Sustainable Sourcing Strategies that also Improve the Bottom Line
Supply chain sustainability is becoming pivotal in determining success or failure for discrete manufacturers. Growing demand for green products and looming environmental reporting mandates could have a material impact on companies that aren’t meeting regulatory benchmarks to reduce greenhouse gas (GHG) emissions and help to mitigate climate change.
The pandemic illustrated how procurement teams can minimize disruption through effective supplier relations. And because supply chains can account for more than 80% of a typical manufacturer’s GHG emissions, it’s also the cornerstone of any CO2 abatement strategy and business shift to make sustainability a core focus.
Forward-thinking companies are making sustainability a core business focus. A true business shift requires corporate leadership to tie their environmental, social, and governance (ESG) pledges to measurable goals across procurement, IT, manufacturing, and other operations.
Let’s examine how sustainable sourcing is central in driving business practices to achieve net-zero goals. Read this article from the beginning or jump to key sections using the following links:
- Sustainable Sourcing Business Advantages
- Sustainable Supply Chain Case Studies
- 7 Steps to Addressing Sustainable Sourcing Goals
- Apply Sustainability Insights for Competitive Advantage
Sustainable Sourcing Business Advantages
The largest US firms (S&P 500 companies) see a multi-trillion-dollar opportunity in the shift to products and services for the low-carbon economy. That’s according to survey results from CDP, a global non-profit that runs environmental disclosure system for public and private organizations. The September 2022 findings also reveal that US firms project the financial benefits to be 15 times higher than the risks associated with not transitioning business practices to decarbonization.
Across the globe, Bain projects that Southeast Asia could reap a trillion-dollar annual economic opportunity by 2030 if public and private sectors address regional sustainability challenges.
And a typical company that implements sustainability best practices can improve its profits by more than 50% within three-to-five years, according to noted sustainability expert Bob Willard. Mr. Wilard calculates profit-margin growth based on increased revenue, reduced energy, waste management, water, and material expenses, among other factors.
Manufacturing Strategies for the Circular Economy
To reach reduction targets for carbon dioxide equivalent (CO2e) emissions, manufacturers must redefine their product lifecycle strategies and incorporate sustainable sourcing practices into their operations. In discrete manufacturing, products are typically designed for planned obsolescence (products are purchased, discarded, and replaced). But the United Nations (UN) and other global organizations see a “circular economy” that emphasizes recycling and reuse – as a critical path forward.
The UN notes that manufacturers support the circular economy by designing products to be “reused, remanufactured, recycled, or recovered and thus maintained in the economy for as long as possible.”
In addition to maximizing the value and use of materials and other resources such as water and energy, the circular economy model also minimizes the consumption of virgin materials, hazardous substances, and waste production.
Developing a sourcing strategy to support a circular economy is an essential element of “green procurement.”
Sustainable Supply Chain Case Studies
1) BMW: The multinational automaker’s “Secondary First” approach makes reused materials a priority for production. Today, nearly 30% of BMW cars are manufactured with secondary materials (e.g., aluminum and other “secondary”/reused materials). To help improve supply chain sustainability, BMW collaborates with its suppliers and has them self-assess their sustainability management capabilities. BMW also independently audits select partners regarding their carbonization levels.
2) Collins Aerospace: The technologies and solutions provider for aerospace and defense industries uses alternative material selection to reduce cost and contribute to circular economy initiatives. The company is now specifying thermoplastic composites to produce a variety of parts. Thermoplastic composites can reduce weight by 50% compared to metallic alternatives. These lighter parts help to reduce the overall weight of aircraft. And lighter aircraft minimize fuel consumption and carbon emissions. The company can produce thermoplastic composites up to 80% faster than thermoset alternatives, which reduces energy costs. And unlike thermoset materials, thermoplastic composites can be 100% recyclable.
3) Ørsted: The Danish company develops and manages green energy technologies ranging from wind and solar farms to renewable hydrogen. The company’s supply chain decarbonization initiative identifies and addresses “hot spots” that have the greatest impact on a product’s carbon footprint. As an example, more than 50% of carbon emissions from the company’s wind turbine production and installation come from steel that goes into the foundations (below the waves) and the towers (above the waves). This insight enables Ørsted to prioritize alternatives that will have the biggest impact.
7 Steps to Addressing Sustainable Sourcing Goals
There’s been a widely held assumption that manufacturing sustainability gains come at the expense of lower cost or dependability. But as the previous examples from Collins Aerospace, BMW, and others show, there are critical opportunities to simultaneously reduce cost, resources consumed, and a product’s carbon footprint.
That said, capitalizing on these mutual gains requires clear corporate goals, along with the visibility, transparency, collaboration, and analytics to meet business objectives. Reliable supply chain insights and visibility serve as a foundation to support strategic decision making. Cross-functional teams require accurate data to consider design and production scenarios and select the optimal mix of cost, CO2e pollution, and manufacturability (which includes product performance and resource utilization).
The pandemic forced many companies to improve supply chain visibility through digitalization and other efforts to increase resilience. Business leaders can also use those investments to address sustainability priorities. Procurement executives are revising and expanding their current supplier management initiatives to incorporate sustainability. Our seven steps to implement and advance a low-carbon procurement model follow.
1) Use Sustainability Reporting to Guide Action
Mandatory ESG reporting begins for qualified European Union (EU) companies on January 1, 2024. The US and other regions are in various stages of implementing their own non-financial reporting requirements to provide investors, customers, and other stakeholders with better metrics on the environmental impact of business operations.
Business leaders are increasingly using sustainability reporting standards and frameworks to help prioritize and guide objectives to improve their environmental performance.
