatest opportunity for reducing GHG emissions. Product engineers can typically compare multiple product designs and intuitively select the most cost-effective option for both cost and DFM. But when you add carbon to the mix, the answer is usually far from obvious.
But by using real-time CO2e feedback from the 3D CAD model, teams can proactively modify the product’s design to reduce its embodied carbon. They can also ensure that a product meets its targets for cost, DFM, and sustainability by selecting the option that best balances all requirements for sustainable design.
Adopt A Culture of Sustainability Throughout your Organization
It takes more than publicizing your carbon reduction goals or investing in new technologies to make a company and its employees truly committed to reducing global warming. It takes a clear, ongoing commitment to build and maintain a corporate culture of sustainability.
Automaker Toyota, for example, takes an integrated approach to embedding sustainability into its core operations. And it also provides transparency regarding progress toward meeting its sustainability targets. Visibility is essential to ingraining sustainability into daily operations. Addressing sustainability during the early product design phase provides teams with a way to gauge the impact of their decisions, makes sustainability a regular part of design reviews and other activities, and helps to underscore a company’s active commitment to reducing its carbon footprint.
The financial and competitive advantages of being a sustainability leader are well documented. It’s also playing an increasingly important role in attracting and retaining talent. Deloitte surveyed 23,000 Gen-Z and Millennials globally and found that climate change weighs heavily on these age groups, and influences where they want to work. The survey reveals that 40% have, or plan to, change jobs due to a company’s climate efforts. And 55% of respondents say they research a company’s environmental impact and policies before accepting a position.
A product designer, for example, may be more inclined to work for a manufacturer that provides green buildings with products that reduce the negative impacts of CO2e and increase energy efficiency. Read our case study on Carrier’s design thinking and its approach to sustainable design.
Take the Next Step to Optimize Sustainable Design
Optimizing sustainable design and manufacturing is not just a choice: it’s pivotal to addressing today’s market requirements and customer demands. aPriori’s four-step sustainability maturity model presents a comprehensive strategy for manufacturers to align their operations with environmental stewardship while enhancing profitability and market competitiveness.
This four-stage model provides a roadmap for best-in-class green manufacturing based on strategic design strategies. It also underscores the need for data-driven insights to make effective design choices amid increasingly complex supply chains. Mature companies in this area will contribute to global carbon reduction efforts and position themselves as leaders because sustainability is increasingly a determinant of success.
Watch our 3 Real-world Examples of Cost-Carbon Challenges
Get insights into our approach – and our results!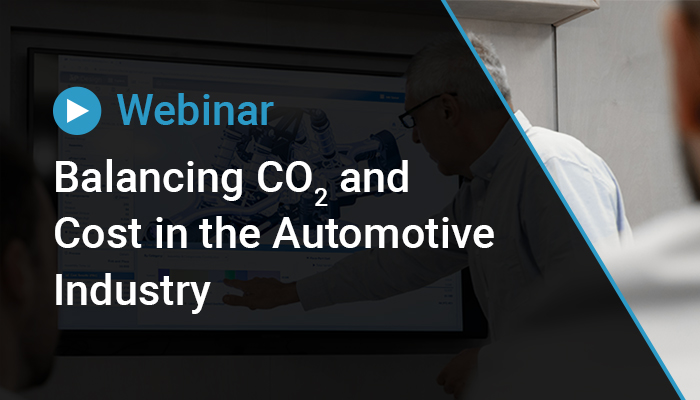