For example, most companies that are required to comply with EU Green Deal mandates will need to reshape their organizations to meet these shared goals – including R&D, product development, procurement, manufacturing, etc. And business leaders need to align their departments and operations to gain efficiency and address evolving market needs. (Read our blog post about EU Taxonomy reporting requirements.)
2) Expand Supplier Collaboration and Qualification
Technology advances alone won’t change the inherent tension between some manufacturing brands and their suppliers. After all, each side is working to increase margins and favorable terms at the expense of the other. Sourcing research confirms what many of us inherently understand: that personal relationships between OEMs and suppliers is the foundation for deeper collaboration.
Supplier relationships are vital. Manufacturers that share information are often more likely to increase supplier collaboration. For example, manufacturers can provide their award selection criteria during the request for quote (RFQ)/bid process. RFQs that focus on cost and additional services are well-suited for suppliers with relevant capabilities, but not for vendors that solely compete on price. And OEMs that articulate the strategic value of a project to a supplier – and spotlight the financial benefits of shared success – are better positioned to foster collaboration and data sharing.
Understanding suppliers is crucial because manufacturers face ongoing challenges verifying vendor sustainability claims, according to a report published in the Cleaner Logistics and Supply Chain Journal. This challenge is primarily attributed to a lack of data standardization/sustainability reporting and because digitalization is not commonly used for sustainability assessments.
Suppliers and manufacturers can use third-party services to demonstrate adoption of sustainability best practices. This could include certification as a B Corporation or in ISO’s quality management standards for sustainability.
3) Baseline Current Supply Chain Emissions
Measuring upstream and downstream emissions is essential because your suppliers – and, by extension, their vendors – can account for a significant share of a manufacturer’s environmental impact. To help understand your company’s actual carbon footprint, the Greenhouse Gas Protocol (GHG Protocol) provides three levels/scopes of CO₂e measurement for manufacturers:
- Scope 1 addresses direct emissions from owned or controlled sources.
- Scope 2 includes indirect emissions from purchased energy generated, along with the GHG tracked in Scope 1.
- Scope 3, the Corporate Value Chain Standard, measures all upstream and downstream emissions along with GHS tracked in Scope 1 and 2.
Use Scope 3 results to measure your supply chain’s carbon footprint accurately. Manufacturers typically use product life cycle assessment (LCA) software to collect sustainability information once a design is complete. But this manual process is cumbersome, and sustainability information isn’t integrated into other systems.
4) Establish a Supply Chain Sustainability Plan
Procurement leaders can use current carbon footprint information to develop a roadmap that details how green supply chain initiatives will help achieve overarching corporate goals, such as reaching net-zero emissions by 2050. Armed with concrete sustainability objectives, procurement leaders can collaborate with suppliers and internal stakeholders to drive change through various methods.
5) Develop Key Performance Indicators (KPIs) to Track Progress
Monitor GHG emissions and other upstream impacts to track progress toward procurement and business goals. Best practices include:
- Create a KPI baseline and determine how KPIs should be reviewed and adjusted
- Only use KPIs that directly map to overall targets/goals
- Get input/buy-in from suppliers. This includes incentives for meeting or exceeding specific targets
6) Extend Traceability to Include Sustainability
Visibility and traceability also can help companies meet stakeholders’ growing demands for sustainable products by ensuring that they are sourcing raw materials and developing and transporting products with a net-zero impact on the environment.
To help ensure responsible sourcing, third-party organizations, such as the Initiative for Responsible Mining Assurance (IRMA), monitor suppliers for ethical sourcing, safe working conditions, and other sustainable procurement benchmarks for manufacturers.
Successful raw material recapture and reuse at the end of a product’s life cycle depends heavily on traceability. An effective circular supply chain tracks materials throughout the product life cycle so they can be identified and fed back into the conversion process for reuse, recycling, or remanufacturing. These circular supply chains are not limited to a single company’s value chain. Third-party vendors often recycle and feed the materials into another sector’s value chain as substitutes for virgin raw materials.
7) Gain Real-time Insights into Cost, Sustainability, and Manufacturability Trade-offs
Select companies are gaining these insights by integrating sustainability, design, sourcing, and manufacturing data. One multinational commercial vehicle manufacturer worked with aPriori to extend its digital factory capabilities to include sustainability insights. And we are using this proven solution as a framework to commercialize this capability.
Apply Sustainability Insights for Competitive Advantage
The business case to make sustainability a strategic imperative for growth is clear. And while creating a sustainable supply chain is essential, it’s also incomplete without advanced analytics. To gain a true competitive advantage while reducing GHG, manufacturers require the ability to reduce CO2 emissions and meet their other product requirements simultaneously.
With aPriori, select companies are gaining these insights by integrating sustainability, design, sourcing, and manufacturing data. The aPriori Manufacturing Insights Platform enables users to identify trends and guide effective decisions amid increasing supply chain complexity.
aPriori enables businesses to gauge a product’s CO2 impact during early design phases, and then evaluate opportunities to reduce a product’s carbon footprint. Importantly, teams can simulate design alternatives using different materials and manufacturing processes to meet environmental, cost, and performance targets.
Companies with capabilities to evaluate the impact of changes to product sustainability, design, bill of materials, and manufacturing processes are well-positioned to achieve environmental targets. And a sustainable supply chain management strategy will help to enable manufacturers and their suppliers to embed carbon reduction in everyday operations.
Struggling to Balance CO2 and Cost Requirements?
Watch "Keys to Making Informed Design and Sourcing Decisions."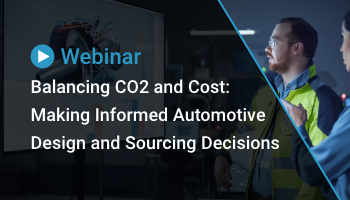